Completing and Perforating a Well
Posted by Heading Out on September 20, 2009 - 11:10am
This is another in the technical series in which I talk about the different aspects of getting fossil fuels out of the ground. Others can found at this link: tech talk. This link is also available on the header of The Oil Drum home page.
It would be nice, once the drill hits the oil-bearing rock, to say that you were done. That having connected the feed line from the well through a choke valve (that controls the outflow from the well), we could proceed to tie the outflow into some kind of collection network, and then we could sit back and count the money as it flowed by.
Well not quite. There are a number of different steps that we have yet to go through before we can finish what is commonly called, the completion, of the well.
At this point in the process the bottom of the well is still an open hole. And one of the first things that we do is to flush out the drilling fluid, and then clean the walls of the well – firstly by washing the remaining mud from the well down in the production zone. That means that the rock wall is exposed, just as it was drilled. There are several issues that can come about as a result of this. The first is that the rock we have drilled into can be fairly weak. This is one of the peculiarities of geology. To a degree the richer in oil the rock is, the weaker the rock will be. (And that also holds true for oil shale - of which more at a later date). Why is that?
Well let's talk a little about the rock structure, particularly in this post the porosity that it has. (I’ll talk about permeability next time). There are, simplistically, two types of rock, that oil is usually found in and for now, to make a simple generalization, I am going to call them sandstone and carbonate (as I said holding shale until a later time). Sandstone rock is made up of relatively large grains that are glued together at the edges with various different types of natural cement. The grains do not fit that well together (think apples filling up a room, and connected where they touch). We call the gaps between the grains, the pore space of the rock, and it is these gaps that the oil fills up to form the reservoir. And so we can calculate the "free volume", as it were, of the rock as the (relative amount of free space in the rock, you can get this by subtracting the weight of the rock from the weight of the same sized piece cut from solid quartz and it will tell you how much empty space there is in the rock, and thus, how much oil there could be in that volume.
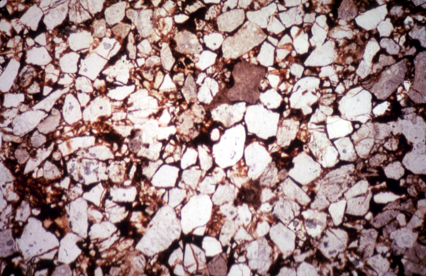
Section of sand with oil in the pores-–this is actually an oil sand, so the grains aren’t that well cemented together. (Syncrude)
So say we had a core that weighed 144 lb/cu ft and the weight of solid quartz (flint) is 220 lb/cu ft. Then only 65% of the rock (144/220) is solid rock and the remainder is what is known as pore space. Now these holes can be connected or totally separated, with each pore surrounded by a solid piece of rock. Normally the percentage given is reversed, i.e porosity = proportion of void space to total volume, or in this case 35% of the total volume is not rock. (Another picture showing porosity of a sandstone can be found here. Now in the reservoir rock this space is going to be filled with a fluid, either gas, oil or water. For now let us assume that it is filled with oil.
What I have described so far is known as primary porosity,i.e. that which is created by this initial structure of the rock. With carbonates more than sandstone there is a secondary porosity, and this is the porosity induced by rock movement and the dissolving of channels and holes in the rock by the movement of fluid over the rock through the millennia. Again put simply the oil found in a sandstone will occur between the grains of the rock. In the case of the carbonates, which normally have a much smaller individual particle size, the oil is more often usefully found in the cracks and joints formed were the rock bedding planes were created (and which can be seen in exposed rock in a lot of road cuts along the highway).
The voids and spaces in the rock are also formed from the spaces from what might have been old coral reefs, or where water dissolved holes through the rock. But sometimes the two methods of formation mix, and I would like to quote from Kenneth Deffeyes book "Hubbert's Peak" (my favorite text as an explanation of the geological case).
Fine grained calcium carbonate mud usually gets consolidated into massive limestones, usually with little or no porosity. . . . . . . .About 10 percent of ancient limestones do have porosity. . . . . . .Most massive and nonporous limestones contain textures made by invertebrate animals that ingest sediment and turn out fecal pellets. Usually the pellets get squished into the mud. Rarely do the fecal pellets themselves form a porous sedimentary rock. . . .I twisted Aramco's collective arm for samples from the supergiant Ghawar field. . . . .Examining the reservoir rock of the world's biggest oil field . . .a small part of the reservoir was dolomite, but most of it turned out to be fecal pellet limestone. I had to go home that evening and explain to my family that the reservoir rock in the world's biggest oil field was made of shit.
