The Drilling Rig Part of Creating an Oil Well
Posted by Heading Out on September 13, 2009 - 11:09am
Well, there are several ways to go after talking about the pressures that develop at the bottom of oilwells. But before going on to talk about completing the well, let me first just cover some basic terms and parts that go into getting the bit to actually turn and drill the well. In other words, today I want to talk about the oil derrick and what happens on the rig floor. Trying to update this, I discover that the term “derrick” has an interesting past.
The term derrick comes from Thomas Derrick, a hangman who invented a type of gallows using a movable beam and pulley system during the Elizabethan era. During his lifetime, Derrick executed over 3,000 people, many of them with his modified gallows device, and the supporting framework for his gallows came to be known as a derrick.
Well, the ones that we are dealing with have to be a bit taller than that. The reason comes from the connection that we have to make from the rig floor down to the bit at the bottom of the hole. Because we are continually pushing the bit deeper into the ground we need to use something that we can keep extending. (From this it also follows that the top guy on the rig got to be known as the tool pusher).
At the same time, this connecting device has to be able to allow the mud to get down to the jet nozzles on the bit. The logical way of doing this is to have a tube or pipe, into which the drilling bit can be threaded on the lower end. (Which gives rise to the expression oilfield tubulars). Now, by attaching the mud pumps to the upper end of the pipe, we can also get the mud down into the bit. There is usually a special piece of pipe that fits between the bit itself and the main sections of the pipe, and this is called the drill collar. These normally have a thicker wall than normal pipe so that they can add more weight to push the bit into the rock. (see below).
Drill pipe comes in various sizes, depending on the hole that is being drilled, but for the sake of an example we might use a pipe that is 5.5 inches diameter on the outside and 3.25 inches wide on the inside. This would weigh around 14 lb a foot, and is normally used in 30 ft lengths. This length is a standard, and the pipe will have a threaded connection welded to each end, known as the tool joint. One is male and one is female, so that additional lengths of pipe may be threaded into the original piece to extend the overall length as the hole gets deeper.
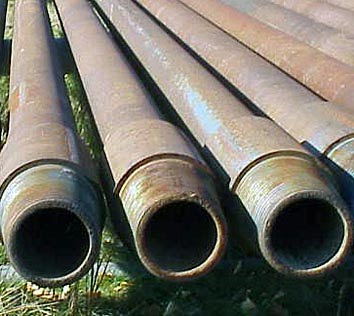
To handle these lengths of pipe, and to have them already in place and vertical before we need them, we need a handling system that can lift the pipes into place, and this tall initial support structure is called the mast. Typical modern masts may be around 140 ft tall, with the space between the legs around 12 ft. So to follow through the parts I’ll make a simple version of a mast, and then as I explain what the parts are, I can add them to the model.
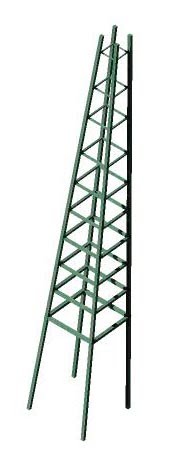
I mention the length because there are several things that control the rate of penetration (ROP) of the bit, and one is the thrust that is applied to push the bit into the rock. This comes from the weight of the pipe that is connected to the bit, and thus is known as the weight on bit. However, if you do the arithmetic, 14 x 30 = 420 lb. per length of drill pipe. So if we have one length of pipe, we are pushing the bit into the ground with 420 lbs of weight. Add another length and we are up to 840 lb. And so it continues, except that there is, for each bit and rock, a bit weight that will cause that bit to drill at its best ROP. Typically this might be around 15 - 20,000 lb depending on hole size and rock type. But we get that weight from the pipe with only 36 lengths, or a total of around 1,000 ft of drill pipe. But increasingly we might be drilling a well that is much more than 7,000 ft deep. (It is actually a bit shorter, since for the first few hundred feet the additional weight of the drill collars is needed to keep the thrust up).
To keep the bit weight at the best level to give the fastest ROP, the driller will carry the rest of the weight of the pipe through the derrick and will adjust the weight on bit by controlling the amount of lift through a block and tackle arrangement to a traveling block on the top of the drill pipe. So to the model we will add a platform at the top, (or crown) of the derrick which will have a pulley on it to feed cable down to the travelling block.
