Energy Costs in Drilling
Posted by Heading Out on August 16, 2009 - 10:57am
Just as the thread on post on Drilling was winding down two weeks ago, horizonstar posted a comment about the tools that Potter Drilling is developing for geothermal drilling, with $4 million worth of help from Google. The comment takes you to a Grist post, from which I am now going to pinch the top illustration.
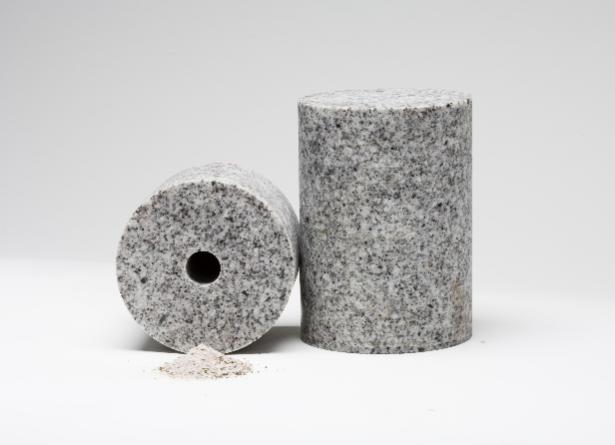
Now (if you will forgive the vanity) I will add a picture from my doctorate, and an experiment that I carried out in 1967.
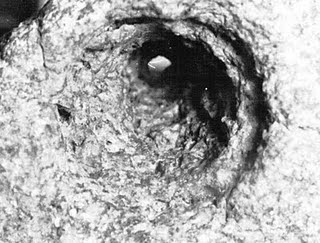
Now if you look at the two holes you might think that the top hole is the better, and more efficiently drilled. This post is going to try and explain why in fact it is the bottom hole that is better.
It will become one of two posts that I plan on writing on the relative performance of different tools in drilling, including ideas such as lasers, electron beams and the infamous REAM. There is a video of the two stages of the development of the Potter drill in an article in Popular Science from a couple of months back that is worth watching, since it explains their idea.
So why isn’t their approach a good one – well there are a couple of reasons, let’s start with the basic idea of breaking rock. Way back when the world used a lot of coal men still mined it using a pick and a shovel. In using the pick the miner would attack cracks in the surface of the coal and grow the crack so that he could wedge out larger lumps of coal, rather than picking out the coal in small pieces. If he did it effectively he would use something on the order of 4 joules of energy to mine each cubic cm of coal he mined (4 j/cc).
If you are breaking out rock from the solid the amount of energy you need depends on the surface area of the rock that you have to form to break the rock out. Assume that it takes 1 unit of energy to hold the molecules across a sq. cm of rock together. If I want to split the rock through that cm of contact I am going to have to break all those connections and (if the process is 100% efficient) this will take just slightly more than that unit of energy to make the break. Now here is the important bit:
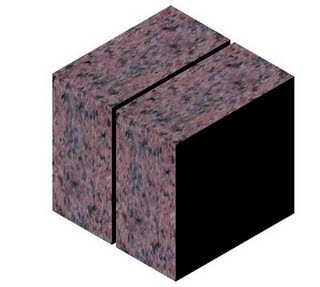
If I take a cubic block of rock that is say 1 meter in size, and split it down the middle I will cut through 1 sq m of rock over the fracture that I create. So with that same amount of energy holding the rock together (which we call surface energy) it will take 100 x 100 = 10,000 units of energy to make that one crack.
Now if, instead of breaking that rock into just two bits I broke it into a sixty-four, by making three cuts vertically parallel to the front, three cuts vertically perpendicular to the front and three cuts horizontally, then I would have split the rock into 64 pieces each 25 cm on a side, but it would have taken 9 cuts of a sq m each, and required an input of 90,000 units of energy to break the rock into the smaller sizes.
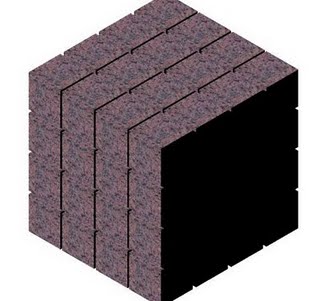
Thus the smaller the size the pieces are broken into then the more energy that you have to put into breaking the rock to make those smaller pieces. Consider that if you are breaking the rock into a fine powder (as the pieces are with the hole drilled at the top) then if those particles are 0.25 mm on a side then the energy input becomes that much greater (4,000 cuts along each direction – 12,000 cuts amount to a total of 12,000 times the energy needed if we just broke the rock out in two big bits).
So breaking the rock out in bigger bits is better – but how can we do this with fluids. Well, this is the difference between the thermal process and a water-jet based process. With the thermal process what you generally rely on for the fracture in granite is a phase change in the quartz element of the rock that occurs at about 1300 deg C. This causes the rock to spall and has been used in the granite industry for initial channeling around the blocks to be quarried. (It is very noisy and fairly slow – around 14 sq ft/hour of production). The particles produced are very fine, and the energy required is around 12,000 joules/cc.
Water cuts into the granite in a different way, first penetrating into the cracks between the different grains of the rock , and then as that water wedge is pressurized by the following jet, forced deeper into the crack, growing it and breaking the individual rock grains away from the surface. These grains are much bigger (so the hole wall that you can see in the second picture is rougher), so the energy required to drill can be down in the hundreds of joules/cc instead of thousands.