So there you have it. And the reason for the quote is that the rock at the bottom of our well can be very weak, and may be left in poor shape by the oil drilling bit that just passed it by. Now remember it is this wall around the hole that is the barrier through which all the oil in that rock must pass to get into the well. So before we leave it we have to ensure that it is in as good a condition to allow that flow as possible. (Hence the reason for the removal of the mud and the cleaning of the wall). We also have to isolate the production zone from the rest of the well, and we do this with what is known as a completion or production packer.

One of the problems is that the drill bit may have overly crushed the rock, so that fine carbonate particles are pushed into the cracks and pores of the rock, right around the bore. These can block the passages that will allow the oil to enter the well. And so, in order to get rid of these particles, a strong acid can be poured into the bottom of the well. This acidizing dissolves these fine particles and opens up the cracks leading out into the surrounding rock, so that the oil can flow into the well bore more easily.
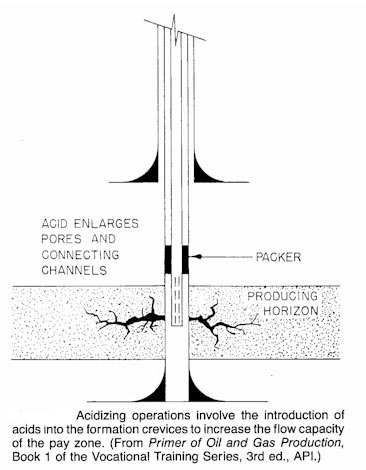
Another problem is that the rock may be very weak, since a lot of its strength comes from the oil that fills the holes within it. This oil only provides strength as long as the rock is totally confined on all sides, but when the pressure is removed on one side (think of popping a champagne cork) then the oil can flow away, taking the support for the surrounding rock with it. If the rock bridges that are left are weak then they can crush. This will cause the crushed rock (sand) to mix with the oil, which will require a de-sanding process at the surface, but it will also close some of the passages through which the oil is flowing to the well. A well operator that speeds the flow of oil out from the rock around the well, can reduce the support that the oil gives to the surrounding rock to the point that it crushes, and permanently reduces oil flow into the well. We can put in a screen that will hold the rock in place, but allow the oil to seep through slots in the screen wall.
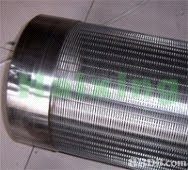
Or, to stop that rock crushing from happening and to reinforce the rock, we can pump a layer of concrete into the bottom of the well, cementing a steel liner into the rock, just as we cased the well higher up the well. The steel liner, or production casing, has, however, one problem. Once it is cemented into place, there is this hollow tube all the way to the surface, but there is no way that the oil can get through the cement and the steel into that passage.
And this is where Her Majesty's Explosive comes in. Small, specially designed, explosive charges, known as shaped charges are now put together into specifically designed charge packages, and lowered down into the well into the completion zone.
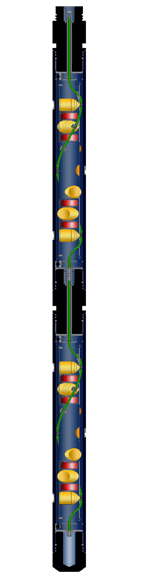
Here they are detonated, sending small jets of metal against the wall of the casing and perforating the steel and concrete into the surrounding rock. There is an animation that shows the jet being produced (see also information here) .
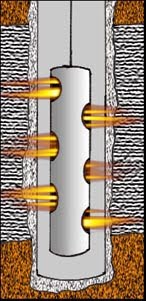
This gives the passage for the well to flow out of the rock and into the well bore. We have finally completed the first stage of our oil production.
Again this is a very simplified explanation of a quite complex process, but it moves us along to consider some of the other issues relating to how the oil now flows to the well, that will be next.
Since this is simplified additional comments and questions are welcome.
HO:
Great post, as always. What I would like to know is, was the first guy who introduced explosives into a well bore extremely desperate, or just clinically insane? To my way of thinking it's one hell of a gamble.
Again, thanks for your work in attempting to explain extemely complicated drilling/engineering techniques for the mechanically clueless (such as myself).
