Drilling through Rock
Posted by Heading Out on August 2, 2009 - 11:00am
There are times when new technologies are proposed as being better ways of drilling for oil and natural gas. However, to understand how these are better (or more likely not) than existing technologies, you have to know how the industry commonly drills through rock. There are two basic ways of doing so, depending on how hard the rock is. The first is the one that made the Hughes family very rich (if you ever saw the film The Aviator, Howard Hughes extravaganzas were paid for because his father had invented an effective way of drilling oil wells). The other, somewhat slower, was developed the last time that we had an energy crisis, and uses artificial diamonds, in the main, to gouge into and scrape off thin layers of rock.
Before I describe the diamond bit, let me borrow a bit from a post I did four years ago, and describe the idea behind the Hughes bit, which for reasons that I will explain, is usually referred to as a tri-cone bit.
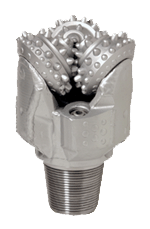
I have put together a number of tech talks in the past. This is the first in a series of updates.
To start one can go back to the mining industry (can we call it one of the older professions) where holes were drilled, until about a hundred years ago, by taking a chisel in one hand and holding a hammer in the other with which one whacked the upper end of the chisel as it was held against the rock. This is called hand steeling and if you want to try it or see it, there is a video here and student competitions at various places. A skilled miner can drill a 1-inch hole at the rate of about 8 inches in five minutes, using a 4-lb hammer.
Now what he does (if you watch the video you will see this) is to hit the chisel, turn it about a quarter turn between blows, and then hit it again. The turning is the critical bit. Because when you hit the chisel it crushes the rock directly underneath it, but the wedge head pushes sideways against the rock on either side. So if the driller turns the chisel between blows he will not only crush the rock, but will also chip out the thin layer between the second blow and where the first hit. This removes a lot more rock for the same amount of energy. In fact it is the skill of the driller that will make bigger chips, for less muscle power, by turning the bit, rather than using brute force to crush the rock just under the chisel into powder. (On a larger scale the same idea is used to drill very large tunnels. Bit disks roll over the surface of the rock crushing the rock immediately below them, but the rock in the inches of spacing to the next disk spalls out of the face without direct contact with the tool).
When it came time to drill the first oil wells this was the technique that they used. Except that they made the chisel much larger and heavier, so that, by lifting it and dropping it, it's own weight would act as the hammer. Normally a larger spudding bit was used first to make a larger diameter hole from 4 to 22 inches in diameter, and down for 50 ft or more. Once this starting hole had been drilled (using a cable over the derrick to a crank to raise and drop the bit) a steel pipe was lowered into the hole and cemented in place. This pipe provided a base for the deeper hole, and provided a case around it. Thus it became known as casing, and it protected the hole as it went through the top soil and weakest of the upper layers of the ground.
Once the hole had been spudded-in, and this initial conductor pipe installed, then the normal sections of steel tubes could be strung together to form a pipe (hence the name drill string), and the drilling bit (in those days around 4 to 5 inches across) would be raised and dropped by a walking beam engine. As the hole was drilled they would stop, perhaps every couple of feet, to pull the bit out, and sharpen it, and to bail the crushed rock or cuttings, out of the hole.
Progress was, as you can imagine, slow, and this tool is very difficult to steer, particularly as the drill goes down several hundred feet. And so the industry was ripe for a better way of drilling.
This was invented by the older Howard Hughes who realized that if very small chisel shapes could be set around a roller they would do the same thing as the dropping bit, but could be moved around by rolling, and pushed into the rock by the weight of the connecting rods to the surface. To spread the load over the face of the hole, and to balance the bit, he used 2 rollers which tapered towards the center of the bit.
Hughes, along with his partner Walter B. Sharp, formed the Sharp-Hughes Tool Co. and produced a model of his new bit. Rather than sell his bits to oil drillers, Hughes and Sharp opted to lease the bits on a job basis, charging U.S. $30,000 per well. With no competitors to duplicate their drilling technology, they soon garnered the lion's share of the market. Flush with their success, the partners built a factory on 70 acres east of downtown Houston, where they turned out the roller-cone bits that quickly revolutionized the drilling process.2
This later evolved into a 3-cone assembly and what is now known as a tri-cone bit, a modern version of which is pictured above. (The shape of the teeth vary as a function of the hardness of the rock that is being drilled. As a rough rule, the tougher the rock the smaller the teeth are, and the smaller the chips that are generated).
