Tech Talk: Early Mining and Transportation of Coal
Posted by Heading Out on April 25, 2010 - 10:28am
On the 18th April, Ugo Bardi posted a piece on The Oil Drum discussing some of the dark sides of coal mining. In particular he started with one of his favorite paintings 'The Riverbank' by Telemaco Signorini. He ties this picture of men towing a coal barge into a memory of his earlier life. And so, from the other end of that supply chain, that brought coal to Florence, today I am going to talk about the early history of coal, but from the region around Newcastle, and further north up by Alnwick, which is where my coal-mining ancestors came from.
When I saw Ugo’s painting I was immediately reminded of the movie “1612” which has, in a more modern recreation, more than five men hauling a boat.
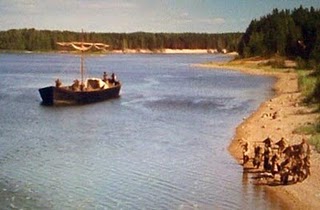
The commentary that comes with the DVD makes some point of the difficulty in hauling the boat, even though it was relatively small and there are more than twice as many men as Ugo portrayed. It was also unladen.
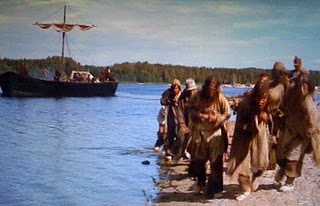
Though the crew look strong, they are after all actors, and are attached to the boat by a harness of ropes that it likely take more time for them to learn to properly operate than they had for that shoot. (As one of the comments on Ugo’s post noted, this scene could have been taken to reproduce the Russian painter Ilya Repin’s painting “Burlaki” which it emulates).
Ugo also deals more with the political constraints in the coal trade after 1860. Since I am more concerned with discussing reserves and methods of mining and the more technical considerations, I am going to start a little earlier in the use of coal, when it was mined in the UK, and some of the early practices.
When coal was first used, the legends have it that it was collected along the sea coast near Tynemouth in the North-East of England, and taken to the local priory and the rights to the coal were given to the monks. (The scene is illustrated in the movie “Nine Centuries of Coal.” (Which if I understand the BFI rules you can download if you are at a British University or school).
Coal was used to provide the fire for the local lighthouse at Tynemouth until about 150 years ago. The monks did well by their ownership of the coal rights, by 1281 they were shipping the coal down to London where it brought nineteen shillings a chauldron. (There were 20 shillings to a pound, which is currently worth $1.44, though the value has historically been higher). A chauldron was a wagon that would hold around 80,000 cubic inches of coal or just over 45 cu. Ft. of coal, or about 1.7 tons of coal, when it was mined. When it got down to London the measure changed so that while, by one definition, a chauldron was 36 bushels, but
8 chaldrons at Newcastle, makes at London about 15 chaldron.
The unit was abolished in 1963.
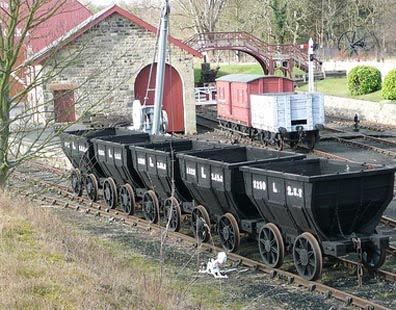
So we know that coal was heading down to London, where King Edward (because the fumes apparently sickened his mother) banned it, with the threat of torture and death to those that used it. (This is the king that had Wllliam Wallace, as played by Mel Gibson in Braveheart, chopped into bits, while alive, so he generally wasn't someone you wanted to mess with). But is was sufficiently cheaper than the wood alternative that the ban had little effect, and coal has been a major fuel in the United Kingdom ever since.
The king, incidentally, was compensated in other ways, since a royal duty was imposed on the mining and shipping of coal, that brought in a large income over the years. In 1818 the mines were estimated to produce 15 million tons a year, for domestic use, with additional amounts used by industry. The duty was 9 shillings and four pence to London, and 6 shillings to other ports in the UK. And this brought in a revenue of 570,066 pounds in 1816. Some 2.25 million chauldrons of coal were shipped, roughly half of which originated in Newcastle. The coal was generally taken by rail, though hauled by horse until the invention of the locomotive (by a local miner), down to the river where equipment known as “drops” were used to swing the chauldron down to the collier for unloading.