Pete Deer
Pete:
Probably desperate! They need to line the well to hold the walls open in weak rock, but then they have to poke holes through the walls. The first tests were using small gun projectiles, and shaped charges work more consistently and can be made small enough to fit into the space without much problem.
HO
Thanks for another excellent post. Your posts are highlighting the complexity and expense of drilling and maintaining an oil well. This is after discovery costs and before above ground needs are discussed. It is my opinion that most people have not considered how complex and expensive these processes are for each and every well. It is just assumed that oil wells produce a lot of money and most people could not even calculate how long a well must produce to pay off the set up costs, so to speak.
At present we are comparing the mature technology of oil, gas and coal return on energy and investment to the infant alternative energy systems like solar, wind, biofuels, etc and see all the complexity of these new industries that reduces energy efficiency and profitability to less than current fossil.
It strikes me again after reading your posts that psychologically it is easier to ignore the costs and dangers of fossil fuels because all the issues are literally hidden from view undergound. And unless you are an insider you don't even know how many very complicated speciality companies, like Baker Hughes or the makers of shaped charges, must exist just to have the right tools already invented and available to solve down hole operations to keep the cost down.
Whereas the alt energy systems are in plain view, literally held on high in fields and roofs, with the unique support tools and industries hardly even invented ye . Logically as more sophisticated support industries mature to help the alt energy systems the costs should come down at a faster rate than fossil fuels, if costs can drop at all in those mature industries.
NC:
The whole problem of what actually produces the power that makes the light go on when you flip a switch is not really understood by many of those that do. The sources of power that folk perceive are often as a result of public relations campaigns that bear little relation to true reality.
Consider that there are parts of the country (and world) where wind is not practical for a variety of reasons, or solar for that matter, yet to the average inhabitant of say Missouri they see only the adverts and assume that they can have it for the asking.
By the same token public relations can use either favorable or negative pictures of many fossil fuel production operations to support their side of the argument. Sadly it is often only when we have a tragedy such as the one in Poland this week that the public sees any of the personal costs that can be incurred.
The early days were kinda' hit and miss....my maternal grandfather was a "nitro jockey" for a short time around Ranger, TX. He moved on to less bloody pastures after his best friend hit a bump in the road and perforated the truck....Please know it is no longer done this way.....
http://books.google.com/books?id=5mjaZXcPEzkC&pg=PA125&lpg=PA125&dq=oil+...
I find this all very interesting, after hearing about many of the parts, but not seeing the story together in one place.
As far as you know, is the technology being used now pretty similar (in terms of equally advanced) all around the world now? My impression has been that it generally is, because of the dominance of all of the sub-contractors like Schlumberger and Baker Hughes who transfer technology from one place to the next.
In partial answer to your question Gail, I followed the article's completion screen link and it led to:
Haixing Wedge Wire Co.,Ltd.
[China (Mainland)]
Online Postings:. Products [19] Trade Leads [20]
Business Type:Manufacturer
City: Hengshui
Province/State: Hebei
Country/Region : China (Mainland)
So I'm not sure if it has gotten to backward areas like Western Europe yet and probably not so much in Antarctica </smirk>
Yes, is the technology relatively mature? I agree with Gail that it probably is, but would like to hear confirmation from multiple petroleum geologists. Thanks DIY, anyone else who knows?
HO,
Thanks for another short and clear explanation of a part the complex, multi-staged process that lets pull up to the pump and energize our little time machines (all motorized transport is just that, jets being the most powerful we commonly use).
You mentioned
A well operator that speeds the flow of oil out from the rock around the well, can reduce the support that the oil gives to the surrounding rock to the point that it crushes, and permanently reduces oil flow into the well.
That certainly points up a good reason operators won't 'just open the tap more' so to speak to increase short term production.
I have more often heard of the permanent flow reductions being caused by temporary well shut down. Is this a good place to go into that issue or will it be or has it been addressed in a different tech talk post (my work schedule doesn't always free up time to get to TOD especially in the five or six months snow isn't on the ground here).
As an aside but related to the packing rings you mentioned, I grabbed a rather homespun book on the Prudhoe discovery in the airport the other week (can't remember the name of it) and in it the author describes the day big oil was discovered on the Kenai (thus enabling Alaska's statehood). He talked of the engineer/geologist (I can't remember which and I left the book on a coffee table on the other end of the country) playing cat and mouse with the tool pusher to give the test he was running enough time to let oil percolate up through the drilling mud to show how fast it could fill a pool on the surface. The first person relation of that story was near worth the price of the book.
