Mud, mud, glorious mud*
Posted by Heading Out on August 9, 2009 - 10:35am
This is one of a continuing series of posts that I am making to describe some of the technology that is used in the production of fossil and other fuels. Last week's post on tri-cone and diamond drilling bit can be found here. That post, plus tech talks I have done in years past can accessed through this tech talk link. They can also be accessed by clicking on "Tech Talk" in the rectangle at the top of The Oil Drum home page.
In my post last week, I wrote about physically breaking the rock, either by pressing a series of small teeth set in rings around the perimeter of cones that rotate around the bottom of the borehole, or dragging diamonds that are attached to the bottom of the drill string. There can be different numbers of cones and in the picture you can see a bit with four. In this particular case we had added a nozzle set through the center to jet under the teeth as they cut into the rock. The reason for this is that if you wash out the crushed zone of rock under the bit, as it is formed, then you don’t re-crush and compact it and the bit can penetrate into the rock more easily and faster.
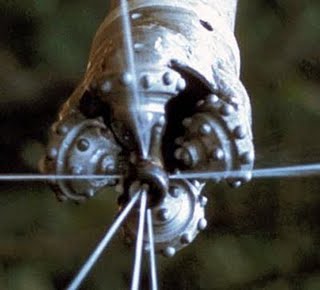
The jets both remove the crushed material and keep the bit cool, which is important if it is to remain sharp. (Removing the crushed material can increase penetration rates by a factor of 5, but that is another story).
The cones are mounted with their largest diameter running around the outside of the hole, and thus each cone will have the greatest number of teeth along that edge. We call the outside edge of the hole the gage, and the cones, bearings and mounts combine to form the drill bit.
Now if we just turned the bit round and round in the hole, it would start to drill into the rock, but after a short while the chips and crushed rock would fill up all the space between the bit and the solid rock, and the bit could go no further. We have to get the crushed rock out of the way, and preferably before it is crushed by the following bit tooth since that would also waste energy. And thus we have today’s topic.
When the old miner was hand steeling, he could either blow the chips out of the hole with his breath, or wash them out with a squirt of water. On a more sophisticated level this still holds true, but with some differences. In very short holes, or special circumstances, compressed air can be used to blow the chips that have been cut from the rock (hence the name cuttings) up out of the hole. However as the hole gets deeper this becomes less practical and some form of liquid must be used. Again it could be water, but there are several reasons why this is not usually the case.
Firstly the rock is much denser than water, and so if the water flows back up the hole (usually in the space between the drill pipe and the rock wall, a gap often called the annulus), and the fluid is not moving fast enough, then the cuttings will settle back down the hole, blocking the gap and sticking the drill pipe in the ground. For this reason the water is usually mixed with very small particles of different types of material that will increase the density of the fluid so that it will help lift the cuttings all the way from the bit to the surface. This can be as far as 3 miles up or more (15,000 ft or so) and so it's important to choose the right density for these additional particles. Usually the particles that are added to the water are made from finely ground clays, and this makes a mud, and the fluid has thus now, regardless of what is in it, become known as a drilling mud. The mud has to be thick enough to help carry the individual chips to the surface, but, it also has to keep them held in suspension when the flow stops while another length of drill pipe is being added to the string.
The mud, however, has a few additional things that it must do as it is pumped down to the bit, through the inside of the drill pipe, and then circulates back up the outside carrying the cuttings to the surface. This circulation is sometimes reversed (i.e. reverse circulation) so that the mud flows back up the inside of the drill pipe, but this is not common.
The first thing that it must do (as mentioned above) is keep the bit cool. As the bit rotates, and the cones turn on their axes there is a lot of friction generated under the thrust being used to push the bit into the rock. Some of this friction will generate heat (in the same way as happens if you press your palms hard together and rub them back and forth). Because the bit is in a confined hole, without the mud there is nowhere for that heat to go, and so it would otherwise build up, until it got hot enough that the bearings failed, and the bit fell apart at the bottom of the hole. (This is not a good thing to happen, since how can you drill through the parts of a broken bit with a new one?) So the mud flow also serves to keep the bit cool enough to keep working.
