Death of a Battery
Posted by Gail the Actuary on March 20, 2013 - 1:15pm
This is a guest post by Tom Murphy. The original can be found at Do the Math.
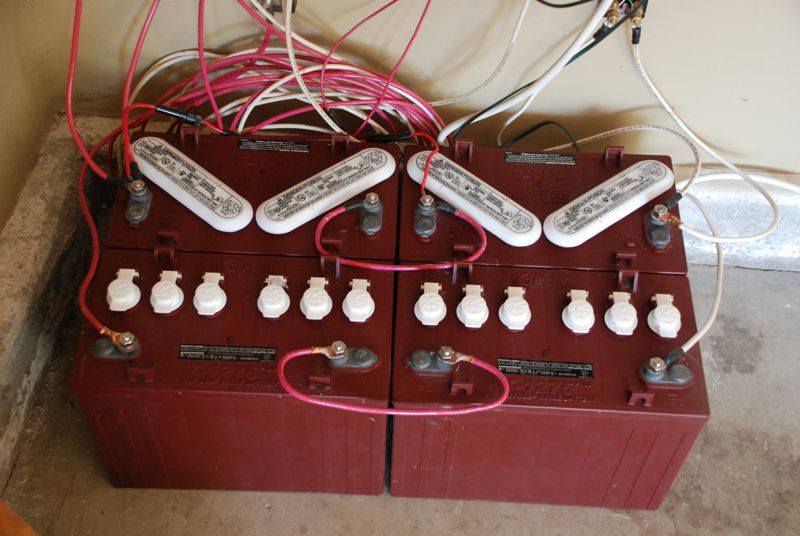
All the metrics looked great. The 2.7-year-old lead acid batteries in my off-grid photovoltaic system appeared to have settled into a consistent mid-life performance. Monthly maintenance (equalizing, adding distilled water) promised to keep the batteries in prime condition for some time to come. Based on cycle depth, I expected another 2.5 years out of the present set of batteries. Life was good.
Then, during my absence over the course of Thanksgiving weekend, one of the batteries expired. No forewarning. Just gave up. A previous post expressed an overall disappointment in batteries, now reinforced by this sudden nosedive.
In this post, I’ll show the metrics on my system detailing the demise of “Battery E.” The gruesome graphics are intended for mature audiences.
Everything was Peachy
Let me first recount the status of my battery system as detailed in a post from September of this year.
Thus far, I have used Trojan T-1275 batteries in my PV system—each 12 V, each rated at 150 Ah (yielding an energy storage of 1.8 kWh: just multiply voltage by charge capacity). Empirically, I found that my batteries have always behaved as if their capacity was 125 Ah, from day one. During the first few years of my growing PV system, I operated with two batteries, labeled A and B. I worked them pretty hard, and they gave up around the beginning of 2010. I replaced them with two fresh batteries on 2010-02-15 (batteries C and D), and added two more in parallel a few weeks later on 2010-03-04 (E and F).
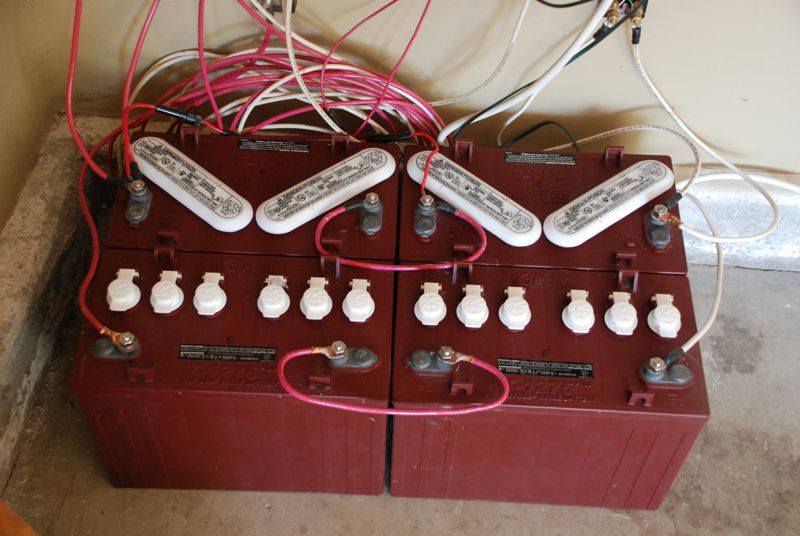
Studying the discharge curves for every night, I found that the batteries had settled into a very stable performance, actually improving in years two and three from year one.
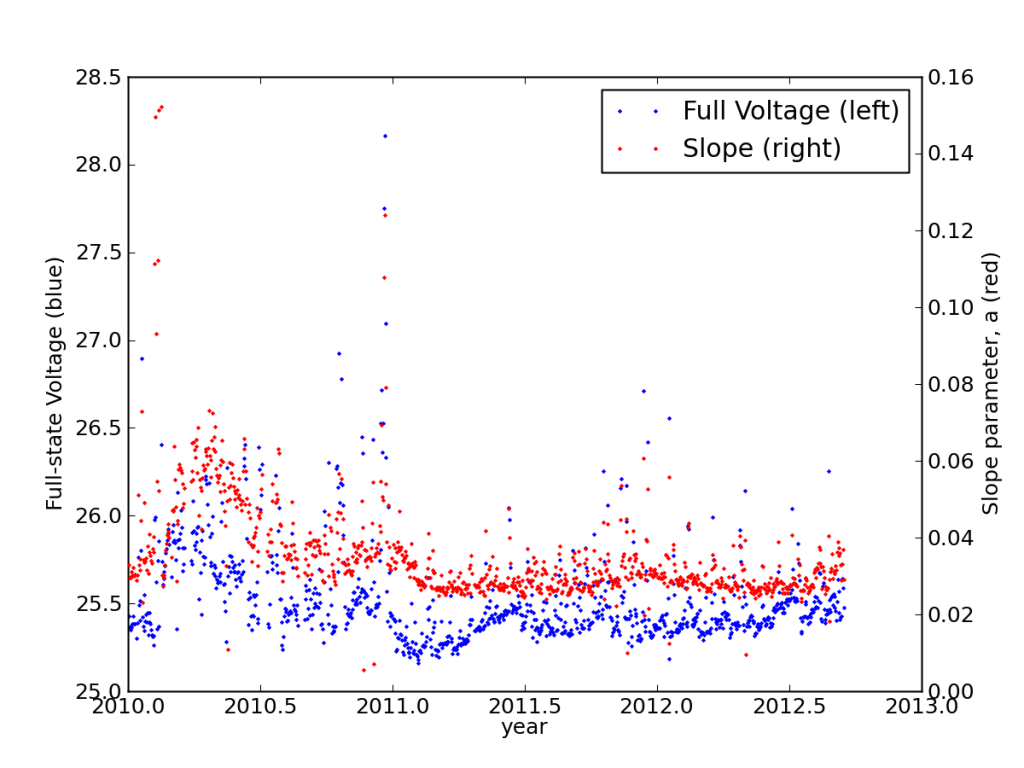
This is also seen in the load-corrected state-of-charge plot vs. voltage, where recent performance edged closer to matching the battery specifications—after adjusting for the realized capacity.
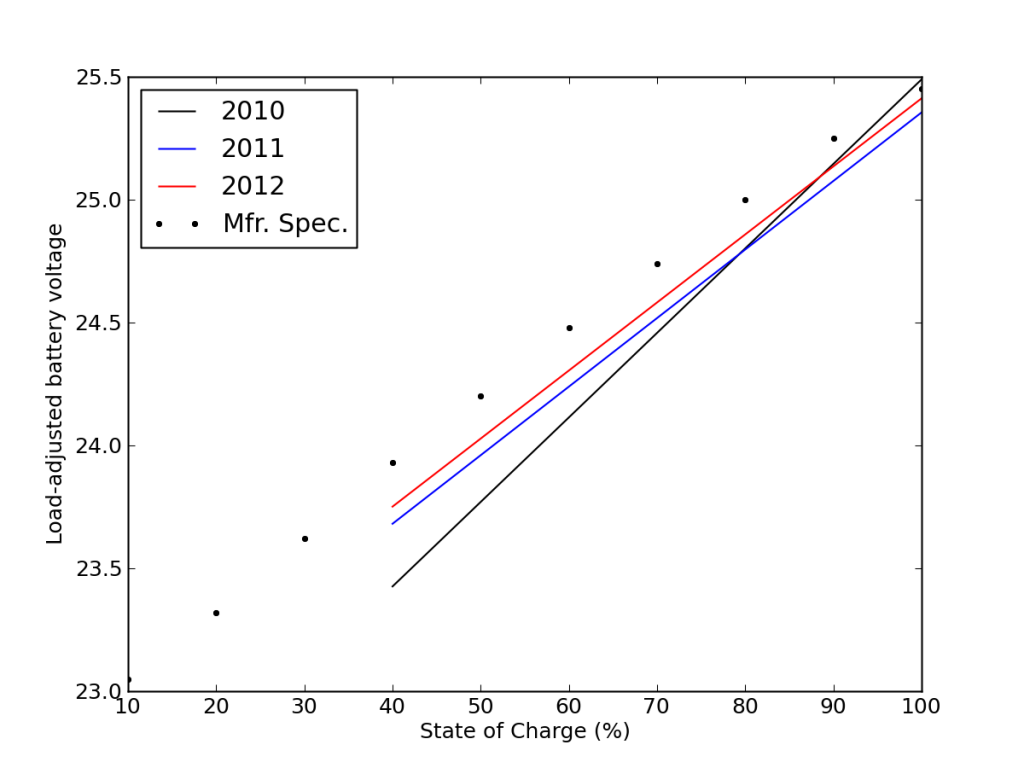
I calculated my average daily cycle depth to be 31%, and from cycle curves, expected 2000 cycles at this depth. But 995 days after installation, battery E fell off the cliff. So much for my rosy statement in September:
At this point, I have sourced 1686 kWh from my four batteries in 30 months, or 422 kWh each. At a de-rated 1.5 kWh per battery, I have gone through 281 full-depth equivalent cycles. In about 915 days, this means my average cycle depth is 31% and I might expect 2000 such cycles (5.5 years; 620 full-depth equivalent cycles) at this level. So judging by this, I’m almost halfway done.
Oh that it were true.
Watching the Crash
Every day, an automated script grabs data off of my solar recording apparatus, and most nights I check the day’s performance. Below is a typical plot of the five-minute resolution data. The post on PV efficiency details the curves, but in brief: red is solar input; cyan is the load (refrigerator cycle spikes evident), black is battery voltage (right-hand scale), green is battery state of charge (percent full), and the yellow dots indicate what fraction of battery current is flowing to battery chain E/F. The reference line at 50% is a useful gauge. Ideally, battery chains C/D and E/F would contribute equally to sourcing or sinking current, and the dots would always be at 50%. Minor ticks on the horizontal axis are at one-hour intervals, so it’s fairly straightforward to read the time (0.25 days is 06:00, etc.).
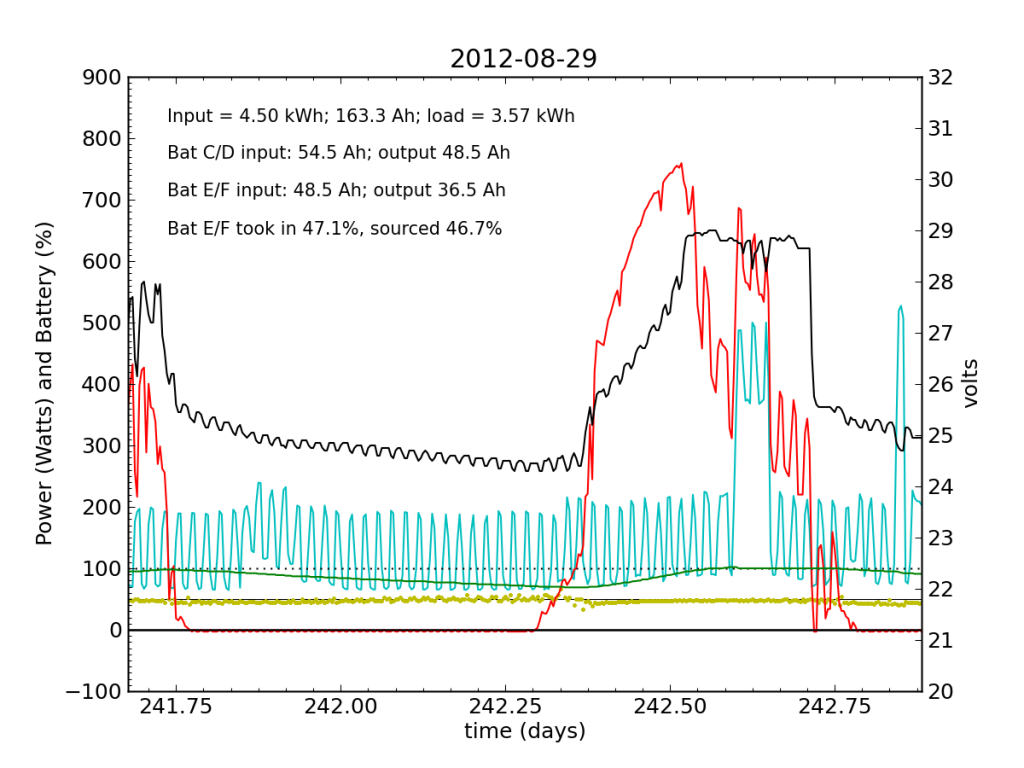
We see here that during the day, when the batteries are charging, the two chains receive nearly identical current (and therefore similar power, since their voltage is guaranteed to be the same by the magic of connective copper). In the evening, Battery E/F doesn’t contribute quite as much as C/D, but after midnight, it reaches parity, and even wiggles around depending on load variations due to the refrigerator. I am accustomed to seeing Battery E/F slightly under-perform, but not by a large margin.
Notice also the gentle slope of battery voltage decline during the night.