Luke:
I am going to do a separate post on workovers, but stopping production for a while is something that will give a boost in production, generally, when the well is restarted.
Aramco is a great believer in this and will rest their wells when they can to improve ultimate yield numbers.
The book sounds vaguely familiar, but I can't put my finger on the title, nor where I last put my copy.
Thanks HO,
Aramco would certainly seem to have enough data to know what works in its fields.
'Discovery at Prudhoe Bay OIL' by John Sweet is the book I refered to earlier. Uneven but has a lot good first person narative extracted from multiple sources and good photo sections as well.
sorry, but resting wells sounds too "renewable."
imo, a better explaination would be that in this highly heterogeneous reservoir, gravity segregation and imbibition account for the benifit of a shut-in.
aramco has claimed that their water displacement in ghawar is gravity stable. gravity stable displacement will result in a very good recovery of ooip, on the order of 65%. gravity is good, gravity is always there. gravity seems to be all but ignored in petroleum engineering lore.
how to fit this on a bumper sticker ?
I have a post on "coning" and the other problems of trying to speed up production, but it is a little ways off yet.
coning is a wellbore problem, i am talking about the displacement rate for the reservoir.
Heading 0ut, thanks for this (as always) excellent post, which comes quite in time:
I would be glad to find some information about a process not mentioned here, which is the backfilling and sealing of the annular space surrounding the well as well as the sealing of entire abandoned wells.
The background is a technical discussion about the long-term performance of Carbon capture and storage (CCS). One potential leakage path is through abandoned wells within the storage area, whose backfilling isn't tight enough to retain the carbon dioxide from moving to the surface.
I know about an incident where this happened with an underground natural gas storage: According to the responsible company (the responsible government agency had misteriously "lost" their documents) the gas leaked through the wells, which obviously had an unsuitable backfilling, so that within a year the gas was noticed at the surface.
This gas storage project was in the early 60s and the company was still in the "learning by error" mode with (one of?) its first projects, so maybe suitable backfilling was used in all later wells, but there are no evidences to be sure.
I have read that according to the
for example the state of Alberta has a regulation demanding that all existing backfilled wells have to be re-opened and backfilled again with suitable material. According to an expert the cost of doing this would probably make most CCS projects unfeasible.
My questions:
I suppose that the backfilling of an abandoned oil or gas well is only designed to prevent the mixture (saline and fresh) groundwater from different aquifers and (when indicated) the rise of remaining gas or oil under low pressure.
I don't expect that it was designed to retain (gaseous or hypercritical) carbon dioxide under high pressure nor to withstand aggressive carbon acid.
I expect this even less from the backfilling of unsuccessful dry wells.
Does anyone have information on the CCS-suitability of the typical backfilling of oil or gas wells?
Thank you very much!
If I understand you correctly you are talking about the cement that is injected between the casing and the rock wall, and which I described in an earlier part of the series .
Abandoning a well comes under a different set of rules, and I'm not close to getting to that as a topic, sorry.
Yes, I mean the cement that is injected between the casing and the rock wall as well as the well sealing of an abandoned well.
We read about the concern that natural gas get into water supplies after fracking. It would seem like CCS with its constant high pressure and its issue with acid formation would be worse.
Gail -
I tend to agree.
From the admittedly small amount of geology and hydrogeology that I do know, I think the widespread application of CCS is a very dubious proposition, particularly when viewed over the long term (say up to 100 years). Unless one has ideal conditions and a near perfect uniform formation, that high-pressure CO2 is going to sooner or later find a path of least resistance and wind up back in the atmosphere.
CCS strikes me as wheel-spinning at its worst, and I strongly suspect that the coal people know it's really going to go nowhere but just want to throw it out as a red herring to make people believe that coal is going to be 'OK'. I doubt that it's ever going to happen except for a few highly publicized demo projects.
Not to mention the fact that it takes one hell of a lot of energy to separate CO2 from all that stack gas and to then force it way down underground. CSS is hardly an elegant solution, and is in fact an exceedingly ham-fisted one. We can do better.
