Tech Talk: Moving the coal from the face to the shaft
Posted by Heading Out on June 6, 2010 - 9:28am
This is a continuation of a series of tech talks, most recently relating to coal, that have been offered on Sundays. Here, Heading Out continues to tell us about the history of coal mining. Some of these techniques are still used today.
At the surface an underground mine might appear to cover a relatively small area, but this may be quite deceptive of its actual size. Even back around 1850 the mine that James Dunn worked in extended out more than a mile from the shaft. As they extended, so the areas that were worked left pillars that might contain up to 40 – 50% of the coal in place, but had to be left to hold the roof up. The miners drove “headways” into the coal that were connected by cross passages or bords. At Houghton Colliery, for example, the pillars would be 5.5 yards deep, while the headways were 2 yards and the bords were 3.5 yards wide. The headways would advance about 20 to 40 yards before a cross drift was drive to hole through and create a new bord, along which the ponies would bring the empty tubs, and haul away the full ones.
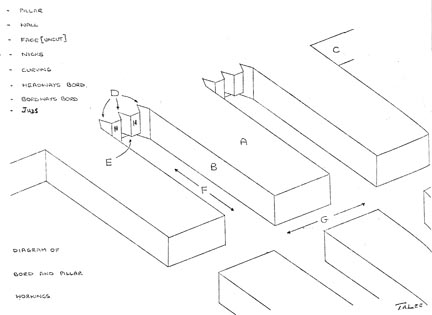
The method of mining the face can be seen in the drawing. First it was undercut, then three vertical cuts were made (the nicks) and then the intervening coal could be broken out in the larger pieces that were favored by those buying the coal.
Back then, the tubs of coal were moved from the working face to the shaft by teams of boys and men. But that only worked when production rates were relatively low. As the demand for coal grew with the Industrial Revolution, so the need to produce coal in greater volumes, and to move it faster to the shaft grew.
Pit ponies went underground, but would only pull a certain (small) number of tubs, and so better ways were needed. With the coming of electricity, this turned into the use of long “endless” ropes that wound their way along the centers of the rail lines into the depths of the mine.
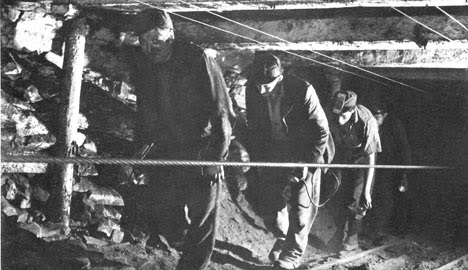
Hauling the tubs in either direction meant manually attaching a front shackle or chain to the moving rope, which then pulled the set of tubs down the passage in the direction required. Usually these systems were restricted to the main haulage ways or “Mains” since the ability to turn corners was limited. The main drive engine was usually by the shaft, and when the rope was not moving continuously it could be engaged by signaling the operator through a series of bells and cables. (The wires above the pitmen's heads).
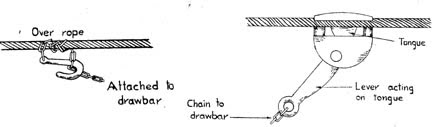
In an alternative method of haulage the rope was attached to the front of the set of tubs, while a second rope was attached to the tail end of the set. (Hence the name Main and tail). Thus as the tubs were pulled into the mine (inbye) they extended the rope that would later be used to haul them back out (outbye). But again these systems were largely kept in the main haulage parts of the mine. Once they reached the area where mining was continuing (the working “district”) they would be broken loose and could be hauled further by the pit pony. Thus on the map of the mine, the mains could be identified as the two parallel tunnels that would run out from the shaft in the four main directions (though this was oriented to the patterns of fractures in the coal, or cleat, rather than the compass points).

Full sets would then be reassembled after they were brought back from the working face and hauled back to the shaft.