Chronicling the Demise
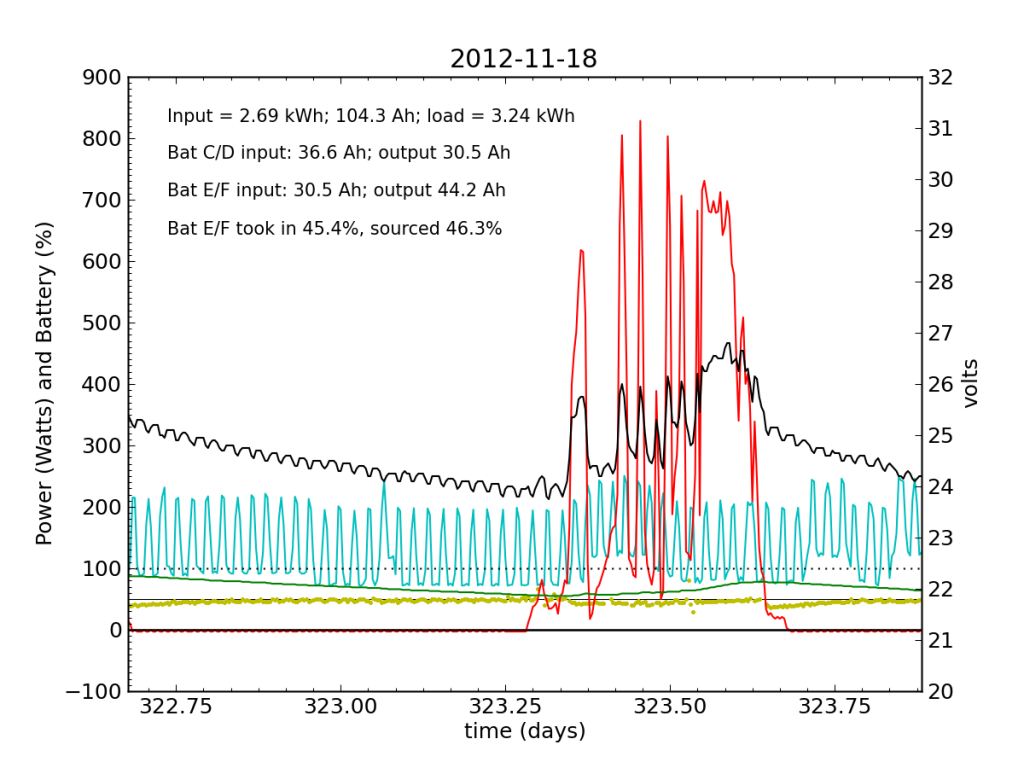
November 18 was a partly cloudy day, as seen by the spiky nature in the red (solar input) curve. The battery did not get fully charged, but we see the typical dance of the yellow dots; just shy of 50% for the most part.

November 19 was a sunny day, but the previous day’s deficit caught up to the (undersized) battery bank, causing the inverter to switch to utility input at about 04:00. During times when the current into or out of the battery is small, I do not plot the yellow dots, because they can become meaninglessly scattered when comparisons between small numbers are made. Otherwise the battery looks pretty normal: no alarms.
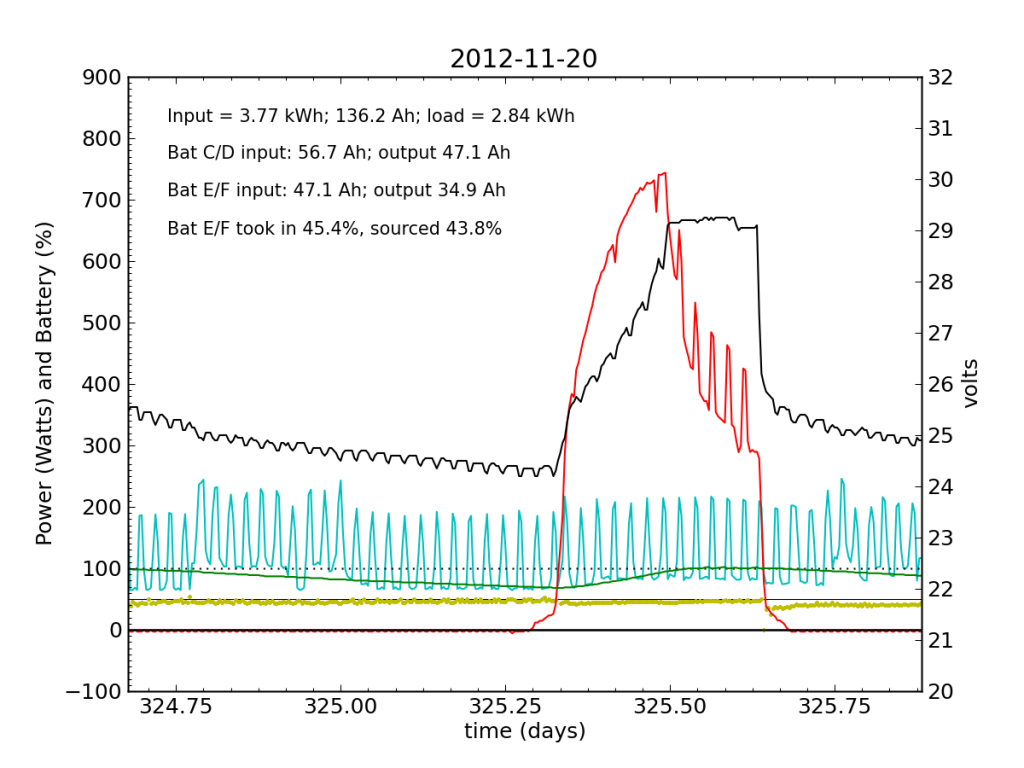
Tuesday, November 20 is a picture-perfect example of what I like the PV system to look like. Sunny weather, plenty of time spent in absorb state (battery voltage plateau, while solar utilization scales back to accommodate), loads cranking away doing their thing, and the yellow dots behaving reasonably. Aside from the fact that the system is requiring 200 W to maintain absorb state at the end of the cycle, things look great (absorb state took just 130 W on 2012-08-29).
On Wednesday, after weather in New Mexico blocked our attempt to shoot a laser at the Lunar Reconnaissance Orbiter, I did scramble out of town for a weekend in the mountains. No internet. I had no way to check on the system’s performance on Wednesday. But little worry on my part. I’ve left the system essentially unattended for months while away (though checking remotely), and nothing went off the rails. I had no reason to expect anything different.
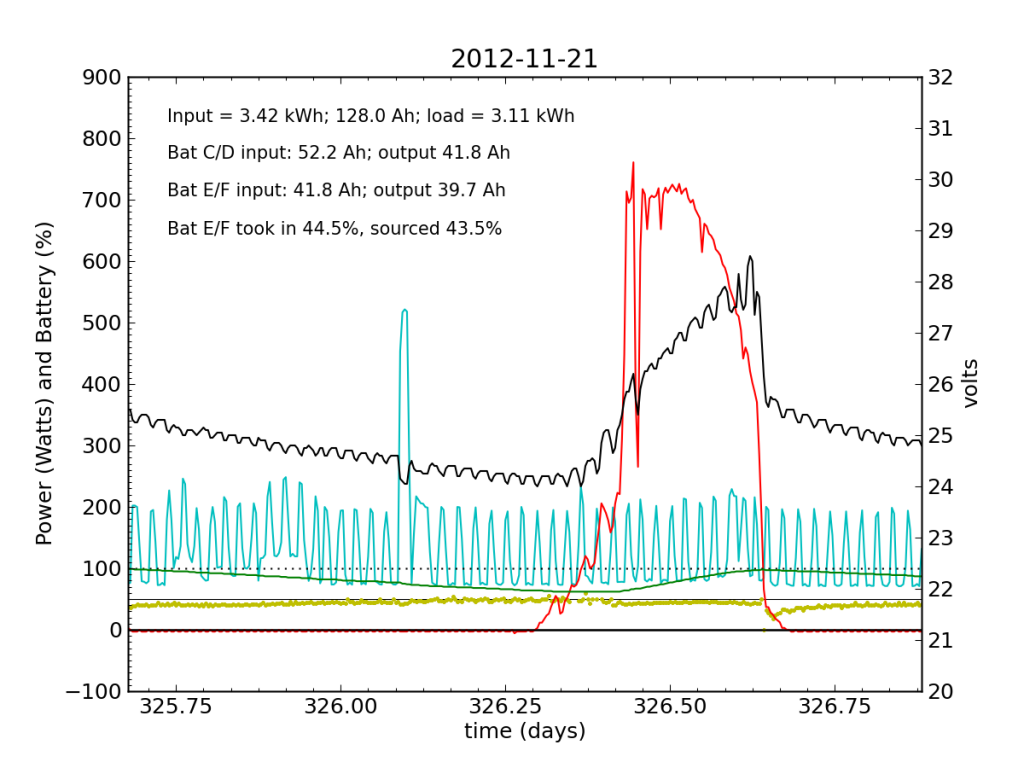
Undetected by me, the system started showing a problem on Wednesday, November 21, when Battery E/F was only sourcing 25% of the power immediately after sunset. It also did not quite reach up to 50% in the afternoon, as it normally does. Would I have caught this problem in my often hasty scan? Who knows. I didn’t get to try.
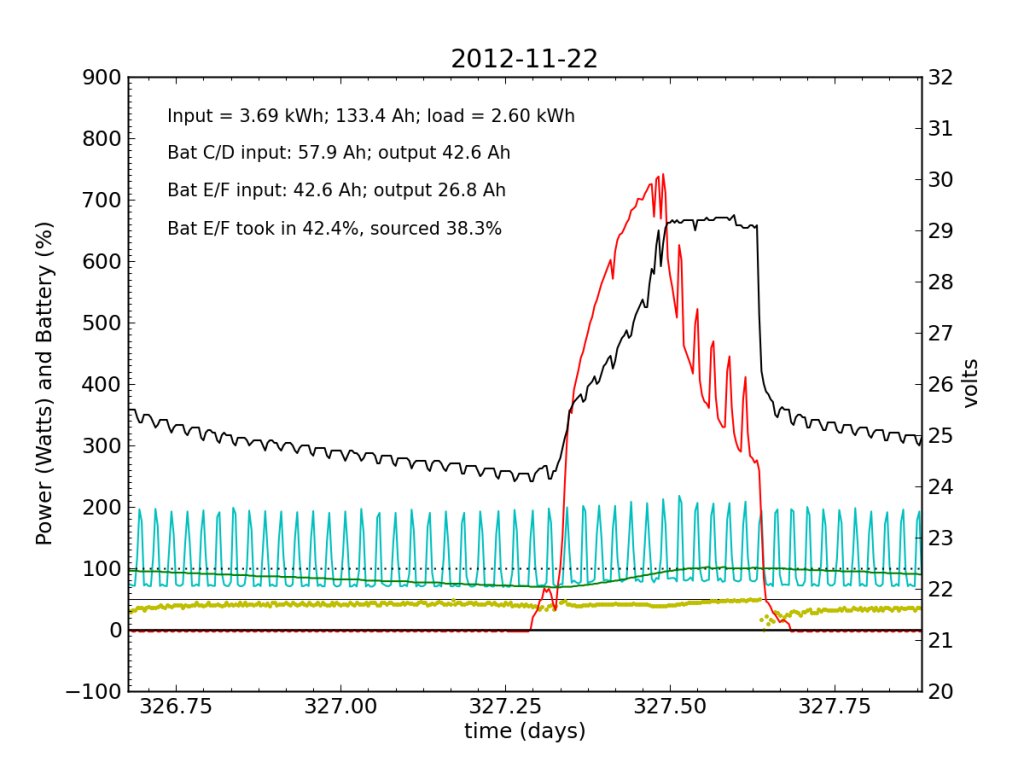
Thanksgiving Day, while we fussed over cooking a 12 pound turkey in a small charcoal grill, the PV system started showing serious signs of trouble. In a 24-hour average, Battery E/F only took in 42% of the input power, and sourced only 38%, dipping alarmingly near zero just after sunset.
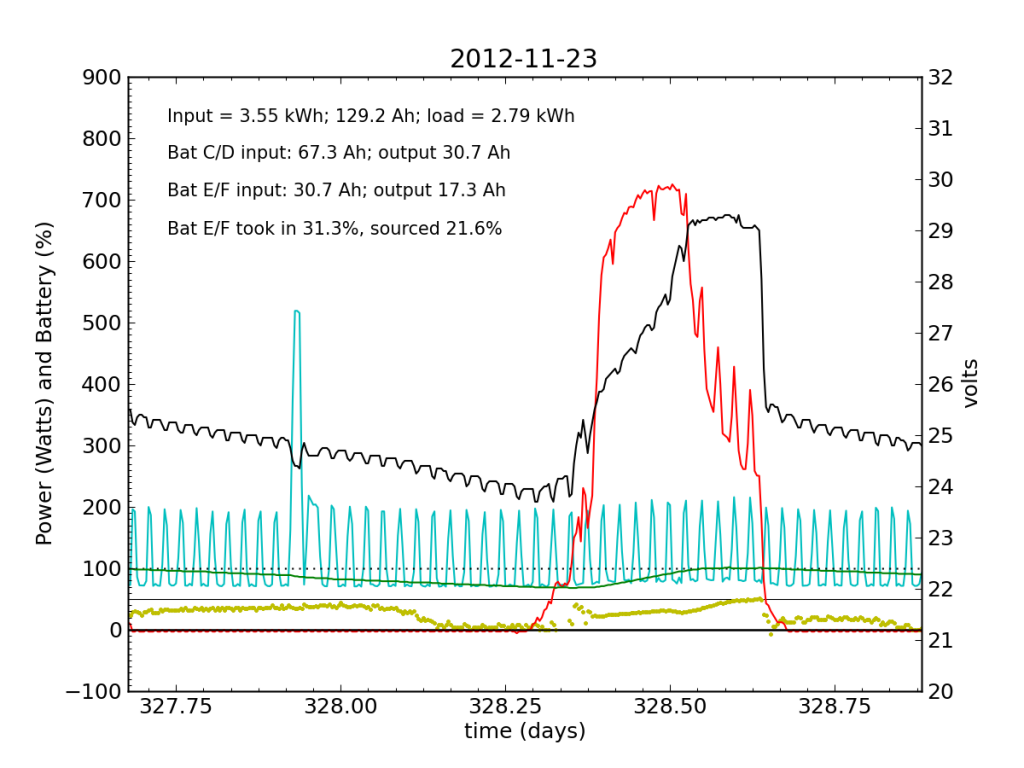
Over the following night and day, things went seriously ill. Around 02:00, Battery E/F began to shirk its share of running the house. It decided that 10% was enough. The battery voltage turned downward as Battery C/D stepped up to fill the gap. During most of the ensuing day (Friday, Nov. 23), Battery E/F accepted far less than its fair share of charge. Over a 24-hour period, it only accepted 31% of the total charge (about half as much as did Battery C/D), and only contributed 22% to driving loads.
