Tech Talk: Pre-mechanized longwall mining of coal
Posted by Heading Out on August 1, 2010 - 10:30am
In the last post on this subject, I wrote about how miners were able to remove almost all the coal from a section, either by leaving small remnant pillars or building packs to hold the roof in place, while that coal was removed. By retreating the face back towards the shafts, the overlying roof rock was then allowed to collapse into the void left by the coal removal. However, as this process began to evolve the miners noticed a couple of significant things that helped in the understanding of how the roof was responding, and helped to make longwall a safer and more effective method of mining. The first was that as the roof broke behind them, the rocks would bulk up (they gain about 60% volume as they break and pile). Within a distance of about 2 seam heights, as the roof was converging, without underlying support, it would then meet the broken pile of rock, and thus get some support from this. As a result any support that the miner installed would not need to carry the full weight of the overlying roof to the surface, but only that of a few feet, which needed much less strength.
Thus by about 1870, and possibly in the Lancashire coalfield in the UK, they had modified the process further, and were only supporting the roof around the actual mining operation. How could they get away with this?
There was one other fact that helped make it possible. In some of the earliest tech talks I mentioned that the weight of the overlying ground can be simplified to being around 144 lb./sq ft for every foot of depth – based on the simplifying assumption that a cubic foot of rock weighs 144 lb. Thus converting this to a pressure in lbs/sq inch. (of which there 144 sq ins to a sq ft) this means simplistically that for every foot of depth one goes into the ground, the pressure increases by 1 psi.
Now when you make a hole in the ground, that load, or equivalent rock pressure, has to move somewhere. And it moves just a little so that the weight of the ground over the hole is carried by the rock on either side. However, what happens if this additional load is too high for the rock and it fails?
Well if the rock were just a thin column it would collapse, but if it were thicker, then the weight would just move further into the coal. Now if we came along and moved the coal that had failed, then the hole would just continue to get bigger. But if we leave the coal in place, then the broken coal acts to confine the coal further into the solid. And this confinement gets higher, as the failing pressure continues to move into the wall. And what happens is that this confinement builds up the strength of the coal, so that at some distance into the wall (or face) the coal strength reaches a point that it can carry the weight of the ground above the working area. (For a simple analogy think of a deck of cards, which individually cannot bear weight, but when held together by a rubber band, or a carton, can support quite a bit of weight). (And for those who prefer a more scientific description – the lateral confinement moves the failure from two-dimensions into three, with the minimum principal stress building as one moves into the solid material, and raising the overall failure stress behind it).
This works not only for the coal in pillars, or ahead of the working face of the longwall, but also for the rock that has fallen into the waste and is confined by the rock around each piece. This allows it to regain some strength, and so collectively the broken rock behind the working face (called the goaf or waste) will continue to compress as the full load comes on it, but will carry the weight of the ground from about twice the seam height, all the way to the surface, and with the other end of the "bridge" as it were resting on the confined coal ahead of the working face. (While the width of this bridge varies with depth, coal and rock strength etc, for an initial estimate, you can imagine it as being around 500 ft).
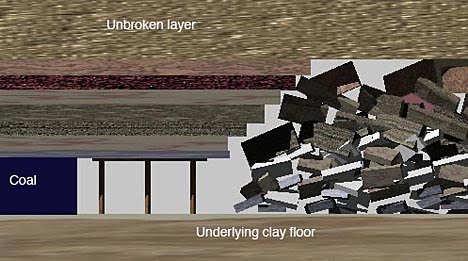
Thus the miner, working at the face, needed only to support only the rock that is up about twice the seam height he was working (in those days women did not do the actual mining). And this could be done with relatively small tree limbs, called props. However, because the rock could break into pieces, the prop support would be distributed, by having a plank, or half split timber, as a bar on top of the prop. Putting one prop at each end thus gave a sort of "goal post" support. Thus, along the face, there would be, at about 4-5 ft intervals, these prop supports holding the roof up. (The coal is made slightly blue in the pictures to give a better contrast - sorry!)