I know I went to a conference at Georgia Tech a couple of years ago. Several people talked about CCS, and they were uniformly not optimistic about its ability to perform as planned long term.
The problem is not only that CCS is a dead end but that we debate ineffective solutions to nonexistent problems. Climate fears disappear if you factor in Peak Oil and the resultant economic crash. Production proves reserves. Declining production is reality.
Significantly increased poverty will lead to significant suffering and early death for billions over the next 50 years. That's a real problem with no profitable quasi-solution for the presently entrenched, so they ignore it. Just as they will ignore solutions for the rest of us. So it doesn't really matter if a solution exists, you'll never hear about it in the media unless there is potential profit.
joule -- I'll tend to agree with you as far as the unlikely success of CSS. Just my knee-jerk reaction but gas injection is a very expensive proposition and it's difficult for me to imagine the public willing to pay the toll. But you probably are already familiar with my low expectation of our fellow citizens to pay the price to spare the environment.
OTOH, as long as standard protocols are observed there little likelihood "that high-pressure CO2 is going to sooner or later find a path of least resistance and wind up back in the atmosphere" IMO. As long as the injection pressures don't exceed the earth's overburden pressure they won't leak THROUGH THE ROCKS. There can be some unique geologic scenarios where it might happen but they would be rare but can be anticipated and avoided. But as others have pointed out the CO2 could easily leak out of abandoned wells with bad cement jobs/corroded casing. A likely problem in the bad old days 30 years ago. But even if that happens any wells in the area of CSS would most likely be monitored for such leaks. I once even saw an old wellhead blown into the air when we frac'ed a nearby well which should not have been affecting offsets. Sh*t happens as we say in the oil patch. But when it happens you put a rig on the offending well and spend some $'s fix the problem. Lose some CO2 back to the atmosphere for sure but no one dies. But, as I pointed out above, this is purely an academic discussion for me. Given the choice of burning more coal/pumping more CO2 into the ever warming climate or abandoning any effort to maintain BAU you know my expectations.
But when it happens you put a rig on the offending well and spend some $'s fix the problem.
This may be okay if the amount of CO2 is so big that the leakage can be detected (e.g. by pressure measurements, carbonic acid in the groundwater or even higher CO2 levels in the atmosphere. But you have to be aware that the underground "tanks" needed to take up the emissions of even only one power plants are *huge* (a three-digit number of tonnes CO2). So if there are only small leaks where the gas seeps out slowly over decades it won't be possible to notice this by pressure measurements and I doubt that these can be detected by other methods. So these seepages may evade without being noticed.
Although you may easily find the tiny hole of a flat bike tire it may be impossible to notice such a spot on a Zeppeline.
I rather suspect that the initial wells that are used for re-injection (bear in mind that it is something that folk are now doing) are going to be instrumented to a very high degree, and monitored in detail. It is the ones that are put in after it becomes a conventional tool that need to be of more concern, but (recognizing the caveats that reality will always bite you in painful places) with enough ingoing knowledge, there should be less reason to worry - about that part of the process anyway!
drillo -- I would think they would use direct detection to monitor wells. A hand held CO2 detector should ID leakage. Any volume they can't detect won't be relevent. But, as always, rules don't work if they aren't enforced. The biggest potential threat IMO would be casing leaks into shallow water reservoirs. But other then a corrosion problem with some water wells I still don't think it would add to be a big problem. But back to my earlier point: I just don't think folks will pay the cost of compressing the CO2 to levels needed for injection. I've seen cost figures for other gas injection programs and I suspect most folks don't realize how much horsepower it takes to bring those pressures up. Before I would spend much time debating leakage problems I would like to see the proponents offer total cycle injection costs. Just a guess on my part but I doubt the consumers will accept the price. Such ideas tend to look good in general discussions but hit the wall when the bottom line costs are offered.
Update
Now I found an insightful document mentioning the experiences in Alberta:
http://www.co2captureandstorage.info/docs/wbifinalreport.pdf
I picked out a few highlights:
So my interim conclusion is that leakage from old wells IS an issue for the feasibility of CCS.
Thanks for another fascinating insight.
More an abservation than a question, but the things that amazes me is how you can get the oil to flow quickly enough to be economic. It's trapped in rock, it's viscous, it has to be squeezed through a completion screen or similar into the bottom of a five-inch hole, then it has to be persuaded up to the top. It just seems improbable that you will get more than a slow ooze, though clearly you do.
