Tech Talk: Burning Coal in Place, or Underground Coal Gasification
Posted by Heading Out on January 31, 2010 - 11:03am
Last week I wrote about the SAGD process and how it is used to extract the heavy oil/bitumen from the oil sands up in Alberta. What I will write about this week is the more general topic of In Situ ("in place") Combustion. I’ll talk about In Situ production as it relates to coal this week. Perhaps next week I'll talk about Toe to Heel Air Injection (THAI), a form of In Situ production which is being tested for use in the oil sands.
This is one in a series of weekly tech talk posts that deal with the technologies of conventional fossil fuel recovery. They are relatively short and so the descriptions are not provided in detail, rather they are meant so that you can understand some of the complexity of the process, and that it is not always easy.
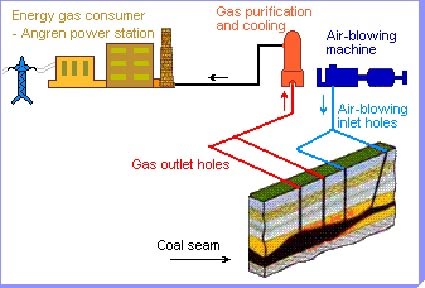
The way that we use the majority of the coal, oil and natural gas that comes out of the earth is to burn it so that we can generate heat, which in turn is then used productively, either in the generation of electricity or more directly. But getting the fuel out of the ground can be quite expensive, either in direct cost or in the amount of energy expended. And so the question, why can’t we just burn it where it is to get the energy out more easily?
With most deposits, the costs of recovery of the fuel conventionally are still low enough, and the energy recovery at the surface sufficiently high that this would be a losing proposition. But where coal seams are thin, or the oil is thick, using part of the fuel underground to recover a significant portion of what is left can be a winning proposition.
Of course burning coal underground is not always a deliberate act. Coal seams have caught fire for a number of reasons, and in parts of the country have burned for decades with significant environmental problems at the surface. Part of the reason for this is that if the coal seam is relatively close to the surface, then as the coal is burned away, the overlying rock collapses all the way to the surface, opening cracks which allow air to get down to the burning zone, in this way providing oxygen that helps keep the fire burning. If the fire is burning uncontrollably, then it becomes much more difficult to establish control since the cracks to the surface help keep the fire going, and they may not all be that large and easy to detect. (Though I have seen some big enough to hold a cow’s carcass).
My own first encounter with underground coal burning was when wandering into a mine that was something like a hundred years old, and being conscious of all the smells in the return air-way. I was told that an old part of the mine had spontaneously caught fire, could not be extinguished, but had been sealed off and left. The fire, in that case, was fed oxygen through the mined out passages around the place now on fire.
This brings up the first point, which is that coal can, on its own, catch fire. The old pit heaps that dotted the landscape around mines were made up of old coal waste, including a fair amount of un-recovered coal. When they were later reclaimed it was often found that the tips had caught fire and burned the clay into a red-brick-like material. This self-ignition is known as spontaneous combustion and occurs because coal reacts with atmospheric oxygen even at ambient temperatures and this reaction is exothermic. If the heat liberated during the process is allowed to accumulate, the rate of the above reaction increases exponentially, and there is a further rise in temperature. When this temperature reaches the ignition temperature of the coal, it starts to burn - hence the term "spontaneous" combustion.
The temperature at which the coal oxidation reaction becomes self sustaining and at which spontaneous combustion occurs varies generally depending on the type (nature and rank) of coal and surrounding conditions of heat dissipation. In poor quality coal and where the heat retention is high, the coal and carbonacous material may start burning at temperatures as low as 30-40° C.
Coal oxidation can occur in coal storage – even on a battleship and, as I mentioned, underground.
The fires are not always spontaneous--perhaps the most famous is the Centralia fire which Joan Quigley has written about in “The Day the Earth Caved in.” The coal seam outcropped at the surface where it caught fire, and the fire then moved underground and beneath the town of Centralia, PA. Despite vast amounts of effort, money and time, the fires are still burning.
This brings me to the second point. For a fire to continue to burn it has to have fuel (the coal) and air (oxygen). If the fire is totally cut-off all the air is consumed and the fire goes out. But if there are cracks through which air can reach the fire, then it will continue to burn. Thus, in Centralia, for example, as the coal burned in and under the town, it removed part of the rock holding the town where it was. The ground would then collapse into the burned out cavity, and a crack would run up to the surface along the edge of the opening, allowing air to flow back down to the fire and continue the progression.