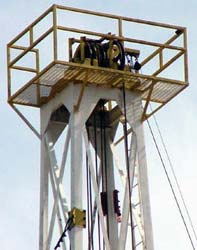
The cable that connects the traveling block to this second crown block at the top makes a number of loops between the two blocks and in this way the cable can carry up to a million pounds or more of weight.
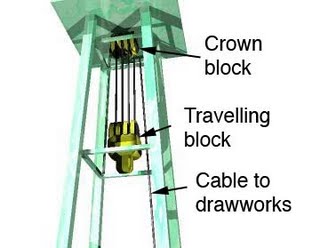
From the crown block the cable feeds back down to the reel on the rig floor where it is stored. The reel and the motors that drive it are known as the drawworks, and the driller controls the reel rotation and thus the weight carried through the cable to the derrick, to control the amount of thrust on the bit.
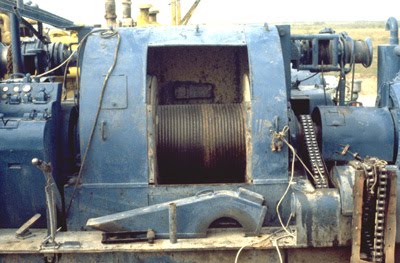
There are two other things, however, that have to be controlled. Firstly the bit has to turn, and so there must be a way of allowing the pipe to rotate. This is done by adding a swivel below the traveling block. The swivel also allows a connection to the mud system and mud can be pumped into the pipe, without the mud line having to turn.
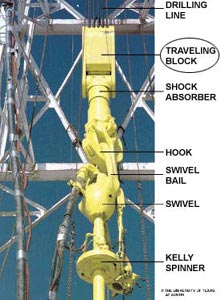
This is done through a rotary table that sits on the rig floor and a special piece of pipe (some 43 ft long), known as the Kelly, that is connected between the swivel which sits right under the traveling block, and the first length of drill pipe. The pipe is square or hexagonal and will slide through the turntable as the hole gets deeper. At the same time the shape allows the turntable to grip it and turn it, and the attached drill string that connects below it to the drilling bit at the bottom of the hole. There is a motor, generally under the rig, that drives the turntable.
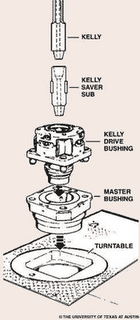
Some more modern rigs can have an electric motor at the top of the mast, attached to the bottom of the traveling block, which drives the pipe without the need for the Kelly and rotary table.
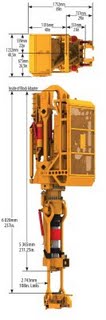
Bear in mind that after the drill bit has penetrated 30 ft (the length of a single length or joint of drill pipe) then drilling must stop. The Kelly is disconnected from the top joint, and raised while a new joint is swung in up the catwalk (from where spare joints are stored on the rig) and connected, at the bottom end to the existing string, and at the top end to the Kelly.
The drill is then ready to go forward again. While I am not up on current performance, I was once taught that a good crew cannot make more than 7 connections, or drill more than 200 ft of hole an hour. (There is another way of adding pipe that can allow a faster ROP but we’ll get to that another time). Now also remember that if the bit needs to be changed because it wore out, or because it can't drill in the rock that it has not started to go through, then the entire string above the bit has to be removed, one joint at a time, until the bit reaches the surface. Then it is replaced, and the joint in turn have to be replaced, again one-at-a-time, until the bit hits bottom again. Now hauling the string out of the hole goes a little faster than drilling, but you can see that this process, known as tripping, can take more than a day. Which can be quite expensive, especially since, while you are tripping you are not making hole, and that is what the rig is being rented to do.
When tripping the well, the drill pipe has to be held in place with slips, which are a wedge shaped tool that fits around the top of the pipe and grips it, while the connections are made or unmade.
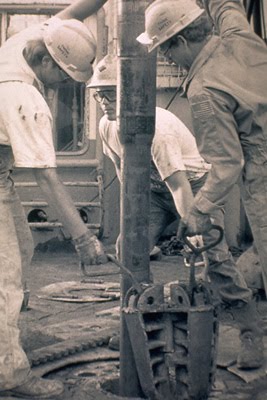
Well, this is a bit of a hard subject to cover in less than 50 minutes, and without 60 pictures, so if there are things that are not clear, or if some of my numbers aren't quite up to date please comment or ask.
Thanks, Dave, for filling in the details for us and all of the photos. You always have an interesting way of putting things!