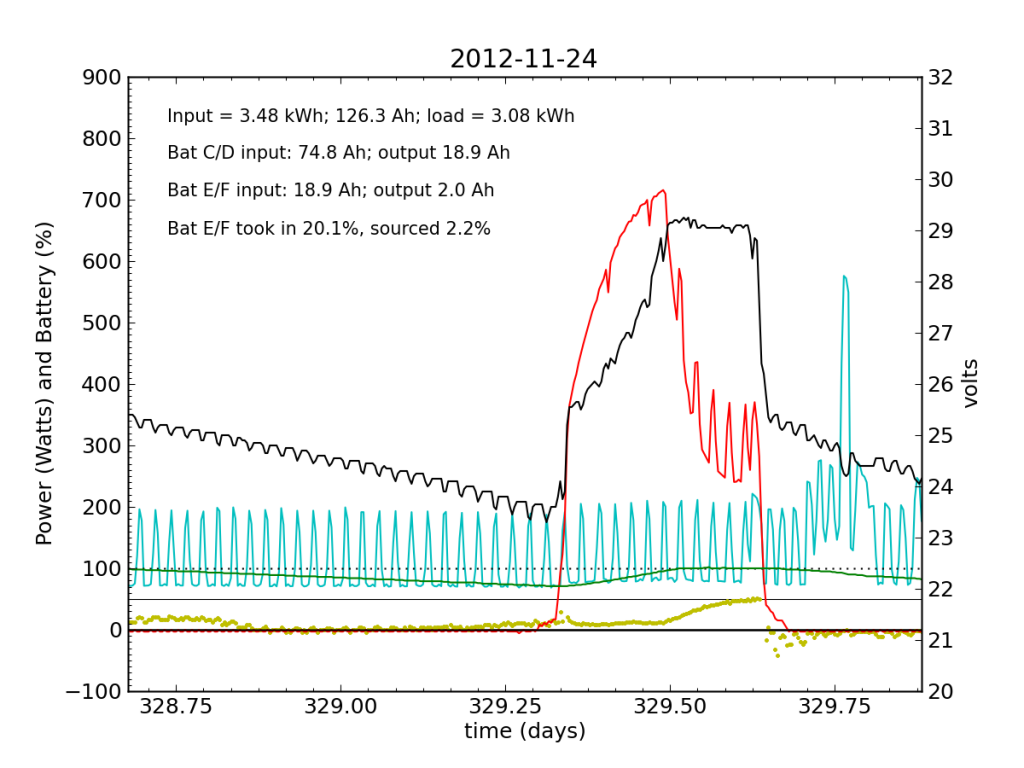
The failed battery proved itself to be practically useless the following night, and only really started accepting appreciable charge once Battery C/D reached its absorb potential and began refusing current. This time, after sunset, we see a net transfer of energy from battery C/D into battery E/F (yellow points in negative territory). Bad battery!
It was at the end of this Saturday that I returned home and checked the system. Imagine my surprise, remembering the performance from 2012-11-20 and suddenly seeing the plot above with an obviously defunct battery! It only contributed 2.2% of the outbound juice in the 24-hour period from 21:00 to 21:00.
Be advised that now the green line (percent full) has lost meaning, as the capacity is no longer that of two fully-functional battery chains in parallel, but effectively only half that.
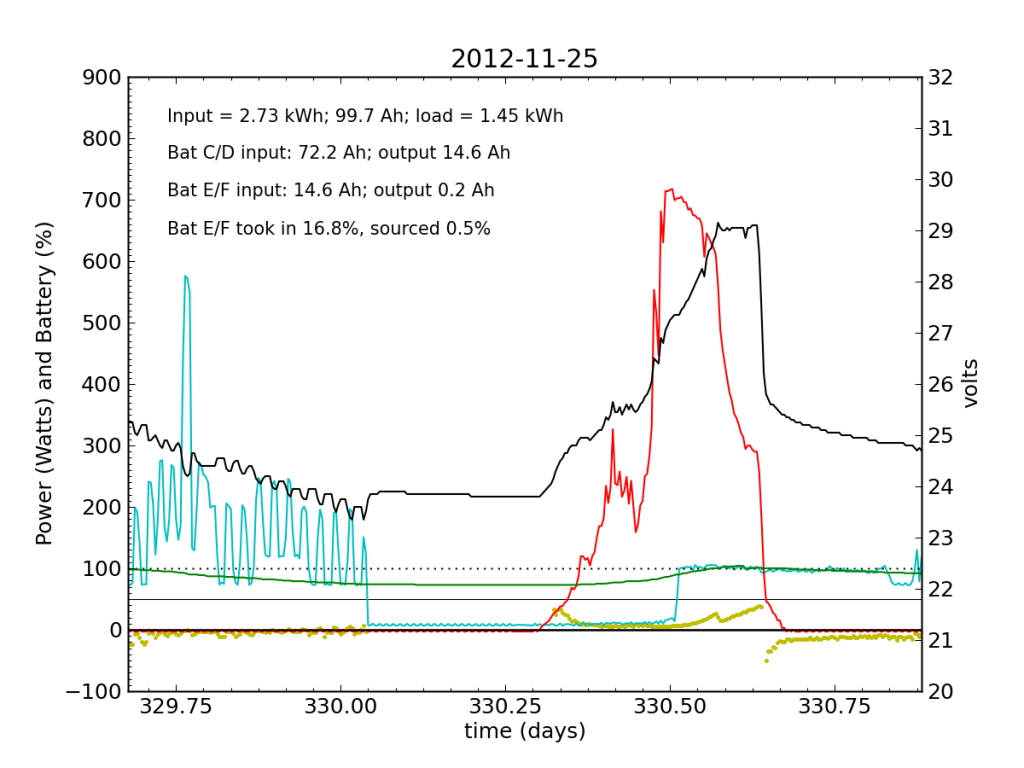
Around 01:00 on Nov. 25, the steeply declining battery voltage had fallen far enough to trigger the inverter’s switch to utility input. Battery E/F was effectively a drain all night. The following day (Sunday, the 25th), some charge managed to get dumped into Battery E/F, but not much. It was now dead weight, contributing nothing while sucking up available energy. At noon, the inverter switched back over solar/battery. That morning, I had accepted the fact that the system was seriously impaired, and disconnected the refrigerator from the PV circuit, plugging it into the utility outlet for the first time in years. So sad. The result is smoother load plots from this point forward, while my TED plots are much messier than usual on account of the change. We see a net E/F drain again at night. I did not have much time to characterize the problem that day, playing catch up on work from spending a few days away, and also having to write a blog post from scratch.
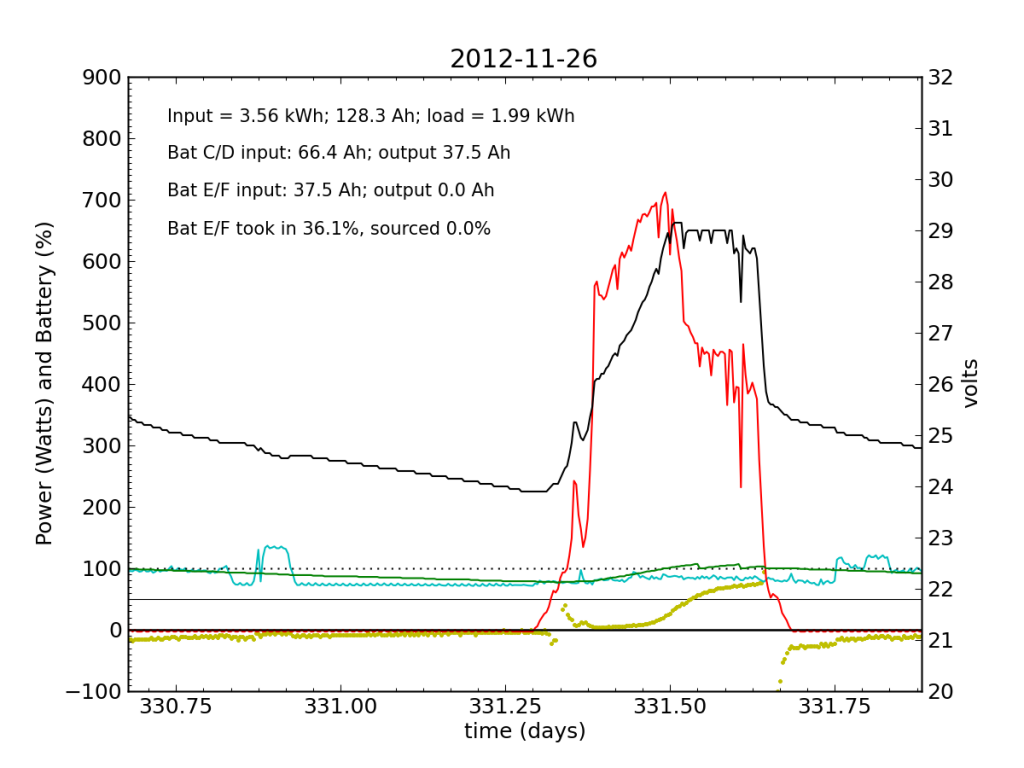
Without the fridge load, Battery E/F took in a bit more juice (thanks to longer absorb cycle), but at this point is still a net drain at night.
That evening I measured batteries C through F to be 12.33, 12.39, 11.12, and 13.59 V, respectively (both chains must add to the same voltage). So it’s Battery E that is the problem. Battery F is super-charged (and oozing a bit of electrolyte).
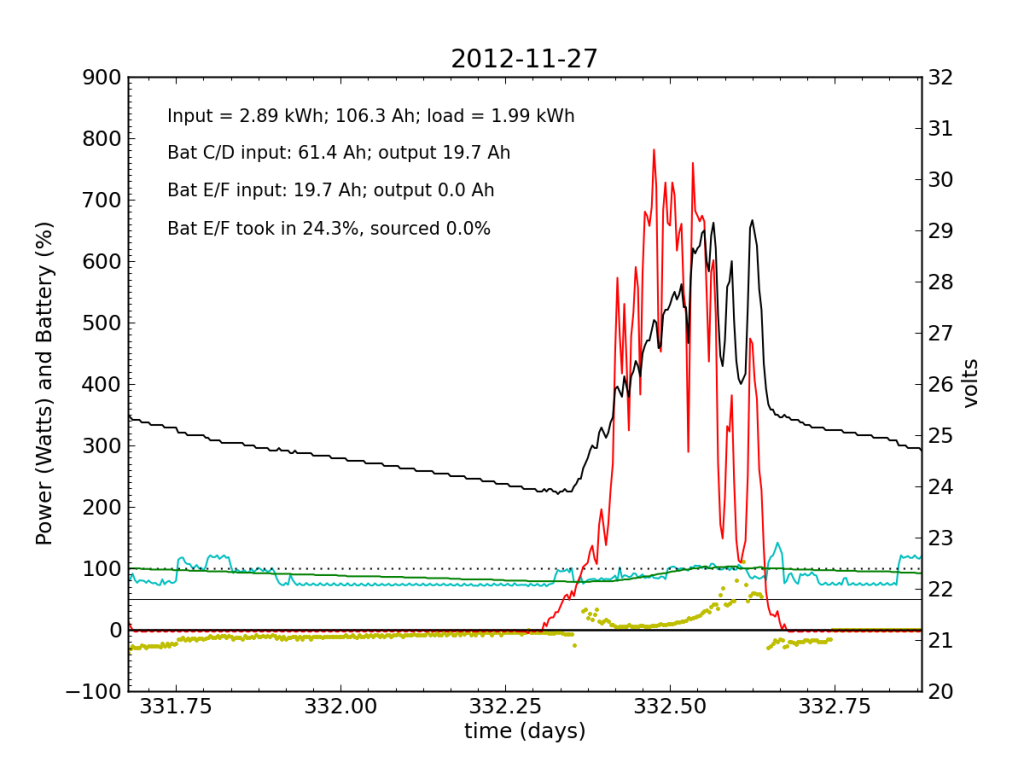
I worked from home the on the 27th and made occasional checks of battery voltages, to learn what I could about the dynamic charge state. At 07:45, I measured (11.91, 12.00, 10.79, 13.12) for the four batteries. At 11:40 (during a cloud passage, unfortunately), I measured (13.31, 13.37, 12.12, 14.71). Okay, so Battery F is roughly at an absorb voltage, still shy of the 15.5 V equalization voltage. So I’m not absolutely toasting it.
Tired of having the dead battery act as an energy drain on the system, I finally pulled the plug on Battery E/F, disconnecting it from C/D around 18:00. Just before disconnecting, E and F measured 11.29 and 13.81 V, propped up by batteries C and D (drawing power out of the good batteries). After disconnecting, they relaxed to 11.15 and 13.5, slowly creeping down. As of this writing, on 2012-12-09, the batteries have settled to 10.49 and 12.63 V.