Having been once involved in fighting such an event, it is very difficult to tell where the fire front is, and the coal does not burn in a vertical front, but in a very jagged pattern, depending on air flow and relative composition of the different layers of the coal. The air generally flows through the cleat pictured here.
But knowing that coal seams can burn in place, we still have to work out how to make that useful. Short of running water pipes down, and using the steam that comes out for power surely there has to be a better way of getting the energy, and there is.
Before the advent of North Sea gas, British towns were dominated by the Gas Works, old gas-from-coal plants that produced town gas from coal. Simply put, by heating the coal, and passing air and steam across it, one can generate "producer gas" and
"The final composition of producer gas is about 12% hydrogen, 25% carbon monoxide, 7% carbon dioxide, and 56% nitrogen; the nitrogen comes from the air used in the producer gas reaction." So that if we can get the water and air to the coal fire underground in the right quantities then we can generate a gas that we can extract, and it can be used as an energy source.
Sounds easy, right? It turns out that it is not quite that simple. From the BERR report on the Chinese work written in 2004:
Underground coal gasification (UCG) experiments have been carried out in many coal mining countries and industrial scale production has been achieved in the former Soviet Union. More than 15Mt of coal has been gasified by UCG and in excess of 50 billion m3 of gas has been produced from UCG projects around the world. Despite research and many trials in different countries, no truly commercially viable UCG project has yet been demonstrated. However, various technologies are now available which could change this situation. A shallow seam, commercial power generation project is currently under development in Australia.
The first major plant was at the YEROSTIGAZ facility in Angren, in Uzbekhistan, which started in 1961, works a brown coal deposit and is now run by Linc Energy. The plant produced 35 million cu ft of synthetic gas a day, which is fed into the local power plant.
Advantages of the process are seen to be:
* Capital investments in construction of underground coal gasification stations are less by 2.5 times as compared with those in construction of pits and quarries.
* The productivity of labour is the same as in open-cut mining and 4 times as high as in pits while the cost of final product being the same as in open-cut mining is 3 to 4 times as low as in extraction from pits.
* Hard and dangerous underground labour becomes unnecessary, working conditions are much better, and the extraction process can be completely mechanized and automatically controlled.
* Coal transportation, loading and unloading are excluded. No fuel is lost in transportation to the user and the atmosphere is not polluted with coal dust.
* There is no necessity for large areas for waste and ash dumps, and this allows conservation of fertile soil. The cost of land recultivation is five times as low as that with the conventional method of coal extraction. The mineless method of underground gasification allows exploitation of coal deposits with unfavourable mining conditions unsuitable for underground or open-cut mining. This allows more complete utilization of coal resources because non-conditioned and over-balance coal reserves can be used.
* Unlike coal combustion, the –underground gasification requires no fuel preparation, and consequently, no ash and slag disposal. No environmental pollution occurs because the gas combustion products are free of solid particles, carbon oxide, sulphur and nitrogen oxides.
The process is illustrated:
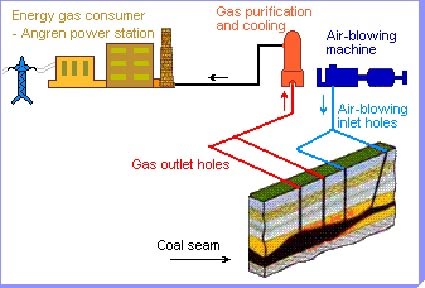
Linc has since opened the Chinchilla UCG operation with initial tests in August of 2008, running only air into the coal and recovering gas.
During its almost seven months of operation, the generator has operated very stably, producing gas of consistent quantity and quality. Gas has been produced with a typical composition (on a nitrogen-free basis) of H2 32%; CO 17%; and CH4 18%. The H2/CO ratio of 1.81 is ideal for Linc Energy's GTL process. Since commencing operation of the 3rd UCG generator, Linc Energy has gasified approximately 2000 tonnes of coal, producing over 5 million Nm3 of synthesis gas.
China began building an industrial scale pilot plant in Inner Mongolia in May 2007.