The way the tri-cone bit works has a lot common with the earlier methods. While the bit crushes the rock immediately under the bit teeth their most productive work comes in creating chips from the rock between two adjacent tooth indentations by a combination of wedging and uplift that breaks the rock under tension and shear.
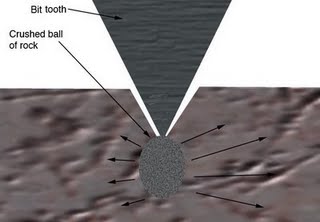
As the bit is pushed into the rock it crushes the rock immediately under the tooth, and this crushed rock distributes the applied force around the edge of the zone as it plastically deforms. This gives the lateral and upward forces on the surrounding rock that causes it to crack and spall from the solid as a chip.
This bit has a number of problems under different conditions (it is harder to control in directional drilling since if the pushing force varies too much it can wander off in odd directions) and there has to be a way of getting the rock out of the hole. These have led to other drilling ideas, including the “diamond bit” drilling idea, that I discuss in the second section of this post.
But as you watch the movie "The Aviator" remember that all those shenanigans were paid for with the money that came from that drilling bit, and that Hughes (the company) is still reported to have 40% of the world market share of oil well drill bits.
Drilling with Diamonds
One of the problems of a tri-directional bit is that some rock is too hard to be able to push the tooth into the rock and create a big enough crushed zone to do much good with conventional materials. So, obviously, the next step is to go to a harder bit material. And to make sure that we can cut into the hardest rock material, it is logical to want to use the hardest material, diamond, for the bit tooth.
Historically, however, finding and being able to afford diamonds in the sort of half-inch size we need for the bit tooth was a bit difficult. The ones that were affordable were the very small diamonds known as industrial diamond, in the very small sizes. So the way in which we had to cut the rock was changed. Instead of having a few teeth that rotated over the surface of the rock, instead the face of the bit was coated with a thin layer of small diamonds set in what is called the matrix.

The very small diamonds scratch into the surface of the rock, in the same way that a diamond in a ring might cut into a glass plate. Individually the scratches are small, but if the core bit is pushed into the rock, they accumulate and remove rock, although quite slowly. A tri-cone bit might go through rock over 100 feet an hour, while a conventional diamond bit which is taking much smaller bites, will go at only a few feet an hour. It also turns faster than a conventional bit, which is why they are often combined with a down-the-hole motor on the bottom of the drilling string to give this faster speed.
And if you push too hard on the bit, then you can push the diamonds down into the matrix, so that the matrix is rubbing against the rock, rather than the sharp diamond edge, and this slows things down. (This is particularly a problem if drilling through granite, which I once spent a summer doing). And so the question came as to how to make this sort of drilling faster. We would still need the diamonds, to cut into the harder rock, but couldn’t we find a better way of making an artificial diamond – after all we only need to have it on the surface of the bit, and perhaps just apply it as a coating to a bit.
Well it turns out that this was possible, and depending on which convention you adopt the Polycrystalline Diamond Compact (PDC), or the PolyCrystalline Diamond (PCD) was born. Simply put (and the technology is actually anything but) a thin layer of diamond power is put into a mold and a central core of tungsten carbide is then nested in the middle of the mold. The mold is then put into a special press where the assembled powder is subjected to extremely high pressure and temperature, using specially designed anvils. Temperatures are in the 2,000 oC range, and pressures around 60,000 bar (882,000 psi). The result is an element (they come in a variety of shapes) where the carbide bit is coated with a thin layer of a polycrystalline diamond, since all the diamond particles have fused together to form the surface layer.
(In reality the technology is a bit more complex, since a single thin layer of diamond is brittle in the way the shell of an egg is, without strong back support, and so there are graded layers to make this “diamond” shell tougher so that it does not shatter when it hits the rock hard).
The most typical shape that is used in oil and gas well drilling is a small cylindrical insert, with the bit made up of a number of these individual cutters.