I know you are traveling to Poland right now, so may have some trouble getting back to us with comments.
So who was this Kelly person?
ROCKMAN answered that one for me last fall, but let's hear it again.
Recommended reading: Oil on the Brain by Lisa Margonelli. The chapter on drilling is a certifiable page turner, great book altogether.
Sorry! I looked but couldn't find Rockman's answer - and I don't think I know.
I'm appalled! Also still in the dark, here's what ROCKMAN actually had to say:
To which no answer was forthcoming. Sounds like he knows the answer; I remembered an answer, anyway...This book lets us know that it was originally called the "grief stem" or "drill stem": Roughnecks, rock bits and rigs. Page 176 if that doesn't link directly there.
Hold it, here's part of the answer, from one of those maddeningly cut off Google Books excerpts: "The Kelly joint got its name from an old baseball song that many of the ..." Many of the what!?!?!? Oil -industry history - Page 105. This book was published 2005; actually, it seems to be a bulletin from something called the Drake Well Foundation, now published by the Petroleum History Institute.
Baseball song, eh?
Slide, Kelly, Slide on Baseball Almanac Internet Archive: Free Download: Slide, Kelly, Slide by Arthur Collins. Recorded pre-1910.
Thanks again HO for another great tutorial. The story continues to unfold. Lots of people must read the series without commenting so don't be disappointed at slow response.
I second this sentiment - it's hard to come up with smart Q's to a series based on just facts (this is how it works)-
But as a layman myself (on these subjects) it is a really good feeling to get this sensation of understanding something much better now ..... operations I just had some vague ideas about earlier. Again thanks HO and keep your series rolling .... or should I say swirling. Talking about swirling, now have a look at this drill-bit - are we talking EOR-on-the-fly here?!
My greatest Take Away from this series is of a mental dimension - They (oilcompanies) actually have to do "all this" for every single well attempt ... be there oil or not! And if no oil was found- that was monies straigth 'out of the window'. 'Break even' calculations exists for everything- say for instance the (Norwegian) North Sea-operations has struck too much 'almost oil' in resent years - fingerpointings have started, fresh evaluations tell that investments will be cut in half (compared to 2008) over the next 2-3 years now- according to the Norwegian Oil Directorate.
As a symptom of the Universe .. err... the above, I mean, there is a great haggle in Norwegian politics these days over a minor unexplored area up north- whether it should be opened up for oil or not .... It is the breeding waters for the largest remainders of Cod in the world . (the cod-stock filling the entire Barents Sea are spawned here and therein lies the problem)
Heading Out -
Two questions for when you get back or are able to answer.
1) For the 5.5-inch OD drill pipe used in your example, what is a typical range of rotational drilling speeds in terms of RPM?
2) It would appear to me that the torque required to turn the drill string is composed of two components: i) the torque needed to enable the drill bit to cut the rock at the bottom of the hole, and ii) the torque required to overcome the friction resulting from the drill string turning in the hole. I would imagine that the former is pretty much constant for a given type of rock, whereas the latter probably increases with the length of the drill string. Correct? Can you give us a range of the torque required to do drilling with our example 5.5-inch pipe?
I think you can see where I'm going with this: the product of the above two numbers should give a rough estimate of the power requirements to drill a well using 5.5-inch pipe. Of course, one has to add the power for pumping mud as well as that associated with other related functions. I suspect that even if you have to use a pretty big engine to drill the hole, the amount of energy expended in drilling is probably a tiny fraction of the energy content of the oil produced over even a very short period of time. However, I'd like to get a rough feel for what that number is.
Joule, I'll try to field your questions about rotary torque and total energy consumption.....
1) I have drilled with anywhere from 40 rpm to 200+ rpm on a regular basis. The bit type is the biggest determining factor. Generally, the faster you turn, the faster it drills, but if you tear up a $35,000 PDC bit in four hours, you've made hole but not money.
Interestingly, if you turn your drill pipe too fast over a long period of time it will severly embrittle it and shorten its life. I have never had it explained to me in technical terms, but there is a "harmonic balance" at a given (recommended) maximum rpm, and if exceeded, things get out of kilter and your drill pipe starts coming apart.