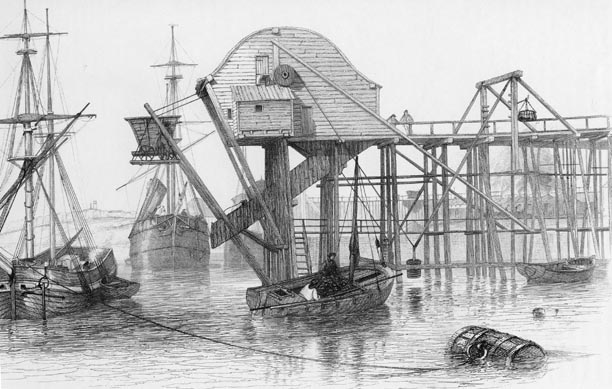
The staithes includes the short pier and feeds to the drop.
At its extremity is fixed the drop, consisting of a square frame hung upon pulleys, and counterbalanced by back weights. The loaded wagon, together with the square frame, descends by its own gravity to the hatchway of the vessel, delivers its coals, and, in turn the empty wagon is returned by means of the balance weights, the motion heing in both cases regulated by a brake wheel. A man is lowered down with the wagon , whose business is to unhasp its moveable bottom, and thereby let the coals drop into the hold of the vessel.
The drop was patented in 1800 by Wm Chapman. A tapered spout led the coal into the hold of smaller keels (the boats used to carry the coal out to larger ships). The main coal mined came from the Bensham and in 1836 93 ships carried some 15,519 tons of this coal through the staithe at Wallsend to London, where it sold for 7s 9d a ton, while one ship carried 318 tons from the Bensham Wallsend, and it sold for 8s 6d a ton. (Personal note – I have worked in the Bensham seam, albeit some 125 years later.)
Mining had progressed by that time from the initial collection of loose coal washed up on the beach (sea coal) to mining it where it outcropped, and then mining back into the seam outcrop from the surface, and this often meant that the tunnel that was mined sloped down into the ground. The dirt that was mined out was dumped at the entrance to the tunnel, and often created a small narrow feature on the ground, a tip, some of which can still be seen today. Our family, for example, used to be coal miners at Eglingham. This is a small village found in the North East of England, not that far from the Scottish border.
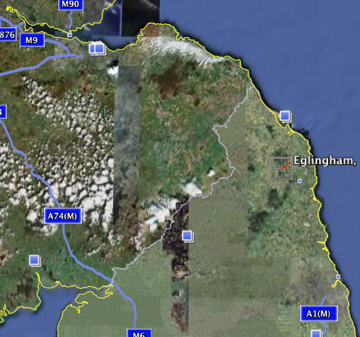
I have marked an overview of the village with a couple of arrows to show where the two tips were that I have walked around (and where my ancestors no doubt worked) on an overall view of the village (using Google Earth) which is at the bottom of the picture. Given the fact that I am going to show you that it was a mining site, it was wryly amusing to see signs in the local parish hall asking for action to protest the location of wind turbines on this "pristine English countryside."
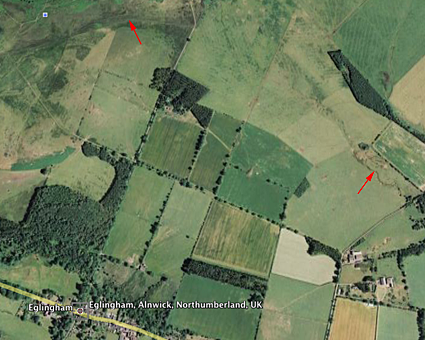
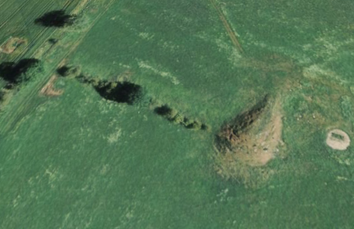
My aunt (the Teacher) had done some research on where we lived, and this was not down in the current village but up where the top left arrow points, and where all that is left of the houses are circles where the gorse grows, but where rabbit warrens have brought up small pieces of china, and other remnants of the time that folk lived there, only a couple of hundred years ago.
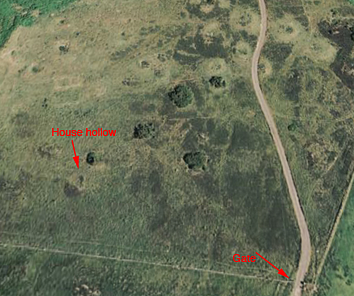
In those days it was pre-mechanization, and the miners used only a pick and a shovel to break the coal from the solid. It was then put into woven baskets called corves, that were dragged to the surface on a wooden board, either by younger boys, or by women. The board would slide up the tip, and could be dumped before being dragged back underground. The tunnels were driven to the height of the coal, which in the area may have been somewhere around 4 ft 10 inches (with an interbedded layer of stone that ranged from 3 inches to 2 ft thick) or 5 ft 8 inches, (with 3 ft of interbedded stone) not the richest of workings. It was only after some years, and larger mine developments that the baskets went from being carried on folks backs, or on these boards, to being put on flat cars and moved by rail.