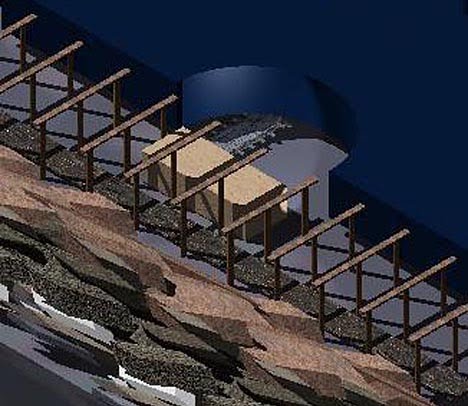
In the initial working of the longwall panel, the coal was undercut by a team of holers, who each cut a slot at the bottom of the seam, to a depth of about 3-ft, and collectively undercut the face over the course of a shift. As the faces grew longer there was a search for a machine that would make that undercut without the intensive manpower. One such tried to mechanize the simple swinging action of the pick.
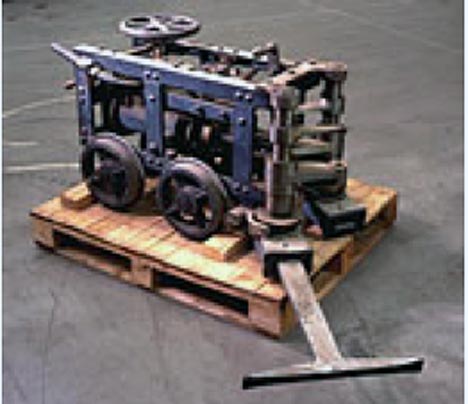
The development of the machine, the coal-cutter, dates from around 1876 when a compressed air machine was developed by Francis Lechner, in which picks mounted on a chain, did the cutting of the coal. (The more modern versions of this look like a chain saw on its side). It took a number of years for the machine to evolve into something that was widely accepted, and by that time the company had been taken over by Joseph Jeffrey (a banker) and became Jeffrey Manufacturing Company. (By the time my dad worked for them they had become British Jeffrey Diamond, and they later became part of the Dresser Group). They had spread to Europe by 1905.
And electrically driven machines were developed, which have not changed that much in the intervening years.
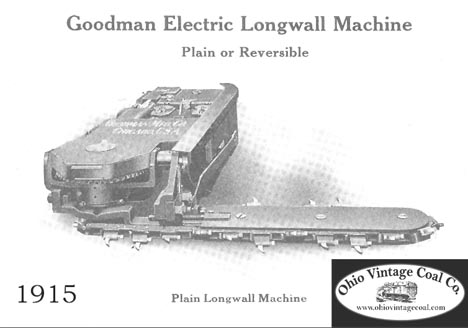
With these machines pulled along the face, undercutting the coal, to give a cut depth that was more typically 7-ft deep, the next step was to break down the overlying coal. Sprags (small wooden wedges) were slipped into the slot at intervals, as the cutter passed up the face – usually run by three men. At the same time holes were being drilled along the face, about 6 ft apart, with a stick of dynamite placed in each one.
After the face had been undercut the coal was blasted down between shifts (7.5 hours) then the collier shift would come in and each man would have about 10 yards of face to load the coal from, and to re-support. To get the coal from the face, a rubber conveyor belt was run along the back end of the supports that were in place before the blast, and the coal would normally not break that far from the face. As the miner shoveled he would also put in a new set of timbers, overlapping the old, and supporting the new working area. Typically this would take another seven hours, with an ideal seam height being about 4.5 ft. Above that the coal volume to move was much greater, and below that it got a bit awkward. For example, below 2 ft thick, you lie on your back, with a prop under your shoulder and shovel over your head - how would I know? (Yes, there was a reason to go to college).
