Tech talk: Early coal mining machines and their use
Posted by Heading Out on June 14, 2010 - 10:15am
This is part of a series of Tech Talks that I write on Sundays. Note: It is appearing on Monday, for this week only, though. - Gail
This series is meant to provide some background information on the extraction of fossil fuels and metals from underground, both as general education and as a resource when, as with the Gulf oil disaster with the Deepwater Horizon, or with an underground mining disaster such as that at the Upper Big Branch Mine folk need to know what is going on. Thus, for example, at the beginning of the Deepwater Horizon spill, I combined some of these to describe some of the critical parts of creating a well.
Today, in that tradition, I am going to be describing how the extraction of coal progressed from manual mining of the coal, with a pick and shovel, to the next stage which was the early use of compressed air power and led into the mechanized mining that we use today. At the end of the last talk I showed the method by which the pattern of mining evolved, with a miner first undercutting the coal, then cutting vertical slots, and breaking out the ribs between to extract the coal in relatively large pieces.
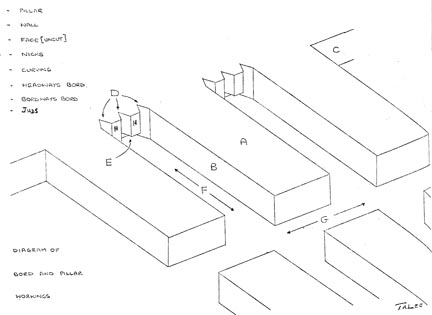
The first step in mechanization was a change from the physical mining of the bulk of the coal, to drilling a hole in the coal face, inserting a stick of explosive, and breaking out the coal more rapidly. The miner then had to do less picking and more loading of the coal into tubs. Initially the holes were drilled with a manual drill, with the miner bracing the bit with his body, as he turned it into the coal. The bit was held at the right height using the pinned prop that is shown in the picture.
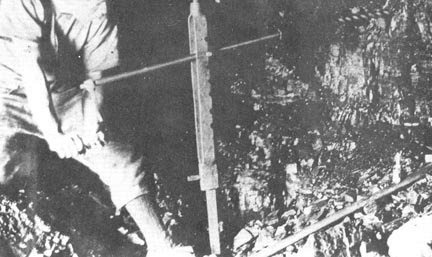
Drills, over time, changed to first compressed air, and then, more recently to electric drills, though these, though more powerful, were heavier and drilling was done without the aid of the prop.
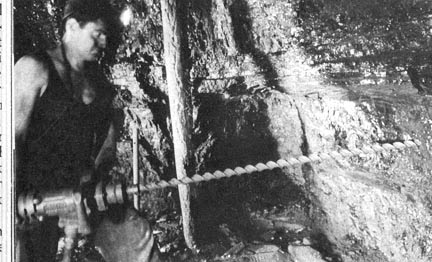
The shotfirer was generally the lowest level of administrator in the mine, and had to be certified, after an examination. The explosive was generally moved around in a wooden box, for protection, and fired in later years, with an electrical detonator, to allow a suitably safe distance. Earlier ignition used a burning fuse (as shown in many movies), and this was more hazardous since you could only get a certain distance away after lighting the fuse. The rod that was used to push the explosive into the hole, and stem the hole (usually with clay or coal dust) to contain the blast, was an initial sign of authority.
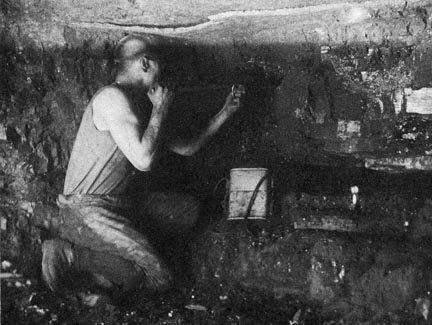
Once the coal was broken into pieces, moving it with a shovel became a lot less work than physically breaking it from the solid. But before the coal could be blasted down, it still needed to be first undercut to give a free surface to break to. And that was still done manually. Until, that is, the invention of the cutter bar. Simplistically, the first cutters were a series of small picks mounted into what are known as boxes, along a cutting chain that is itself fed around a long bar that is powered (very similar, on a much larger scale, to the bar of a chain saw).
The first of these was developed to help in the driving of the tunnels or rooms, from which the coal was mainly mined.