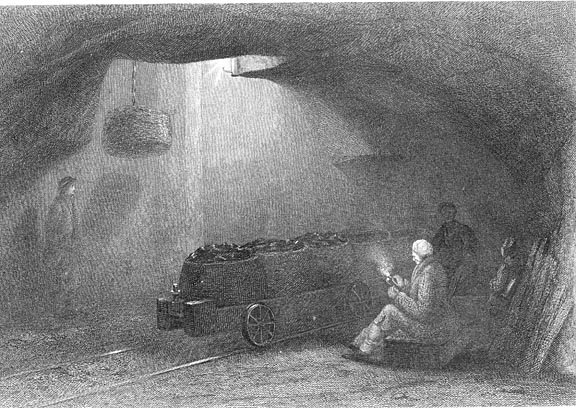
Stephenson, who invented the Rocket, the first locomotive as a way of hauling mine chauldrons down to the staithes, began his working career by weaving canes into these corves in a pit yard.
In these small operations, with all the excavation from the initial tunnel into the side of the hill, the coal was mined by individual workers, or families. The miner would work with a candle as a light, and that would be mounted to a wooden post that he would use to hold the roof up.
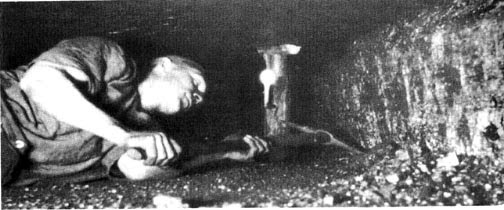
Laying on his side, he would then take his pick and cut out a slot at the bottom of the coal. This undercut, perhaps 3 ft deep, would be cut along the total face of the coal, before the miner would start to work up. Depending on the size of the tunnel he may also make a vertical cut to create a second free face. (You can see some of these markings in the walls of old stone quarries, and in the mines under Bath in the UK, and the salt mine at Wieliczka in Poland). He would then break out the coal in individual lumps that were several inches in size. (4-6 would be ideal). If he used the joints (called cleat) and the bedding planes of the coal, then this was not too difficult to do, and so he could mine out several chauldron’s worth of coal in a shift. In the measurement of the work he did using a modern measure it would take as little as 4 joules/cc of energy to break out that coal.
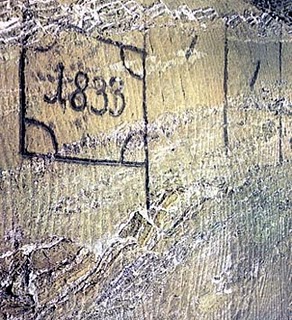
A typical shift would be around 8 hours, but it shrank, so that when I went into the mines it lasted only 7.25 hours. As well as mining the coal, the miner had to hold up the roof, and, if there was a roof fall repair it. But of all his concerns the most prevalent was that of gas. Remember both that he had to breathe, and that coal emits methane, or natural gas, from most seams. The methane will burn, or in the right concentrations in the mine can explode. And when that happens it consumes all the oxygen, so that even if the miners aren’t in an area where the explosion happened then they may still die as the de-oxgenated air circulates underground.
Initially the miners would work only a short distance into the outcrop and though the mining site here was worked at least from the early 1700s, in the south of England miners had already learned to sink shafts and to mine out from them – but I will get to that next time.
Thanks, Heading Out!
In many ways, this post is an anachronism on The Oil Drum. What it says to me is
1. Coal mining was very different, 200 hundred years ago, or even 50 years ago.
2. We can't go back.
If for some reason, current technology fails us--for example, replacement parts aren't available for some high tech machines, or we can't get enough oil to maintain mountain top removal, then we can't go back. The methods of years ago didn't allow us to mine nearly as deeply as we can today. The amount or reserves available depends very much on the technology available at a given time, and these reserves would be very much smaller than we have today, it something interferes with our current production methods.