While the coal was mined by hand, and then loaded out by hand this system remained capable of handling the production. It is still, apparently, used in China. However, as mines grew larger, the inflexibility of the system, and its intermittent nature reduced its popularity. It was still around, however, in the early 1960’s since I spent an uncomfortable week or two of my apprenticeship working the engine on the maintenance shift, where the rope was only needed a few times in the shift to move tubs. It was there I discovered that by just cracking the engine on, the current running through the resistance bank would slowly heat it up, while the engine had not enough power to turn. This could, as long as a) you didn’t get caught and b) the rope didn’t move, keep you warm in the cold air of the downshaft flow.
A better way was needed for hauling coal from the face, and this came with the development of the conveyor belt. Initially mining belts were relatively simple. Long flat strips of reinforced rubber belting would be joined at intervals with wire clips, to form a loop. This was, in turn driven by a motor at one end, and a tensioning return drum arrangement at the other. Miners could load the coal onto the belt, and this would carry it out of the district, where it would transfer to a second conveyor belt that would carry it to the mains, where it would transfer to a much large belt, now carried on rollers, often suspended from the roof, that would carry it to the shaft, or in shallow mines out to the surface.
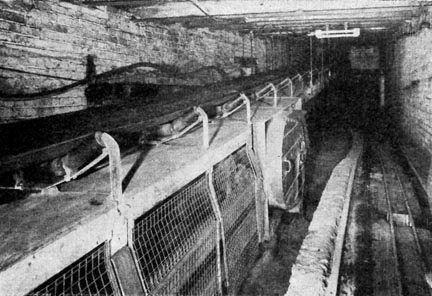
One of the reasons for the suspension of the rollers rather than having them set in a frame resting on the ground is that it left clearance under the conveyor. Thus as small coal and dust fell off the conveyor it fell into a space where it could be seen and removed before it became a risk. If it was allowed to build up it could rub against the rollers, generating friction, heat and ultimately causing the coal to catch fire.
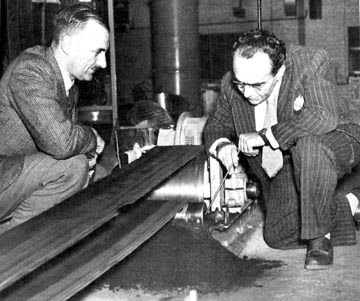
The fire at a transfer point at the Cresswell Pit in the UK in 1950 created clouds of carbon monoxide, which flowed into the workings and 80 men died. Fires associated with poor belt maintenance and failure to remove the coal powder that accumulates around the transfer points and similar locations, are, sadly, still occurring even within the past month. They don’t have to be underground and one of the major problems created is the smoke that is formed, which can very rapidly make it impossible to see.
Conveyor belts do, however, when properly maintained, provide a relatively rapid and simple method for getting the coal from the working area to the shaft or out of the mine. They can even (in some cases officially) provide a way for miners to ride their way out of the mine at the end of the shift.
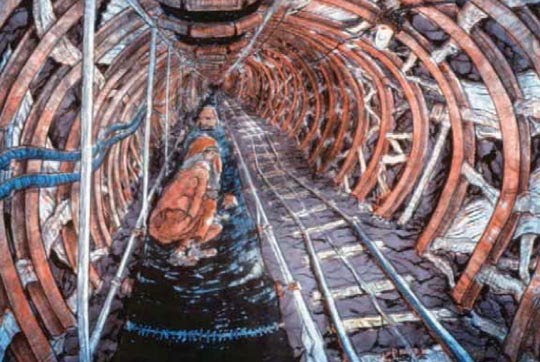
You just had to stay awake enough to get off the belt before the next transfer point.
Thanks, Heading Out. Very interesting!
When you talk about pit ponies dragging the tub, or ropes pulling the tubs, did the tubs have wheels? Were they like little wagons, or what?