But there is also a lot of heat that comes from the rock. This is because of something called the geothermal gradient. This is one of the last, almost untapped, sources of energy that we have. While it varies around the world, the numbers where I come from are these: At 500 ft below the ground the rock temperature is 60 degrees F. For every 60 ft you go further down, the rock temperature goes up a degree. So that if you are 1100 ft down, then the temperature is 1100 - 500 = 600 (extra depth)/60 = 10 extra degrees + 60 = 70 degrees F. And at 8,000 ft (a deep gold mine) it will be ((8000-500)/60) +60 = 185 degrees--which is why they refrigerate the air in mines that go that deep. And this rock temperature in deeper wells can also damage the bit. So the mud flow has to also take account of the depth and the rock temperature.
To keep the bit cool and carry away the cuttings the mud flow has to be quite fast. But there is a small problem that arises (and is not always fixed). As the hole gets deeper the weight of the mud in the hole will press down on the chips that are being formed by the bit. It will try and press them back down against the rock, (it is called chip hold-down). To stop that happening the mud has to be formed into a stream of fluid that can be pointed at the rock and (just as you move dirt with the pressure from a garden hose) will push under the chips and lift them into the circulating mud flow, as it then flows back up the annulus. To do this the mud feeds from the center of the bit out through a set of jet nozzles that point the streams down onto the rock. The deeper the bit is drilling, the closer the nozzles have to be to the rock, in order to reach through the surrounding mud liquid with enough power to lift the chips and get them moving when it reaches the rock.
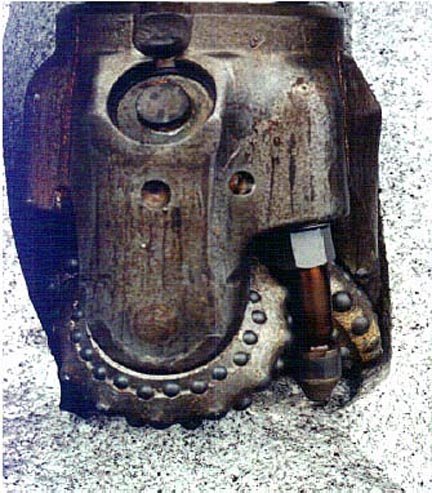
The third thing that the mud has to do is to act as a seal around the wall of the hole, where the bit drills through the different rock layers. As the hole gets deeper some of the rocks it will go through are very permeable. In other words the mud can flow into them, or water can come out of them. We don't want that to happen. If the mud flows into the rock, then it is lost, and the circulation of mud stops (its called lost circulation). Without the mud, the cuttings settle back down to the bottom of the hole, and the bit is stuck again. So to prevent that the clay particles are made large enough, so that if the mud starts to flow into the rock, the particles cannot enter the very small gaps in the rock. Instead they are filtered out and are left on the edge of the hole. As the water flows into the rock, leaving the clay behind, the clay builds up and forms a layer of clay along the rock wall. This seals the rock from the mud in the well, and stops the fluid from leaking out of the well.
To do all these things, with different temperatures in the well, different chemistries in the different rock being drilled through, and different fluids flowing into the hole, requires that the mud be very carefully selected for each job. And sometimes that chemistry may be such that simple water cannot be used as the carrier fluid. There is a shale in Texas, for example, called the Gumbo shale, that turns from a hard rock to mud (like a Louisiana gumbo); when it gets wet. So if you are drilling through it, either the water has to be treated with chemicals so that it stops being able to wet things, or you use a different base fluid, and change to perhaps an oil. There are a number of patents that deal with different additives to the mud, of which I have cited, for example, just one.
So making mud, and using it properly can be an ongoing job on an oil rig.
Again, if there are questions, or comments, let me know, since I tried to make this relatively simple, and may have gone too far for some of those involved.
* The hippopotamus song by Flanders and Swann
Thanks, Dave. I never cease to be amazed at how complicated and high tech this all is.
What kind of degrees do the people have that develop drilling muds?
What kinds of companies make and sell drilling muds?
Nice article.
In terms of companies Gail, MI Swaco (http://www.miswaco.com/) is among the industry leaders in drilling fluids. For degrees - chemistry is a good under graduate starting point.
The properties of mud also make it rather effective for the telemetry between the surface, and the drill bit.