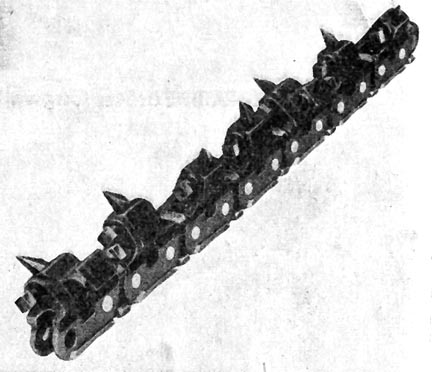
The initial bar could be swung through a 180 degree arc to undercut the coal at the face of the room, as mining advanced. The machines could cut at different heights above the floor, although the base of the seam was much preferred.
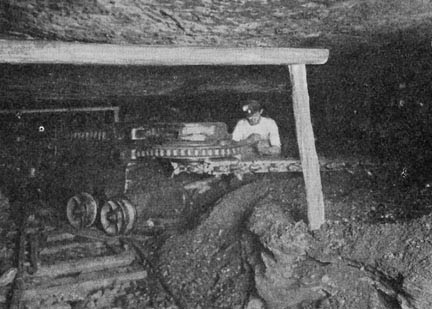
The earlier machines were manually moved around on rails, which in turn meant that the rails had to keep up with the face. And the early motion was relatively primitive.
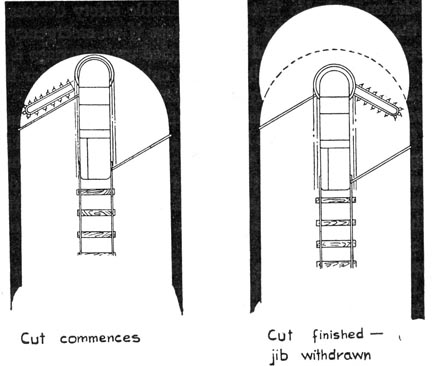
Two things remained to be mechanized. The first was breaking the coal into small enough pieces that it could be loaded into tubs or onto conveyors. A variety of different ideas were tried over the years. This one used compressed air and a variation on pneumatic pick action to break the coal:
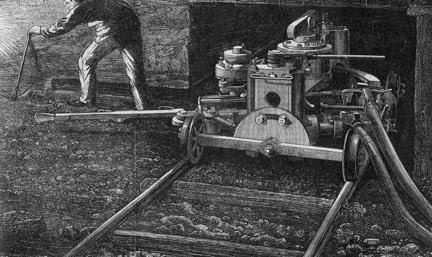
My grandfather, I believe, worked with a variant of this machine.
But the last hold-out was to change from manually loading the coal to mechanized motion. After all, if the coal was cut with power, and broken with power, it made sense that it should also be loaded by power. Again there were a variety of machines that were tried, but then Joe Joy entered the picture with a machine that led into the tools of modern day mining.
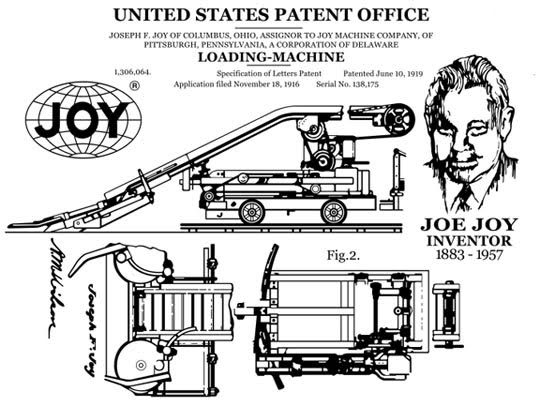
And it is with this image of the Joy Gathering Arm loader (the arms rotate about their pivots to move the coal to the central conveyor) that I will pause, before moving into the modern version of this machine and its offspring. All the components for modern day machines had been invented; it was just a case of putting them together in the right way.
As I look at these post, one of the questions in my mind is how easy (or difficult) would it be to put in such technologies now, if we had to rely solely on local resources.
Out East, it seems like most of the mines are sufficiently mined out, that any kind of technology, short of what we are using today, wouldn't be that helpful. Out West, it seems like surface extraction rather than any kind of mining is being used.
If we didn't have the big earth movers that we have today for surface mining, I suppose that we would have to figure out some sort of extraction method, and this might be an option. But it isn't obvious this method would be easier to implement / use less oil than other modern day approaches.
One caution--I am strictly a lay person when looking at this. Are these techniques being used today anywhere in the world?
Gail:
The questions that govern methods of extraction depend on where the coal is, how much there is and what the market is like. For small brickworks, say in far Western China, it may be that this can be supplied from mines not that much different than this. But it is getting easier globally to mechanize so that even in Botswana, when the new mines go in they will likely use state of the art equipment. But given that it is a Chinese company doing the development the supplier of the equipment may no longer be Joy.