Yes Gail the tubs had solid axles the wheels were about a foot in diameter, which made them difficult to turn,all the tubes when I worked in the mines like heading out in the early 60s were all made of steel and would contain about a ton of coal when properly filled. Because they had no breaking system and as the coal beds are not level you have plenty of gradients. To slow the tubs down a primitive braking system was used we called them pigs tails which consisted of a solid round metal bar bent into the shape of a pigs tail. This was then jammed into the spokes of the wheels causing them to stop turning. The loop was to stop the bar going too far into the spokes and stop you losing a couple of fingers.
In the early part of the last century nearly all the coal underground was transported by tubs it is only during the later part during the modernisation after the Nationalisation that conveyor transport became general.
Much of the coal getting during the early part of the century was subcontracted to groups of men who worked different boards. My Grandfather was the boss of one of these gangs and was referred to as the puffler. He was supposed to do the puffing and the rest the work. It was not so he worked dammed hard. My Mum used to tell me that as a child during the first world war my granny used to send her down to the pit yard Friday afternoon to pick up the wages. My grandfather would be squatting in a circle with his group dealing out the money to the men. What was over was put into a leather pouch minus a gold sovereign to buy the lads a drink in the Atlas pub. She would then go back to give it too granny.I find it rather astonishing that a girl of 6 could be trusted with a bag of gold and silver. My Mum found it astonishing that I could think that way, if they had had a good week then she would receive the odd farthing of halfpenny from the men of my granddad's gang.
The tubs of coal from each gang were identified by a round brass disk with the no. of the gang stamped on it, this was attached to the tub by a cord. These disks were called motties in Yorkshire where I come from. When the tub of coal reached the bank, the top of the mine it was run over a weighing machine similar to what is used for weighing lorries, two men would check the weight and enter the weight accrediting the weight too the gang whose no was on the disk and take the disk off the tub. The one man was the representative of the mine owners and the other usually the Union branch secretary called the check weight man. It keep cheating to a minimum.
Gail a picture is worth a thousand words, this should give you an idea of the size, although they could vary somewhat
http://www.bowburn.net/images/pit_tub.jpg
Deep Regards
Yorkshire Miner
Your diagram shows "bord and pillar" mining arrangement. In the US it's usually called "room and pillar" mining.
I wonder if the 40 to 50% of remaining coal could be mined by using some variation of "long wall" mining technique. But subsidence is much more of a problem with long wall. Subsidence can even ruin agricultural land as it changes the water flows.
Question for Heading Out:
Do any of these closed coal mines produce methane mine gas for industrial use or heating?
The mine gas is used frequently in the US where the shafts can be well sealed and extraction pipes bored into various parts of the mine.
Coal bed methane is being considered as more and more of a resource, if it can be drawn from the coal before it is mined. During mining and in order to keep the mines safe, such methane as escapes into the working area is diluted by the volume of air in the main flow so that it falls below dangerous levels. At least that is the aim, but in doing so it makes it impractical to recover the gas.
I know very little about coal mining (although Dad's first job was on a tipple). Though not common, I've heard of using the <1% methane ventilation air as the combustion air for IC engine generators to recover some energy from the diluted methane. I believe that there are also methane collection systems in use in gassy mines to reduce the required ventilation air.
Interesting, as always. The more details you provide, the more I understand why the Appalachian coal mining companies are so eager to blast the tops off mountains and strip mine the coal.
Thanks for the post HO good to see regular tech talk coming back on line.
I can imagine there may have been a few digits or more lost connecting tubs to endless ropes. Years ago I met a pair of Dutch couples at a Montana bar. When I mentioned I was doing carpentry they held up their hands a with two or three fingers folded over and smiled back over their glasses of our weak American brew--apparantly the hard drinking Dutch carpenters had had a bit of trouble adapting to the electric 'skillsaw.' I can just guess how well connecting tubs to a somewhat jerkily moving cable in deeply shadowed coal mines worked out for many of the uninitiated, over tired or just careless miners fingers and hands.
We called them "dregs" in Northumberland, and I learned on the surface where they took a run of tubs up to the top of a pit heap, and let them go one at a time. We, at the bottom, had to stop them using a variety of dregs, some of which had a protective cross-bar in place, others did not. Never was one of my favorite pastimes.