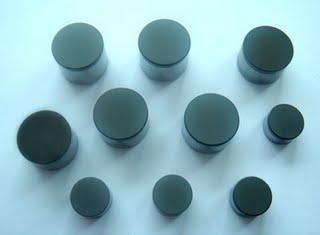
There was a considerable effort put into designing the best way of combining these cutters, back during the last Energy Crisis, with a lot of the work being done at Sandia Labs. The bits that have emerged are now much larger and more robust, and are quite widely used. Energy Tomorrow featured a picture of one back in May.
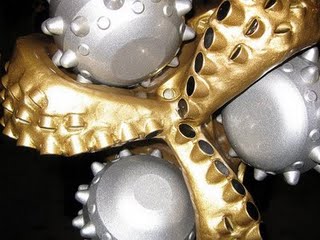
Notice that the diamond cutters are along the edge of the rigid parts of the drill bit. This is because the diamond, although a very powerful cutter, is very sensitive to temperature. Since the cutter is being dragged over the surface plowing up and peeling off a slice of the rock, there is a lot of friction under the cutting point, and if the cutter heats up above about 300 degrees then it softens, which is not good. So by placing it on the face of the bit, and with an open passage to the face, cooling mud (of which I will write more next time) can now flow across the face of the cutter, keeping it cool, and thus sharp, and able to cut through all the rock in the way. (If you were to look at the full face there are more cutters in the center of the bit and along the edge to make sure that none of the cutters is asked to cut too much – remember that the whole bit is turning, so the cutters on the outside also move faster over the rock).
This type of cutter is now large enough that can now cut deeply enough into the rock that it can chip some of the rock out ahead of it and so the process also becomes a little more efficient. (But I will revisit that topic when I talk about the energy of different rock drilling methods in a later post).
One of the reasons that the support for the cutter is so long is that the edge of the cutter is pushed into the rock, and still has to crush the rock under it, to get enough purchase to be able to chip out the rock ahead of it. (Though once that starts less rock has to be crushed as the bit moves forward).
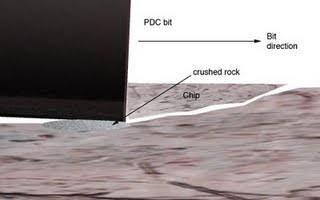
As usual with these tech talks, I have simplified the description in order to keep this short and to the point. If those knowing more wish to comment, please do so.
Thx very much Heading Out - this was a very interesting piece of post. I have little to add as such but now at least - I can debrief and debunk some of my 'don't know how'-friends on this subject :-) Looking forward to your follow-ups and (BTW) 'The Aviator' is one of the more entertaining movies ever made IMO, hard to understand that it is based on someones actual life ...
That was great info - thanks! I really appreciate your clear descriptions.
One of the more enjoyable museum trips I've made was with my 8-yr-old grandson, to the oil museum in Oil Springs, Ont. They had a tri-cone drilling bit we could handle, and we rotated it on the floor, imagining drilling thru the carpet, then the concrete floor, then the ground under the floor, until we hit oil. And he greatly enjoyed climbing up on a railway tank car. On the way home we discussed how the road surface we were driving upon was made from oil, and that really impressed him.
I'll be sure to pass along your explanation of how the tri-cone bit works, next time we handle one.
The California Oil Museum in Santa Paula CA. Their collection of photographs includes two of Union Oil Picnics circa WWI during the time interval that the workers changed from horses to cars.
http://www.oilmuseum.net/
There was also one in the Natural History Museum in Houston last time we visited that fair city.
Thanks for the info, HO. I always enjoy your accounts of the actual technology of mining and drilling.
Ther is a large granite quarry near my home and thier scrap metal winds up at a steel recycler where I shop frequently for the beams,channels, angle iron, and pipe that will be unobtainium one of these days.
I have bought a couple of dozen of the "drill steels" as they are known to locals who work there.The tricones described screw onto the steels and the steels can be screwed together to bore holes as deep as necessary.
I have found a couple of the tricones possibly discarded by mistake that appear to be in excellent condition. I saved them for conversation pieces.
Maybe I will discover a use for them someday.
