Tech Talk: Controlling the Roof - More on Longwall Coal Technology
Posted by Heading Out on August 8, 2010 - 10:40am
This is another post in Heading Out's tech talk series.
In describing the earliest types of longwall I mentioned that the evolution came from initially putting different mining sections into a line as a way of simplifying the ventilation and the haulage of supplies to the miner, and coal that he had filled into tubs. This is a layout showing one of those early operations, and the roof is temporarily held up either by pit props, typically around 4 – 6 inches in diameter, and cut to length as needed, or small packs. Because the miner was penalized if there was too much stone in the tub (the entire tub would not be counted) he could stack the stone he found in small packs, with the larger stone on the outside and small stuff shoveled within to provide the roof some support, as needed.
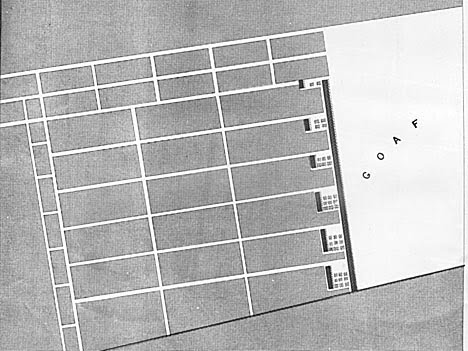
The first transition was to change the direction of mining so that it wasn’t perpendicular to the goaf (or collapsed waste) but parallel to it, and then to join all the individual stints into a single face. At this point the supports became more organized and regular plans were developed to ensure that the roof was supported. (These were assembled in a book that the mine manager had to certify, with the conditions for each face specified, and any special support locations laid out.) An early version of such a plan showed the plan and spacing of the props.

The face is shown after it has been undercut, but before it has been fired, and the coal blasted down. In addition the back set of supports would be removed, and the conveyor advanced, before the shot went off. After the back row of supports were removed, it would look more like this, and more typically undercutting and inserting the powder would take pace after the move.
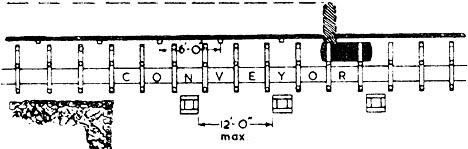
The path of the coal cutter can be seen, and thus use of square sets of timber that were used in bad ground to help support the roof long enough to remove the coal. These replaced the stone piles that had been used earlier. Personally I did not work on faces that used them, except when we had a major face collapse, and we had to mine through it – but that’s another story.
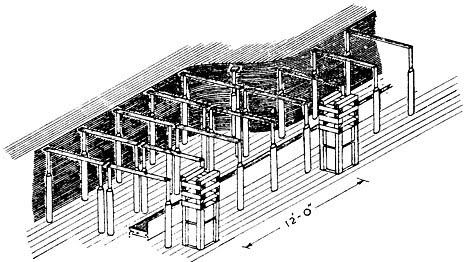
Once the back set of props was removed and the conveyor split, moved forward and remade, then the coal was blasted down and then, as each man loaded out his fifteen yards of coal, the new set of supports was installed.
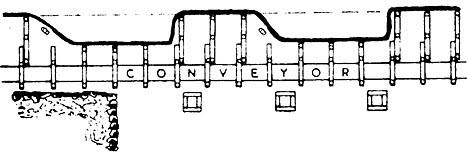
The reason we could get by with using wood was that the process was relatively slow, and we would mine only one cut a day. This gave time for the roof stresses to redistribute, and the collapsed roof to build up and support the overlying strata.
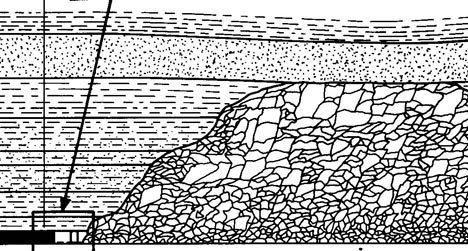
As mining began to mechanize, one of the first things that changed was the material of the roof supports. The first step was to change the wooden bars on top of the props for steel ones. Sounds like a good idea, right?
Well imagine that you are kneeling on the floor and you have to erect one of these supports. You put the long bar on your shoulder,pick up the axe and a wedge in one hand, the prop in another, and raise your body until the bar is pressed against the roof. Then you put the prop in the middle, and slide the wedge on top, and tap it tight with the axe. With the bar then stabilized, temporarily, you get a second prop and put it at one end and tighten it into place, and then do the other. Then you remove the central prop. With a wooden bar it was relatively easy in heights from 2.5 ft to 5 ft. With the greater weight of the steel it was harder to move, more critical that you be near the middle when you start, and more vital that the first prop was close to the middle. With a wooden bar there was also a little flexibility in driving in the wedge, absolutely none with the steel bar. Oh, and since we were re-using these (pulling them out of the waste as the last row was collapsed) they pretty soon got bent and so had to be straightened a bit before they could work.