Seven ignition and production wells reached the coalbed 200 meters below ground by May 23 in the project's $112 million first phase. The project consists of underground drilling and ignition, aboveground coal-gasification power generation, and chemical production.
The plant is located at the Gonggou Coal Mine in Wulanchabu City and by 2010 will produce 1.5 million cu. m/d of syngas, 100,000 mty of methanol and methane and generate 32.4 million kwh/y of power. The city is developing a coal-chemical industry with its more than 15 billion tons in coal reserves. Methane isolated from the syngas will be used to produce town gas and generate electricity.
In Australia Carbon Energy having run a successful 100 day study has started to install a 5 megawatt generator at Bloodwood Creek.
Let me, briefly, concentrate on two problems.
In the initial concept, it was proposed that two wells could be drilled from the surface to the coal seam. In one early US test of this idea, in Hannah WY, the seam was relatively close to the surface, and for the first test the wells were set 75 ft apart. After reaching the seam, it was intended that the connecting passage between the injection well and the extraction well would be created by starting a small fire at the bottom of the seam, at the first producing well, and then by blowing air down the injection well have the fire work back to that well along the cleats through which the air was passing. By restricting the flow it was intended that the passage would be small, and run along the bottom of the seam. Then, once a passage existed, more air and steam could be fed into the injection well, increasing the size of the fire, and creating the producer gas that could be extracted from the production well.
Unfortunately the fire would not "behave" and over-burned the coal, rather than burning in the lower section, and did not otherwise go as planned. The conclusion was that this passage had to be artificially created first. The need for a long hole in the coal requires a directional drilling tool, and in the 1970s when the earlier trials were made, those were not available, particularly ones that could turn ninety degrees within the 140 ft from the surface to the seam. One had to be invented (and was). Thus in recent experiments the UK planners have looked at directional drilling from the surface to the coal, as a way of creating the initial passage, and providing paths for the air and steam to the fire and for the producer gas to come out.
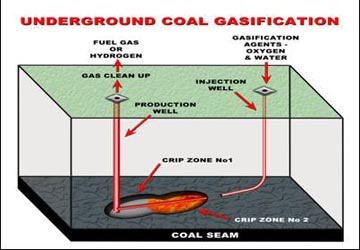
Two different approaches are being looked at in China, one of which works by creating panels in existing mines from adjacent cross-cuts, while the second uses a pair of directionally drilled holes with the fire to be initiated between them. Although as I mentioned from the work done in the US, getting that initial connection may be rather difficult, and long-term control of fire location gets to be rather tricky.
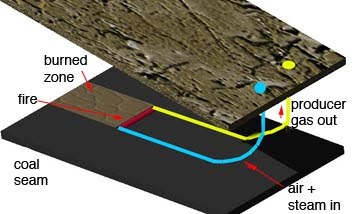
The use of the two bounding holes confines (in thinner seams) the burn to the geometry desired and gives a method of control that is more difficult to achieve in larger seams, or without those bounds.
I'm glad your illustration has the gas going to a power plant and not to households as "town gas". That is nasty stuff. Quite a few people have died from it, some by accident, some by suicide. I do hope we don't go back to using that stuff anywhere.
Considering the alternatives of strip mining and mountaintop removal on the one hand and sending miners into dangerous underground shafts on the other, I have to see this type of thing as having some merit, if we are going to be using coal at all.
Until about 40 years ago, it was the preferred method of suicide in the UK, at least for women. My wife's grandmother died that way.
When town gas was phased out, carbon monoxide from car exhaust was an alternative. With the introduction of catalytic converters this method became too slow. Legal medical drugs combined with alcohol is most common now (My wife's cousin).
Since most of the rest of my wife's family have died of dementia, she sometimes says the gas oven is the better option.
Then theoretically the huge coal deposits under the North Sea or wherever could be exploited just like the oil industry does offshore and from quite a distance so that virtually unlimited amount of coal enrgy could be made available which is in current terms just a pipe dream. We could do the same perhaps in Alberta and Orinoco. Leave the top soil alone and burn everything in place. Oil is relatively easy to get out as it is liquid but coal and similar are very difficult to remove once it is not very near the surface. This might be the future of the oil industry in 20 years when not much is left. Just take all those huge drills and offshore computer imaging equipment and find any carbon based deposits of any sort and do same drilling and make electicity/heat in situ. The factories could be put over the drill site and population moved there until the site is burned out and then people could move on.