2) You are spot-on with the main factors determining rotary torque. The weight on bit does make a difference in an homogeneous rock. If you are running 10,000 lbs weight on bit and increase it to 30,000 lbs you will hear the engine turning the pipe bog down and observe its increased manifold vacuum/operating temperature. It takes a pretty big horsepower drain to do that. Wall friction between the drill pipe and formation/casing is big too. Hole deviation will increase the rotary torque. If the hole is near perfect straight and not too deep, you can turn the drill pipe very easily, as it is riding on ball or roller bearings (constantly lubricated) in the swivel up in the derrick. As far as a range of torque, it varies so much because of all the above factors, relating a "range" is hard to do. I just finished up a 10,700 ft test with @ 3,000 ft of horizontal lateral, and I was having the drillers use 600 ft/lbs of torque as a guideline of where to drill. This quite often gave an "apparent" weight on bit of 65,000 lbs according to the weight indicator, but that was mostly the friction of the pipe pushing its way through the 90 degree bend and along the lateral. There was no where near that much weight on the bit.
Rotary torque can become so troublesome as to hamper your ability to drill, and there are several additives you can put in the drilling mud to lower torque. Some that come to mind are diesel, crude oil, graphite, fine mica, and several different polymers, as well as glass beads.
Keep in mind that the "tool joint" as explained and shown in the pictures in the beginning post have a minimum, recommended, and maximum makeup torque to insure a high pressure seal without damaging the threads/shoulder of the tool joint. If your rotary torque greatly exceeds the "maximum recommended makeup torque" of the tool joint, the joints will be screwed together down hole while drilling and can and will damage and possibly cause immediate drill pipe tool joint failure.
Rotary torque is not a big percentage of total energy used to drill a well. The mud pumps use a bunch of horsepower when running (drilling and/or circulating), and pulling the pipe out of the hole is also a much larger horsepower requirement.
If you want a raw number to deal with, I expect a 1,000 hp (drawworks rating) rig running two pumps while drilling with 2,500 psi pump pressure will consume @ 1,300 gallons of diesel a day. If you are largely idling (such as running wireline logging tools) for 24 hours, I'd expect the fuel consumption to be in the 500-600 gallons a day. Keep in mind the centrifugal pumps used to stir the mud run 24/7 so the big generator that runs them draws most of this fuel while "idling".
Excellent questions!
Deeper
I just finished up a 10,700 ft test with ...
Wow, almost 2 miles of drill string. How long does it take to trip it?
[edit] more than 2 miles /
DeepChaser -
Thanks for the reply. That pretty much answers my question and gives me a ballpark number for energy consumption required for drilling.
One other minor point that puzzled me a bit: the threaded ends of those drill pipes appear to have a significant taper to them. This does not look like typical threaded pipe (though a plumbing pipe thread does have a very slight taper to the threads to make the joint tighter as it's screwed together). Is the reason for that taper just to make it easier to insert the next section of pipe into the one already in the hole or is there some other reason?
joule -- Another variation to the torque/horsepower parameters. I think I mentioned to you the other day the ever increasing use of downhole motors to turn the bit. Instead of rotating the entire drill sting a downhole mud motor is installed right behind the bit. As the mud is pumped down the drill pipe this energy is transfered to a rotor which then turns the bit. The drill pipe only moves vertically as progress is made. This has become a critical technology when drilling very deep holes and in horizontal drilling. It has also allowed great advances in controlling the direction of the drill bit. Even though I've done it more times then I can remember it, the accuracy we have now is hard to imagine. About thirty years ago I would give a driller a target at 10,000' with a 1000' wide cricle to shoot for and pray he would hit somewhere inside of it. Now I can drill a well to 34,000' and have reasonable expectations of hitting within 100' of the spot on the map. Horizontal steering is equally amazing. If everything is working properly I can drill a well down to 12,000' and turn it horizontal and then keep the drill bit in a 3' vertical window for a couple of thousands of feet.
All this technology has developed as a indirect result of PO. Seismic technology can now identify targets of ever shrinking size. The rule has always been that the bigger the risk the greater the target size. As the easier stuff is found early on you're left with te smaller targets and thus can only drill them if you can increase the probability of success. 3d sesimic data greatly improves the risk but at a big cost. But now having smaller targets you have to be able to hit them and do so with greater efficiency. Current seismic technology now alows us to image every deeper targets. But this also required big improvements in the drilling side of the equation.
And all this costs big bucks. As rates/reserves declined, increasing price expectations began to drive these investments. In that sense these advances would not have happened if it were not for the always increasing difficulty of finding new FF's. If the world were truly awash in FF as some cornucopians profess the billions of $'s invested in advancing all these technologies would not have been made. Every one has a right to there opinion of course. It's just that some folks put a big chunk of money behinde their beliefs. As they say: follow the money and the truth is generally apparent.