Some may ask if we could go back to an intermediate step--for example, coal mines completely powered by coal. One of the issues I see is time--just to put together the new (old) approaches. Another issue I see is likely higher cost, leading to Jevons' Paradox in reverse. (But so is going all the way back!) A third issue is that whatever causes us to lose current technology is likely also to make going to an intermediate technology much more difficult. For example, if our problem is failing international trade, we are so dependent on imports and expertise from around the world, that it will be difficult to make, for example, high quality steel alloys, with just local materials (or to do enough importing to make the system work).
We are reminded by the recent explosion that even with our current high tech ways that accidents still happen. If we have to go back, even partly, accidents are likely to be more and more of an issue. We won't appreciate our current technology until we start to lose it.
Gail -
You seem to express doubts about the concept of coal mines completely powered by coal. Well, since a lot of the underground mining equipment is electric, to some extent this is already taking place (depending on the mix of coal/natural gas fuel the local utility is supplying). Whether the electricity comes from a utility or from a captive onsite power station is of little importance.
Now, I am assuming such is the case, because I find it hard to visualize how one can safely operate internal combustion engines in the confines of an underground mine without an elaborate force ventilation system solely for the removal exhaust the combustion gases. Not to mention the danger of an obvious ignition source.
(Heading Out: am I correct on this, or do they actually use diesel equipment underground?)
Regarding our inability to make high-quality steel alloys in a period of failing international trade, what specific materials are you referring to that we can't get from either the US or Canada? Nickel should not be a problem. I believe the US imports a good deal of chromium, but that could be more of an economic consideration rather than a total lack of domestic chromium ore deposits. Vanadium? This is also an area where substitutions are possible.
As far as losing technological expertise, steel-making technology is quite mature, well understood, and hardly proprietary (in its most basic form). So, I don't think it realistic at all that we are going to wake up one morning and find out that we no longer know how to make things like alloy steels and other essential materials.
I would go so far as to say that with the careful selection of the proper technical textbooks, handbooks, manuals, and data complications of an amount that would fill a few good size bookcases, one could start over from scratch and reproduce most of our current basic industries. Of course along the way there would a lot of mistakes made and a lot problems encountered, but this is hardly a case of some sort of 'sacred knowledge' being irreversibly lost forever.
In many respects, technological know-how, not unlike money or oil, is rather fungible. Which is why it is very difficult to maintain a truly proprietary position in those industries making basic materials.
Diesel can be used in some mines, it is much more prevalent in metal mines than coal, the main issue at the moment deals with diesel particulates.
My coal-mining experience is rather ancient -- a vacation job with the NSW Joint Coal Board fifty years ago. But the one day I spent underground impressed me with the efficiency of the operation. And it was effectively all coal-powered.
All underground and surface equipment at the mine was electric, and at that time all the power generation in the area was from coal. In fact, the mine was dedicated to supplying a single power station. If I recall correctly, the mine produced around 1000 tons of coal per day with a total workforce of less than 15. Two underground crews worked underground, one preparing a face for blasting, and the other mining the face which had been blasted the previous day. The coal seam was about 12 feet with one or two shale intervals of an inch or two.
The preparation consisted of undercutting the seam with a giant chainsaw, then drilling a pattern of holes into the face, to a depth of (I think) about 12 feet. Then dynamite was loaded into the holes, and the charges wired for detonation. At the end of the day, after all men were out of the mine, the charge was detonated. This crew was (I think) five men.
The other crew brought the broken coal from the previous day's blast to the surface. One man operated a "continuous miner" which scooped up the broken coal and conveyed it out the back of the machine. Here two electric shuttle cars filled up and took the coal to the conveyor belt to the surface. A single miner with a jackhammer broke up any excessively large pieces as they landed on the conveyor belt. The total crew actually doing the mining was four men.
The day I went underground there was another crew of two men and a horse cleaning up a fall from the roof.
In addition to these eleven or so men underground, there was the mine manager and his secretary, and a single operator of the coal washer.
This mine did use diesel trucks to deliver coal to the power station, but the mine itself was completely coal powered in that it was all-electric and the electricity was coal-powered. Of course, the explosives used may have been manufactured using oil, but they were quite a small part of the energy input.
So fifty years ago a mine could be operated without direct oil usage. I'm sure the same thing could be done today.
Two remarks, both tossed out for discussion.
And for a generation Illinois and Kentucky coal was vulnerable to the thick seam, shallow, low sulfur coals of the Powder River Basin, since the higher sulfur of the Eastern coals was more expensive to clean up in the power stations.
mcain, at the risk of nitpicking, I have to call you about using Stirling generators. There is only one industrial Stirling engine (30kW) available today, and at huge cost, and requires very high tech manufacturing, and hard to produce gas like Helium or Hydrogen. If the scenario ever plays out, it would be steam engines that make a return, far simpler to make and operate. Despite all the attention given to Stirlings in recent decades, there has never been a successful scale up to over 100kW. They are no better than steam engines, just more expensive and less practical.
