Tech Talk: Making Room for the Pony - Concrete and Steel Support of Tunnels
Posted by Heading Out on May 23, 2010 - 10:46am
Prior to 1842, horses were most often used outside of mines to help raise the coal up through the shafts, often with the aid of horse gins such as this.
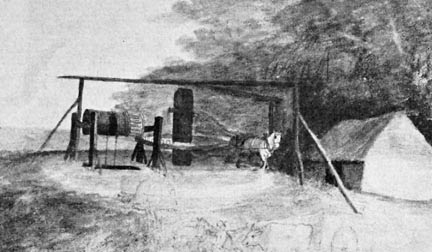
As I noted in the last Tech Talk, the passage of legislation in the UK in 1842 prohibited the employment of women and children under 13 in underground mines. Their labor had to be replaced, and the replacement was often with pit ponies. However, unlike women and children who could be trained to cope with working heights shorter than they were, this did not hold true for horses. And so there had to be some change in the way that the mines were operated, particularly where the coal seam was not that high. Today’s topic will discuss some aspects of how they drove that, and will end with a comment on concrete shaft liners that might have some relevance to the recent events in the Gulf of Mexico.
One of the first steps attempted to gain the extra height was to cut a deeper passage in the floor of the mine. This was often softer than the roof, and would give the additional height needed, but as I will explain later, often only for a short time.
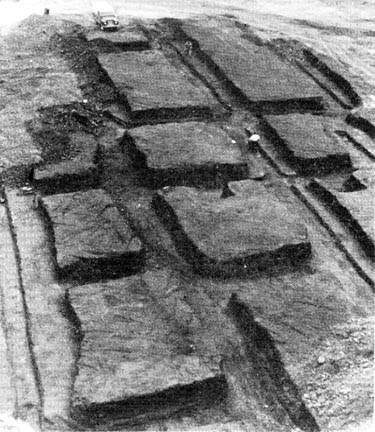
This did not prove to be that popular, and the more common practice was to fire explosives in the overlying rock and thus drive a higher tunnel, for the passage of supplies in, and coal out. The brow of that excavation was generally kept up with the face of the mining operation, and required special support. (There was a man killed at a mine I was working at, when this area collapsed.)
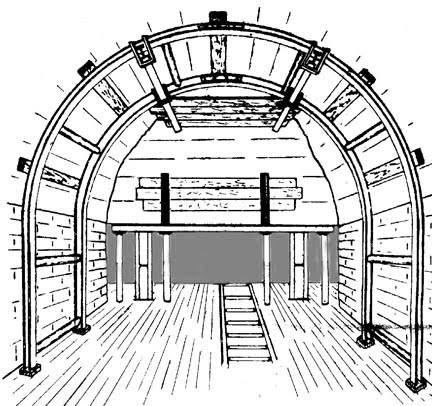
It was found that the tunnel was more stable if the overlying roof was broken out in the shape of an arch, and it could be shaped so that steel arch girders could be placed to hold the roof rock in place. There was, however, a problem in getting rid of the rock that was blasted down. Taking it out using the tubs occupied valuable space and time and earned no-one any money.
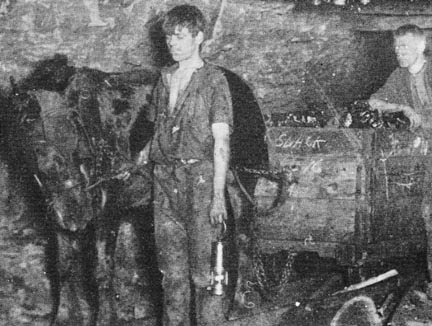
It was found that if the coal on either side of the main tunnel was removed, that this would leave a space into which the overlying rock could be packed. The larger blocks of rock were used to build the walls from the floor to the top of the opening, and then the “stone man” would shovel the smaller broken rock behind it, packing it up to the roof and providing additional support. This gave a gain in production from the coal removed, while helping with disposal of what would otherwise be waste rock.