Surface to downhole communication is referred to as downlinking : this is used to send direction commands to the rotary steerable tools.
For transmitting information to the surface, measurements made whilst drilling (MWD) to the surface, the expression "mud pulse telemetry" is used.
Of course, with wired drill pipe (WDP), neither of these techniques are required, as the information is conveyed along a wire in the pipe. However, WDP is still in its infancy and only used on a handful of jobs worldwide.
Degrees in chemistry and mechanical engineering would be useful foundations. Apprenticeship with a drilling mud alchemist is probably necessary as well, since mud technology is at least as much an art as a science.
Some of the biggest equipment I've seen on flatbed trucks on Texas highways has been mud pumping equipment.
And thanks, HO. I always enjoy these tutorials.
Gail -
For some time now, I've been toying with the idea of writing an article for TOD along the lines on how people perceive technology and what is meant by 'low-tech' and 'high tech' technology. I have always been a bit uncomfortable about the way people throw around the term 'technology' without fully thinking through what it means in a given context.
Your above comments reinforce a notion I have had for some time that what is or is not considered 'high-tech' is largely in the eye of the beholder.
In my view, just because some activity requires a great deal of acquired knowledge and specialized 'art' does not in and of itself make that activity 'high-tech'. As an example, a Japanese craftsman laboriously making a samurai sword by traditional methods (a process that can take over a month of tedious hard work) is doing something that would be virtually impossible for someone uninitiated in the art to duplicate, regardless of how much academic information that person had access to. Does that mean that samurai making is a 'high-tech' activity?
So, from that point of view, I really question whether doing drilling mud is 'high-tech' at all. Sure, the petroleum engineers and geologists have to know what they're doing, and they get to know what they're doing by both hands-on experience and from decades of oil company acquired knowledge about what mud to use in what formations and under what conditions. This is sometimes called 'art'. But is it really high tech?
In my view, while the associated seismic modeling associated with oil well drilling clearly qualifies as high-tech, the physical act of pumping mud down a well does not. Why? Because it involves commonly available equipment such as large high-pressure pumps and pipe. Furthermore, most of the components of the drilling muds are hardly exotic and hard-to-obtain substances and require no super-sophisticated manufacturing processes.
As I see it, for something to legitimately qualify as high-tech several conditions must be met, but I don't have the time right now to get into that here.
I expect that if for some reason we had virtually no electricity, drilling mud would be mostly a lost art.
Somehow the right size particles would need to be made or selected. This could be done by making particles of various sizes, and filtering them through screens of various sizes. These screens would somehow need to be sized precisely.
Large high pressure pumps may be common, but I am sure they need to be made to very fine tolerances, to work properly. We often forget this. I expect the steel in the pump would have to be made at very high temperature, using materials imported from places around the world.
I suspect that the artist could continue to do his work, regardless of the availability of electricity or imported products. He would be much less likely forced to stop because of Liebig's Law of the Minimum interfering with some minute aspect of the operation.
You may not call this high tech, but it is vulnerability to disruption if our world suddenly changes in some unplanned way.
Gail -
Well, if there's no electricity, then practically everything requiring power will come to a stop. So what's your point?
What is so high-tech about sorting particles by size? It's been done in one form or another for several hundred years. No big problemo.
Large pumps, like all process equipment, need to be made according to certain specifications. And yes, steel begins its life in a molten state, as it always has since people were making swords out of the stuff. Again, a big SO WHÅT?
Vulnerability to disruption and high-tech are two very different things, though by no means mutually exclusive. Something simple, like growing corn with a high synthetic fertilizer input can be highly vulnerable to disruption, while some rather complex things are relatively robust and quite secure.
So, we have to be careful when we talk about high-tech/low-tech. As I said, this is a subject that I might want to expand upon in an article. Do you think the subject has merit?
Whether or not a discussion of high/low tech would be of merit is of course debatable, but the ensuing discussion could be fun. joule, I have an inkling that your definition of high tech would be near what my retired electrician kin calls fm (f*cking magic)--stuff at the extreme leading edge of technology's capability--quite at odds with the former GE executive's view (mentioned in a post farther down) of high tech as near bullet proof mature technology. At the very least I am curious to see how you define it.