That begs the question of the need to scale to over 100kW or even 50kW. Iirc the Swedish Gotland Class subs are equipped with twin Kockums Stirlings each producing 100kW... admittedly a very specialized application. Several years ago in a naval exercise in the US one performed admirably but was built at a fraction of the cost of nuclear subs.
Well, that's a fair question about scaling up, and I am a proponent of small scale generation, but Mcains comment was specifically about "honking big" equipment. Why build hundreds of Stirlings, when for less $/kW you could build tens of steam engines. There is no machine yet built that has a better operational record, for longevity, than the stationary steam engine - there was one in Britain, i think, that ran continuously for 130 years! The (reciprocating) steam engine is a great machine, and can be made reasonably efficient. Oil engines are more efficient, and steam turbines offered greater power densities, but the steam engine was to the 19th century what the ICE is to the 20th - ubiquitous.
Great for the Swedish army, who, with a military budget did develop those Stirlings, but even with that head start, those models have never made it anywhere near reality. They are to steam engines what fuel cells are to ICE's - expensive, fragile and unproven.
Stream engines worked just fine before, they can do so again, if called upon.
Somehow after hearing the praises of Stirlings sung for a life time,I have yet to come face to face with one in actual use.
We will not see commercial adaptations of this technology anytime soon except concievably in concrntratin g solar plants where an extremely high heat can be achieved on the hot end,or maybe at locations where a lot of fairly hot waste heat is available.
They look simple but actually building one at a reasonable cost that is capable of a useful out put is apparently almost impossible.
It should not be forgotten, that just 100 years ago, the prime mover, of choice, for electric power generation, was the gas engine, fuelled on manufactured coal gas.
By 1900, it was realised that the limited efficiency, and fuel consumption of the reciprocating steam engine was seriously affecting the profit of the factory or power plant.
Banks of large gas engines were used, often 1000hp per engine to drive alternators.
Ludwig Mond, a notable industrial chemist of the day, devised a process for producing consistent quality gas, from the poorest grades of waste coal.
His slogan was that a pound of coal, produces 1 horsepower for 1 hour.
This represents an efficiency of some 16.4%. Gas engines could be left unattended for several hour's, which reduced the labour requirement compared to steam plant.
A fascinating, illustrated book (as pdf) written in 1903 describes Mond's process and its application to industry:
http://www.archive.org/details/mondgas00woodrich
Gas engines continued to power industry up until the 1940s.
After about 1914, the steam turbine had become sufficiently developed to allow it to take over from the gas engine for large scale electricity production.
2020
Very nice post, HO, thanks! The history of coal mining is incredibly fascinating - it is a mirror of our own age. We have forgotten most of those times, but things haven't changed so much. One thing that has always struck me is how efficient the system could be; "efficient" to the point of being cruel to the extreme. There are some stories about early British coal mining that have stuck in my mind. One was of the girl who had the job of opening a door everytime a cart pulled by a donkey would pass by. The door was located somewhere inside the mine and it was dark. Now, the girl wasn't given a candle - she stayed all the time in the darkness, except when the cart arrived. The cart had a candle; of course the donkey had to see where it was going. But the girl didn't need to have a candle. Why waste a good candle for a girl? In the darkness, she didn't have to do anything and when the cart came, the candle of the cart was enough. So, you see? Maximum efficiency; even if that meant keeping a girl in the darkness most of the time. That meant optimizing coal's EROEI, I suppose!
By the way, those picture you showed of collier ships being loaded; there are equivalent ones of collier ships being unloaded in Leghorn, in Tuscany. I had found those pictures on the web, but I can't find them any longer. Maybe later.....
Thank you Heading Out. Interesting history.
Thanks for the comment, Ugo:
I think it was my great-great-grandfather who started his pit life as a child doing things similar to those you describe.(The laws in the U.K. changed in 1842) but I don't think in the UK we used many donkeys - mainly pit ponies (Welsh predominated I think). I have seen photos of oxen used in American mines.
This also highlights the child labor that was key part of the coal mining industry. Coal mining was a brutal business of manual and animal labor. Work conditions were very bad, disease and accidents were high, and pay was poor.
Did people want to do this work as an alternative to agriculture, or were they forced to (by the enclosure movement etc.)