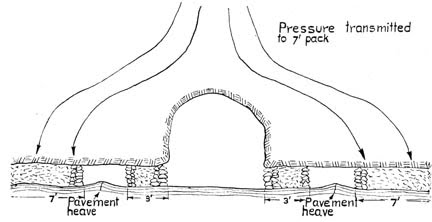
The illustration helps illustrate another advantage of this over taking up the floor. The rock under the coal is often a shale, that can soften. When the rock weight that rested on the rock removed from the tunnel shifts, it does so to the rock immediately beside the tunnel. If that is a solid connection, then the additional pressure is applied to the underlying shale. If this is softer rock, it can flow out under the pressure, pushing the rock floor of the tunnel upwards, which is known as floor heaving. This can get to the point that it reduces the height of the tunnel by over two-thirds and the tunnel floor has to be removed with a secondary mining pass. If the coal has been removed to either side of the tunnel, then the floor heave that takes place can occur in the pack area outside the area of the working tunnel, as the picture above shows. This makes it easier to maintain a clear passage.
However, there will still be some compression of the rock packs as the weight of the rock comes on them, and so the arch girders that are used to support the tunnel are put on small wooden stilts. As the weight comes on the arch, it is pushed down between the two pieces of wood, converging without distortion, and still supporting the roof.
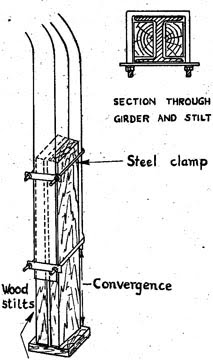
Steel arches of this type were used in much roadway construction, both for mining and civil tunnel support (including subway systems) for many years.
However the arches, even when supported with wooden struts between adjacent arches, are not waterproof. Thus they were not of great benefit when, for example, it became necessary to sink a shaft through water bearing rock to get down to the coal. There were two ways of dealing with this: one was to weld steel plates together to give a continuous casing of the shaft, from the surface down to the seam. The other was to use concrete to pour a liner to the shaft as it went down.
However there are a couple of problems with using concrete alone as a supporting system, for while concrete is good as a support that resists loads that do not change much, and that put the support into compression it is brittle, and more vulnerable to cracking when subjected to tensile loading. It has been noted that where conventional concrete comes under a pressure, then the small fissures in the structure of the concrete can open up and extend so that the concrete becomes permeable. Part of this is due to the differential compression of the different phases of the material in the concrete. If the loading is relatively even around a cylinder in compression, then the cracks can remain quite small, but when, for example, you get the differential loading, such as that which is shown in the picture above of the pressure distribution around the arch with two walls, one can imagine how there is sufficient differential loading that cracks can open and water, or other fluid, enter the passage. As a result in mining operations concrete has proven, alone, to be an unreliable water seal and often requires additional steps to prevent water access, or ways to collect and trap the water, so that it can be carried away without interfering with workings. From personal experience, lying on your side shoveling coal, while water drips onto your back has little to recommend it.
Thanks, Dave. It is easy to lose sight of the rather basic improvements that were needed to get to the high-tech coal industry we have today.
Do you have any idea what proportion of mines are using technology such as this today? I would imagine some in China, and some other lesser developed countries.
This is actually a lead in to a couple or more posts that cover where most mines are today. I put this one in because it deals with pressure around an opening underground, which relates to what you need to hold an opening underground, and it has a little relevance to the gulf because of the problems that you run into in keeping the lining impermeable under those conditions.
Not many comments but I have been enjoying this series --- thanx Heading Out.
Yes great series. But I still have the question I asked a few weeks back, which is about the lateral edges of a coal face. How wide is the face? Does it peter out at the edges or do you always tunnel forwards even if there is coal at the sides? If so are there multiple parallel tunnels all driving into the face? I have never understood this!
I will have a map of the development with early measurements in next weeks post. The width was about 2 yards in those old workings. They tried widening some of them, weakening the intervening pillars, but that could bring the roof down. Essentially it was a lot of cross-connecting tunnels with pillars between for roof support. The size of the pillars is controlled by the depth. The width of the openings is controlled by the strength of the roof rock.
Having a couple of ponies myself, I love reading this. I've done a little research into historical uses for ponies, but more into agriculture than industrial. I tease my pair about turning them into pit ponies, but the reality was pretty grim.
Do you find your ponies to be as intelligent and trainable as horse and mules?
