Tech Talk: Driving a tunnel and holding the walls with bolts
Posted by Heading Out on September 12, 2010 - 10:55am
Last week I wrote about the development of steel girders, and how they were designed to hold the immediate roof above the tunnel, but not the weight of rock all the way to the surface. By allowing a natural bridge of rock to develop around the opening it is possible to lower the amount of support that the rock actually needs. This takes a bit of time, but if you wait a short while before putting in a support, the relaxation of the rock around the tunnel into the open space will generate a zone of compression in the rock around the tunnel in much the same way as building a Roman bridge relied on the compression of the blocks around the opening to mutually support one another, and the load applied to the bridge. Because of this, the amount of support that is required can be reduced considerably from that needed if the tunneling team were to try and hold the rock wall in its original space. (For those of a scientific bent that want to look at this in more detail it is known as the “Method of Characteristic Lines” or the Convergence-Confinement Method and Charles Fairhurst, was an early proponent).
The problem that arises, with putting large rigid steel girders into the tunnel to hold it up is that these tend to be rather stiff and unyielding. One way of getting around this was to put the bottom ends of the arch girder into a frame where the “H” section of the girder had a wooden plank in the lower end of each side of the H. They were held tightly by metal straps, but as the weight of the overlying rock continued to increase as the walls moved into the hole, the girder would slide between the two pieces of wood, or stilts, yielding at a set load, and allowing the walls to deform and build up a natural arch.
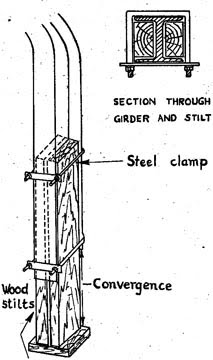
But the design still had to estimate the size of the girders needed so that they could be on hand as the tunnel was driven, and if the design proved wrong, then usually the discussion ended in court and a lot of productive time was wasted. A more flexible method of holding up the walls was needed, and it came from the combination of two different rock support systems.
The first of these is known as a rock bolt. It has been suggested that the first rock bolts were just rods of wood that were stuck into holes in the roof, and wetted, so that they swelled and gripped the rock. While these worked passively (in other words they did not apply support to the rock until the rock moved, and their presence and acceptance of load then began to resist the movement) they were not, initially, seen as a great help in helping develop the natural tendency of the rock to hold itself. Now there are whole books that have been written on the use of rock bolts, cable bolts and cable trusses (a combination of the first two). I may offend some purists here, but I am going to chop through a lot of that development, and simplify a whole lot in what follows.
If a rock bolt could be inserted in a hole in such a way that it squeezed the rock along the borehole, then perhaps it could be used to build larger blocks of rock, from the rubble around a tunnel, and thus build the bricks, that would lock together as the rock moved into the tunnel, building that natural arch. To generate the compression in the rock, the rock bolt was designed in two main parts, a threaded rod that ran from the mouth of the hole, to the back, and an anchor system which, as the rod rotated through it, pulled a small wedge down into the anchor section, which was spread to grip the rock, and then resisted further pull down the hole, so that the rod went into tension as the wedge tried to advance further, and the rock between the anchor and the bearing plate on the end of the hole, was compressed.
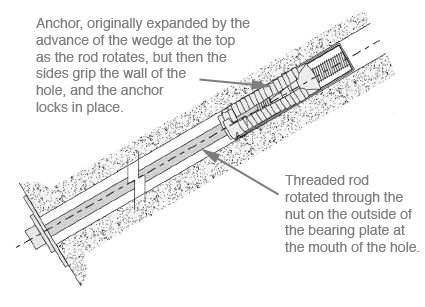
There are a lot of things that can go wrong with this concept, and in the 1970s when bolts in a mine were tested the vast majority were not working as they were supposed to, and as a result a regulation was passed that a mine should regularly test these bolts, by putting a torque wrench on the installation bolt head of a representative sample every day, correcting any with a problem. The torque would be a measure of the load the bolt was carrying, and how effectively it was holding the rock together.
This was an expensive requirement and alternate bolt designs were looked for, to find a way of installing rock support that would not need this testing. And the inventors went back to the idea, which I mentioned, of holding the rock along the full length, rather than just at two points. (I have at times suggested that this was looking for a way of using the “nail” idea, rather than the screw – nails are generally cheaper). There were two ideas that came along, The most popular was known as the “Split-Set” and was invented by a colleague of mine, Jim Scott. The idea was very simple, in essence take a steel pipe, just larger than the size of the hole being drilled, cut a slot along the length. Then compress the pipe and stick it into the hole, with a bearing plate on the bottom. The released pipe will grip the rock along its length, and provide immediate resistance to motion. There are two things that made it as successful as it became, internationally. The first was that it could not be tested conventionally, and thus the testing crews were not needed. But while that got the bolt an entry into mines it was its success in holding the roof in a simpler, yet cheaper way, that led to its widespread adoption.