I think many of us view Karl Marx as a quaint anachronism, but at the time he was writing about the urgent reality or the Industrial Revolution.
One topic that has not been explored on TOD is the modern political systems - liberal western democracies - which arguably are supported by huge surplus of energy.
One could argue that western democracies can only flourish in an industrial society powered by oil.
How will our political systems change when our energy base shifts?
“Coal mining was a brutal business of manual and animal labor. Work conditions were very bad, disease and accidents were high, and pay was poor.”
People will do any job to fed their children and have throughout history. Recently a neighbor had his septic tank cleaned out, I met a truck driver carrying hogs to the market (boy did he stink), there’s a local slaughter house in town (boy does it stink), and there’s hundreds of dangerous stinky jobs no one wants to do. Once while wiring a single wide trailer and found myself eye to eye with a dead cat. I’ve seen mice, rats, snakes, and raw sewage under peoples homes. It takes a brave soul to go down in a black pit and dig. Coal has been an important source of energy and will continue to be in the future. I appreciate the hard work of the miners.
hotrod
Conditions depended very much on the mine. Seghill and Hartley, for example, were quite warm and dry, and as long as there was light it wasn't that bad - especially on a cold winters day at the surface. But at Bardon Mill, which mined under the Tyne, the conditions were wet and thus a lot less pleasant.
There was a lot of camaraderie among miners, good since it was such a team working job, as I will later describe. But then I worked in the mines after nationalization, and there was a lot less pressure and greater care for the work force by then. Though some of the coal companies, Ashington being an example, were reputed to be good to work for.
Indeed, I recall in the late 1980s, when many of the remaining UK coal mines were closing down the paradoxical view from some of the miners summed up as:
"My grandfather worked down the mine, as did my father. When I started down the mine, I expected my son to follow in my footsteps. Now that the pit is closed, I'm glad he won't have to follow me"
On the one hand, it was a secure employment, that ensured the family was provided for. On the other hand, many of them hated every day they worked.
When oil and gas become too expensive, I wonder how willing people will be to re-open (on a smaller scale) some of the old mines (in a similar way that some of the US oil fields have been abandoned by the big corporations as uneconomic, but can turn a profit for the smaller, independent, companies).
AKH
Thanks for the article HO. I'm guessing you will address this but if I recall properly sometimes British hand coal mining paid relatively well, at least to the person who had the right to mine a section, and the miner was an entrepreneur of sorts who hired his own help to get the coal out. It seems this system was in place in at times in early US coal mining as well. Unfortunately I'm trying to bring this all up from memory, the last book I read on it being returned to the library a year or two ago. But if memory serves the relative pay for coal mining varied up and down quite a bit and sometimes over relatively short time spans.
As an Indentured apprentice in 1961 I was paid 4.5 English pounds a week, the men at the face at the time made, as I remember, about ten pounds. Things changed quite quickly after that and wages went up, but those that worked at places other than the working face, where the coal is actually mined, were not paid nearly as much - but these were often where you still found work after you had contracted black lung.
Pay was always an issue, and since the miners often lived in tied cottages, or houses, this became an issue when there were strikes. The issue is a bit complicated and I may do a post on this later in the series.
Coal mining was, and still is, a dangerous, gruelling operation.
Recent accidents in the US and China, show that it is hazardous. You may hear of the men that die in pit-falls or explosions, but you perhaps don't hear so much about the thousands that die of lung disease in later life.
A real eye-opener of conditions in the mines, is George Orwell's "The Road to Wigan Pier" written in 1936. (Text available on line, chapters 2 & 3).
http://www.george-orwell.org/The_Road_to_Wigan_Pier/index.html
Whilst safety has improved over the last 70 years, and there is far more mechanisation, to reduce the manual work, there are high human costs in coal mining - not to mention environmental damage.
Coal, like petroeum is a finite resource. How long is it until we reach peak coal? We have certainly come to the end of "easy coal", with the higher grades of bitumenous coal already exhausted in some countries.
In a world of dwindling petroleum reserves, there is only so far that you can go to substitute coal for oil, using Fischer Tropsch and coal to liquid technologies. Integrated Gasification Combined Cycle (IGCC) power plants offer an improvement in efficiency over conventional thermal plants. A full scale switch to a coal based economy seems unlikely - because of the finite supply of coal resources.
If we are to make a return to coal, it should be using 21st century technology, not 19th. Reciprocating steam engines are notoriously inefficient, and should not be used when much better steam technology is available.
5% efficiency for a typical 1000hp engine, whilst by converting the coal to gas and running a large gas engine, you can quadruple this figure, and reduce the pollution from the coal smoke.