Testing the cells with a hydrometer, it is not hard to identify the weak cell, which has an off-scale-low specific density (below 1.10). For a sense of the numbers/variation, the table below lists measured values.
The Edge of the Cliff
If I plot the fraction of juice accepted (blue) and sourced (red) from Battery E/F during 2012, We see the dramatic endgame.
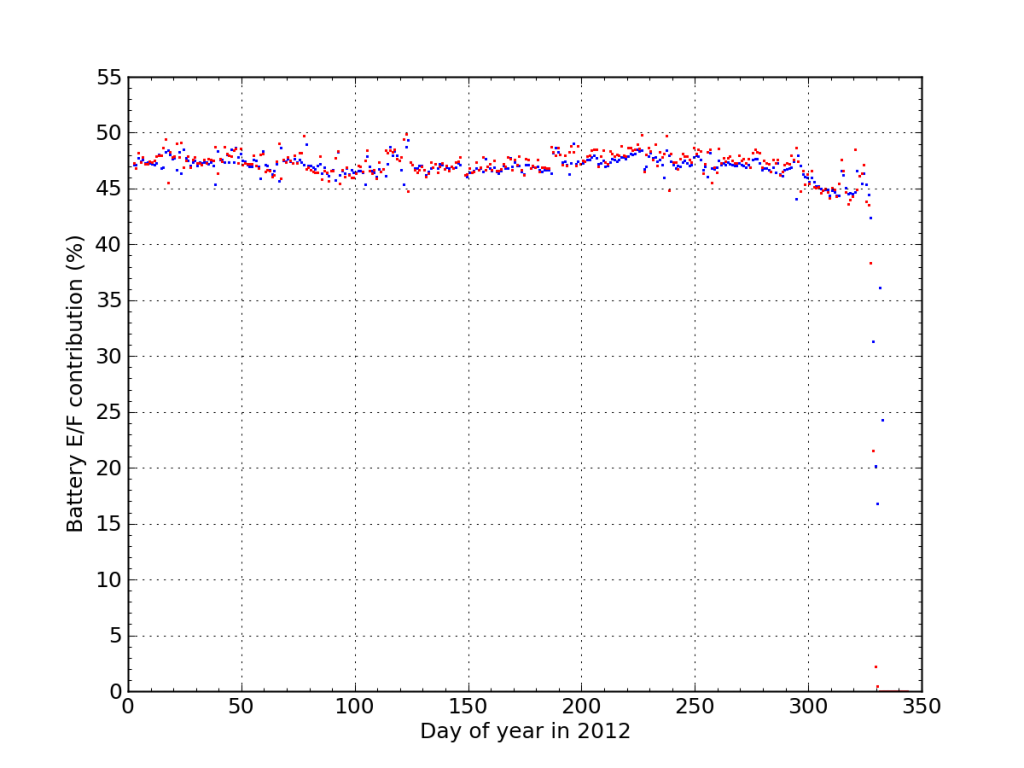
I think this plot nicely illustrates the degree to which the battery failure caught me off guard. Aside from the “while you were away” twist, the failure was really fast. There were no instances outside the 45–50% window the whole year, and then bam.
Now the Conundrum
Okay, so I have a bad cell in a battery. Maybe the situation is salvageable. Perhaps a “battery doctor” could bring the battery back to an operable state. I’ve seen prescriptions online for how to recover some functionality from a bad cell. You can’t expect original performance, I gather. But perhaps it is possible to turn an otherwise heavy block of junk into a useful battery again.
Let me say up front that I am not a battery expert. I may be carrying misconceptions that need to be cleared up. Please correct me if I have things messed up. It’s a safe bet that when I get through this failure episode, I’ll know more than I do now.
Whether or not battery repair is possible/effective, I judge it to be a near certainty that the revived battery would be poorly matched to its brethren. We have, in my 2×2 arrangement, a series problem and a parallel problem. In series, when one battery is in worse condition than its partner, it will sit at a lower voltage in both charging and discharging scenarios. It would seem, then, that the partner in better health gets a higher absorb state (or equalization) voltage, which has the effect of keeping that battery in relatively better condition than its lesser companion. So there is a self-reinforcement going on that I imagine will ultimately go unstable, producing another cliff-edge. Perhaps this is also why single cells in a battery (stacked in series) drive off the cliff.
The parallel problem is that if one chain is weaker than the other chain, a similar phenomenon happens. The “good” chain gets higher current during charging, better conditioning that chain while in absorb state. And then we have the power swap issue after sunset, where the weaker battery drains energy from the better battery until the two are at a similar charge state.
I am not, therefore, convinced that I want to try and revive the defective battery, almost certainly leaving me with a mismatched condition. So what’s the conundrum? Just buy a new battery!
Firstly, a new battery paired with old Battery F would produce a series mismatch problem, and also a parallel mismatch problem—assuming C, D, and F are in similar shape. To avoid the series problem, I could buy two new batteries, but this seems an unfortunate waste of battery F. For all I know, Battery E is an anomaly and I can expect another several years out of the other batteries. [It's this sort of thinking that often gets me labeled as an optimist, despite impressions you might have otherwise formed from the content of Do the Math.]
Secondly, even biting the bullet and buying two new batteries will leave me with a parallel mismatch and attendant problems.
So it seems like a really bum deal! Must I replace all batteries at once?
I suspect that I am missing something here, and that a new battery in an otherwise old set may work itself out in some non-destructive way. I am still adapting to my reduced-capacity PV reality, and meanwhile needed a bloggable topic that I could cover quickly, even if the saga is incomplete. I still need to do some research, and perhaps comments will help set things straight.
Perspective
I have written before about the disappointment inherent in batteries. Now I have another personal example. Just when I had decided that my batteries were in their prime, crash. In our forced migration from fossil fuels over the coming century, large scale implementations of solar and/or wind are likely to transpire only in connection to energy storage solutions. With storage comes headaches, even for technologies as mature as lead-acid. Batteries will fail, and seldom at convenient times. I liken my recent experience to driving a car without a gas gauge. How tolerable will this situation be to our demanding society? Big adjustments ahead…
He posted this one on his site a quite while back. When the battery went, it went but...I still think having it sit on the concrete led to a stratification of the electrolyte and inhibited equalization. He'd need to cut the casing off and dissect it to be sure though. The battery in his truck, which he mentioned as one of his other disappointments at one point, is easily explained by the small draw from always-connected accessories when the truck is "off" for extended periods of time. My own car will deplete a battery in two weeks if I don't remove the cable from the terminal (stays viable for months if cable removed). Batteries are tricky little buggers though.
Batteries sitting on concrete have been claimed to be problematic, though I can't explain why from a physics or chemistry perspective, unless it exacerbates stratification and hence sulfation.
Charging to only the 50%+\- charge level is serious undercharging;
http://www.trojanbattery.com/BatteryMaintenance/Charging.aspx
"10. Prevent undercharging the batteries. Undercharging causes stratification."
Batteries sitting on concrete have been claimed to be problematic, though I can't explain why from a physics or chemistry perspective,
Back years ago a common battery was the Nickel-Iron battery. These Edison Batteries came in a metal case, and that metal case resting on a concrete floor DID cause problems.
http://opensourceecology.org/wiki/Category:Nickel-Iron_Battery_Prototypes in case you decide you'd like to attempt to make your own.
I'm rather surprised no one else has commented on the continual undercharging as a possible major contributor to the battery failure. A once a month equalization IMO can't make up for the effect to a battery from continual undercharging. From the same Trojan website;
http://www.trojanbattery.com/tech-support/faq/maintenance.aspx
"Undercharging: Generally caused by not allowing the charger to restore the battery to full state of charge after use. Continually operating the battery in a partial state of charge, or storing the battery in a discharged state results in the formation of lead sulfate compounds on the plates. This condition is known as sulfation. Both of these conditions reduce the battery's performance and may cause premature battery failure. Undercharging will also cause stratification."
http://www.theoildrum.com/node/9873#comment-952732 (3 days ago)
" I now realise that my previous battery sets suffered an early death, mainly due to being in a perpetual state of undercharge."
To me the real question is what caused cel 4 in Battery E to fail catastrophically, in what, by all measures, should have been an otherwise perfectly happy and stable system, with a long life ahead of it.
In my mind this warrants a full autopsy by the original manufacturer. At the very least I would present the data you have shown in this post to them. If they are a reputable business. they should replace the battery a no cost to you even if it is no longer officially under warranty. And in my mind if I were them I would want to know exactly what happened and would pay to have the defective battery shipped back to their premises for analysis.
My personal experience with batteries of this nature leads me to believe that this was probably an unfortunate fluke due to an unforseen defect either in the materials or the actual manufacturing process. The anaology I would use is a young athelete in his or her prime suffering a heart attack on the playing field. As tragic as that might be I would not conclude that it was unsafe for most other young athletes to engage in strenous sports!
Cheers! Best hopes for longed lived battery banks.
From the photo above,It looks as if your wires are on the small side.The wires should be atleast as large as the battery wires on an auto or golf cart,also the coiled wire behind the batteries acts as a transformer,While i am thinking of it, i would advise you to put some closed cell foam between the batteries and Ground,build a rack or something as placing them on the ground shortens their life.good luck
I don't see a gas alarm either, highly recommended for static lead-acid battery installs. Bunding the batteries to contain acid spills is a statutory requirement for commercial setups, again something missing from this picture.
I echo the "thicker wires" comment -- the connection joining the 12V batteries should be a lot shorter and a lot thicker, for one thing. I'd also like to see a lot of "Hail Mary" in-line fuses in the wiring to prevent fires if shorts happen. I'd hope there's some kind of exterior-vented cover over the batteries that's been removed for the purposes of this picture but I've been disappointed in that area before in other circumstances.
On another matter, I take from the article that the batteries are wired in series-parallel, i.e. two sets of twin 12V batteries in series and their resulting 24V output paralleled up to provide a single higher current feed to the inverter? I didn't think that was a good idea for lead-acid batteries -- if one battery cell starts to fail short it can cause the other parallel battery chain to discharge through it, wasting energy and potentially damaging the other good batteries.
No, it doesn't. Beauty of DC current. You need AC for transformer [to work]. The only moment when this coiled wire acts as kind of transformer is when the current is switched on/off = change and just for the very short time. And of course it lacks common core that would induce pulse in a "secondary winding", so I wouldn't worry about this at all. ;)
My wires are small, but sized according to my system's actual need. I never see more than about 35 Amps through these wires: it's a small system, with small ambitions. If I scaled up, bigger wires would accompany the change.
The 4 Trojan T-1275 batteries cost about $200 each. If the storage system only lasts 1686 kWh then the battery-only capital cost is 47 cents/kWh.
Here's how the US Navy managed the 126-cell batteries installed in submarines, during the time of my service in the Submarine Force 1981-2000. A key attribute was individual cells, with accessible interconnecting busswork. This allows jumpering out any failed cell.
Another key attribute was the ability of the DC electrical system to operate over a wide range of voltages.
It was typical for one to three cells of a 126-cell battery to fail in the manner described by Tom Murphy over the 66-month nominal life of the battery. The failed cells were jumpered out and physically left in place while the remainder of the cells served out their normal life. This meant that capacity of the battery was only reduced at most about 2.4% by failed cells over the life of the battery.
I see that Trojan does sell individual cells. So my recommendation is to build a nominal 24 volt battery using seven cells. This allows a higher probability that you'll get to nominal end of life with enough cells for a functioning battery. Failure of one cell would lead to a 15% reduction on energy capacity.
One would hope that inverter manufacturers have allowed for a wide enough range of input voltages, and adjustability of setpoints for changeover to utility power, to allow the approach to battery design that I've described above. If not, perhaps this is a business opportunity!
Been there, done that: "1MC: The smoking lamp is out during battery charging. I repeat, the smoking lamp is out while charging batteries!"
Our current battery cells were made by Hawker in Chattanooga, same as the batteries on the LA class sub I was on.
As for inverter voltage ranges, our Outback inverter can operate from (IIRC) 19 volts to 34 volts. I have our LBCO (low battery cut off) programed to 20.5 volts (never have gotten there). If we had grid power, all inverters can be set to start charging at specified voltages. In our case, the Outback inverter will auto start the generator if voltage approaches LBCO. Off grid inverters have had these features for many years. Remember: Amp draw goes up as voltage falls. Size wiring and breakers/fuses accordingly. I oversize wy wires by at least one wire size. Improves efficiency a bit an allows for expansion.
As has been noted previously.. Leaving Bats sitting concrete is not good.
2nd observation.. Packing those batteries in a dense configuration is also not good. (That deficiency helped ground Boeing's 787). They need air gaps and forced air cooling when charging at high rates. The Idea to maintain thermal consistency between each cell.
Remember while charging 25 to 35% of the energy you put in will end up as waste heat.. If you don't promptly remove that waste heat(from interior cells), it will significantly degrade the battery performance.
While our batteries have a piece of 1/4 inch perforated plastic between them and the slab, I've read that, for lead-acid batteries, placing them directly on concrete isn't a problem for the batteries, though an acid spill may be a problem for the concrete. IIRC, this was an issue when batteries were encased in metal cases, and for nickle-iron batteries. I'll see what I can dig up.
As for packing batteries too tightly together, and heat, it shouldn't be an issue with smaller battery sets. Forklift battery cells are packed tightly in a metal box, and are generally recharged at a high rate. Boeing's batteries are a completely different animal; many small Li cells packed together. Also, as I mention below, good charge controllers have temp sensors to detect overheating. Having said this, I put 1/4 inch plastic spacers between my cells, just in case. I also have a floor drain under the battery set so I can rinse them down during their annual cleaning.
It looks like the most probable cause for problem with one of the batteries (cell) is most likely a partial short from debris falling to the bottom of the cell. Pull that battery and check it independently for a high self-discharge rate. Talk to Trojan as indicated earlier. Replacing just one of the batteries with a new one however will likely cause you various problems because of the now "mis-matched" battery bank.