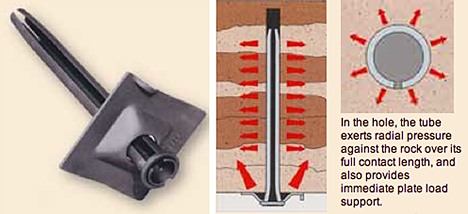
The alternate method was to fill the gap between the steel rod and the rock wall with a resin. This became known as resin bolts, or full-column rock anchors, and there have been a wide number of different designs. Very simplistically a hole is drilled, and cartridges containing a resin and a catalyst are inserted into the hole. Then a reinforcing rod is inserted into the hole, and spun as it is pushed to the back of the hole. This mixes the resin and catalyst so that the resin sets very quickly, and grips both the steel rod and the rock. It works well in rocks where, for example, the chemistry of the ground water might corrode an unprotected bolt.
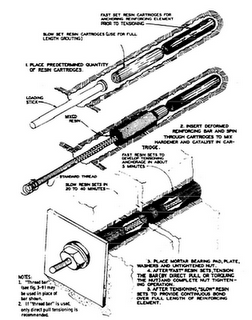
One can thus go into broken rock, and by using bolts to build larger blocks of rock, have these intersect one another and “build a bridge” to hold up the overlying rock. The problem comes with the raveling or crushing at the edges of these blocks, and the slow failure of the tunnel surface. This is now solved with shotcrete – but I’ll talk about that, and putting girders, bolts and shotcrete together in a later talk.
Another touted advantage of the resin bolt is that it seals the shale layers in the top from exposure to moisture which weaken the shale and may cause a roof fall even in bolted top. Sells a lot of epoxy from DuPont and others.
Miner foremen carry rods to poke the top looking for hollow sounding top indication bad top or separated strata layers.
HO: Thanks for the post, once again! Always enjoy these with a cup of coffee on Sunday morning! Was just wondering if one uses a pneumatic hammer to drive those split-sets in.
Thanks, appreciate the kind words. Split-sets were initially more rapidly adopted into metal mines (over coal mines) because most of the drills were pneumatic (now increasingly hydraulic) and they could be easily adapted for installing the bolts.
Interesting. In typical heavy construction we end up using variants of all the rock bolt systems to fasten building components to the concrete. I'd never considered that the same applications could be used to hold rock together and create arches. We always have the luxury of putting steel reinforcement in our 'rocks' before they harden if we need concrete arches ?- )
Whats really interesting is how similar this is to pegged wood construction using blind wedges.
I have to imagine the failure mode is the same i.e you open up a natural fracture causing rapid failure.
Assuming water is present this fracture can develop overtime.
For a wooden chair you have a split for a mine its a tad worse.
And sort of going back it seems like that simply encasing a tunnel with dry rock arches i.e adding specially shaped loose rubble that would be compressed would do a similar job.
Not saying you do that simply that it seems to accomplish the same thing. Makes me suspect that your next article may well show that the shotcrete is under compression and acts in the same manner as my roman arch :)
I was at an old uranium mine with my brother once - the roof was covered with bolts & the entrance was shotcrete - I remember looking at the bolts & thinking their purpose was to prevent rocks from falling on people. Essentially correct. A purpose of the bolts is to tie layers of rock together (where you can't see the layers and cracks) so the arch doesn't fall apart on you. Even if there were no faults & cracks in the rock though, the tensile strength of the bolts still helps the rock remain in compression.
Another old hardrock mine I saw had a short section of passage where the wooden supports were splintered and crushed because the roof had lowered over the years to about half its original height. The walls and roof were bowed and flexed as if they were made of plastic. Scary odd. No rock had broken. An example of the tremendous forces at work.
HO,
I appreciate your effort on these posts. Though I rarely respond to your articles, it's not because I'm disinterested but simply that the tech is so far from my realm of expertise and business interests.
Your articles are like reading Scientific American but focused on applications -- the evolved technology for oil and mining. Great basic education for those of us who want to learn about everything!