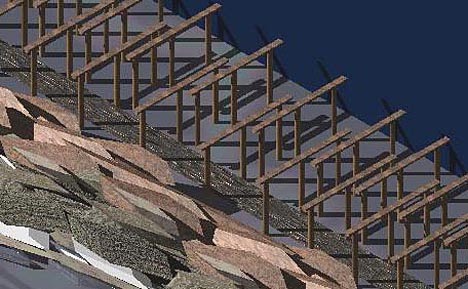
In the third shift, the men would come in and break down and move over the conveyor belt, and then remove the last row of wooden supports, bringing the roof down, beyond the new line of supports. (Smart folk would use a come-along and a chain to pull down the props, young idiots (guess who) would go in with an axe to chop them first). For this was the state of the industry when I went to work in it in 1961. There have been many changes since.
Really seems spooky to me to read this, and then think that 1961 was the same year that the Soviet Union put a man into orbit, and Kennedy said that we would put a man on the moon in less than ten years. The Shippingport commercial reactor had been in operation for three years. And you were down there hand-chopping timber ceiling supports.
Thanks again for this series Heading Out. I do agree with your post mcain6935. Amazing what was still 'normal' as recently as 1961.
Thanks for these articles. My dad was a miner in the South Yorkshire coalfield (as were many members of my family). He was a face worker and they used long wall methods, right up until most of the pits closed in the early 1990s under Micheal Heseltines 'Dash For Gas' (a 20 year binge of our now rapidly depleting North Sea gas fields).
For anyone in the UK (or on holiday here) that wants to see the props/conveyors/coalfaces etc. as per your diagram, actually in situ in a museum 204 yards underground in a decommissioned coal mine, then I'd recommend the National Coal Mining Museum in Yorkshire (http://www.ncm.org.uk/). I have no connection with it, and it's free anyway, but a visit was really moving for me, as it gave me a big insight into the working life many of my forefathers lived for the previous 150 years or more. You can go underground for free, and it starts with pre Victorian mining methods and ends showing early 1990s highly mechanised techniques.
This reminds me of the old saying translated from French, "The more things change, the more they remain the same."
I grew up while hand methods of mining were being replaced by mechanized mining in WV in the 1950s. My Mom's Dad was a worker in the coal mine, he was a hoist engineer, didn't go underground, but was exposed to cars of coal being dumped in clouds of dust, and so died of black lung in his late 50s.
Before I even went to school, grown men would knock on the door and ask Mom if she had any work to be done, just for groceries they would say. Meaning his family had nothing to eat, without begging directly. It was all these proud miners could do to ask for day work. So Mom would have them cut some brush and rake and clean up around the property, and give them a full bag of real food, what once would cost $10 and now runs more like $60-70. It wasn't much, but it was all she could do for them.
The employment in the mines went from nearly 500,000 to under 100,000 in just a few years, a decade or less. And all these surplus workers, proud strong men, were left without means to feed their family. I knew even at the age of 5 or 6 that things were bad. People were living in abandoned coke ovens by closed mines.
Now the mines are hyper mechanized. A crew of a few men can move thousands of tons with a mechanized longwall unit. And the same in mountain-top removal mining, just a dozen men can move thousands of tons a day. To be burnt in power plants and steel mills, pushing the proportion of CO2 in the air higher every day.
If you want to see a museum showing how hand mining was done a hundred years ago, Beckley, WV has an exhibition coal mine, with underground trams and machines, and a mining town just as it was in the 1900s. Just like over in England. There are little houses, a miner's house, a foreman's house and the superintendent's house.
Between my home today and where I grew up and learned to drive is where the "Upper Big Branch Mine" exploded the other day, killing 29 men, and in the old days it would have been a couple of hundred men, with shovels and picks. Just like the old days, we know what causes the "accidents" but we won't stop the reckless cheap SOBs from running the mine into a state of disrepair that causes the explosion.