The point raised about the wire gauge used for the battery interconnects is a very valid one, as (unless you are feeding a small inverter), the DC input current to say a 3 KW inverter can be 175-200 amps at max inverter load. Personally, I have a 3 KW Prosine/Xantrex fed by a series/parallel bank of 4 210 AH Concorde AGMs. The "interconnect cables are 2-0 gauge "welding cable" (Look at "standard" battery interconnects listed on many a Solar supply store.
Thirdly, the point raised about battery venting is quite valid when it comes to standard "flooded" non-AGM batteries, they can release a goodly amount of hydrogen gas when in the gassing phase of charging. A outside vented enclosure is a very good safety measure for those type batteries. You might consider AGM (Absorbed Glass Matt) batteries (for the system at the start of the thread) because they tend to recombine the hydrogen and oxygen inside the battery cells rather then vent it to atmosphere, and do not require the addition of water over normal use and lifetime.
Fourthly and lastly, I can dispel the long held assumption that "you should never place batteries on concrete" (unless the concrete is very cold and could keep the batteries from operating somewhere around normal room temp. where they work best). The story was true about batteries going bad and discharging when placed in concrete...true at least in the early part of the 1900's when battery casings were made of essentially an asphalt impregnated fiberboard material. This type of casing would actually "weep" a bit of electrolyte thru the case and onto the concrete and create a partial conductive discharge path with would discharge the battery. After battery cases began to be made of bakelite and up to todays plastics. They no longer had that problem, but somehow many people still think its true.
looking at the photo - and noticed the different cell caps.
Looks like the two strings were (slightly) mis-matched already.
Even if one has the same model number (as here if I read the numbers right),
different lots are going to be different.
OH! - went to trojanbattery.com
These are apparently somehow mis-matched:
The 6 individual caps are T-1275 Plus, the two diagonal caps are plain T-1275.
Hmmm - same high level specs though, and I can't find any more detailed info - would be interesting to know what the difference is.
Were the strings put into service at the same time?
Was non-distilled water added at any time?
A lot to be said for large amp-hour capacity single cells in one string,
so if/when a cell does an infant mortality/mid-life total/sudden death,
one can toss just that 2 volts and not worry so much.
(or pay big bucks for the batteries that allow you can re-connect individual cells).
Even pretty good batteries aren't uniformly perfect,
and sometimes one just gets "lucky" and a cell shorts.
I do note that Trojan docs say to allow some space for expansion and cooling in hot environments.
Up top Tom wrote:
So the batteries in each string were matched (as well as possible) but the strings were slightly different. If the set was being fully charged and occasionally equalized, it shouldn't cause premature failure of one battery cell. One cell may have been defective or damaged. I watched a guy at (big superstore) throwing automotive batteries onto a rack pretty roughly one day, hard enough to dislodge a plate. Who knows?
Even though I got the batteries at roughly the same time from the same vendor, they switched from 1275 to 1275-plus and I did not have the option to get the old 1275's. I was assured that nothing internally had changed: same plates, same geometry. The differences were purely external (fill caps).
Never anything but distilled water.
Some things:
Too many cells; makes maintenance a pain, one bad cell is harder to identify, and one bad cell brings down the whole string. Your 1.8 KwH battery set has twice as many cells as my 52 KwH set. Our last set of twenty 6 volt Rolls S-460s had 60 cells to maintain - ouch (5 strings of 4 batteries. They failed after @ eight years due to a few cells having low water (exposed plates) while we were out of town. I sold the remaining good batteries to a friend who is still using them 13 years after they were originally put in service (now two 48 volt strings). We now have one string of 12 two volt cells, 2200 amp/hours each. Only twelve cells to maintain and equalize. Each cell weighs about 100 kilograms.
No mention of specific gravity: Get a good electrolyte tester and check each cell after a full charge. Cells that show signs of not performing like the others can be relocated in the string; sometimes that helps. Also, the one battery that has a bad cell can be removed from the set and charged separately (try to find a 6 volt charger that has a 'restore' function, basicaslly a desulfator). Charge the crap out of it in a safe place. Probably won't work, but I've seen it help get a couple of years more from a failing cell. Also, dumping the electroyte and flushing the cells with water may remove scale from the cell bottoms. Scale can short plates.
Wire size and length: Keep'em short and big. My cell-to-cell conections are copper pipe forged flat and bolted to standard automotive battery terminals:
My main cables to my load center (inverter and charge controller breakers) are 4/0 welding cable with lugs made from copper pipe, forged and soldered:
A smaller setup wouldn't need this heavy cable, but I always recommend oversizing lower voltage DC wiring. I also use de-ox on all connections. I thank the solar gods that I did all of this right when copper wasn't so expensive. I also learned the hard way. Heavy, flexible battery cable is now available that is listed and meets code; wasn't available when I got started.
Battery watering: When I put this battery set into service, I ordered an automatic battery watering system. It has special valve caps that replace the originals. It allows water to gravity flow into all cells from a tank; keeps all cells full and at exactly the same level. One advantage of manually filling cells is that a problem cell will generally use more water than the other cells, but I now check specific gravity once or twice a year.
Temperature compensation: Good charge controllers have a battery temp sensor to better control the charging cycle. My Outback setup has one temp sensor shared by all Outback components via a "Hub". Didn't have to buy a sensor for each component. My Trace inverter/chargers each have their own sensor. Another good practice is to feel each cell during a good charge. Failing cells often get hotter than the other cells.
Voltage: Homepower did an article on charge rates and voltages citing some Sandia Lab studies (which I haven't been able to access). It said that folks who have good success with battery longevity run their battery sets "hot", bringing them up to 30 volts or more (for a 24V set) frequently. This really stirs the electrolyte, reduces sulfation, and keeps the cells equalized. This, of course, requires good ventilation and carefull battery watering. Since I installed auto-watering, I set my charge controllers to 30 volts. On a good day, I can hear the cells 'boiling'. With my 27 inch tall cells; it's quite noticable.
Cycling: I derate my cycle round trip by 20%. For every 100 amps measured out of the battery, I assume 120 needs to go in. Battery monitors like the Bogart Tri-Metric allow these parameters to be programed, and their newer 'PentaMetric' has a PC interface that logs data from multiple inputs (PV, more than one battery, etc.) It's on my shopping list. Good data is priceless. Without knowing how many amp/hours are going in and out of the battery set, you're flying blind. Most good monitors use a shunt on the negative side.
Alternative charging source: It's a good idea to have another charging source besides PV. It allows one to equalize the battery when PV may not be up to the task. In our case, we have a small diesel generator hooked to our inverter/chargers. Folks with a grid connection can connect the inverter/charger to the grid, or get a separate charger. It's not just the number of cycles, it's the frequency and how long a battery remains in a discharged state. I'm sure many battery failures are due to folks never getting their batteries really fully charged, and leaving them in a state of partial discharge for too long, cumulatively. If your batteries only get to a full charge (I mean really full) a few times a month, they'll fail earlier. This is why I charge mine at a higher voltage, and if they are in a discharged state for more than a couple of days I'll do a hard charge with the generator. Remeber, it's hard to overcharge a healthy lead-acid battery as long as it has plaenty of water. That said, always monitor the batteries when doing a hard equalizing charge.
All of this may sound like too much work, but I think I only spend an average of an hour a week tending batteries. I average much more time in the garden (or on TOD ;-) Most of my 'battery time' is spent checking the meters and glancing at the battery set to make sure all is well. It's a routine chore like feeding the dogs. Most of my metrics are viewable on an old laptop where I'm sitting now, the primary battery meters (two Tri-Metrics) are mounted in the kitchen in plain sight, one showing voltage, the other showing amps in/out of the battery.
Here's a more recent article from Homepower: Battery Installation and Maintenance
What are those red and green rings supposed to do? I have seen them in the local Autozone but no explanation of what they do.
NAOM
Those Red and Green rings have two purposes. They give you a visual indication of which post is positive, and negative, and they contain materials to prevent corrosion around the battery posts.
Yeah, they're just colored felt with an anti-corrosive in it. I got several packs and the terminals when a local autoparts went bust. All available at Walmart. They help keep the terminals clean. I also use a spray, the red stuff on the posts, to prevent corrosion. A little goes a long way.
Thanks guys, I'm going to look into it when I next go over to WallyMart, Autozone is in the same centro.
NAOM
Perhaps I should have said these things were available at Walmart. Last time I was at our area superstore, things were pretty picked over. Who knows these days. Anyway, when it comes to our batteries, I try to give them any advantage I can like big wires and protecting connections from corrosion; ounce of prevention and all that.
I built a new battery vent fan last night using PVC fittings and a brushless DC fan salvaged from a PC power supply. I the 'store bought' vent I bought years ago was built pretty much the same way. It died the other day, and they want $80 for a new one. I plan to put in a second vent as well since our new PV has the batteries gassing quite a bit. I'll post picture links if anyone is interested.
Yes, please post pictures of your batteries.
I have the picture of your electronics bookmarked.
You can see our batteries in my post below:
http://www.theoildrum.com/node/9873#comment-953421
"I also use a spray, the red stuff on the posts, to prevent corrosion. A little goes a long way."
That's all fanciful-like...I slather my car terminals in petroleum jelly - a little sticky but does the trick :)
Yeah, Sub, I've used Vaseline for years, but this stuff has an acid neutralizer in it. Nothing's too good for my batteries ;-/
Actually, I think Vaseline costs more. A can was about $3.
Those connectors look nice. One small point: Pipe grade copper versus wire grade copper. Of course you have some bulk that should overcome the impurities in the pipe grade copper. Wire grade would be electric galvanic plated out of solution or some process like that.
John in SF
Pipe grade copper versus wire grade copper.
Ok - what are the ACTUAL numbers here? Is this like the difference between .999 fine and .9999 fine Silver?
You've made a claim there is a difference - so can you show assays showing the difference?
He's raising a point of detail, and disclaims it pretty fairly as such. He's not making a hard claim about it.
Can't you ask for more clarity as if you're interested in learning and discussing it, and not just challenging people for proofs and validating evidence?
Because based on what I understand there is no real difference in the purity of modern Copper wire or Copper pipe.
In the case of electrical conductivity I'd stake out that the difference would be even less than a 99.999 fine Copper wire and a 98% copper pipe...if there as a 1.999 difference. (a difference in Copper scrap wire and Copper scrap pipe, that I'd believe.)
But here is someone claiming there is a difference and I'd like to see the data they've based it on.
Can't you ask for more clarity as if you're interested in learning
But you see I am. Old Copper scrap has Silver in it and as I understand modern scrap-> new ingot production results in 99.9+ fine Copper. I have an interest in the reclamation and use of 9.9+ pure Copper for some castings I wish to do. To separate the Copper from the "tinned" bits means I'll have to use an electrochemical process but its far simpler to use Copper wire and Copper pipe if I can get it.
So yea, it matters to my personal education.
I use Type M (thicker wall) copper pipe. It's 99.9% pure copper according to THE COPPER TUBE HANDBOOK. I've never felt one to get warm, even when pulling a couple of hundred amps at 24 volts.
I also make my large wire connectors from it. Remove about 2-3 inches of insulation from the wire; cut a piece of copper pipe the same length as you removed; put the bare wire in the tube (I wire brush the inside); beat it flat on a vice or anvil; heat with torch and solder from both ends (will suck up a lot of solder). When it cools, wire brush everything nice and shiney. Drill your hole; cover contact area with tape and dip in Plasti-Coat, or use electrical tape or shrink tube. I dipped mine in Plasti-Coat 'til about an inch of the insulation was covered. When dry, score with razor knife and peel off tape. I grind the end a little to make it look nice.
Great input from all. My personal knowledge is limited and thus I put the comment out there seeking to learn. When I was doing metal recycling I found that they would pay me more for electrical wire (especially if stripped) than copper pipe. They argued "purity" and when I researched the process on line for making electric wire I was impressed by the lengths some wire manufacturers go to.
The proof is in the pudding and as Ghung put it so well: his system doesn't overheat. Good tips. Thanks!
John in SF
When I was doing metal recycling I found that they would pay me more for electrical wire (especially if stripped) than copper pipe.
A couple of reasons here:
1) The Lead (then later not-Lead) solder joints.
2) The Calcium and other build-ups in the pipe.
Beyond the desire to turn Copper into much higher value castings + "art" there was a time when I was on a sucker-mailing list. The phishers-for-suckers thought I'd bite on "semi-precious" "investment grade" gems.
So I researched "semi-precious" metals. Turns out at that time the "law" was one could not own more than 200 lbs of Copper. And thus the people calling for me to invest got my pitch for "investment grade" Copper. (and due to JP Morgan the law was reversed in 2012. A further aside - how much Copper is in American homes with Copper pipe and 200 amp service - more than 200 lbs....)
And Copper is often recycled so that Copper atoms mined from the US Civil War timeframe odds are exist in the Copper pipe you buy today. (Source - Copper mine tour)
I put the comment out there seeking to learn.
And the learning aspect is why I challenged you to produce the assay info - because my understanding was your claim was incorrect and here on TOD we try to have facts rule.
Observation and drawing a conclusion != a provable fact with an assay.
I have heard that batteries on concrete is a good thing, helps keep them cool.
The old myth about concrete discharging batteries persists.
I think the myth derives from having the batteries in direct contact with solid concrete and unable to dissipate heat from charging and discharging through their base. They really need good temperature control, neither freezing in winter or cooking in summer if you want them to last a long time. This usually costs in terms of electricity and infrastructure though. In the case of the remote-site battery packs for radio repeater stations I was installing decades ago it was regarded as cheaper to simply replace them every three or four years on a site visit rather than burn power to keep the batteries warm during a Scottish mountaintop winter.
Just a guess, but I suspect it comes from people pulling batteries out of cars and letting them sit without wiping off the road dirt (salt and other conductive corrosion products). Then they check the battery six months later and they can't understand why it is dead so they blame the concrete.
It is my understanding that placing batteries on concrete causes a thermal gradient across the cell.