This is post is very good information in showing the complexity of oil and gas production. Most people have no idea of how a hole can be made through rock. I always thought the drill bit was cutting like one goes through wood when drilling, but it is more like making many small chisel impacts on the rock with tri cone bit. Even a mechanical engr. like me can learn new technology. Diamond bit appears to do both crushing and chipping of rock face.
One question that persists is how does the broken rock (chips and dust) get out of the hole?
One question that persists is how does the broken rock (chips and dust) get out of the hole?
Please, Heading Out, don't make us wait too long before you write about the glories of mud ("Talk dirty to us, big guy!).
It is already up on Bit Tooth which is my own site. As we used to do back when these started, Gail and I feel that these Tech Talks will probably continue on Sundays, since they are slow days for other news, and thus these don't get in the way of other things.
Ok...someone has to do it...
What a boring post!
I'd always wondered how those tri-cone bits actually did any good. For some reason I'd always imagined that it chewed the rock to death rather than tapping on it to death. Wouldn't last very long trying to chew with brute force, but that seems like the strategy of the diamond bit. A step backwards, supported by advances in materials technology?
The old style bits that were raised and dropped were still used in some applications into the 1950's - I have an NCB film of the shaft sinking at one of the mines where they started off using it. They were putting in a freezing ring around the shaft area to prevent water coming into the shaft while it was excavated, but they could not drill the holes straight enough with the original system. (They were going down less than 2,000 ft).
When they switched to rotary drilling with the tri-cones not only were the holes drilled a lot faster, but they were much more accurately drilled.
I'll have a couple of posts on directional drilling before long, and talk a little more about other methods of drilling. Diamond drilling helps you get through harder rock faster in some cases than you can achieve with the tri-cones.
I suspect you know this, but for those who do not, cable tools are still used on a limited basis for certain specialized applications. Deeping out an open hole completion by a few feet to obtain a higher rate of fluid entry (while avoiding the potential for drilling mud related problems) is one of the more common.
The Bit Tooth site won't accept my TypePad id, so I'll mention this here. You might want to add a paragraph about blowout prevention. I recall the guy who taught the "practical" mud class at UT-Austin many years ago telling stories about failing to increase mud density quickly enough in response to rapid pressure changes, eg, when drilling into an unexpected geopressured brine reservoir.
Thanks - there is actually a post on borehole pressures and some of those issues in the works - last time I did the series it came two weeks after the mud post. However I may put in a couple of posts on EROI of drilling before we leave bits and the bottom of the hole, this time around. But with your indulgence we will get there in time.
Fluid is circulated down the center of the pipe, with two purposes, one to cool the bit (as I mentioned with the diamonds) and one to carry away the cuttings. I'll be revisiting my original mud post next (since the fluid is called drilling mud).
During the 60's I began a survey of the energy and materials used in medicine, especially radiology. I was amused when I learned that barium was used for barium enemas and in oil well drilling mud.
From Wiki:
"Barium sulfate is used for its heaviness, insolubility, and X-ray opacity. It is used as an insoluble heavy mud-like paste when drilling oil wells, and in purer form, as an X-ray radiocontrast agent for imaging the human gastrointestinal tract."
Wasn't it Howard Hughes' father who invented the tri-cone bit?
yes it was - and I reckon you were fooled by the heading text in the link "older Howard Hughes", but the first paragraph in the main body you have .... "Howard Hughes' father, Howard Hughes Sr., made his fortune by designing a drill bit that could drill through hard rock. "
Chill out, I admit i didn't read the whole article (though I plan to) but I just remembered hearing that Howard Hughes' father made his money from designing a drill bit. I suppose I was right.
Perhaps the father and son both contributed. From Wiki: Howard R. Hughes Sr.
"Hughes drill bits
Hughes engaged in various mining business endeavors before capitalizing on the Spindletop oil discovery in Texas, as a result of which he began devoting his full time to the oil business. On 20 November 1908 he filed the basic patents for the Sharp-Hughes Rock Bit, and on 10 August 1909 was granted two patents for this rock drill. Hughes had patented a two-cone rotary drill bit that penetrated medium and hard rock with ten times the speed of any former bit, and its discovery revolutionized oil well drilling. It is unlikely that he actually invented the two-cone roller bit, but his legal experience helped him in understanding that its patents were important for capitalizing on the invention. According to the PBS show History Detectives, several other people and companies had produced similar drill bits years earlier. In its initial tests at Goose Creek Oilfield in 1909 where the first offshore drilling for oil in Texas was occurring in Harris County, twenty-one miles southeast of Houston on Galveston Bay, the Sharp-Hughes Rock Bit penetrated 14 ft (4.3m) of hard rock in 11 hours which no previous equipment had been able to penetrate at all.