...but to the key post
Thanks Heading Out, such clear, digestible, piece at a time explanations of the drilling process are likely to really stick with readers quite a while.
I eagerly await. *O.O* I love discussions of this kind.
EDIT: I got way ahead of myself and posted Waaay off topic for this article, so I deleted it. Please write it sooon!
I used to be in the supercomputer business. The definition of what a supercomputer was was time dependent. Obviously the capability of the supercompter of 25 years ago, is much less than of your cellphone today, but we don't call the callphone a supercomputer. A similar sliding scale applies to high tech. Twelve thousand years ago, a cleverly shaped stone spear point "the clovis point" was "high tech". The Samurai sword was the high tech of its age. So high tech has more to being close to the recent cutting edge of technology.
I believe that possibly, familiarity breeds contempt :-)
In my case at least, having worked as a deap sea diver on oil rigs and having had the rather unique experience of shooing sealions, sunning themselves in spilled drilling mud, off the access decks of a drill ship in the Baja California, drill bits and mud don't exactly make me think of "High Tech".
Here is one example of what I think of when I hear the term "High Tech"
http://www.edge.org/3rd_culture/church_venter09/church_venter09_index.html
The geek in me loves these articles. Paradoxically though, the fundamental human desire to do better and find solutions to problems is exactly which has gotten us into to trouble in the first place. So far we have been able to "solve" problems by using human ingenuity to use natural resources in a way which has been overall accretive to humanity. It seems we are now at a (I hate to use the term but will anyway) “tipping point” where the externalities of human cleverness are starting to become so obvious that they are difficult to ignore.
Still, articles on the nuts and bolts of how we extract mankind’s most important resource (a friend of mine refers to oil as a gateway resource, which I think is very apt) are important because it shows how we collectively have figured out very complicated problems while at the same time highlighting a certain desperation to get to oil….
WeekendPeak
Thanks for the huge information, actually I don't know about this. Thanks for add some more useful stuff in my mind vocabulary.
camping tents & hiking equipment & camping equipment
Thanks HO - this is highly entertaining and enlightening - and extremely high-tech. No wonder a deep drillhole-op today costs 'in the hood of' $ (X+1/2y) gazillion :-)
I can just imagine the extra challenges awaiting off shore Brazil in the years to come. Also, what happened to Jack 2?
Wikipedia : Jack 2 proved the existence of a new play in the deepwater Gulf of Mexico. The estimated oil reserves the play could contain range between 3 and 15 billion barrels. News of the find was credited for contributing to a drop in crude oil prices.
It's been 3 years now, so what have you "Jack2", 3 or 15 billion barrels ?
I suspect that it will be 0 barrels due to the ongoing financial apocalypse. Jack is likely to be one of the first casualties of that event.
Well, Jack #1 comes online 6 years from now: Chevron runs rule over Jack and St Malo - Upstreamonline When the Jack 2 discovery was announced it was assumed production was right around the proverbial corner: Five years to first production - GLG News. i.e., 2011.
How drilling "mud" copes with molten salt is something I'd like to hear more about.
How drilling "mud" copes with molten salt is something I'd like to hear more about.
They probably don't even need a rotating bit. Just run brine through the mud plumbing. But then of course the hole goes away when you trip the string...
How big are the chips? If they're close to sand or dust in size, why don't the drillers just run a vacuum line down to the bit? It would take a hefty vacuum, but probably no more energy than pumping mud down into the hole and then forcing it out again... Of course, I've never heard of this being done, I've always heard about drilling mud being used and that's it.
It depends a bit on the bit design, which is in turn controlled by the rock that you are drilling through. I will be writing about considerations of chip size etc in probably the next post in this series. Generally they are quite a bit bigger than dust, and that is what you want, since the smaller the fragment size the greater the energy cost in creating it.
Drawing a vacuum is functionally equivalent to blowing air in as addressed in the article. The medium density is simply insufficient for drawing the chips up far enough in most cases.
not quite. the difference between ambient pressure (14.7psi) and a total vacuum (0 psi) is 14.7 psi.
The difference between pressure (say, 3000psi, the pressure found in a scuba tank) and ambient is enourmous. 3000 psi will blow a chunk of steel the size of your wrist through a concrete wall.....