We no longer use draft animals, but the old folks had both horses and mules which were capable of showing a certain amount of what could possibly be called initiative, such as knowing when to go and when to stop with a wagon as they loaded it in the field, often without a verbal command.
Ponies have always been scarce around here and were kept as pets or mounts for children if kept at all.
Old Farmer Mac,
Most of the Ponies at our pit were Welch or Dartmoor ponies. They were certainly intelligent, Queenie the on I had in the late 50s, could certainly count. She would only pull three tubs and if you tried to put on another tub she could count the clinks of he chains as they took up the slack and she would stop, no matter how lightly loaded. If they didn't like you they had a tendency to push you accidentally into the side of the tunnel when you were trying to get past. I saw one knock a man down, stand over him and piss over him, they sure can piss. He looked as if he had just come out of a shower. I don't know if they had a sixth sense but I used to let mine lose at the end of the shift in the return airway and off she would go of at gallop down an unlite airway over 1,000 yards long. She would be be safely tucked into her stall and half way through her food by the time I popped in to check how she was.
They had a much easier life in the 50s because they were mainly used for pulling supplies up too the coal face in the return airways. Most of the coal by then was transported from the coal face by conveyor belts or by endless wire ropes on to which you could fasten the coal tubs. It was a different thing when you were using ponies to haul the coal and your wages depended on how much coal you produced, I am certain that many a pony received a good whacking if if he was perceived to be slacking. I personally never saw any mistreatment of the 20 odd ponies we had working in our mine. Mind you the mine manager would have fired you instantly if he thought you had mistreated a pony. He used to check into the stables everyday when he made his inspections.
When we brought the ponies out the pit for the last time the checkweightman bought one, the rest went to the knackers yard, glue and dog meat was there fate for all the years of service: it used to follow him like a dog through the village. He stabled in the field where we used to put the ponies during the two weeks summer holiday.
Checkweightman = was a union official usually the branch secretary who used to check the weight of the tubs of coal when they came out of the pit, to see the men didn't get cheated. I wonder how that could happen?
I hope that has helped in answering your question.
Deep Regards
A little bit of home tunnelling may be useful. During the Australian firestorms 18 months ago in which nearly 200 people died I think 8 or so were saved by home made firebunkers. Here's my early attempt dug into weathered igneous rock
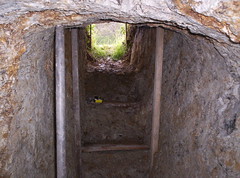
When above ground temps are 40C/104F below ground it is 16C/61F. Since shoring it up better still won't stop the mould and damp I may replace it with a watertight structure.
It is great to get the real story of how things were. The photos are wonderful as well. Thank you for this series and we will check back for more. I think that students need to study this in school as well.
Your comment on the plasticity of rock is noteworthy.
If rock like shale can "flow" in the shaft & tunnel of a coal mine, then what about the same happening in the seabed where a hole is drilled for oil? Seems like cementing a casing in an oil well could have the same problem of the cement not taking the tensile stress very well if the pressure inside the casing is high. Casing could slightly expand (modulus of elasticty of steel being 30 x 10*6) and concrete would then be under tensile stress if rock has heave or flow.
Mention has been made of Deepwater Horizon well bore being larger than drill size due to rock washing out (happens in soft rock?) which resulted in more concrete needed to fill void between casing and bore hole. Maybe extreme pressure of reservior on casing caused some concrete cracks. These then initiated oil and gas leaks that got larger when pressure of mud was removed. Gas will leak through much smaller cracks than water.
Mark S Bucol
Enjoying this series a lot HO thanks. I built a few five foot high steel reinforced tunnels (suburban sewer line) that were only about 100 feet down once upon a summer. Was the concrete lining used in the coal mines steel reinforced? It would seem these days some sort of water impermeable barrier could be applied to the raw rock before concrete forms were built. We used to have arched steel forms we rolled in on tracks for the upper portion of the pour. The concrete was blown back to into voids with compressed air via a special fitting on th last pumpline pipe. Small doors in the top of the forms allowed us to break down the pipes and remove them as we went. But this sort of tunnel was expensive and would only make sense in a main access shaft that was to be used for many years.