He co-founded the Sharp-Hughes Tool Company with Walter Benona Sharp based in Houston, Texas in 1909, and after Sharp's death in 1912 took over management. Hughes began purchasing the Sharp stock immediately and by 1918 had acquired full ownership of the company. The essential asset of Hughes Tool Company (renamed) were the 10 August 1909 patents for his dual-cone rotary drill bit. The fees for licensing this technology were the basis of Hughes Tool's revenues, and by 1914 the dual-cone roller bit was used in eleven U.S. states and in thirteen foreign countries. After Hughes Sr.'s death in 1924, his only child Howard R. Hughes, Jr. assumed control of the company as its sole owner. Nine years later Hughes Tool Company engineers created a tri-cone rotary drill bit, and from 1934 to 1951 Hughes' market share approached 100 per cent. Sharp-Hughes Rock Bit found virtually all the oil discovered during the initial years of rotary drilling, and Howard Junior became the wealthiest person in the world. During 1972 he made the tool company public and realized $150 million the day it sold.[4]"
Well..."history" is often written by public-relations flacks or outsiders like me who repeat rumors..."
Why no mention of the other heirs of Howard Hughes fortune? Howard Hughes Junior grabbed his 100% control by buying all the remaining stock from the other heirs while, quite cleverly, paying off Texas judiciary so that he would be declared a legal adult in Texas at age 19, thereby enabling his 100% scheme. I am only slightly jealous.
Some years ago I worked at a factory (Smith Tool) in Ponca City, Oklahoma that makes Hughes bits. These days they are running on a skeleton crew, and the night shift is shut down completely.
I consider this factory to be a bellwether for the economy -- when Smith Tool starts cranking out the drilling bits, then I'll say recovery is underway (for the time being).
Thanks for the post! I especially appreciate all the photos, and there is even a video you link to above.
I was wondering what the approximate timing on all of this was. It seems like tri-cone bit was quite an advancement--maybe would be reflected in the extraction data.
It would seem like the diamond coring bit had certain specialized uses, but wouldn't be quite as much of an advancement, at least for general work.
Where are diamond coring bits most often used?
You generally want a lot more information about the layers of rock that have the oil or gas in them, and so you will core those parts of the well. Cores are also commonplace in mining where we need to know both where the ore is, and where the trend of the deposit is going.
According to the secondary Wiki entry posted above, the tri-cone rotary drill bit was developed around 1933.
"After Hughes Sr.'s death in 1924, his only child Howard R. Hughes, Jr. assumed control of the company as its sole owner. Nine years later Hughes Tool Company engineers created a tri-cone rotary drill bit, and from 1934 to 1951 Hughes' market share approached 100 per cent."
Os course there might be a artifact resulting from Joiner's discovery of the East Texas Field in 1930.
I am sure even if the tri-cone drill was developed around 1933, it took a few years for it to be widely used. The EIA graph of US Oil production shows that oil production more than doubled in the twenty years after the tri-cone bit was developed.
We sputtered our way down the hole in the 1970s at 3000ft. because the crew and machine was cheaper. On the other hand, it took about twice or three times as long to get down there...
Easy drilling, and for us time was NOT money.
Cheers, Dominic
yes, but the Quantum-leap came with the two-cone drill in and around 1909 - and "that" is possible to observe in your chart , no ?
From Wikipedia on Hughes Sr -
...... and on 10 August 1909 was granted two patents for this rock drill. Hughes had patented a two-cone rotary drill bit that penetrated medium and hard rock with ten times the speed of any former bit, and its discovery revolutionized oil well drilling. (That is an order of magnitude saved and thus gained...)
I see the tri-cone drill bit as merely a logical follow-up from the two-cone.