Thanks HO for the details on this subject. I will add that usually during offshore drilling, the sections of drill pipe used & stored vertically in the derrick are normally built up of three/four sections each, which makes the 'down time' while adding/tripping pipe, less time consuming. The newer derricks are now mechanized to do all this moving of pipe (no people aloft in the derrick/not so many fingers hands/heads around the potential hazards). It's quite fast & impressive to say the least.
Some offshore drilling units also have motion compensators in the derricks to counter the vessels movement from the wave action as to maintain constant (or maybe a more constant?) pressure on the drill bit. Again, impressive to observe. Thanks again for your time & effort on all.
hi dasbootcap- you sound like a non-layman to me, so a Q follows ...
Q : After a tripping-op and during re-entry, what is the likelihood of the drilling-string just starting to dig in a 'new' direction - that is, gradually leaving the original hole?
I reckon this Q is most relevant during horisontal drilling ...
paal m
Sorry but I cannot answer that, as I am an observer only (from the position of a supporting work boat at the location). Perhaps HO can articulate more on this in the future.
Q : After a tripping-op and during re-entry, what is the likelihood of the drilling-string just starting to dig in a 'new' direction - that is, gradually leaving the original hole?
I reckon this Q is most relevant during horisontal drilling ...
I'm a newbie here but have rig experience, so let me chime in on this one. The chance of deviating unintentionally while tripping in the hole is just about zero. The drill collars and drill pipe are such a "stiff hookup" that it just doesn't happen.
In order to intentionally deviate a hole (for geological reasons, junk on bottom, etc.) the common procedure is to spot a cement plug just below the intended deviation and let it set up good and hard. If the formation is softer than the cement, the bit will usually drift over to the softer digging and deviate naturally. A metal "whipstock tool" is used to "cut a window" in casing and drill out the side of the casing if required.
Hope this helps,
Deeper
I loved this clear technical exposition. It leaves me so satisfied I have no questions or comments.
Where you end up sidetracking unintentionally is when you have undergauge hole and you have to do extensive reaming getting back to bottom. So it is a good idea if you are on a directional hole to do check shots every once in a while to make sure you haven't jumped the hole. You'd think WOB would tell you when your cutting new hole but if it's soft formation and undergauge enough, it can happen. Just something to look out for.
In regard to open hole sidetrack, if it you are going around junk or if you have had a trainwreck directional job- pump cement, let harden (check your cement samples for hardness) cut a trough and then time drill in the direction you want to go. This is a long process usually starting at about 1 foot per hour and gradually increasing slowly as you go. Of course if you don't get off, another plug has to be set.
You can open hole sidetrack a horizontal well with out cement using the same process.
Whipstocks are common in re-entry work or multi lateral horizontals.
The neat part is casing the hole.
Hopefully thats next esp for the super deep ones these days.
Maybe you missed Casing a Well two weeks ago. The series can be accessed at the Tech Talk link on the front page.
Next week is "Completing a Perforating a Well". That should be interesting also.
Yep missed it dang.
Well given that it exists and people see how deep and long these wells are you can end up with a physically small well for a lot of modern wells. This limits the production capacity of the well as it acts as a natural choke.
So if I miss the completion post I'm interested in the limits of these wells as far as how much fluid can flow at x amount of pressure for a given size and length of well. I'd have to think that modern super deep wells might be limited on the number of barrels they can produce in any given day because of the physical constraints.
Question is whats the limit ?
And I'll save it for the completion article if needed but think about it.
Memm, It's a good question (which you yourself could answer with a bit of maths!(http://www.pipeflowcalculations.com/)). But presumably once a first hit has been scored it is a relatively easy and confident task to sink some parallel extra ones. I guess the source rock permeability complicates matters though: http://en.wikipedia.org/wiki/Permeability_(earth_sciences). I suspect from the usual separation between wells, that the permeability is the more limiting factor, else they'd be having wells right side by side.
[Heck, what rubbish am I writing here; see my next for a more sane response.]
Math does not tell me the relative importance of the numbers waiting on your next response. I don't know if this is really a limiting factor or not. And drilling more wells has its limits esp as they get deeper and more expensive.