But that was the easy step (in retrospect) because the next thing to replace was the wooden prop. Both the wooden prop and bar were easy to move. But to replace the prop the first idea was to use a friction prop. Here’s how it worked:
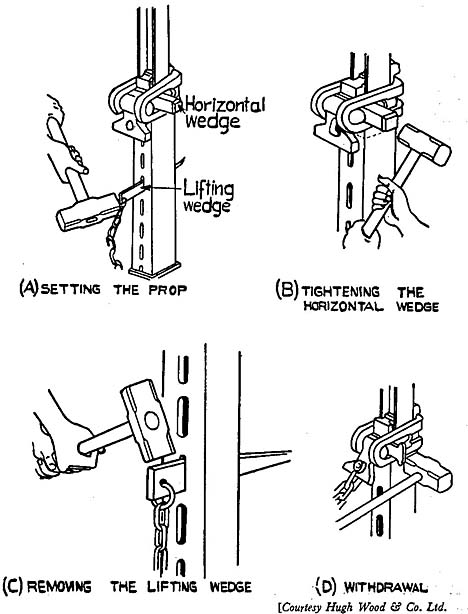
You lifted the central section until it was about right, then tapped the lifting wedge until the prop was tight against the bar. Now you could move to one side and tighten the horizontal wedge that gripped the sliding section and held it in place. Then you removed the lifting wedge. And when you wanted to remove it, all you had to do was tap the horizontal wedge.
It had the advantage that as the roof stress changed so the prop was intended to yield, with the inner section sliding within the friction band, rather than failing as the wooden prop would if the stress got too high. However, you might want to remember that here we were doing this individually in relatively low coal (at least we didn’t have to saw them to length) with a 6-ft steel bar resting on your shoulder while you try and drive these wedges in. It was a learned art, one of the first things to learn was not to hold the prop above the wedge while you tap it out. The prop drops when released and will hit your hand – usually the thumb – and it has the weight of that steel strap on top of it. Funny how you still remember!
They didn’t last long, for a variety of reasons, but were replaced with the forerunner of today’s roof support, the hydraulic prop. The first ones were relatively simple, and heavy, but much easier to use.

Simply you put the pump handle in the socket, and started pumping. This moves fluid from the upper reservoir to the lower, pushing the central cylinder and the top cap up, and against the prop. To release it you put the handle in the link, and pull, and slowly the prop sinks. Much easier to work with.
But that was only the start, and moving these by hand was still slow, and so the transition to full mechanization began. And before long instead of the simple hydraulic prop, the roof was supported by massive, and powerful hydraulic chocks, but this also required other changes to mining practice. For, as it was said at the time, “We cut the coal by machine, we transport the coal by machine, isn’t it stupid to still load it by hand?”
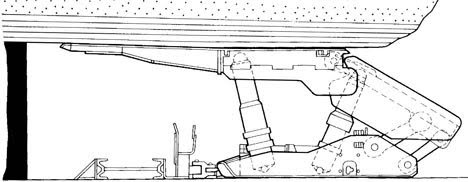
HO: Thanks, again, for the post. Geez! Those friction props sound like they were a real pain in the rear to set up or knock down. I can surely see that it was a rather heavy balancing act trying to hold up the bar and get that thing set and run up there! thank goodness for hydraulic jacks! Here is a little verse: Come all ye fellers, so young and so fine. And seek not your fortune in the dark, dreary mine! It will form as a habit and seep in your soul. Till the blood of your veins runs black as the coal! It's a Merle Travis song my friend and I used to sing when we were fine young men! Heh! Heh!
Just to say I am really enjoying your coal mining posts Heading Out.
I was brought up in the East Midlands coal fields and I do not think myself old but but already very few persons can relate street names or local features to a once thriving coal mining industry. In Cornwall the relics of tin mining are treated heritage sites but the coal pits have all been flattened and the slag heaps landscaped so that nothing is visibly left, I wonder why that is.
Thanks for all your personal reflections on this. I see the United Kingdom still produces a little coal.
Is the mine you worked in still open? (It would seem like the coal would be gone long ago.) Do you still have relatives or friends in the mining industry there?
The mine closed after operating for over a hundred years shortly after I left to go to college. There were still several seams untapped, and the seams we were working were not fully mined out, but it will now be all flooded, and the shafts were concreted in (plugged like an oil well) and soil graded over it so that you drive past the site now and would never know that a mine once was there.
My cousin was the last in the industry and he moved over into civil construction - helping, among other things, to drive the Channel Tunnels. He too is now in America. I don't think that there were any of my class, other than one that went into civil construction (water tunnels) that stayed in the UK.
I would like to invite people from the oil drum to come and join the live chat on peak oil and the collapse of the industrial civilization...
http://express.paltalk.com/index.html?gid=1344986069
Many thanks Heading Out for this excellent series. Coal is clearly going to be a major part of the energy mix in the future, and a Hubbert Peak for coal could possibly in future be even more devastating than the one we are experiencing for oil. It is vital that the process of coal mining is being explained so well so we can assess the prospects for the future.
My question: The UK has some coal remaining, and perhaps once North Sea oil is gone we will return to mine the anthracite that remains in my native South Wales. How much mineable coal remains in UK, and how do we go about reopening the mines if/when the time comes?
HO, there is a good new book "The British Industrial Revolution in Global Perspective" by Robert Allen.
He asks why did the Industrial Revolution start in England, when other countries had the same pre-existing conditions.
His thesis is that British labour was far more expensive than Continental labour, and the availability of cheap English coal was greater.
Capital was also less expensive in Britain at the time.
So capital had an incentive to develop coal burning machines to replace labour sooner in England than elsewhere.
the steam engine, cotton mill and blast furnace gave Britain not only a better standard of living, but were a key building block of the economics of Empire. They stumbled into Empire
Its interesting because it shows why the logic of fossil fuels is so compelling, and why the "virtuous spiral" of industrialization is so hard to break
One observation is that Asia today has raced profitably into fossil fuel industrialization despite the cheapest labour anywhere, and despite much more expensive energy. So the equation does not seem to hold today.
HO, I just wanted you to know that I read all of your excellent posts. I don't feel qualified to comment, but enjoy and learn from every post. Thanks for your hard work. Great stuff!
Yes - thank you - your series is something I look forward to every Sunday.