So if the number of cones indicates some sort of efficiency gains - then we have the following logic :
2 cone ==>> 10 times better than earlier bit
3 cone ==>> 1.5 times better than 2 cone => 15 times better than pre 1909 tech. Also a fantastic gain.
I think it's fair to say that - Hughes Jr/Sr - really gave industrialization a whole new direction and order of magnitude potential possibility to aim for growth. Those bits (the two cone) are not obvious - not to me at least (!) .... when would they arrive if not Hughes ...?
It does look like the two-cone bit was quite helpful. Thanks for mentioning it!
A rather interesting post for thoise of us who don't know Jack about drilling tech. I didn't think much hard rock was encountered in oil drilling, as I think of hard rock as crystalline or igneous, and oil is found in sedimentary rock. Of course drilling for geothermal heat should largely be in igneous or crytalline rock, so being able to drill the harder stuff is probably going to become increasingly important.
I read an amusing post a few months back in Sciblogs, about a geothermal borehole that went into magma. I woulda thought they would notice the temperature increasing, but with all the drilling fluid pumped down, they were blissfully unaware. In any case magma is usually viscous enough and the diameter of the hole small enough that it doesn't turn your borehole into a volcanic vent.
Cubic Boron carbide is harder than diamond. Has it been tried?
boron carbide is both very hard and a useful neutron absorber (the 20% of naturally occurring boron that is B10 desperately wants to acquire one more neutron and become B11), so is used in nuclear power plant control rods and in some spent fuel shipping casks. However, this black material is not nearly as hard as diamond. Nothing so far known to man comes anywhere close to the hardness of diamond.
Actually graphite is harder than diamond as a polishing compound if prepared properly. It must be thoroughly degassed and dewatered with heating and in a hard vacuum. Any trace of water and the layers slip so badly that it is a good lubricant.
It is no good for use in drilling.
A neighbour is going to use a percussion drill to sink a borehole about 20 metres in sandstone. The rig can go to 100m I gather and is faster than rotary. The compressed air exiting the inline motor blows rock chips and mud back to the surface.
One of the problems with granite geothermal has turned out to be steam leakage in the 4,000 metre well casing. Critics thought the problems would be with the horizontal plumbing since fracking hot slightly viscous granite is unpredictable. First the need to stop leaks in the vertical plumbing. Then a bunch of other problems I suspect.
Percussion drilling is still based on the idea of the chisel and the chip that comes from hand steeling. The rifle threads automatically turn the bit the required angle between blows to get the chips formed. It works well in more brittle rocks, and remains the primary rock drill in mining (though power in now quite often provided hydraulically rather than pneumatically).
High-pressure fluid (above about 20,000 psi) actually drills granite quite effectively - we have used it to carve granite in the past.
My property was owned by a water well driller. The gate supports are made out of 6" well casing...topped with three cone drilling bits. So, I see "bits" each time I drive in or out.
Todd
Thanks, Heading Out, for your elegant brief on drilling tech...and bringing it to TOD where I come to read other most valued authors, too.
This bit has a number of problems under different conditions (it is harder to control in directional drilling since if the pushing force varies too much it can wander off in odd directions)...
Not so, tricone bits are virtually zero-torque devices and are much easier to control in directional drilling than PDC bits which generate very large amounts of torque.
Grin:
There are two sets of forces involved in drilling. One is the force that you use to push the teeth into the rock. This we usually refer to as Thrust. Then there is the force required to either drag the bits through the rock or cause the tricone to roll. This is perpendicular to the Thrust and can be called the Cutting Force. It is also the force that generates (or requires, depending on how you look at it) the Torque.
The one I was talking about was the Thrust force. If you are drilling a horizontal hole (and this comes from the early trials of horizontal drilling) and have either too high or too low a Thrust force, then the bit will either climb or sink, and take you out of the zone you are trying to drill.
Torque is a different animal, and, as you note there is a bit difference, in part because of the way they break the rock, between the rolling bits of the tricone, and the drag bits of the diamond.
The early days of horizontal drilling used Neolithic techniques long since abandonned. Almost all of horizontal drilling nowadays uses steerable BHA's, either motor based or rotary steerable (or even both together) and are "geosteered", ie, downhole gamma, resistivity and density measurements indicate whether the borehole is remaining in the zone of interest.