Rgds
WeekendPeak
Um, that depends on the area that it is applied over in order to generate the required force. High pressure has changed definition over the years. In the waterjet business (where it is used for cleaning and cutting) below 5,000 psi is considered pressurized (as in pressure washers); up to 30,000 psi is considered high pressure and above 30,000 psi is considered ultra-high pressure. Cutting tables can now run with waterjets at pressures up to 100,000 psi.
Making equipment operate at a pressure of 10,000 psi has not always been trivial. One year we bought every swivel that claimed it could operate at 10,000 psi and ran tests of their operational lifetime. I ended up standing holding a hose on one that, with that cooling, would last 14 minutes. But in that 14 minutes it allowed us to drill laterally into a coal seam a distance of 50 ft.
Ummmmm. Steam engines were invented because you can only suck up water about 32 feet, equivalent to a change in pressure of 14.7 pounds per square inch. With dense mud the height would be a lot less.
You are correct, of course. This moves the solution in the wrong direction for drawing the rock chips up the hole.
People don't have enough experience with vacuums and frequently overestimate the power available from them.
Well actually there is a technique that allows you to do a little more than that. It is called hydro-excavation and is one of the more recent "hot" things to do. Simplistically you use a small water jet to disintegrate soil into its grain sizes (say around 250 micron) and marry this with a vacuum suction to pull the fragments away.
It is delicate enough that we used it to remove soil from over landmines, but the trick to getting it to go deeper (some of the new applications go down up to 140 ft) is to a) marry it to a vacuum truck b) keep the nozzles and suction tube within less than half-an-inch of the surface. At that point you are sucking in air from the surroundings and the velocity of that air will carry the disintegrated soil up the distance you want it to go.
It comes in very useful for removing soil from around fiber optic cables, clay pipes and other delicate objects in the soil (did someone say sewer lines) that you really don't want a backhoe to cut into .
That sounds like a very interesting technique.
One of the greatest uses of the drilling fluid is to continue to fill the well bore to prevent soft formations from sloughing off and to provide a balanced pressure to offset the formation fluid pressures. The mud properties are carefully monitored to ensure the density is correct for the current depth. If the pressure is to great, it could fracture a soft formation, loosing the drilling fluid into that fractured zone. As the net head pressure is lost due to such a fracture, then shallower zones could suffer a blow out. (I once had a well hit a prehistoric oyster bed at about 1000'. We lost mud and then a sand at 800' blew the well out)
On the other hand if the mud weight is to light especially drilling into an over pressured zone, then the formation pressure could simply cause the well to come in, flooding it with less dense formation fluids. As more lighter formation fluids enter the well bore, the pressure is lost and again a blow out could occur.
Another danger is that if the mud weight is to heavy, lower pressure zones in the formation would have some liquid components of the mud separate and seep into the formation. This would occur until enough of the solids collect to form an impermeable mud cake barrier. This is normally a good thing, but if the mud weight increases a large pressure difference could build between the well bore and the formation, where the mud cake acts as the barrier. If drill pipe movement or wireline logging cuts the mud cake and the pipe or wireline tools stop just for a moment,they could become differentially stuck because of the pressure which then leads to a painful and costly fishing job.
Thanks for the input and information - I have a post in the series that will talk about pressures, perhaps in a couple or three weeks. But then I need also to explain the different geologies so it is going to take a while to cover the waterfront.
Thanks for your efforts. I didn't want to jump ahead, but was trying to address the initial question upthread on the use of a vaccuum to suck out the cutting.
There are so many facets in the industry most people never even consider, eg the beauty of mud. Please keep up the great work.
Something else that should be pointed out is that this same technology is used in drilling water wells and wells for geothermal heat pump installations.
Something that goes along with the "drilling mud" technology is the grout used in wells - especially geothermal heat pump wells. Under Minnesota's antiquated laws, only one of the many grouts can be used for this purpose - And that is not always the best one from a thermal transfer perspective. More Government regulations preventing modernization and efficiency improvements!
I was told that some of the people doing drill tunneling under roads and such were looking into how they could drill geothermal heat pump wells to cash in on the coming boom in geothermal installations. My guess is that when they find out they will have to have an expensive rotary drilling rig and spend a LOT of time developing the "on the job" know-how of well drilling, that they will decide that it isn't such a lucrative undertaking?