Kind of like the Oil bidness in the gulf, we know better, but we can't make them do it better.
Heading Out,
Really good descriptions. Thanks for doing this.
You wrote of tree limbs used as props, with planks to distribute the load above and below. That work is the stuff of nightmares. I can't imagine working in a void in the earth wondering if I had used enough props to keep me and my mates alive.
Would the mining engineer calculate the size, spacing and number of props needed based on the depth and character of the geology and thus the weight of rock overhead? When you pull out the prop how quickly would the rock come down? Or does it only fall when multiple sets of props have been yanked out? There really isn't a 'safe' place to stand, is there? I mean, you're a few feet away from tons of rock dropping straight down to a full stop.
With this long wall method is the problem of mine subsidence on the surface less pronounced, or is that a result of many years of compaction in which the spaces between the broken rock are gradually filled and flattened? Or does it only happen with the room and pillar style of mining?
If the seam is much deeper than 4.5 feet, how do you work out getting it all? Is it the case that you work to the height of the seam and with the consequences of a much bigger void? Can you go back into an area that's been worked or is it too unstable to tunnel through the fallen rock?
hkriel
Let me have a go at answering a few of your questions as I am contemporary of Heading out. The only difference is that I worked in the Yorkshire coal field and Heading out in the Northumberland and Durham coalfield. pit props are not tree limbs they are tree trunks mainly spruce imported from Sweden usually 6 inches in diameter and cut off to length. If you are working in a 7 foot seam then they are seven foot and if you are working in a 4 foot seam they are 4 foot.
If you are working on the face and you feel that thing are not safe you will put up a forset, which is a single prop when you have finished cleaning out the coal you will then put up the final props and bars and pull out the forset.
I don't know if they are calculated concerning size spacing and number of props I suspect that it is a rule of thumb worked out over the years and is evolved. Every face is different. I have worked in different coal faces in different seams where the quality of the roof was very different I preferred to work in the seams that had bad roofs counter intuitive at it may seem I always felt that they were much safer. When you took out the props in the gob or goaf the roof would collapse much quicker and the weight of the roof would be thrown backwards onto the debris. A good self supporting roof was particularly scary, as you could have an overhang of as much as 25 yards,you were looking into a void. When the weight came on the whole place used to creak and groan and you could see the roof of the gob slowly descending until it broke and filled the gob and sometimes rocks and debris would knock out the last line of props. Having the attributes of a gazelle certainly helped at times like this.
Mining subsidence is a science of its own how it effects the surface is a function of how deep the seam is how thick it is and how quickly you extract the coal, deep thin seams affect the surface less shallower thicker seams more. The speed of extraction determines how quickly the surface settles down, the quicker the better if you going under a row of house. Concerning subsidence with room and pillar working I am afraid I do not know as I only worked on longwall faces.
When you work a seam of coal you try and get as much out as possible, but once again it is a question of what is best practice in working that seam. In the seven foot seam we always left a foot of coal in the roof to help with supports, you can certainly go into areas that have been worked. In the Midlands under Coventry they used to work a 26 foot seam in three takes they used to drive the roads out too the boundary put in a long wall face and work back towards the main road take out a bottom slice of the coal then drive another long wall face after that face had advanced a few hundred yards then do it again.
I hope that this has helped in explaining a few things
Deep Regards
Yorkshire Miner
YM
Yes, that is very clear and increases my understanding and respect.
Thank you
Thanks for the nice articles ! I am very grateful for them.
I was thinking about what there is to be done with multiple layers of coil on top of each others?
Do you take the top seam first - let it collapse and then the bottom layer? To me this seems to increase the likelihood of collapse in the underlying seam(s) due to the losening of the soil?
Or take the bottom one fist - then letting it collapse? Doesnt seem right either. Same problem.
Perhaps one takes both of them with supports and collapse them at the same time?
Sorry if it is a silly question. :-)