Large steam turbine plant can return 35% efficiency and IGCC offers around 50%.
A double acting steam engine might at first appear to be a simple prime mover, but don't forget the additional boiler, feed pump, condenser, furnace, stoker and all the other equipment that is needed to make up a complete system.
Centralised power production is by far the best way to utilise coal, reducing the transportaation costs. Large IGCC plants located in the coal mining districts, with a HVDC supergrid distributing the power to where it is needed.
2020
As the world warms a whole lot more coal could be become fairly easy to access. Mostly ice free ports on the northwestern edge of Alaska would be within a couple to a few hundred miles of about 3.1 trillion tons of coal resource (reserves would of course be a much smaller number). Burning all of that to produce electricity for another five to ten decades might not be the best choice of paths if we wish this civilization to move forward. My guess is we will want coal for lots of other things over the millennia if we carry forward successfully.
As my great-grandfather both struck for better mining conditions and pay and died of black lung I've some awareness of the cost of coal. There was a time before mechanization when the skilled coal miner was a subcontracting entrepreneur within the works, and as such the miner could in some periods do well for the times. I'm hoping one of Heading Out's future posts describe how that worked as I have forgotten the few details about it I once knew.
Readers may like to google for "The Big Hewer", a poem and Ewen McColl song, about mining for coal. I think it is originally from North East England. I first read it 45 years ago in the children's magazine 'Finding Out'.
... coal dust flows in the veins where blood should run. Go down. ...
Thanx James --- a Youtube version: http://www.youtube.com/watch?v=g1pNuQBcBBc
We also have coal mining songs in Canada --- here is one by Rita MacNeil with some graphic photos: http://www.youtube.com/watch?v=E-EiwiiAh68&feature=related
They've wonderful traditional music in Northumbria, well documeneted at the FARNE - Folk Archive Resource North East website. Searching for 'coal' you get all manner of printed broadsides and poems, which may be of interest.
Ewan MacColl wrote The big hewer himself. If you'd like to hear a whole album of trad music and song about UK coal than you'll not do better than the High Level Ranters' The Bonnie Pit Laddie: A Miner s Life in Music and Song.
They've wonderful traditional music in Northumbria, well documeneted at the FARNE - Folk Archive Resource North East website. Searching for 'coal' you get all manner of printed broadsides and poems, which may be of interest.
Ewan MacColl wrote The big hewer himself. If you'd like to hear a whole album of trad music and song about UK coal than you'll not do better than the High Level Ranters' The Bonnie Pit Laddie: A Miner s Life in Music and Song.
Tommy Armstrong was really the pitman's poet, writing pub songs etc at the turn of the last century.
There was an old vinyl record of his songs that I have, and it seems that it has been transposed to CD, and is available in the UK.
We sometimes read stories about the Chinese trying to close down unsafe small coal mines. According to this report, China has 28,000 coal mines, many of them small. I often wonder how different the small mines are from the ones we had 50 or 100 years ago. My guess is the level of technology is pretty low, and the amount of cheap labor is pretty high.
HO: a question about mining I have never understood (to my shame as a geordie): what defines the lateral limits of the face? Does a coal seam have a width as well as a height and depth? If so why? The edge of the ancient forest? Does it peter out to the sides or end suddenly? Why do pictures show miners at the end of narrow tunnels rather than attacking a wide face?
Always baffled me!
This is going to be easier to discuss in the posts that will follow over the next few weeks, if you will forgive my dodging the question for now, since it is actually a bit more complicated than I can cover in a short answer.
I just started reading King Coal by Upton Sinclair, a prominent muckraking author in the early 20th century. It appears to be good on describing the mining operations, and, of course, on the litany of abuses practiced by the mine owners. The concept of lying on your side and swinging a pick to undercut the face speaks to how valuable this commodity was and how desperate people were for work. The book is fiction but he does his homework. Recommended.
very interesting - Northumberland is one beautiful place - I have had fantasies about living there since first visiting in the 70's. And of course - the decaying signs of the old coal industry and the lime industry are all over the place.
A response to the comment about western style modern democracy requiring surplus and what may happen when times change. Democratic institutions existed in cultures that did not have surplus - in fact - one might say that subsistence groups were more apt to have a form of democratic governance. England or Ireland before the Conquest would be very good examples of societies with layers of democratic institutions from the local village to the county and further up to the Witenmagot which selected kings in England. These societies were generating some surplus at different points in time - but they maintained these groups decision making institutions even in times of scarcity. Perhaps a factor which assured democratic processes was simple survival - one had to have the best leaders possible as well as relying on the food producers - giving the agrarian folk more power. I do think this may be an encouragement to those who fear what sort of "governance" collapse might bring.