Another interesting thing gleaned from talking to a local well driller about geothermal wells and water wells is that the State of Minnesota laws prevent a well driller from replacing a deteriorating well casing on an existing water well. This is done routinely in other States, but in Minnesota you have to seal the existing well and drill a new well at very major expense. Another case of government bureaucrats dictating to the people who actually know how things can and should be done.
Thanks for a very informative post. I presume that once you hit pay dirt, you don't want to use a mud that will clog the pores? Then in operation I suspect you want to maintain the seal in the hole above the oil bearing strata, but not clog the pores of the oil bearing level. So I imagine it can get a bit tricky to get it right.
On weekdays my bikeride takes me through a small oilfield with five operating pumpjacks. Every few months one or more well seems to be stopped. Then a drill truck comes up and does some sort of downhole maintenence for a day or two. The cycle seems to repeat every few months. So I guess there is some sort of regular maintenence required for some or all wells?
I am going to write about what happens after you get the hole in place (and how the treatment depends on whether it is in sandstone or a carbonate rock) in a future post. This includes pumping in cement and a number of other things.
Something I didn't see addressed, are the muds recycled or are they one time through. It seems it would be very difficult to filter the small particles of rock out so as to not wear out the high pressure pumps.
What kind of flow rates are we talking here? Gallons/hour, gallons/minute, gallons/second?
They screen out the cuttings (which they want to see since it is a check that they are drilling what they think they are) and then recycle the mud. The circulation rate depends on the diameter of the hole, in terms of flow rate, and it is in the gallons-a-minute type of range. You don't want the flow back to be at too high a speed, since the fluid can cause hole erosion if it is moving too fast.
About these various muds and "frac' fluids-I hear that the composition of most are rigorously gaurded secrets although the basic list of common ingredients is not very long and well known.
Surely it would not be hard to steal a sample large enough for analysis if you were an environmental activist,for instance,and willing to go under cover as a laborer/trainee?
I would think that simply leaving the job site w/o cleaning up would be enough,if you save your bath water, for a serious CHEMIST to get started.
This information would be of great value of course if water pollution were to occur-which is apparently happening from time to time.
I wonder about the cost and availability of some of the more exotic components of drilling mud. Clay is dirt cheap (of course!) but isn't dense enough to suspend rock chips if circulation is halted. So I understand that barrium sulfate powder is added to increase density. Is there an ample suply of barium sulfate to support all the drilling required for obtaining our natural gas supply from tight sand and shale formations?
During the 60's I did a survey of resources used in medicine, especially radiology. At that time I found that barite was very common with ample long term supplies. At that time much of the domestic production was in Missouri. At the present time domestic production seems to have shifted to Nevada. Note the imports from China in the following USGS link.
-- I once had the impression that the weight of the barium in drilling mud was useful to counter pressure and prevent blowouts??
http://minerals.usgs.gov/minerals/pubs/commodity/barite/mcs-2009-barit.pdf
Roger - perhaps you're thinking of the ingredients in fracing fluid, which are proprietary, as I recall. Here's a list from an environmental website: EARTHWORKS - Hydraulic Fracturing 101
I liked the discussion (pro and con) on whether the use of drilling mud is high or low tech.
I have encountered this debate many times over my corporate career in R&D - not about drilling mud but about all technologies.
I once read book by a retired R&D chief in GE on that subject and he had an interesting thesis. His point was that people have high and low tech backwards because most of them have never been involved in product development.
His example was comparing personal computers with home clothes washers. Clothes washers went through a long development cycle and gradually through many technology improvements eliminated every possible mode of failure and for the most part ran effectively for years.
That was high tech. Personal computers may someday reach that level of excellence but for now are highly unreliable by comparison. They are low tech.
I think he would have defined drilling mud as pretty high tech.
Right. Having worked in a number of technology fields I got the impression about 20 years ago that the computer nerds decided that only their narrow little field qualified as high tech. Not too bright reporters got on the band wagon and thus we have to have this discussion.
I would simply say that high tech is anything that involves some arbitrarily complex level of scientific endeavor. Here are some non-computer related fields that I would call high-tech:
-The Apollo program (even today!)