Gail,
I dug around and found a summary of current technology for underground mining in New South Wales (N.S.W.), Australia, which is one of the major coal producing areas of the world (Newcastle is the largest coal export port in the world, with typically fifty to sixty bulk carriers anchored offshore waiting to load).
Underground mining accounts for about a third of the coal mined in N.S.W.
It appears that the bord-and-pillar technique described in 1749 is still in use, but it being rapidly phased out in favor of longwall mining.
Details of the machinery used is not given, but there is a limit to the possible ways of extracting coal. N.S.W. coal is largely in quite thick seams (8-12 feet) and dips are very slight in most mines. The main geological problems are small faults and channels eroded in the coal soon after deposition, both of which are usually widely spaced, and thin intervals of clastic deposition within the seams.
A very detailed coverage of current underground mining techniques is available on line from ACARP and the University of Wollongong.
The mine near Newcastle I spent a day in fifty years ago used machinery similar to that described in the original article, all of it electric powered, with the loaders, cutters and shuttles all running on rubber tires.
The big surface mines in Wyoming get most of the attention, but six of the biggest 50 mines in the US (by tonnage produced) are underground mines in Colorado, Utah, and New Mexico. You may remember news stories about the Crandall Canyon Mine accident in Utah in 2007, where six miners and three rescue workers died.
mcain: Yes. Years ago, CF&I shut down their iron mine near our town, and alot of the guys I knew moved to Colorado and Utah to go to work there.
If push came to shove, a large part of the surface mining operations could be electrified. The biggest draglines and bucket-wheel excavators built are already powered by electricity; very large electric shovels are also available; large conveyor systems may not be as flexible as the enormous trucks used today, but are feasible. For that matter, some versions of the big dump trucks are diesel-electric already, and the diesel-fueled generator could be replaced with an alternate fuel. An LPG turbine would suffer somewhat from lower fuel density, but if you want to cut back on oil...
If we wanted to start arguments, we could ask about the EROEI of bringing in one of the proposed 100 MWe truck-mounted nuclear reactors to power an electrified coal mine...
Yeah. I kinda like that idea.The Navy has a LOT of expertise that could be accessed, hopefully, plus an excellent safety record. One could still run the dragline and/or stripping shovels on electricity and the haul trucks on LNG.
Gail: I believe improved, but basically, the same equipment is being used to mine underground coal today. Its kinda like the difference between the micro wave oven my parents bought and the one I have now. Does that help? Out West here, the open pit mines have very little overburden atop the coal seam. In Campbell county Wyo , for instance, there are areas in some mines that have as little as 70 feet of overburden on top of 80+ foot coal seam.
HO: I think Bucyrus Int'l is making underground equipment now, as well as others.
lrd: good info there. Need to know more about underground mining as my little experience is limited to open pit coal. Helped build load out structures in a couple mines in the Powder river country.
Hey! The Navy could help with that. Doncha think? Could work.
Caterpillar actually makes a fair bit of underground mining equipment (most people are more familiar with our above ground work). A while back Cat purchased the Elphinstone company in Australia.
Ive been fortunate enough to go below to get a close up look at how our machines get used in a copper mine in Tasmania. We dont currently make any equipment for use in a coal mines though. Metal mining and coal mining are worlds apart in that typically a metal mine isnt so concerned with the build up of explosive gas.
Even though it wasnt a coal mine the techniques applied are similar.
One of my take aways is that the explosives used were going up in price just like fuel prices. The one mine I went down used hundreds of thousands of dollars in explosives every month. I was amazed at the sheer tonnage of explosives used. The chemistry isnt so different from fertilizers (some is identical - ammonium nitrate)
The drilling was done by atlas-copco machines. Cat equipment was used to scoop and load Cat trucks. The large tunnels were big enough to fit these trucks and loaders in and it was all blasted out of the rock. The whole mine was ventilated so that diesel powered equipment could operate, however the environment was still hostile. The mine was so deep undergound that the rocks were warm to the touch. I recall being about 1km below sea level. The air was hot and thick with humidity, acidic and saline water poured in through cracks and was constantly being pumped out. And by Saline I mean Extreme salt, 7 times more salty than sea water. Equipment can rust vey quickly. A huge crusher was built in a cave about halfway down so that the trucks didnt need to come to the surface, from the crusher material was conveyed to the surface mechanically. They even had maintanence caves built into the mine way below the surface.
The heat, sweat, and darkness were overwhelming. You get the impression that hell is only a few more feet down.