But it seems only yesterday . . . . .(retires to the back of the cave to hang up his sabretooth shirt and loincloth).
Some of what we did is still relevant, since not all of it got applied the last time around, though it has evolved a bit.
Always room for a better mousetrap! Apart from the extreme heat, one of the technological problems with EGS exploration is the necessity of drilling large diameter holes in hard rock efficiently.
http://www.grist.org/article/2009-04-09-potter-geothermal/
"A veteran of the Manhattan Project is developing technology that could make it easier to tap geothermal energy locked deep underground.
Potter Drilling
It’s the archetypal Silicon Valley story: Unknown entrepreneur toils away on a Big Idea in an anonymous office park until discovered by one of the Valley’s legendary deep-pocketed investors.
Another boy wonder CEO hatching the next Twitter or Facebook? Not quite. Meet Bob Potter, 88. He started his hardware company when he was just 83 with technology that grew out of his work on the Manhattan Project (yes, that Manhattan Project) back in the 1940s at Los Alamos National Laboratory in New Mexico.
http://www.grist.org/article/2009-04-09-potter-geothermal/
It’s all about bits, not bytes. Bits as in drill bits. Potter Drilling is developing a deep-drilling technology to tap geothermal heat miles below the earth’s surface—heat that could be used to generate carbon-free electricity.
Conventional geothermal power plants draw upon underground aquifers of hot water relatively close to the surface to create steam that drives electricity-generating turbines. The problem is that underground water currently tapped for geothermal is found mainly in the western United States. But the technology Potter is developing could drill much deeper, meaning geothermal energy could be generated nationwide.
According to a 2006 MIT study, so-called Enhanced Geothermal Systems could potentially supply 2,500 times the country’s current energy consumption. That grabbed Google’s attention, and last August the Internet giant’s philanthropic arm agreed to invest $4 million in Potter Drilling as part of its green energy initiative.
The tech twist: Potter drills not with hard-as-diamonds bits but with water—extremely hot water. (More on that in a bit.) The goal is to radically cut the cost of EGS to spread the technology to regions that rely too much on coal for generating electricity but are not suited for solar, wind and other renewable energy generation.
“It is fun to see some old dreams come true,” says Potter standing in the company’s Redwood City lab-slash-workshop in a light-industrial park wedged in between Interstate 101 and the railroad tracks. He has just pulled into the parking lot after making the 1,200-mile drive up from his home in New Mexico (with a side trip to Fresno to visit his 95-year-old brother).
Tall and lean and partial to bolo ties, Potter looks as much a western rancher as a rocket scientist. He is in fact one of the fathers of EGS. Starting in the 1950s, Potter and colleagues at Los Alamos began investigating the potential of fracturing pockets of super-heated rocks located deep beneath earth’s surface. Their idea: Inject water in the fractured rock and pump the hot water to the surface to create steam to drive a turbine. The water is then re-circulated back underground in a closed loop.
But Potter soon encountered a major obstacle to making geothermal as common as coal: Drilling as deep as six miles below the earth’s surface is incredibly expensive, presenting a host of obstacles to overcome. Even conventional geothermal developers spend millions of dollars to just drill test wells. But EGS rigs must penetrate miles of hard rock that slows drilling to a crawl. And a broken drill bit 30,000 feet underground can force the abandonment of a $10 million well.
“Getting into the drilling was forced on us in a way because that was thing that really prevented hot fractured rocks from being viable,” says Potter.
When government funding of geothermal research dried up with the crash of oil prices in the early 1980s, Potter moved on to other endeavors. But in the late 1990s he returned to geothermal, and with MIT chemical engineering expert Jefferson Tester patented a drilling technology called hydrothermal spallation. Potter then persuaded his son Jared to start a company in 2004 to commercialize the technology and serve as its CEO.
The younger Potter holds a Ph.D. in geology from Stanford University and had already started two Silicon Valley geological-related companies. Potter Drilling limped along for a few years, unable to interest the Valley’s venture capitalists to fund basic R&D on something that seemed so, well, industrial and old economy.
Then Google came calling on a recommendation from Tester. “If Google hadn’t come along, the company would have died,” says Jared Potter, 56.