Here's an advocacy group for UCG-GTL - Underground Coal Gasification - Gas To Liquids. Also this: Green Car Congress: Alberta to Award C$285M to Underground Coal Gasification with Carbon Capture Project for Power Generation; 75% Lower GHG Intensity Than Existing Coal-Fired Generators
In situ coal gasification = ISCG = Swan Hills Synfuel's own coinage.
Peat seams can combust as well, of course; there are crazy big peat fires in Indonesia: Peat fires drive temperatures up
Low quality coal was mined about 10 miles from my house in the Willamette Valley of Oregon, until a fire shut things down. This was about 90 years ago, I think. I was surprised to learn there were any fossil fuels in the vicinity, outside of the small Mist gas field in the state's NW corner. There were coal seams mined in the southern counties on the coast as well, and a sprinkling of wildcat wells drilled in the WV which didn't yield any oil but have been very valuable as sources of geologic information.
China has monstrous out-of-control coal seam fires, too: Anupma Prakash: Coal Fires
An important question is how carbon intensive the produced energy is. In a worst case, we totally burn the coal and all the carbon ends up the the atmosphere. This would be more carbon intensive than mining plus combustion because much of the heat is wasted underground. It is also possible that much CO2 would be retained underground, some in uncombusted coal, and some in the surrounding rock. So at least at first glance, it seems possible that this could be relatively low carbon energy if done right -and the sequestration of the CO2 is stable. I would think IGCG for shallow deposits (except under water) carries the risk of creating underground coal fires that can't be put out. But deep deposits probably can't get any oxygen, except that pumped in through the wells.
You had two examples in your article town gas (H2 12% CO 25% CO2 7%) is quite CO2 intensive, much worse than burningthe coal directly. The Chinchilla numbers H2 32% CO 17% CH4 18% look pretty good (assuming they haven't omitted CO2). If the CO2 is being absorbed underground by the coal, then I think the carbon intensity would increase as the fraction of the coal burned up goes up.
I think carbon intensity is somewhat irrelevant. While the combustion of gas in a combined-cycle facility is far more efficient than burning coal in a boiling water generator, whether the coal is extracted as a solid fuel or as a gas, the extraction and combustion of our coal reserves will nonetheless increase the overall concentration of CO2 in our atmosphere, albeit at a potentially slower rate.
As an issue of economics, however, I doubt this technology will ever be commercially viable versus shale gas. Perhaps if the continued rise in use of gas as the preferred generating fuel for our country (most of the new additional generating capacity in the US has come in the form of gas and wind) and oil prices increase high enough to justify liquefaction of gas for transportation fuels, will demand for gaseous fuels increase to the price-point necessary to spur further development and deployment of this technology.
By limiting the flow of air into the process, the burn rate may be controlled. Coal was often in a formation overlain by shale that blocks the flow of air to and from the coal, this is why coal bed methane did not leak out of the coal and is being recovered from coal deposits around the world. The hydrogen produced in coal gasification might be used to power electric generators. Great Britain has been looking into coal gasification as its North Sea gas reserves decline. Jobs and cheap electricity seem more important to many of the electorate there than other issues.
There's always the "what if".
What if cracks develop allowing an uncontrolled intake of air?
Ghung -- haven't been following too closely. But if you're concerned about surface air leaking into the subsurface formation there's little possibility. As you go into the earth the pressures increase. I'm also guessing that the combustion process would increase formation pressure above hydrostatic pressure. As far as other concerns I don't know.
Plus - if we are talking about the North Sea, there is water on top.
An empty belly trumps principles every time.
And while I do understand and support environmental cleanup iniatives of just about every sort,the only people I meet who are ardently in favor of such initiatives invariably have significant disposable income and can afford what I refer to as Bill Gates type charity and taxes-meaning that even after you give away a fortune , you can still eat lobster , fly first class,and so forth. In practical terms this means a few dollars less every month to the typical environmentalist for his 401 but no real sacrifice at all in day to day life.
It's different if you avoid the dentist because you don't have money and eat mostly fat and starches because you can't afford fruit and veggies.
The average environmentalist strikes me as very much like the professor at a small liberal arts college who couldn't understand how Mc Govern lost because after all"Everybody I know voted for him".