When I was there copper prices were peaking. I got the impression that the world was rather desperate for copper to have all this money and energy invested in a hole to drag out rocks with a small percentage of copper in them.
I can only imagine! I've spent my whole life out here on the Great High Plains, and I like seeing the horizon for the better part of each day. It takes a special person to go down in "them thar nether regions"!
At the Pebble Mine site where the huge ore body sits at the head waters that spawn the last really large wild salmon fishery left in the world (Brirtol Bay, AK) the potential harm that desperate need can bring about comes into sharp focus. This Pebble mine web site hits you with a gulf oil spill gallon ticker before you read a word about the mine. Answers are not easy and the stakes keep getting higher.
HO,I appreciate your posts,including this series on coal mining.
What seems to have escaped a lot of people,including commenters on TOD,is that coal mining,whether open cut or underground,high tech or low tech,is producing a product which is the most polluting of the fossil fuels.Burning coal is responsible for well over 50% of carbon dioxide emissions by humans as well as other pollutants.World wide the industry is a death trap in so many different ways
We need to kill coal,using nuclear,geothermal and renewable electricity generation as quickly as possible.
You may want to find out what the Chinese have for scrubbers over there. If they even have them.
GEEZ!
Well, I guess we could cut our face off in order to save our nose. What is the date for that new nuclear plant coming online? Has anyone figured out the carbon footprint of building and erecting one of those big windmills? Solar seems impossibly ineffecient in the main.does anyone know how much fuel it takes to produce one barrel of cement? That nuclear plant is going to take ALOT of that.Dont know for sure, but I heard there is 400 to 600 yards of concrete in the base of one of those big windmills.I have two in my line of sight off the back porch looking towards the Medicine Bow range here. There are a whole lot more in that farm over the hill there. about half are working at any one time.
"What is the date for that new nuclear plant coming online?" Not much more of a wait. Watts Bar 2 should be fueled in 2012 and hooked to the grid in 2013. It will probably be about 4 years after that for the next one though.
I've been talking to various 'friends' about this disaster, and it appears, based on what they told me, totally, totally, of the record, that this is bar far the biggest environmental catastrophe in US history, dwarfing the Exxon Valdez spill. Arguably this may be the largest polution catastrophe in human history.
Privately people are telling me that what the Obama administration is doing is playing for time, easing towards telling the US population the truth about the real scale, and the dangers connected with the spill.
The game is a simply, though cynical one, divert the people's attention away from those who are really responsible for the circumstances that led to the disaster, like the financial collapse, primarily the government, and direct people's anger towards BP instead.
Politicians cannot be trusted. Telling the truth is an almost completely alien concept for the vast majority of them. Rhetoric yes, truth no. And Obama is a practiced master at political rhetoric, but when it comes to truth, forget it.
For example, can one have it both ways? If one is a politician the answer is yes.
If BP is so useless and incompetent, why have they not been simply pushed out of the way by the US governent already? Can the US government do a better job than BP? If it can't because the disaster is just too big to be manageable, that it's not fixable within a short timeframe, then why criticise BP so much? Simple answer, because the US government and Obama are using BP as a scapegoat hoping to conceal their own incompetence in allowing drilling to take place in such a sensitive environment without much, much, much, better regulation and control of the oil industry.
It seem the leak is under the seabead, and not above the surface in some pipe. The rock around the borehole has been shattered which is allowing oil and gas to escape into the rocks surrounding the well, and this is now leaking through the seabed at multiple sites. This makes everything far more difficult and serious, and stopping the leak, which is really a series of leaks, far more problemantic. If what I've been told is true, this thing could go on for years, not months, and the environmental consequences are therefore almost unthinkable. What happens to the onshore environment when a hurricane rips through a vast lake of oil, lifts it up into the atmosphere and sprays it out over the states along the gulf? And that is just one of the ghastly fates that are waiting to show their faces.
Perhaps you might try today's other open thread to ask that. I bet they will be more than happy to give a VERY factual update and bring you up to speed. Reading some of the previous threads will serve you well also.
We will see what a hurricane does, but generally the more water tubulence the quicker the oil breaks down into far less toxic substances. BP was cutting corners big time (not unusual for them) but this time the gamble blew up in their face. Sure we all get to shoulder some of the blame as our way of life depends on oil but that absolves BP not a lick from the decisions they made that let this thing blow. Try to find the results of the cement bold log for this hole. For a project as troublesome as this one was it certainly seems the test should have been run. Of course that is usually done 24 hours after the cement job is finished and these guy were displacing the drill mud with sea water a mere 20 hours after the cement was in.