What sealed the Google deal was a demo of Potter Drilling’s technology like the one I’m about to see. We’re standing in front of a contraption that looks like a prop from the original “Star Trek.” Salad plate-sized analog gauges line either side of the seven-foot-tall U-shaped device. Suspended in the center is a silver container about the size of small beer keg connected to various tubes and valves.
A technician loads a 4 x 6-inch cylinder of solid Sierra white granite into the bottom of the container. Above the granite is the drill apparatus. It resembles a round garden hose nozzle with slotted openings at the end. We put on safety glasses and switches are flipped, buttons pushed. As chemical reactants begin to heat up the water supply, a battered, second-hand flat-screen monitor attached to the apparatus shows the temperature rising—200C, 400C, 600C. When it hits 800C (lead melts at 327C), the hot water is forced through nozzle. As the sound of the machinery intensifies, the jets of water begin to fracture the surface of the granite, dislodging tiny particles of the rock.
About two minutes later, the too-hot-to-handle chunk of granite is removed and now features a round, 3.5-inch-long, 1.25 inch-diameter bore hole through its middle.
By dispensing with breakable drill bits and other components that risk failing at great depths, the Potters hope to jump-start EGS by slashing both the cost and the time it takes to drill a well, which can account for more than half of a geothermal power plant’s price tag. That drilling risk has proven a deterrent to investors who don’t want to take the chance of literally pouring millions of dollars down a dry hole.
“We think we can cut the cost by 50 percent,” says Jared Potter. That has sparked interest from such leading EGS companies as Geodynamics of Australia.
But getting from the lab to the center of the earth, as it were, is another matter. Later this year, Potter Drilling will take the technology into the field at its first test site in the foothills of the Sierra Nevada, where the company plans to drill a 1,000-foot hole. The further down they go, the greater the technological challenges, such as maintaining super high water temperatures and evacuating the displaced rock particles.
“Will the technology work? Maybe,” says Mark Taylor, a geothermal analyst at market research firm New Energy Finance. “I think it’s got great promise.”
To make the technology viable will take money. Geothermal has been something of a loser in the green energy stakes, with most private and governmental funding flowing to solar and wind companies. But the Obama administration has increased funding for geothermal, and Potter Drilling has applied for a U.S. Department of Energy grant. The company will soon need to raise venture funding to commercialize its technology.
Given that Bob Potter hashed out the initial calculations for hydrothermal spallation by hand—“I never did get into computers,” he says—any risk-taking venture capitalist’s money probably will go far.
Um!
This is a little embarrassing but using high velocity waterjets to drill through granite is not new - I did it as part of my PhD program some 42 years ago. We applied it as a tool for drilling geothermal wells back in 1976, when we were able to drill at around 1 ft/minute through the granite. We have advanced the technology perhaps two generations from that time.
But thanks for the information, which I shall pass on
Grin
HO
Headingout, I'd be interested in your informed analysis of why this technology has not been adapted after having been around all these years.
Here is Potter's summation of the advantages they claim for their technique:
"Comparative performance for hard-rock drilling
Performance Metric = Conventional Drilling Technology vr Potter Drilling’s Spallation Technology
Rate of Penetration
Average of <10 feet/hour in hard rock Drilling rates up to 5X conventional rates Improved project completion time
Bit Life
Extreme bit wear in hard rock can require costly bit replacement every 200 feet Non-contact technology virtually eliminates wear on the drill head No bit cost and reduced downtime from tripping to replace bits
Casing Requirements
Many casing intervals are required to maintain borehole stability, so expensive wide-diameter casing is used to achieve target bottom hole diameters Fewer casing intervals are required, so smaller, less expensive casing is used to achieve equivalent bottom hole diameters Lower casing costs and reduced downtime from tripping to case wells
Depth Limit
Depth is limited by the hanging weight of metallic drill strings Potential to use neutrally buoyant, composite drill strings Potential to make EGS available at depths up to 30,000 feet
Directional Drilling Capability
Ideally suited for directional and extended-reach drilling "
If Potter is correct this technology could enable EGS to become the major source of future energy worldwide rather than another minor localized player like conventional geothermal.
HorizonStar
I found this an informative article except that Howard Hughes did not invent the tri-cone bit. His partner Walter Sharp invented the bit and Hughes bought his side out after Sharp died fighting a well fire.