If anyone has need of a little insight into poor people voting republican,just focus on the fact that the recent four thousand dollar giveaway on new cars did not go to poor people,and that all the fine talk here about the profitability of highly subsidized solar installations is gall and wormwood to a working poor man if he happens to hear about them-just another gift to make sure the people with money pay less taxes .
I AM NOT saying this is a fair and accurate picture of current reality.I AM saying it is an accurate representation of the views of many working poor people.
Such people see themselves as the victims of "labor friendly" policies advocated by democrats as often as not-after all membership in the UAW EVEN IN THE CURRENTLY STRAIGHTENED CIRCUMSTANCES OF THE INDUSTRY AND UNION is as unachieaveable a dream as Harvard law school to the average man with callkuses and an acheing back.
What he sees is a man in the UAW has a big relative advantage in purchasing power that is grossly unfair to him.
Not only is that 100% right but take it one step further...
the Chinese (and India) have no UAW and they have 3 billion people to feed. They are going to focus on economic growth not the environment because that is their priority (to feed their people and stop them from revolting).
Also, add that U.S. Government workers now make considerably more than those in private industry, not even counting their excessive pensions (which they generally get to pad by working the last three years with overtime).
The U.S. won't even begin to reverse the insane course we are on before the government turns over in 2012 and even then I doubt there will be the political will to tell the American people we are on an unsustainable course in terms of medicare, social security, spending, and peak oil (although politicans will likely be speaking about the last one first).
Exacty right
Don't buy land less than 5m aove sea level. Anyone who believes that real reductions in carbon emmissions are a political possibility is dreaming.
Peak oil is currently manifesting itself as a economic calamity. This will continue for at least ten years (maybe forever). As the effects of economic chaos deepens around the world, no politician will be able to sell further economic sacrifice to their constituents in the name of the environment. Not in China or the US or anywhere else.
There will be a hell of a lot of kicking and screaming, and environmental damage, before we take real measures to address the problem. By then it will be impossible to avoid serious long term consequences.
Dan
I have been fortunate to have had some discussions with a number of the proponents of this technology in Australia.
I had initially thought that the process would be very wasteful in terms of energy loss. Not so. From the discussions I have had, they believe that they will be able to recover up to 90% of the in seam energy content of the coal, some through heat but mostly through the syngas energy content. You then pass the syngas through a combined cycle power plant(58% efficiency) rather than a conventional coal fired boiler (41% efficiency) and the overall system is in front both in energy efficiency and carbon emmissions. Arguably the final plant will also be lower in Capex hence there is a lot of local interest.
There are also a number of pilot plants being built in Australia using UCG not for supply of power generation but as a feedstock for gas to liquids. I am unsure of the economics of this conversion but the developers claim they can achieve recovery of up to 2bbl/tonne of inseam coal. Just one of the Australian resource companies claim to have 3P reserves of 1 Trillion tonnes of coal. This reserve is uneconomic from a conventional mining perspective but is quite suitable for this type of recovery. What is the oil price that makes this type of conversion possible. I don't know but I suspect that it will be a major growth industry if the world can sustain an oil price around $100.
There's other aspect of burning the coal underground and feeding the resulting gas directly into a steam powered electric generator. As the coal is burned, the process also heats the surrounding rock. Once the coal has been completely burned, the underground area of heated rock could become a source of geothermal power by simply pumping more water into the formation until cooled. The resulting steam and/or hot water could be used to generate further electricity. Doing this would also provide some guarantee that the coal fire was extinguished.
E. Swanson
The potential problem with adding water to the burned out coal is that it caused the overlying rock to explode because of the temperature differences in one of the tests we did. The fracturing around the seam made it very difficult to control where the water/steam went - one of the problems of control that is not unique to this process.
Which brings up the question of the long term stability of the rock overhead. As the mass of burned out coal and rock cools, one would expect to see changes in the structure, some what like that already seen in areas of accidental or natural coal seam fires. Wouldn't one expect to see surface water percolate down into the coal seam? As I recall, the coal seams may be overlaid by other sedimentary formations, such as limestone. Cave formation is frequently the result, for example, the Cumberland Plateau. How long must these areas be monitored for collapse?