BM
Actually some oils are extremely mobile, and some of the passage ways can be relatively large so that, with a reasonable pressure differential, you can get a significant flow.
Many thanks for this informative series. Its like reading really good science fiction (You don't expect me to believe this stuff do you?) I am in awe of the processes described and the level of intellectual effort that must have preceeded their use.
I do have an observation: The one advantage oil seems to have in creating these amazing technologies and methods is that the profits accrue virtually in a single place. Whoever takes responsibility to do the work gets rewarded quite hansomely in a very short time if they are successful.
Developing something like solar power, on the other hand, means entering a market where the short term financial benefit is not clear for the entrepreneur or the customer. By the time it was necessary to work this hard to get oil the market was already ravenous.
I would just like to make this general observation regarding casing-cement-formation integrity.
The Earth is alive, hence things are always shifting underground. This activity is bound to have an effect on the sealing ability of the cement over time. Sometimes we even have cases where the casing completely collapses and the well is lost due to the tectonic movement underground. :-)
jj -- Not attempting to invalid your point as it does have some merit but here's a typical scenario on how we get rewarded "in a very short time". In 1991 I began working on a old (30 years) field in La. state waters. I acquire $2 million of seismic data to analyze any missed potential. In two years (1993) (about $400,000 overhead) I develop an idea (aided by 25 years of experience) about drilling a well on the edge of the field which requires taking a new lease from the state. After submitting the leasing request we bid on the tract (1995) and come in second. The winning bidder ($1,400,000) is looking at a deeper objective. We request a sublease to pursue our target. Being a prudent operator the lease winner delays the sublease for 2 years (1997) while testing their idea. They finally decide to give us the sublease. Unfortunately the current pricing levels no longer justify drilling my well. By 2001 prices have recovered but the leases have expired. I start marketing the idea to other companies. In 2002 a company accepts my idea and takes a lease in 2003. Rigs are in short supply and thus we finally begin drilling in 2004. After 5 months we finally finish drilling the well and find no commercial hydrocarbons. Oh well...nobody is perfect. On to my next great idea. And there you have it: 13 years and no "handsome rewards in a very short time" to say the least.
This example has been repeated many thousands of time. Sometimes a little faster and cheaper process and sometimes not. And sometime successful. Like many enterprises where we see what appears to be a quick and easily attained success it has been neither. I suspect folks involved in alt development could offer similar scenarios of great initial ideas thwarted at nearly every turn. But then one day the projects gets off the ground and is a big success. And there will be folks who think what a lucky stroke to hit a home run the first time up. Right now we're one of the few companies with drilling capital and are buying into a huge inventory of stranded drilling projects. The prospect generators have spent many years and 100's of millions of $'s putting their deals together. Now we step in and buy them up at very big discounts. If one were to review our results a few years down the road they would see what appears to be an "overnight success' story. Our company is only 5 months old and already has about $100 million of in ground assets. If we're half as smart as we think we are we could be in the billion $ range in a couple of years. But as you can see our "handsome rewards in a short time frame" will actually result from many hundreds of man-year efforts and tens of millions of $'s in lost capital by others. I suspect that if we had insight to most businesses we would see a similar profile: it can take decades to become an overnight success. For that matter TOD represents a great example. I wasn't around when our founders started up but it's easy to imagine the struggle. But a year ago when I discovered TOD they were at the right time in the right place. Being in the oil patch I bounce around a lot of similar sites. IMO TOD is THE premier clearing house. I can imagine all the editors/volunteers rolling their eyes at being classified as an overnight success.
I'm in the "bidness" too.......well said!!!!!!!!!!
Simplified doesn't come close. I can imagine all those completion operations being carried out in a well for which the oil flow has kindly agreed to stop shortly after the breakthrough. But quite how can you do that while there is all that huge pressure and upward flow of oil (for which there clearly isn't a stopcock down there to seal it off)?
Furthermore I am intrigued that you have to facilitate the flow as I'd have thought the flow would tend to clear its own path. You aren't making it all up, are you?!
Scary ain't it Robin? teheheh.....
We now have the equipment and technology to perforate a static (dead) well and pull the perforating guns out of the well under a LOT of pressure. I have perforated a "static" well (full of 2% KCl water) at 12,300 ft with zero pressure before perforating and 3,450 psi SURFACE pressure after perforating.