This causes internal wear on the cell as the portions of the cell which are at one temperature discharge in order to charge other portions of the same cell at another temperature. The wear occurs as thermal cycling takes place.
It is my understanding that placing a block of styrofoam under stored cells helps a lot in insuring an isothermal cell environment.
I tied as you suggested, bypassing a bad cell. It was a 12v marine battery just out of it's warranty.
Located the top intercell connectors, drilled a pilot hole in them, then put in 2 stainless deck screws. Then used a screw down cable clamp to connect them together.
In my 36V golf cart the loss of 1 cell didn't affect performance noticeably. Had to use a power supply adjusted to 11.5V to charge. Lasted about 1 year, with one failure when a screw came loose. Also drilled a hole in the case and drained out the electrolyte. Junked the battery when a second cell failed.
All in all it probably wasn't worth the time and effort.
The cells should be as evenly matched as possible, even using cells from the same manufacturing batch. Although the internal construction is said to be the same, there is the possibility that the two types are not exactly the same. Therefore it would have been better to put one 1275 and one 1275+ in each series string.
Cell Balancing
Diodes can be used to prevent the good string from discharging through the bad string with a low voltage cell.
You can parallel storage batteries
Yes, it can be done with diodes. but you have a loss of about .5V across the diode.
If your inverter is pulling 100 amps, then 50 watts is being wasted by the diodes. Some PV systems cannot afford the waste.
It would be wasting a few percent.
If that is a 100 amp feed, then according to AT&T -- DETAIL ENGINEERING REQUIREMENTS - SECTION 12 -- POWER SYSTEMS you need No 2 Gauge wiring.
No. 6 -- 75 amps
No. 4 -- 95
No. 2 -- 130
No. 0 -- 170
Whatever the loss through the diodes, over time it will be less than the loss in one battery trying in vain to charge the other.
The diode loss occurs continuously, even when the batteries are in good condition and not trying to reverse-charge each other.
Problem is that the two diodes, assuming you're using silicon devices, will have a forward bias of about 0.6V under load so you'll lose 0.6V x I of power into the batteries and the same on the way back out. Assuming I = 20A under load (for a 24V string that's about 500W) then that's 12W lost during charge and another 12W during discharge, or about 5% total loss for the charge/discharge loop. Germanium diodes have a lower forward bias voltage but Ge devices with decent current ratings are very expensive.
If I was building an off-grid/grid-coupled system for myself I'd probably use a single string of lead-acid batteries to provide 120V DC and look at rewiring the house to install extra "battery" sockets fed from that string via a conditioning and regulating controller. A lot of modern devices with switch-mode power supplies like computers, TVs etc. will run quite happily on DC at that voltage without conversion losses. Other devices like microwave ovens etc. require AC and they'd be plugged into the originally-fitted house sockets fed by a suitable DC-to-AC inverter/grid switch setup.
"If I was building an off-grid/grid-coupled system for myself I'd probably use a single string of lead-acid batteries to provide 120V DC and look at rewiring the house to install extra "battery" sockets fed from that string via a conditioning and regulating controller."
I'm not sure what you would gain by doing that. 120 volts = 60 cells to maintain or fail (BTDT,, it's a bitch), and DC voltages over 48 - 60 volts are problematic (arcing, etc.) and I'm not sure if any building codes will allow it. Breakers, relays, switches, etc. for high voltage DC are also quite expensive, and I haven't seen any battery-based inverters that run at 120 volts, DC side (there's a reason for that). Besides, this is very mature tech; lots of previous experience to call on.
Wire the house for standard, code-compliant AC, add a hybrid inverter (they have built-in transfer switches, chargers, all that), and run some lower voltage DC where it's useful. I have several 24 volt circuits doing various things, including running this computer. It's like having standard grid power with a backup generator. Many of these inverters are also >95% efficient. Put the extra expense into up-sizing your system; more PV and battery. My main consideration was that if the house ever gets sold (or I pass before my wife does) our house can be connected to the grid with few issues; remove the RE stuff and make the grid connection to the standard (code-compliant and inspected) 120/120 AC system.
Wiring and losses are the main reason to go to a higher battery voltage. For example a 700W microwave oven pulls about 6A out of a 120V battery or over 30A out of a 24V battery supply. The higher current means thicker cables, heavier switchgear and greater losses in the wiring plus a greater strain on the battery cells and a beefier inverter. Most electric cars run a 400V+ DC battery pack for this reason although they can still pull well over 100A on occasion. If they were limited to 48V the instantaneous currents would be ten times higher.
My choice for a house backup/offgrid implementation would be to use purpose-built 2V cells for this 120V DC system as you have for your high-capacity 48V bank. Defective cells could be disabled and bypassed as necessary but each cell lost would only drop the capacity of the stack by less than 2% so it would be possible to delay replacement until a few cells had died and then swap the defective units all at once. In your 48V system a dead cell loses you over 4% of your overall capacity.
I'd provide the 120V DC supply I postulated with separate cabling, not connect it to some of the existing AC code wiring. I'd install it to meet the AC code to the point where it could be connected as AC-compliant if needed at the fusebox. Most AC breakers and switches I've seen derate for DC, but not by much -- 15A AC switchgear will derate to 10A DC, for example. Zero-crossing switches won't work of course. As for arcing etc. AC is as prone to that as DC, same with things like insulation requirements.
A big saving is in inverter loads -- no need to waste energy upconverting to 120V AC to feed a device with a switch-mode supply or a purely resistive load (like a lightbulb) which would work perfectly well on straight-off-the-battery DC.
Schottky diodes are better for this, far lower junction drop and are available in high current versions. Dual packs are available that can make for easier in/out connections. Old computer ATX power supplies can be a source for playing with.
NAOM
Thanks, I just ordered some off e-bay to play with.
If two strings are mismatched, an equalizer like this can be used. I use one to center-tap my string for smaller 12 volt loads. Kind of pricey, but keeps two halves of a 24 volt battery set balanced. I also have one of their desulfators; zaps the plates with high frequency while charging.
http://www.solarconverters.com/index.php/products/82-battery-equalizer/1...
I was having a problem with my battery holding charge (I charge from mains to run some LED and inverter lights). I built a de-sulphating circuit and WOW, what a difference after running for a few days. I used a lot of ex-ATX parts to build it but I think I undersized the coil cores, the parts ran hot until one of the coils fried. They should not have heated up but the core was probably saturating. I'll have to make a Mark II with a larger core.
NAOM
I would love to see a copy of your schematic when you're done, as a reference. Please let us know if you're willing to 'open source' your circuit.
Thx,
Bob
This is the design I copied to build mine with tweaks for the components available:-
http://home.comcast.net/~ddenhardt201263/desulfator/lowpower.htm
Used parts salvaged from PSUs and re-wound the coils. As the coils are impregnated in varnish I soaked them in standard, caustic paint stripper until the varnish fell apart then they were quite easy to strip down and re-wind to the required inductance and checked by a meter. If it runs hot it is likely the cores are saturating.
NAOM
Thanks NAOM, appreciate it!
I believe HomePower had an article on de-sulfurnators and there was a yahoo group made to discuss it. Below is the welcome message.
Welcome to the desulfator group - dedicated to the development, advancement, and use of pulse lead-acid battery desulfation technology.
This mailing list was setup to provide a file-sharing area to bolster the main discussion that occurs at the main forums at:
http://pub36.ezboard.com/fleadacidbatterydesulfationfrm1
All discussion should take place there, as likely no one will see it here.
Thanks,
Ben
Moderator, Desulfator Forum
NOTES:
If you do not wish to belong to desulfator, you may unsubscribe by sending an email to
desulfator-unsubscribe@yahoogroups.com
To see and modify all of your groups, go to
http://groups.yahoo.com/mygroups
I think if you had put as much effort into researching how to design off-grid systems as you have into collecting data, then you might have had a less frustrating time!
I have great sympathy for your disappointment, but a few basic mistakes are obvious even glancing at the first page of the article. There's no real need for all the diagrams, any PV installer will look at that and say 'well what do you expect?'
Firstly, you are overly optimistic about your depth of discharge vs life. Your battery bank is probably just too small. (But everyone does that at first because doing it properly is expensive.)
Secondly, you have a series-parallel setup. Bad idea. Circular currents will flow through any sub-par cells, you have seen the results.
To be clear, I DONT believe that battery storage on any large scale offers a solution to our over population of the planet. Its all just a distraction that lets us think we can carry on BAU without facing up to the fact that there are TOO MANY people consuming TOO MUCH stuff. Batteries are not going to save the world - like it or not your grandchildren will have 10% our your annual energy budget, and that doesn't include battery manufacture.
But, as a scientist, I have to point out your personal experience does not invalidate battery technology. It is perfectly possible to put in an off-grid battery-backed system that works well with a battery lifespan of 15-20 years. It just isn't cheap, or for amateurs.
best wishes Ben
Maybe batteries are not a solution to get totally off grid. But they are the easiest way to dampen the effects of rolling brownies. I lived in the capital of the Dominican Republic, Santo Domingo, in 2003 to 2005 when, due to an economic crisis, rolling brownies were common almost every day. With a battery inverter one could go on with an almost normal life, using light, fan, TV and computer at home - with the exception of the washing machine and the fridge. Another solution was to have an own fuel driven generator - but that required some space in the garden/backyard or living in a modern condo - not to mention the horrible air pollution those generators produced.
The batteries of Aquion energy are designed to be very reliable and last very long (25 years). They are preparing for going into production this year. However, they have a lower energy density.
GE is producing its Durathon batteries. Last 10 to 15 years. Higher density than lead acid.
Batteries have future, but not in Lead Acid.
Lucas
This article was perfectly good until it got to the "Perspective" section.
This is a classic case of a "strawman" - no self respecting engineer would ever, ever suggest a huge battery for seasonal storage, as Tom has done before. Storage with high capital costs (hydro or batteries) make absolutely no sense for seasonal storage, which might be used once or twice per year. It's only sensible for diurnal storage, which is used daily and therefore can be amortized over many cycles. No sensible engineer would consider this.
Sensible planners, like the Germans, would:
1) use storage as a last resort, after maximizing interconnection and geographic averaging; overbuilding; Demand Side Management; supply diversity, etc. and
2) use very low capex storage, like "wind-gas". Casual observers will object that such conversions have low efficiency, but for a seasonal application, capex efficiency becomes far more important than conversion efficiency.
We should be far more careful not to exaggerate the problem. Our primary problem is political opposition from legacy industries to a conversion away from fossil fuels. Exaggerating the technical problems only helps them.
---------------------------------------------
A little more discussion:
Batteries and pumped storage would work well to match supply and demand for daily (diurnal) variation, but the sensible storage option for seasonal wind/solar lulls is "wind-gas".
People get hung up on the capex of batteries and pumped storage, but using those for seasonal storage is like driving a M1 tank to work - they only make sense for diurnal storage where the capex is amortized over thousands of cycles.
Overbuild wind/solar production by, say, 25% above the average demand, and use the excess to electrolize seawater and store the hydrogen underground. http://en.wikipedia.org/wiki/Underground_hydrogen_storage
That makes the storage incredibly cheap, and the conversion efficiency is relatively unimportant because you'll only need to draw about 5% of consumption from storage*. Higher efficiency is still valuable, but minimizing capex is much more important than maximizing efficiency.
Further, storage will always be the last resort - many other strategies are much cheaper, and will be exhausted first: supply diversity; long distance transmission; Demand Side Management;, etc, etc. Seasonal storage will only be needed in the distant future when fossil fuels are completely phased out, and in the unusual event that all renewables are low for an extended period in a large geographical area. This might be a 3 week period in January where all supply is 1/3 of demand, so that the equivalent of 2 weeks (4% of annual consumption) is needed.
I think Tom was just discouraged because his little battery died ;-/
By "wind gas" do you mean mixing hydrogen in to the natural gas supply of existing turbines? If so this expedient is merely a stop gap on the way to a fossil fuel free energy supply. Turbines which run purely on hydrogen will be much more expensive than natural gas turbines, and in fossil a fuel free society their capex will be further increased by a utilization rate of only 5%.
In the long run, I would expect the hydrogen to be stored underground, as noted above.
Why would turbines running on hydrogen be much more expensive? I would expect that a utilization rate of only 5% would greatly reduce any costs due to embrittlement.
Now, I agree that their utilization would be low, but that doesn't increase the capex: the capex is what it is, as dictated by the maximum backup capacity required. OTOH, it certainly argues for very low cost engines to minimize that capex. You probably would use relatively few 2 cycle turbines, and use cheaper single cycle turbines. Heck, ICEs can run on hydrogen, and can cost as little as $.10 per W of output - you'd want to use them for that last 10-20% of capacity that might get used only once every several years. They have low efficiency, but that doesn't matter much, because the total volume of energy flowing through them (maybe 1% of annual kWh output) is so low.
Biomass is stored solar energy, so, to replace storage by battery, I have been working on a biomass system connected to my PV driven house that will keep up a minimal battery used to feed the inverter. When solar is inadequate, idea is to have the biomass system kick in automatically to keep the battery up, thus avoiding the storage problem.
The stirling i chose for this job last winter worked ok, but its burner was a problem since the engine, an aerospace left-over, demanded a very hot heater head from radiation only.
Engine is similar to MEC 1kW, but is an opposed pair to eliminate vibration.
http://www.microgen-engine.com/index.php?option=com_content&view=article...
After a lot of struggle, I got the burner to gasify wood pellets and heat the engine pretty well, but by that time i had made the obvious conclusion that a helium charged linear alternator engine was a no-no for a commercial product, and I quit working on it in favor of a low temp burner and an air charged thermocompressor designed around existing catalog items. A work in progress.
I have heard that Nickel/Iron storage batteries have very long working lives. "Edison", cells
Yeah, I love everything about them except the price. Hopefully they'll come down a lot before I need to replace my current batteries. To replace my current set with NiFe Edison cells would be 4-5 times the price. Their self-discharge rate is a little higher than lead-acids, but not too bad for my purposes.