E. Swanson
It depends on how deep they are below the surface and how thick the coal was. There are some coals that have massive sandstone rock overlying them, which normally acts as a bridge and stops the cavity moving upwards. In normal mining you would expect that the rock falling into the cavity would bulk up by about 60% so that the progression of the cavity upwards is somewhat limited by that also. But it can take decades if the circumstances go the wrong way.
One could always pump in proppant/sand.
This would appear to answer claims that coal can be extracted that would otherwise have too low an EROEI for machine excavation. The difficulties of controlling underground fluid flow also seem to apply to granite geothermal.
A good fuel gas should not contain fire retardants like N2 and CO2. I presume surface facilities that burn the gas tend to run somewhat cool and have NOx in the flue gas. The interest in not only UCG but heavy oil, methane hydrates and the like seems to confirm we have picked the low hanging fruit. It's like Mother Nature wants to keep this carbon inaccessible but like drug users who have broken into a pharmacy we want to try everything.
I am a bit skeptical of the idea that air can be used for effective UCG. Linc Energy always talks about air/oxygen. Of course the cost of oxygen($50 per ton?) is higher than air.
http://www.ucgp.com/key-facts/faq/
2CH.7(coal) + O2 -->2CO + .7 H2
You can water-shift CO to hydrogen gas
CO +H2Osteam --> CO2 +H2 and convert CO to
natural gas by methanation
CO + 3H2 --> CH4 + H2O
In the old days, illuminating(town) coal-gas was a product of coking bituminous coal. The amount of coal-gas(500 Btu/cuft) recovered was about 15% of the coal input, leaving resulting 85% as coke and coal tar,
so the amount of coal resource recovery may low for UCG.
OTOH, the link aboves says that UCG could triple cuurent US coal resources of 250 gigatons.
I find this technology interesting and worrysome as a desperate strategy for a post peak fossil fuel society. It ought to be more dispruptive for the peak forecasts then shale gas but unfortunately also much more damaging in CO2 release and thousands of uncontrolled underground fires.
HO:
This is the last bullet point from a list of advantages that you appear to have lifted from somewhere else. I wonder about the claims concerning sulphur and NOx.
Surely, sulphur content is either there, or not there, depending on the geology of the deposit. And NOx is formed by heating air which has 20% 02 and 80% N2. Or are they actually separating the O2 prior to blowing it down the hole? What is your opinion as to the validity of these claims?
And no "carbon oxide". Really? None?
I think it came from here:
http://www.eioba.com/a89138/underground_coal_gasification_in_republic_of...
Rgds
WeekendPeak
I also have the same question (CO2 produced?), and another quote leads to another question:
What is the rest of the gas volume composed of?
The economics are the most impressive aspect of Linc Energy's Underground Coal Gasification with Gas to Liquid fuel synthesis. See Linc Energy's Sept. 9, 2009 Presentation, Slide 4
i.e. $37/bbl lower costs than above ground coal gasification.
$30/bbl production cash costs with say $75/bbl sales gives 60% gross margin - not bad for a commodity product!
Tell me again why we are transferring fiscal sovereignty from the West to OPEC via oil payments- to fund Jihad? - When the USA, Australia, China, Russia have huge coal resources?
See Linc presentations
On Feb. 1, 2010 Linc Energy slide 4 is highlighting Global Oil Production Peaking.
I want to believe brother, but my faith is flagging.
A classic smoke and mirrors tactic is to take two economically non-competitive processes and combine them into a profitable enterprise. If UCG provides the competitive advantage, why aren't they producing electricity? They could put every other electrical generator out of business. I suspect their numbers are bogus.
Linc partnered with Syntroleum for GTL. I was facinated with Syntroleum a couple of years ago, and spoke with the Syntroleum CEO at NAPE. I asked reasonable, Oil Drum type questions (which I don't remember), and left the meeting shaken. He had no grasp of the numbers. Regretfully I put Syntroleum in the snake oil category, where it remains. Any partner of Syntroleum sells snake oil.
Wikipedia says Linc Energy is involved in a
So they can burn coal out of the ground, produce electricity, convert it back to coal with photosynthesis, and bury it at an energy and financial profit. Um, why not skip the coal?
The hurdle is high, David. Dreams are dangerous in a declining world.
Cold Camel
I wonder what sort of flow rates you'd get out of performing the Fischer–Tropsch process normally versus this way. Could this continue BAU?