Assuming that future finds will tend to be deep and hard to extract it looks like there is a sort of technical limit on the rate of extraction going forward with any reasonable discovery rate. I'd argue that despite the technical advances recently that we may well be hitting a sort of basic technical threshold on the extraction rate. For example for deep offshore wells we probably can't find develop and extract 1mbd per year from these sorts of wells maybe at most 4bmd because of the interaction of the numerous limits with this sort of technology.
As a trivial example we have had planes from almost 100 years but people in general don't own their own plane the various limits work to ensure that the technology develops in a certain way at a certain capacity.
If there are no limits then where is my flying car ?
A simple understanding of technology suggest they should have been around decades ago yet they are not.
Oil technology has similar limits I just don't know enough to understand how they all relate I think we have hit them just from reading but you would have to be and expert or probably you need a group of experts to discern if oil technology is reaching the point of rapidly diminishing returns common with advanced technology.
As another example consider mobile phones we could readily make one the size of your thumb or smaller say a ear set mobile phone no basic technical limits however usability esp as data becomes important is and issue. Same for laptops I'd say the MacBook air has probably reached the points of seriously dimishing returns as far as physical size. I suspect that as long as we have computers with screen that we won't see a lot of changes from the air in the traditional laptop. Internally things keep getting better but even here we are increasingly seeing the effects of diminishing returns set in.
Sorry for the long post but to repeat oil technology has these limits I don't know enough to know what they are and were the real problems lie.
Good points memmel. We're all familiar with below ground limits (smaller/fewer resrvoirs to find). And I would agree we're approaching the intersection of diminishing returns on tech advances. The development of 3d seismic was a true step change in finding/exploiting the deepest/smaller targets out there. But improving the depth of investigation and imaging smaller targets have reahed a practical limit. While the low temperatues found in the Deep Water GOM has allowed the preservation of oil at greater depths then normal, this is somewhat local and thus an isolated situation. There are very few areas around the globe where we could find oil at such depths let alone deeper objectives. Thus improving 3d seismic to image much below 40,000' serves little purpose. As far as advancing seismic to image smaller targets is a non-starter also. We can readily image targets that are too small to be economic today even during higher pricing periods.
As far as production technology goes we're fast approaching similar physical limitations IMO. We can now drill/produce in waters depths that represent the great majority of current/future plays. Horizontal drilling has been a big jump forward in conventional reservoirs as well as the shale gas plays. But I doubt we'll ever see any major advances in these theaters. There's certainly a good big of tweaking to do but I don't see the step-wise changes we've seen with 3d seis, DW production and horizontal drilling technology in the past 15 years.
It's strikes me that I remember similar comments about not seeing step-wise changes first back in the eighties and then again in the nineties. One failing as humans is we always think we are at the peak of learning, possibly because we are limited by our own imaginations. Just recently I was astounded at some of the improvements that are being made in seismic processing. I saw a line which was acquired a year ago to image offshore West Africa and although you could image the salt structure flanks passably there was no way of telling what was happening in the pre-salt. I then saw that same line using Reverse Time Migration and was gob smacked with how well the pre-salt structures showed up as well as a knife sharp salt wall margin, absolutely amazing stuff. There are also new techniques in multi-azimuthal seismic and Electro-Magnetics that are helping to image the details of various play types. These techniques are not just helping to image smaller plays but also image plays we never really knew existed such as the large Jubilee field offshore Ghana where EM and high end seismic processing have imaged turbidite channels that form the trap. A few years ago such techniques were beyond most of our imaginations.
I think what you really are pointing to though is that there are diminishing returns. As we exhaust the current technology the next tick up becomes more expensive and even if you were some crazy cornocopian who believed in an endless supply of liquid hydrocarbons being derived from Russian magic there will be some limitation on applicable technology unless oil prices were to rise infinitely.
I agree that we are getting to the limits of major up ticks in drilling technology. Where the advances will come I think is in cheaper ways to do the same thing. This might be in improvements to bit technology (wouldn't it be great to drill 4000m well where you only had to trip a couple of times for bit?), mud technology (what if we could deal with high overpressures without having to increase mud weight excessively and hence slow drilling and increase barite consumption)etc. I suspect improvements to completion technology might also give us access to hydrocarbons in tighter formations that we can't currently achieve with existing technology. Again the law of diminishing returns will come back to haunt you but I'm convinced the Fat Lady hasn't sang yet with respect to technological advances in petroleum exploration and production.
doc -- I suppose it's a matter of degrees. I guessing you're another ole fart as I. Reprocessing will always improve life especially as computing power improves/gets cheaper. But I was referring to very big step-change. Imagination is vital but what's the next big technology that will put in a world beyond 3d seismic, producing in 10,000' of water or drilling a 26,000' lateral in a horizontal well? That's the magnitude of change I was hinting at. basic tech that might going a long way to mitigating PO to some extent for some reasonable period of time. That's where i have serious doubts.