-Ultra low temperature refrigeration
-Optical lens construction, including thin film filters
-Astronomy
-Automobile tires
-Carbon fibre composite structures
-Bridges
-Metallurgy (that can make those swords with intellect instead of "art"
-Nascar type race cars
--Japanese Motorcycles
A lot of common technologies were "high tech" before computers but are mixed with computers now:
-Power grids
-Power plants
-Assembly lines (including kanban factories)
-Machine tools
Personally I consider computer programs to be technology dependent but not, in themselves, to be any more "technical" than good grammer.
I agree - hi-tech is 'everywhere' (!) and - depending on which foot you stand on - one could argue that GoogleEarth ( http://earth.google.com/ ) is "the" single most advanced and Hi-tech achievement ever ... but not b/c images can be mapped onto a rotating sphere on your computer ...
.. BUT because it is the last link in a long chain of amazing achivements. Let's see, Google Earth would not have existed without :
- All sorts of motors / engines / metallurgies - or 'in short common tech' ..
- aviation
- rocket science
- semi-conductor flip-flops / transistors
- satellite tech with navigation and photovoltaics
- telecom, high speed internet
- top computer hardware and software
- best of camera- and lense tech
- bright brains at Google ... (and more)
As a philosophical concept - the modern or actually 100 year old cone-based drill bit(1909) in concert with todays theme here ::: mud ::: - can be seen as the most advanced thing "ever" b/c those are combined 'THAT SINGLE DUAL THING' which really sped up industrialization and put ALL TECHs were they are today! Sole Facilitators of industrialization - very hard to beat!
Un_invent "Hughes drill bit" and kiss your HiTech dreams of tomorrow a ...... long and sticky good nite ! (Hey I'm PO aware, so U don't have to tell me ....)
Thankyou for another really informative article.
Id love to hear more about how they steer these drills, how that communication works etc...
My thanks as well. I look forward to reading more in your series of oilfield technology articles. One topic I would especially like illuminated is the development and use of continuous tube drilling techniques. (Or is it just continuous tube casings?) Driving from Texas back to visit my family in Oklahoma I often pass new drill sites; some have a large reel of tube mounted to the rig instead of stacks of pipe.
I had pretty much put oil drilling technology out of my mind after a few weeks of working as a mudlogger during the summer of 1973. The company was Baroid, then a subsidiary of National Lead. I had dreams of laboratory employment, working on electronic instrumentation, but the only jobs open were on a Glomar drilling ship in the Gulf of Mexico south of Mobile, Alabama. The routine consisted of bagging small samples of drilling chips from the "shale shaker" for every 10 ft the bit descended, which were given to the geologists for microscopic classification of foraminifera. Every 30 ft we would seal a sample in a can with preservative for shipment to the lab in Houston.
Some shifts (12 hours on / 12 off) were completely occupied with changing the drill bit (tripping), so there was nothing to do but housekeeping, drill log maintenance (hand drawings), or pestering the geologists with questions as they consulted thick volumes of "foram" illustrations. One geologist was an Italian that hated the music of Pink Floyd. While Dark Side of the Moon played in one end of the trailer, he would sing opera at the other end. I should have spent more time listening to him.
Two weeks on ship and one off didn't suit me - so I returned to school. Not until finding the peak oil writings of Kenneth Deffeyes via John McPhee's book Basin and Range did my interest in oil drilling revive. Then I found The Oil Drum...
I plan on adding a bit on coiled tubing when I talk about the drill string. Thanks for the story.
For learning about directional drilling Wikipedia is a good start
http://en.wikipedia.org/wiki/Rotary_steerable_system.
Essentially there are two methods in use today - with a "mud" motor, or a rotary steerable system.
Mud motors have been around since before I joined the industry - they rely on the skill of the Directional Driller, and Driller to be effective (hold the right toolface, and prevent stalling), although new technology is automating the process to a certain extent.
Rotary Steerable Systems really took off earlier this decade as they out perform mud motors in terms of ROP (rate of penetration) and hole quality (no micro-doglegs, predictable gauge), and whilst sensitive to drilling parameters do not require such a careful "feel" as a mud motor does making their performance more consistent.