An excellent question with an unsatisfactory answer. I just do napkin numbers, but you are suggesting mitigating the decline of 40% of our energy consumption by ramping up 25% of our energy consumption. We would need a coal growth curve that would make China's pale in significance. CTL (or CTG-GTL) as we know it today is perhaps 50% efficient (direct conversion is 70% efficient but does not work yet).
Could it be done? Perhaps. But more importantly, is the world trending that way? I've been watching for a growth in CTL (CTG-GTL) for 5 years and the answer is no. It's smoke and mirrors. Expect to see and hear more.
I'm a cynic and a pessimist. CTL is one alternative that I think could make a difference during the decline. But it seems that politically, economically, and energetically we're not headed down that path. I would love to be wrong.
Many pundits place faith in a dramatic change coming to the rescue, be it CTL, GTL, Nukes, Conservation, Technology, CCS, etc. In the past, I have hoped for such a saving also. But follow the trends. I've learned that betting against trends is a losing proposition. The one trend we know is going to break is the exponential oil consumption. The rest we should expect to continue. And the rest of the trends mostly make things worse, or don't make a significant difference.
Coal production in the U.S. is declining due to the economy. If your world view were correct, some of the excess (is there any) coal should be directed towards a few CTL plants that can lock in future coal prices and oil prices, and profit from the difference.
This is the monkey in the room. Coal and gas prices are low far into the future, and oil prices have been up to $100/bbl. If these technologies existed, massive money could be made by converting one to the other. It could happen in China, Iran, India, anywhere, but no.... Sasol came to be due to political reasons, not energetic reality. So it appears that energetic reality is not going to force us to save ourselves.
Cold Camel
In the ISCG process, if the coal seam is thick and big enough, once a lot of the carbon has been removed in a large area, what prevents this whole area from eventually caving or sinking to fill the void or cavity ?
See my comment above, but if the seam is thick enough the subsidence will migrate to the surface. However if the seam is deep the ground movement will be over a larger area and it is only on the edges of the subsidence trough that significant damage usually occurs. However if the seam is closer to the surface (Centralia comes to mind) the effects will be more severe.
Here is a link to a web page about Centralia, a Pennyslvania town abandonnned due to a still burning underground coal fire. http://www.offroaders.com/album/centralia/centralia.htm
I'm also back filling on the tech talks and have a question about the drilling phase. What would happen if drilling hits a significant void like a kart cave system-I'm thinking particularly of the lining process and how concrete is forced out the bottom of the pipe fill between the liner and the shaft. Any suggested resources?
Sionnac -- Don't have any specific references but what you're describing isn't unheard of when drilling especially in carbonate rocks. When drilling we normally keep the effective mud weight at the bottom of the drill pipe at a level sufficient to hold back the pressure in the rock. When we drill into a large void the drilling mud can quickly flood into it. We call it lost circulation. In addition to making drilling difficult or even impossible it can be dangerous if there are hydrocarbons present. With the mud column sucked away the pressure in the rock can push those hydrocarbons to the surface very quickly. This can lead to a "blow out" that could explode/burn. One solution is to pump LCM (lost circulation material) down the drill pipe. Usually some sort of fine fibrous material we hope will plug off the pores/holes and keep from losing any more mud. In a very bad situation we might run casing to the top of the lost circ zone, set a plug between it and the LCZ, cement the casing and then reduce the mud weight so we can drill thru the LCZ. Even if that's successful we then have to run another sting over the LCZ because we'll need to raise the mud weight to drill deeper.
Easy to imagine how this can run the costs up. And since wells are designed to run just so many strings of casing a well might not be drilled to total depth if you have to do such unexpected casing runs.
cisco exams
The 17% to 25% of CO in the syn gas referred to above is carbon oxide and will burn into CO2
What we are doing here is a gigantic experiment with planet Earth. It's like 100,000 of asteroids hitting Earth and setting oil, gas and coal fields on fire, releasing all the CO2 which was geo sequestered when the Earth cooled down enough for us to develop civilisation. We go straight back to Jurassic Park.
http://www.abc.net.au/science/crude/
http://www.pacificecologist.org/archive/unchecked.html
The only justification for burning more coal is to use the energy for the manufacture of energy systems which allow us to get rid of using coal.
If we don't do that we'll fall down the energy ladder:
Diminishing Returns of Fossil Fuel Energy Invested
http://www.crudeoilpeak.com/?p=909