Outside my area but I have the same wonderings about solar, wind, etc. All the alternative techs will continue to improve. But do we see a step change where wind/solar collecting efficiency will improve 100's of % in the short term?? As long as FF prices jump up and down we'll see the alts move in lockstep IMO. I doubt we'll see any serious efforts in the application of alts widespread until we see that sort of major tech leap. Or folks are subjected to a very long period of high FF prices. But I think most now recognize the economic backlash of high FF prices and many will hesitate to advance alts in a big way as the antcipate FF price collapse along with the economy.
I'm just concerned that so much TOD space is being given over to the wackiest of sci-fi here. The notion that you can drill through a mile of solid rock to reach some oil that you can magically divine a mile down, then survive the massive pressure shock, and for heaven's sake then fantasise that you can collect some useful product and even make a profit after all that lot.
No evidence is cited that this could actually work. There are so many obvious reasons why it can't.
Can we please get back to more credible options such as satellite solar, please! Thanks.
Nice ironical take on the situation. To top it off, they act like they don't know how much is left in reserves.
Sarcasm Robin???? Having drilled a well below 6 miles last year while responsible for monitoring that "massive pressure shock" I have a somewhat different view. Perhaps you exagerate for effect.
Like you I'm all for expanding solar collection. Just waiting to see it get cost effective to the point where it becomes universally applied.
With the oil and gas leak in the Timor Sea the gas or smoke appears to be at the deck level and oil from the pipe is falling off the deck ie not being collected.
http://www.news.com.au/story/0,27574,26068874-421,00.html
However the casing failure is supposed to be at the 2,600m level though I see no gas bubbles coming from the sea bed. A second rig will try to intersect that from 2km away, suggesting a drill angle of about 45°.
The paper version of this press report is much more extensive, and suggests that this horizontal production well was undergoing seabed completion (divers in water?) protected by a downhole cement plug set above the reservoir. Well is said to have been sea water-filled at the time, not mudded. The plug appears to have failed for unknown reasons. Rather than attemp surface remediation, they all just ran for the hills. Guess you would.
G.
The compensator also keeps the strain off of the riser that connects the BOP to the platform. The riser allows the mud to move out of the well to the platform carring the fines. The shell shaker removes the fines and the mud is used again. The riser is extremely heavy and can take very little addition strain due to the motion of the platform or lateral motion from the well.
What most intrigues me is the going round a corner to horizontal. I can't imagine any way that wouldn't be (even more) dauntingly expensive and difficult. Could you give us any idea when that section will be onlined? Will you also deal with its application to THAI for oil sands?
How do they accurately steer a multi thousand foot drill "round a corner" ?? is it to do with the lubricant or more pressure on one side or ???
Also, what does it mean to spud a well?
downhole motors and steerable bottomhole assemblies. Anadrill a sub of Schlumberger makes whacks of cash doing this. The topdrive assembly that was mentioned also helps. The ability to realtime monitor the bit location through inclination and azimuth coupled with logging while drilling technology contributes to make all of this horizontal drilling a relatively easy task.
Probably I will get to round-the-corner in about 6 weeks, depending on if I add some other topics that might intervene.
Turning the corner doesn't have to be that expensive - depending on depth - though it can be difficult and very expensive to do it close to the surface if you don't know what you're doing (as with a lot of this work). And similarly longer deeper holes can and are a lot more expensive than verticals.
THAI will be a part of in-situ burning of coal and that is probably about 3 months or more away - but if there any new developments in that, then it may go up earlier as part of the normal posts on things that are changing in the industry.
Many thanks for the lucid decription. Obviously there's much more to the story but this is a great primer!
Two minor questions.
My summer job when I was in college was in a steel mill. The lowest level supervisors (between the foremen and us laborers) were also called tool pushers. Not a rig in sight.
The rigs we produced at the Lee C. Moore Corporation in the late 1970's were all set up to utilize preassembled "strings" of 3 pipe 90'long.
Jim Barbin