The cells won't drop in price because they reflect the raw material costs, and Nickel is expensive.
If one is hoping for low-cost magic in the far-away future ... solid state capacitors somehow actually come into existence like EEStor was pitching. Graphine capacitors is the latest hyped "solution".
For long term energy storage high proof Alcohol looks like a way to go. Ignoring the tax issues - it is able to be made from products in 1 years time, it is tradeable for non-energy use cases, to control a fire...add water, one can use it for cooking heat, etc. Another option could be things like the use of wood chips and gassification with things like the GEK http://www.gekgasifier.com/
Man, this post is getting eaten alive by spam.
Maybe time to approve or delay new user comments?
Golf cart batteries have a deep cycle service life of 2 - 7 years. Sounds like Tom confirmed this result.
http://www.windsun.com/Batteries/Battery_FAQ.htm
Maybe he should consider building a more reliable solar system (warranty 7 or 10 years) for his home (rather than cutting corners and bothering us with predictable narratives of misplaced ambition, cheapness, and gerrymandered results). Many companies know this business, and produce effective and reliable results.
I suppose that gives us an answer.
Tom seems fully capable of understanding how to frame a problem with respect to scientifically informed methodologies (rather than his own personal history and anecdotal experience). I recommend he do some reading and let us know what others have said about the issue … rather than cherry pick from his own experience (and suggest this somehow reflects a rule or norm).
"Many companies know this business, and produce effective and reliable results."
Where's the fun in that? I looked at the big Rolls and Trojan 2 volt cells when I replaced my Rolls L-16 6 volters. Found a locally manufactured commercial battery with more storage for less, very popular in industry for forklifts, etc.
I actually started where Tom did about 20 years ago; learned as much from my failures as my successes. As for cheap batteries, I mentored a friend through building a nice off-grid system, 1 Kw of PV, 2 Kw Outback inverter, Blue Sky MPPT controller, nice big wires. The only thing I worried about was the batteries; he got eight 6 volt golf cart batteries (105 AH) from Sam's Club. We wired them for 24 volts. That was 6 years ago (maybe 7). He's still happy with the system, but he called me recently asking if he should be worried about his batteries by now. I said probably, that I've never seen cheap ($85) batteries last this long. He doesn't cycle them much; just a few lights, a radio and an occasional power tool, maybe some wall warts. Checks the water, equalizes from a generator a couple of times a year.
While this guy's experience isn't typical, neither is Tom's. Those Trojans should have given him 5 good years, at least. I cycled the crap out of a bunch of Walmart Cycle 27DC marine batteries ($49 at the time) for over 4 years. They still held a pretty good charge when I replaced them with the Rolls.
My Sunica nickle cadmium cells are still usable after two decades of continuous use. They have a high self discharge rate and low energy density but they will tolerate freezing while being completely discharged. If I knew they were available I would have ordered NiFe batteries instead to avoid toxic cadmium.
Douglass
Yeah, lead-acid batteries don't have the best cycle lifetime. But the price is low such that for static applications they can be hard to beat.
A problem with full battery pack replacement is a possible mismatch with the owner's 'cash flow cycle'. People who go off grid in what we call a 'bush block' in Australia may have sold their suburban house or gotten some kind of cash pay out after being laid off. Initially few think that the PV panels, controller, battery pack and inverter each have a different working life. Years later on reduced income something needs fixing and the cash is not there.
In one case some off-grid people got a diesel generator to power the home at night. The engine noise must be annoying and seems to completely negate the aim of seeking peace and quiet. Traction battery replacement must soon become an issue for PHEV owners. I understand there is a proposal to refurbish 13 kwh lithium ion batteries (if I recall) from the Chevrolet Volt to act as home batteries. Maybe if they were cheap and could be swapped like LPG cyclinders the cash issue wouldn't be so great.
Judging from your posted specific gravities of your good cells, something is amiss with your system of equalization because they range from 1.230 g/cm3 to 1.290 g/cm3. From my last reading of the 24 cells of my 8 L-16 batteries (7 years old), they range from 1.225 g/cm3 to 1.240 g/cm3 with most of them at 1.235 g/cm2. This is with no deep cycling and no equalization. Your cell with a specific gravity of 1.290 g/cm3 is over charged. Maybe the unbalanced specific gravities are foreshadowing old batteries that are about to fail. The next time you buy batteries I suggest you get some with the contacts between cells exposed so you can equalize individual cells.
The maximum voltage on a 12 V nominal lead-acid battery is 14.4 V (28.8 V for your series pairs). You are killing your batteries by overcharging them every sunny day. Only equalize your batteries occasionally when the specific gravities of cells in series become unbalanced. Set your charge controller to limit the voltage at 28.2 V so that the better cells do not get overcharged and sulfated.
Your charts show that your typical load is less than 250 W with a load up to 525 W on Nov. 21, 2012, at night. Starting the compressor motor on your refrigerator probably consumes about 1,100 W for a few seconds. There is also a minimum load of about 100 W. Starting the refrigerator approximately every 30 minutes is drawing about 25 A briefly from each of your batteries. This is reducing their lifetime too. The solution is a bigger battery array to keep the current below 20 A per battery or to connect your refrigerator/freezer to a timer that allows it to turn on only during the day allowing your PV panels to help start the motor and reducing the number of starts. The timer would also reduce the amount of discharge improving their life expectancy.
On cloudy days your batteries are getting deep cycled. Your average daily cycle depth of 31% is not an accurate characterization of how you are cycling your batteries making your expected 2,000 cycles overly optimistic.
Your battery array is overcharged, undersized and deep cycled. You are learning the lesson that many others have learned before you: when you treat batteries roughly, they reward you with a short lifetime.
You have a few options for how to deal with your bad battery:
1. Keep going the way you are with 2 batteries. Every week exchange the third good battery with one in the active pair in sequence allowing them to get equal work time. This will make them age at the same rate. Being insufficient for your load, two batteries will degrade quickly as you discovered with your first battery array. This is cheap and will maximize the usefulness of your old batteries.
2. Purchase a new battery and put it in the battery array in place of the bad one. Connect it in parallel with the battery beside it allowing it to discharge into the older battery. Once a week swap it with the battery in its series string. You do these two things to equalize the batteries in the array. After a while, the specific gravities of the cells in the new battery will degrade to match the ones in the old batteries allowing you to stop swapping them.. Essentially the new battery will only last as long as the old batteries in your array.
3. Discard the bad battery and its series partner and purchase two new batteries to connect as a series pair. The new series pair will discharge into the old series pair degrading its life to match that of the old series pair.
4. Replace the entire battery array with new batteries.
5. Get a 12 VDC to 120 VAC inverter and bigger wires allowing you to connect all three batteries in parallel.
I have done 1, 2 and 4.
Very long time since I have commented but that picture is scary! As many have pointed out you really did mess up with using such grossly underrated wiring. As for that massive coil, yes, you have a DC system but hate to tell you, as the current and voltage change in the system(due to stuff turning on like a frig or initial charging currents) that coil most certainly does cause induction loss issues that are opposing the current flow. Only after the system steadies down do these effects vanish. Besides, all that extra wire is just creating resistant heating for what purpose - art? Get rid of that silly coil since it has zero usefulness and is eating up energy to no purpose - can't believe you have that rats nest in your battery circuit. But please, most of all, add safe wiring that is rated for that current - 120 volt wire for 10/15 amps service is a joke for batteries and causes needless extra resistance (discharge and charging.) So, first off, you MUST read about basic wiring for houses and batteries. Everything else after that is gravy.
My wiring may be underrated to the eye, but not once you consider the rest of the (small) system and overcurrent protection devices. I never see more than 35 Amps through the wires, and they are rated to handle it.
As for the coil, I relocated my PV system when I moved, and set up the panels in a temporary place at first (closer to the batteries, but in a sub-optimal roof location). I later moved the panels to a better spot and used up that coil. Even so, I never seriously worried about the trivial inductive loss during a surge. Small beans.
In any case, it is hard to get the whole story from a snapshot.
Assuming Tom used 10 gauge copper wire, the wires are not too small for the series and parallel connections between the batteries under normal operating conditions. However, the wire that conducts power from the battery array to the inverter should be 6 gauge copper to handle a potential 60 A from the battery array. Otherwise his wires are too small for safety because if there is a short circuit, 10 gauge copper wires are insufficient to transfer the current without overheating the insulation possibly causing a fire. He tolerates risk for the sake of reduced cost of wiring.
My wires are 6-gauge. I use 8 and 10 in other places in the circuit where current is lower. But all are sized with NEC safety factors and appropriate overcurrent protection.
As of NEC2008, In Dwellings, Listed Over Current Protection is required as "close as practical" to terminals sized to product conductors unless the conductor is sized to the short circuit current available from the Battery. Even a small Battery can source hundreds of amps. One Rule of Thumb is 1000A available fault current for each 100Ah Capacity. see 2011 NEC690.72. Any of the #8/10 conductor could vaporize during a fault. Marine standards (ABYC) is within 7 Inches of battery Terminal. If I recall correctly , you can run upto 5 feet of 4/0 to a Breaker from a Battery Room/Box. Make sure the Breaker/Fuse is Rated to interrupt the available short circuit current from the Bank.
Of Interest to many here will be the proposed update to the 2014 NEC on Safe Battery Wiring
http://www.solarabcs.org/codes-standards/NFPA/pdfs/2014NEC%20690.71(H).pdf
How big is that .pdf? 15 minutes later it's still not loaded.
Edit: Gave up after 25 minutes.
It's only two pages; loaded quickly for me. Funny, it's exactly how I did it 10 years ago, even though I ran my big wires in conduit. Common engineering sense told me to keep primary battery cables short and the main breakers should be within a few feet of the battery, but not actually inside the battery compartment.
On the right side of this photo is the main breaker panel (white box), and you can see the 1.5 inch conduits dropping down. The battery box is immediately below the photo. I ran 2 each pos/neg 4/0 circuits to two 250 amp breakers. I later ran a third circuit to a 175 amp breaker (in the gray box) for our Outback inverter.
The messy wires hanging down from top left are temped in, patching in our new panels to test array configurations to the charge controllers, soon to be in conduit as well.
Batteries, a while back when I removed the front compartment panel for cleaning/inspection.
I like the translucent cases because I can see the water level in the cells; full, in the photo, as expected.
http://www.solarabcs.org/codes-standards/NFPA/proposals.html Look for 690.71H
"The maximum voltage on a 12 V nominal lead-acid battery is 14.4 V (28.8 V for your series pairs). You are killing your batteries by overcharging them every sunny day. Only equalize your batteries occasionally when the specific gravities of cells in series become unbalanced. Set your charge controller to limit the voltage at 28.2 V so that the better cells do not get overcharged and sulfated."
Actually, I beg to differ with this one point. I mentioned a Sandia Labs study of L-16 batteries, above. While it seems the link to the study is no longer available (often mentioned in RE forums as the famous "lost study"), here's the Homepower article referencing the study:
http://www.homepower.com/view/?file=HP89_pg120_IPP
...so the finish voltage on a 24 volt system should be 30.6 volts. Your reaction may be the same as mine was; "wow, that's high". As the article mentions, longtime RE/offgrid folks discovered this a while back, the same folks who manage to get 15-20 years from a set of lead-acid batteries.
This why folks like Tom, who have the grid rather than a generator, should have a good charger (preferably a good inverter/charger) to get the battery set up to this high finish voltage and keep it there for several hours about once a week; batteries last much longer. Having recently 'over-built' my PV system, I am now able to do this a couple of times a week. Yesterday, my battery was at 30.2 volts around solar noon and I was load-dumping amps to the hot water tank shortly after, still maintaining this high voltage. It's a mini-equalization and stirs the electrolyte, possibly helping to 'scrub away' sulfation. It's also why I installed a battery watering system; quite inexpensive compared to prematurely failed batteries.
My manufacturer suggested about 30 volts for my twelve big 2 volt cells, for about 3 hours, at least once per week. Since I've started doing this, the main thing I've noticed is that our voltage when not undergoing a charge stays noticably higher throughout the cycle. After a good charge yesterday, our battery voltage this morning was at 24.6, even after running two TVs, lights, a load of laundry, background loads, and the dishwasher, for several hours last night, and under morning loads, our voltage never dropped below 24.3, even on this cloudy morning, even when my wife used her 1600 watt hair dryer. I now realise that my previous battery sets suffered an early death, mainly due to being in a perpetual state of undercharge.
My first battery array lasted 14 years using a relay switched regulator set to shut off at 14.5 V. With maximum charge current from the PV panels it would shut off between 14.0 V and 14.1 V due to the voltage drop across the wires between the regulator and batteries. During the evening when the charge current was less it would shut off closer to 14.5 V.
When referring to a 24 V battery, there are 12 cells in series some of which are better charged than others. Cells with lower charge will have a lower voltage and cells with a higher charge will have a higher voltage. Tom's posted specific gravities showed a wide range of charge states among the cells in his series string. To prevent over charging of the best cells one must reduce the voltage applied across the series string.
Having written that, Trojan's advice for charging flooded lead-acid batteries is in line with your and the article's comments:
I will set the cut-off voltage on my regulator a little higher and monitor what happens to the specific gravities.
My take from the Sandia study, which I was able to read back in the day before it was "lost", was that you can't "overcharge" a cell as long as there is water covering the plates, sort of like you can't "overboil" water (different process, I know). The cell will only accept it's maximum charge, then simply puts all of the current it receives into heating and electrolysing water. This allows the weaker or undercharged cells to catch up. This, of course, is what equalizing does. The electrolyte shouldn't get to a thermal boiling point because most of the energy is dissapated through electrolysis. Taking a charge to extremes can allow the plates to be partially exposed and melt down, (not unlike fuel rods). Party over.