A bit of "maths" here....that column of 2% KCl water weighed @ 8.5 pounds per gallon and the column was 12,300 ft long (or tall, whatever)....
Here's how you figure the pressure exerted by the column of water.....
Fluid weight in pounds per gallon (8.5) times the depth in feet (12,300 ft) times .052
Espressed mathematically, it is (8.5)(12,300)(.052)= 5,436 psi
Or, the hydrostatic column of fluid was exerting 5,436 pounds per square inch (psi) at the point perforated before we ever pulled the trigger.
The ISIP (Instant Shut In Pressure)immediately after perforating was 3,450 psi. So, the formation pressure was 5,436 psi exerted by the column of KCl water PLUS the 3,450 psi noted at surface. So the BHP (bottom hole pressure) was the sum of the two components, or 5,436psi + 3,450psi = 8,886 psi.
By use of a "grease injector head" sealing around the wireline conveying the perforating guns, and rated to 5,000 psi surface pressure, we were more than comfortably able to perforate this well and get out of the hole with the perf guns, rig 'em down and get 'em out of the way, and flow test the well. It was a nice well, and the FFCP (final flowing casing pressure) was 6,130 psi with the well delivering 5.5 mmcfpd (million cubic ft per day) of gas and @ 230 bbls per day of condensate (high gravity oil).
Sometimes you get a little leak, and thats why I always have the phone number for Boots 'N Coots and the local sherriff and volunteer fire department handy....and now that we are 'sho nuff high tech rednecks, I always have GPS coordinates for the location in case we need LifeFlight Helicopters. Don't need no flares to mark the landing site....mother nature provides that.........
I'm new here, and am continually amazed by this site, and the astute observations and questions put forth by laypersons. It is truly gratifying to be able to come here and read of the many projects, ideas, and ideologies expressed.
Sure hope I spelled "ideologies" right!!!
Deeper
HO
another good simplified description of a process that takes place in the worlds most complex industry.
All the comments about the layman not understanding the complexity as well as the time it takes to drill and produce, are very true, and if they were to wake up to the fact then oil prices would probably be on a parrellel with a barrel of coca cola or Pepsi.
I've managed 36 yrs in this industry and it was only 4 years ago I decided to re-educate myself and took my Masters in Drilling and Well Engineering. I must say I really was re-educated as to the complexity and I feel sorry for those who have yet to break the well barrier.
C
Thanks, Deeper:
I appreciate the example
You may have missed the bit about lining the well with a steel production pipe that the oil has somehow to get through before it can get out of the well. The charges poke holes through this and the cement that holds the pipe in place, and provides a seal, before drilling small holes out into the formation that holds the rock. They don't initially go very far - but being out of town I can't pull out some of the references that have pictures to post.
Thanks for this reply but I'm still baffled! As I (mis?)understood it, as soon as you hit the "play" you get that pressure differential and the thing blows but for the rapid shut-off device at the top. Presumably you haven't already lined all the way down at that point? Or have? Or somehow manage to line while that pressurised oil is still there? Or the pressure is first allowed to exhaust itself somehow.
Perhaps what you are meaning is at first you just collect the pressurised supply for as long as it comes, and only once the pressure is no longer supplying, you start on the completion operations to get more?
The latest with the Timor Sea blowout is the relief well should reduce the pressure within days. That drill hole will be L-shaped. The reduced pressure at the deck level on the first rig will enable it to be plugged.
http://www.news.com.au/perthnow/story/0,27574,26110032-2761,00.html
It's not clear which of the drill holes, now inverted h-shaped, will be used to extract oil and gas if it goes commercial.
"Shaped charges" does ring a bell. As we've learned from Iraq and Afghanistan shaped charges can be applied to more than just shooting an oil well. Is it likely that the guys manufacturing these for the more damaging use learned the trade by working for oil country supply firms, same stuff just a little bit bigger and heavier?
Are shaped charges a dual use technology? Is it possible that some of the shaped charges being used for combat purposes are simply the store bought variety that have been diverted from the oil field to the battlefield?
Would it be possible to track down the manufacturers of the deadly version by backtracking of those who formerly worked with the oil supply companies? Or is this technology now so universal that it can't be stuffed back in a bottle?
What sort of manufacturing facilities would it require to make the larger variety? Is it likely that such a facility could be located in a mud hovel?