The new economics of coal has led to a situation in which explosives are traded for manhours, and the whole world becomes an "overburden".
Currently there are 250,000 tons per week of explosives used by mining operations in the Appalachian Mountains as it has been found that the easiest way to get coal is simply to blast your way to it.
The results are horrific:
http://www.google.com/images?hl=en&q=mountaintop+removal&um=1&ie=UTF-8&s...
The coal mining operations deserve credit for being masters of language and brevity, in which the most diverse ecosystem in the temperate zone of the world is described in one word, "overburden", and blasted to bits. The variety of trees, flowers, insects, bird, fish, fungi and mammels in the region are so great in variety that there are plants and insects species that probably have not yet even been calculated, all now captured in one word...not "ecosystem" but "overburden". How descriptive. That so called "environmentalists" such as Al Gore (a Tennessean no less!) can look the other way on this issue is proof enough of the power of the extraction companies to do as they please. It will go into the history books of the future as a shameful and dark time.
Kentuckians, Virginians, West Virginians, Tennesseans and other Appalachian range states know that the concept of "clean coal", if it must be removed by this method is nothing less than a euphemism for one of the most massive attacks on ecological diversity in the history of the world, bar none. If the coal companies are going to use a euphemism, then their word "overburden" is far more accurate. In this sense, we all become overburden. "Clean coal" would be the ecological "final solution" for thousands of plant and animal species and for one of the most valuable national treasures this nation has in in its possession. All would become "overburden".
RC
On a related note, does anyone have EROEI numbers readily available for using explosives/mountaintop removal coal?
Thanks for interesting posts.
It is interesting and joy to see here good and interesting paintings in addition to many (unfortunately rather scary) facts and findings.
I was amazed about similarities and differences of Repin's and Signorini's paintings. I knew Repin's painting for long time but I saw Signirini's painting first time here on TOD in Ugo Bardi's post.
There is a lot of symbolism in both pictures. Especially on Repin's painting each character is very distinguished. Interestingly on both painting one person looks towards to a viewer.
One thing seems to me more realistic on Repin's painting than on Signorini's painting – Repin’s haulers have belts for towing in a contrary to a simple ropes on Signorini's painting. It would hurt a lot. I guess they would not be able to tow it too far this way.
For sure thanks again for all those interesting posts with illustrations, paintings, old photos etc.
It is pleasure and joy to read them.
M
Full size of Repin's paitings here
http://www.russianpaintings.net/articleimg/repin/repin_barge_haulers_on_...
Full size of Signorini's painiting here.
http://artesenzaconfini.myblog.it/media/01/01/118727358.jpg
Repin's painting also includes more historical information --- the defrocked priest for example.
You don't think the towing tech improved from ropes to belts in the six or eight years from the time Telemaco painted his scene till the time Ilya painted his
?- )
Maybe the Russians were just higher tech haulers ?- )
Seriously, it is interesting to try and gauge the completely different effect each work creates. Great to has gems like these emerge here.
Ugo also deals more with the political constraints in the coal trade after 1860. Since I am more concerned with discussing reserves and methods of mining and the more technical considerations, I am going to start a little earlier in the use of coal, when it was mined in the UK, and some of the early practices.tiffany and co
The idea of wandering back down the mine and doing anything like productive work in a post-mineral-energy era is somewhat odd, in my view.
So interconnected is the present industrialised world that it will only take a single failed chip in a generator voltage controller or the loss of a special drive belt to see the local coal fired coal production machine stop. After that it will be picks and shovels - provided the deep mines don't flood.
There will only be meager deposits of any minerals that are of a quality and quantity that are capable of being mined by pre-mineral-energy-era methods. Anything else will have been dug through and over and out as the technology of the day developed.
The old timers will have followed the same EROEI curve up as we are following down. They will have worked through all the highest yield deposits first, then moved on to the harder and more expensive to win resources only when further work with the smartest contemporary technology has become uneconomic.
So I see a future which does not see a sweet and polite continuum of a return from modern production to ancient methods and productivity (and hence price) but rather a very high risk of a very disjointed step-decline to scratching out currently-economic low grade ores (of gram per tonne density) with inappropriate tools, and trying to refine that ore with remnant technology.
The chance of post mineral-energy era commercial-scale production of commodity volumes of any historically-useful mineral seems slim.