The voltage level they arrived at was the optimum at which a happier medium was achieved. The mechanical action of the electrolyte bubbling also reduced sulfation and made sulfation more consistant across the surface of the plates at a much slower rate than the process of discharging undercharged cells. Over time, undercharged cells deteriorate at a much higher rate because they're always playing catchup. Better to get them up to at or near the charge level of the more robust cells, and do it often. This, of course, means more gassing and adding water more often = vent fans and automatic watering in my case.
Most days I have my dump load controller set at 29.5 which actually is cycling the voltage between 27 and 29.8. After a cloudy spell I'll switch the dump load breaker off, allowing the voltage to float around 30 for a couple of hours. These big cells really bubble a lot at that point. The experts said it's a good thing. Hope they're right :-0
Dumping 3500 watts this afternoon. Good solar day.
Dumping 3500 watts this afternoon. Good solar day.
Have you considered placing an air movement source into your compost pile (assumption - you have a pile) as a dump load?
As the newer site (last time I looked) didn't lay out the Oxygen issue as well I'll link to the old site:
http://web.archive.org/web/20040602231212/http://magicsoil.com/MSREV2/ox...
Note how the O2 level drops to anerobic in less than 1/2 an hour. And remember - the lack of O2 makes for all kinds of "nasty" reactions.
Odds are you lack the excess power for one of Jerry's babies (it seems that Jerry is out of the business):
http://jetcompost.com/3672sideways.jpg
What the TerraCycle people found is to make stock to feed their worms the Worm Gin is too hard to manage, but pre-treating with a rotating and forced aeration unit does work.
Have you thought about dumping excess into a hot water heater? And hot water heater storage size can be quite large;
http://www.builditsolar.com/Projects/SpaceHeating/AlanTank.htm
That's what we do. I have a 450 gallon heavy polyethylene tank, well insulated, built into the utility room. It looks like this one. It's 84"h and about 48"w. Its water is heated by solar, the woodstove, and I installed a 3500 watt water heater element in it. When the batteries get full, the aux relay in one of our charge controllers turns on the heating element (connected to our big, stacked 4000 watt inverters, 8Kw total). I would prefer to dump raw DC power, but that's a problem for later($$). Total cost for adding the heating element, including element ($9 at HD), hardware (about $15), and relay (30 amp AC contactor, $20) was less than $50.
I'm in the process of adding a small circ pump to prevent too much stratification when the element is active. Yesterday the temp at the top of the tank got to 175 F (hotter than the manufacturer's recommendation), while the temp at the bottom was 120. No good way to add an element at the bottom at this point. It's about 15" below the top; best I could do. The radiant floor system is setup to dump heat from the tank when it gets to 160, but I switched it off to test how stratified the tank would get; hence, the little circ pump.
The big water tank has a coil of 3/4" copper tubing at the top that heats our DHW, and the radiant floor uses the hot water directly from the tank. In summer, excess PV production goes to an air conditioner in our master suite, cooling the master bedroom and office. Our propane tankless water heater (a "normal" water heater was required by code when we built) collects a lot of dust these days. Nice to have as a backup I guess.
An outstanding system - kudos!
A couple of thoughts about shifting excess electrical generation, which might be approaching diminishing returns;
1. On days when heating is required, a heating element in the ductwork with fan control is one possibility.
2. Even simpler, a small electric space heater on a dump circuit left in the ON position in a frequently used room could also be a simple transfer technique when the dump engages.
Thanks, Will. It's one system that has worked better than I had originally hoped. Not as efficient as commercially available storage systems perhaps, but the idea was to have an unpressurized system so I could heat it directly from the woodstove without blowing things up ;-/
As for #1, I installed ductwork when I built the house, but have never installed an air handler. Someone gave me a nice, slightly used mid-efficiency propane forced-air unit that will get installed someday... I'm also in the market for a ductless heat pump system for the living area, mainly for dehumidification in summer.
...and #2 has already been implemented. I just turn it on manually when there's extra PV production, in whichever space needs it. Since we have a lot of passive solar, thermal mass and radiant floors, we don't need it much. I usually just run the dishwasher, vacuum cleaner, or something.
Lots of options. Too bad the gridweenies can't figure this out on a large scale. Maybe they'll catch up someday ;-)
Today the specific gravity of my batteries range from 1.250 g/cm3 to 1.275 g/cm3, and they needed 3.5 gallons of distilled water to top them off. Ten months ago they needed 2 gallons of water per year. Adding an extra PV panel last year seems to be charging them better and electrolyzing the water faster. The battery with a cell with a specific gravity of 1.250 g/cm3 (the next lowest is 1.260 g/cm3) is getting equalized with a battery charger.
I set the regulator to shut off at 14.3 V with high current and 14.8 V with low current. I can not set things above 15.0 V because my inverter shuts off from an over voltage condition at that voltage. If this new voltage level causes them to needed too much water, then I will probably restore the set points.
Looking at the specifications of your Trojan T-1275 batteries, the 150 Ah capacity is at the discharge rate of 7.5 A for 20 hours. At a discharge rate of 25 A for 4 hours and 40 minutes it provides 117 Ah.
I have not been able to verify the construction of your T-1275's, but traditionally golf cart batteries are made with plates with a thickness less than a commercial deep-cycle battery. The Depth of Discharge vs. Cycle Life chart is for a commercial deep-cycle battery. This might explain why your battery failed prior to the 2000 cycles shown on the chart.
Tom;
Thanks for sharing your experience. I hope the additional experience of seeing it posted here and how it gets discussed tends to be productive and useful to you as well.
Bob
Battery Quality is critical, note that we NEVER spec Valve Regulated Lead Acid (VRLA) batteries with recycled content. The Pb must be Pure and the charge controller MUST be temp compensated & smarter than a Border Collie especially for VRLA. You can get 5000 cycles (Decade+) if you design for 10% DOD and size PV array so that the Battery is topped off EVERY night even on cloudy days. See Life Cycle vs. DOD in this doc. http://www.sunxtender.com/pdfs/Sun_Xtender_Battery_Technical_Manual.pdf
In many applications, LIFEPO4 Batteries can be lower cost of ownership than VRLA,. but.. sourced from makers like CALB. owned by the Chinese Government. US needs to wake up, this is critical technology for the future.
In many applications, LIFEPO4 Batteries can be lower cost of ownership than VRLA
Sure. Lead Acid may get 500 cycles (100% DOD equivalent), but LIFEPO4 may get 5,000. If you get 10x the cycles at 3x the cost, your total cost of ownership will be lower where you use the batteries a lot.
All good points made by Longtimber but depth of discharge is probably the least important comparison. Whatever the discharge depth (not sure what your 100% DOD equivalent means), lead acid wants immediate bulk recharge followed by a long and energy-wasting absorption period to condition the plates. LiFePO4 does not need that, in fact lasts longer when never fully charged so there is no downside to having a battery capacity much larger than the daily PV charge capability. The daily PV output can be stored in a large lithium battery at 95%+ charge efficiency, then if it ever gets full you could take a hot shower whether you need it or not.
Another important consideration in terms of energy efficiency is at high discharge rates, there is no Peukert effect in lithium, so at high discharge it does not dissipate energy punching through internal potential barriers. For a given discharge rate the lead acid battery would need a larger capacity, which multiplies the need for a large PV array to fully charge it every day, which increases the energy waste during the absorption phase.
I did a search for "LiFePO4 solar battery". The closest I came was a 24 volt 30 AH cell, meaning I would need over 70 of these to equal the storage of my lead-acid cells at 8 times the cost. Nice to dream though ;-/
NIFe would be my first choice, cost notwithstanding.
Nick's figures are accurate for bare cells from China, you have to add FUD costs for failure on top of that, minimal for LiFePO4 banks that go between 20 and 80% capacity IMO but your mileage may vary.
Someday there might be a Price-Anderson act to indemnify against battery failure liability...
What was the price? IIRC, the last I checked prices were around 450/kWH.
Link? The 24 volt, 30 AH I mentioned above was $545. I didn't dig really deep though. $545/0.72 KwH = @$726 (X 52 KwH, our current) = $37,752 which is about 6.5 times what we paid in 2007. This is all rough math, point being that it's a lot, especially with shipping. I also haven't researched battery management systems for LiFePO4 batteries this size, but I bet it ain't cheap. We works with what we gots ;-)
Like I said, if I had that kind of money, I would go for NiFe. Hopefully these cells will last long enough to when some of these technologies will come down out of the stratosphere pricewise, and LiFePO4 solar batteries are a bit more mature. I had no problem upgrading our old PWM charge contollers to MPPT over time, and at a cost.
The link I had is dead. Here's a .32kWh (3.2V, 100 AH) battery for $144, so that's about $450/kWh.
http://www.all-battery.com/32v100ahlifepo4lithiumironphosphaterechargeab...
I think LA is about $150/kWh, so that's about 3x as much.
Looks about right. Top quality L-16+ about $145, big 2 volt cells are more, though if one can order through a manufacturer's rep, industrial 2 volt cells can be had for less, like our Hawkers (2200 AH forklift cells). They're big and heavy, about 220# each, wet, 28 inches tall. At the rate we discharge ours we're likely getting better than the 100 hr. rate which is around 2500 AH.
Thundersky (which is apparently called Winston now...?) has some whoppers: http://www.electricmotorsport.com/store/ems_ev_parts_batteries_LFP_win_4...
And you wonder how a Chinese diesel sub can appear in the middle of a US Carrier Task Force without the US Navy knowing its there. I wish we had that technology.
Yes I know we developed the technology, but we can't make it.
appear in the middle of a US Carrier Task Force without the US Navy knowing its there. I wish we had that technology.
Given how bureaucracies work, I'm guessing the US has the technology for parts of the Navy to not know where other parts of the Navy are and thusly a sub of the US Navy could show up in a Navy fleet and the fleet not know until the sub started playing YMCA.
We used to do that quite frequently, get a couple of hundred feet under a carrier and blast them with a really loud ping, or fire a flare nearby. One 688 captain got in hot water because he got so close his flare landed on the fight deck of the carrier he was stalking. The late diesel/electric boats were even quieter on lead-acid batteries. Newer battery tech may extend range a bit; other than that, not much difference.
Don't forget that for Li batteries, you have to add in the cost of a battery management system. You can't just series a bunch of cells and periodically do a equalizing overcharge like you can for Lead-acid.
There are a lot of hobbyists using these cells - I wonder what they're doing? There must be a lot of info out there, similar to the discussion above about LA batteries.
If you have ever been on the EV discussion list, you will be familiar with the products of this company.
Manzanita Micro Battery Management systems.
The advantage of lithium is that you don't need an equalizing energy-wasting overcharge with the associated heat, hydrogen, water loss, and acid spray. In a string of 100 amp hour cells with 80% design range most would go from 10-90% while those that have less charge efficiency would gradually drop towards 0-80%. At that point an LED on the cell could indicate it needs an extra 20% charge, e.g. plug a laptop-type charger into the cell for a certain period of time. That would involve less effort than the periodic monitoring and water additions needed for lead-acid.
Equalizing (or as it's called balancing for lithium batteries) is only needed if you want to store the maximum amount of energy in each cell of the battery, which only makes sense if you then discharge to zero on the weakest cell. You might want to do that on an electric vehicle for weight reasons, but maximum battery life would favor adding an extra cell or two instead so as to never hit the limit on any of them.
Current nickel-iron batteries have poor ~75% charge efficiency and ~1% a day self discharge, so a 10kWh bank would need an extra 100 watt-hours a day just to stay charged. Not a deal breaker if you have room for the extra PV panel.
The advantage of lithium is that you don't need an equalizing energy-wasting overcharge with the associated heat, hydrogen, water loss, and acid spray.
VS the energy-wasting discharge into resistors across each cell with the associated heat in a Lithium pack to attempt to make sure the cells are balanced?
which only makes sense if you then discharge to zero on the weakest cell.
*raises eyebrow*
Lithium to 0 volts in a cell?
And this doesn't result in a dead Lithium? (VS shortened life)
Current nickel-iron batteries have poor ~75% charge efficiency
And yet - seem to last a lifetime with tales of Grandkids getting GrandDad's batteries that still work.
This TOD topic is about a dead battery. NiFe batteries sure do seem to be unkillable.
(and efforts exist to attempt to provide instructions on how to make the batteries yourself unlike other battery tech)
Zero percent charge, not zero volts. The recommended low voltage cutoff varies with the particular lithium type, did not want to specify an actual voltage for fear someone would apply it to the wrong chemistry.
The energy-wasting discharge resistors are as you say an "attempt to make sure the cells are balanced". The point of my post is that you don't have to balance the cells if you limit the operating range of the battery. Just add charge to single cells when/if they go below low voltage cutoff. This will also maximize battery life.
If the fear of entering a lower technology/lower total cashflow life is true, having batteries that one can discharge below the normal operating level and still work and not have to have things like a charge controller which switches load resistors to keep cells balanced may be of importance to some readers.
Same with having a system that if your charge controller dies you could just directly connect the batteries. Having some electrical storage, even if not optimal, is better than having NO storage at all. Go look to stories about how having a few solar panels and a battery has changed various African villages. Imagine how you'll get water if you live in a city or on your rural property if you lack electrical power?
NiFe batteries existed during and after the Carrington event, alas the easy to find comments about the time was disconnecting the batteries and the telegraph system still worked. Plenty of documentation about the batteries existed within the old Ma Bell system, alas hard for outsiders to get or perhaps has not been saved.
An energy wasting absorption period is not a problem for an off-grid PV system because the PV array must be overbuilt by a factor of at least two.
Yair . . . I can never see the point in so called "hi-tech" batteries for domestic solar.
The technology is ancient, we know it works . . . and most importantly the components are not expensive and the batteries can be hand built/repaired at a local level.
Right up untill the mid sixtie's there used to be a "battery-man" in most fair sized country towns . . . some even made their own plates and seperators.
I have a 1920's automotive repair encyclopaedia which goes into detail about dismantleing and refurbishing the batteries in electric cars every year.
Cheers.
Jay Leno's 1909 Baker Electric