The other advantage that waterjets have (if configured with sand in the water) is that they can drill through any rock the drill comes up against. That is not the case with the thermal lance, since some rocks just melt into globby messes when heated, and that has to be pushed away (ask the folks at Los Alamos about the nuclear powered thermal drill that they invented one time – they showed how to do that). And the question is pushed to where when you are drilling holes thousands of meters deep.
And just to respond to the point about pipe-dreams that was mentioned about these ideas being impractical – Gulf actually drilled to about 5,000 m deep with an abrasive waterjet drill about 1970. So these ideas do have some practicality. But I’ll return to that aspect in my next post.
Oh, and just to show that you can break out meter sized blocks - this was from when we were excavating the rock under the Arch in St Louis to put in the OmniMax Theater.
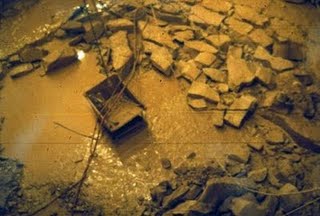
Very interesting. It would be nice to have a sense of scale in the last image. How do the rock pieces "drift" to the top? (This refers to the short video in the potter frilling site.)
While I don't remember exactly I think that the hopper that you see in the middle of the picture was 3 or 4 ft in width.
Sorry I didn't reply sooner, but I spent the day traveling to Houston.
I'm having a problem viewing the video tonight so I'll answer that part of the question tomorrow.
Heading Out,
great work ,very informative! thanks!
What kind of pump can generate such high water pressures and what is it made of?what are the nozzles made of?What is a typical rate of flow for a single nozzle?
The typical high pressure pump we use today may run at 20,000 psi and deliver 10 gpm of water. It feeds the water to nozzles that are about 0.04 inches (1 mm) in diameter - or that order of magnitude. The pump plungers these days may be of a ceramic or steel, and are available at operating pressures to 50,000 psi. For industrial cutting we use intensifiers which can be bought to deliver water at pressures of up to 100,000 psi at flow rates of around 1 gpm. The nozzles that they use are diamond, while at the lower pressure we will use a carbide as the nozzle material (or steel at lower pressures).
So a single nozzle might use 4 - 6 gpm, depending on diameter and operating pressure.
I once had the idea of what I call resonant drilling. If precisely timed hydraulic pulses are sent through a column of water where frequency = length/speed of sound in water then small repeatedly applied forces at the top would as time went by create very large force at the bottom of the column. It is like the ability of a precise pitch being able to break a crystal wine glass.
I'm glad you didn't go ahead with your resonance drilling method or RDM, b/c if successful we would all be part of your planetary dissolvement - :-)
That said - thanks again HO for propagating your know-how..
The idea works, it was used by a company called Hydronautics, under a Dr Andrew Conn, to generate a form of cavitation that proved effective in drilling through rock and other materials.
If I remember correctly Michael Crichton used the same sort of idea in a plan to induce earthquakes or some such in one of his novels.
Maybe this was already covered in one of the previous tutorials, but I'd like to get some idea of how much fuel is actually consumed in drilling an oil or gas production well of the most common diameter. It would be helpful if this were on a unit basis, say gallons of diesel fuel (they are usually diesel powered, aren't they?) per thousand feet of well depth.
I know this will vary greatly with the type of formation drilled, but are there any rule of thumb numbers for say sandstone, limestone, shale, and granite, etc.?
If such figures are not readily available, then I would imagine it would not be terribly difficult to back-calculate a rough estimate if one knows i) the size of the engine powering the drill rig, ii) its specific fuel consumption (say lbs of fuel per horsepower-hour), and iii) the typical duration of drilling time per 1,000 depth for the different types of formations.
I suspect that even if the amount of fuel consumed is considerable, it is still probably only a small fraction of the energy produced by the completed well over its useful operating life. (Of course, one needs to also take into account the energy wasted on drilling dry holes.)
Actually I think it is going to be in the next one. Because holes are of differing sizes we generally use a measure per unit volume of rock removed - with the number from a good tricone being around 120 joules/cubic centimeter (the energy unit, not your good self).
I will have to dig out the specific energy (that's what we call it) of drilling other rocks, but the post does cover different energy levels for different types of rock drilling.
However, as you know, the energy to break the rock is only part of the process. And in drilling the weight across the bit must be carefully controlled to ensure the bit works well. Since the weight comes from the steel in the pipe above the bit most of that weight is actually carried by pulleys at the top of the drilling rig, and only a small amount allowed to fall on the bit to keep it drilling into the rock. However the whole drill string must be turned by the kelly at the top.
So you can see there are a number of posts still to be added to explain all this.
There is a lot of embedded energy in stuff like well casings, or in the case of underground mining, the various bracings used to avoid rockburst dangers etc. How does this embedded energy content compare to the energy needed to simply break and move rock?
In the granite example, th ehigh tech drilled hole certainly has a nice "quality", which might be important if things need to be inserted through the hole. So it may well be, that paying a much lerger energy price is worth it?
That's something I wonder about as well. In "drill and blast" excavation methods for mining, a small hole is drilled, using an admittedly large amount of energy for the small volume of material removed from the drill hole. But the hole then enables a large volume from the rock face to be blasted out efficiently. So the overall energy efficiency can be pretty high.
If hydrothermal spalling is able to bore small holes at a rapid rate, it could be part of a cost-effective excavation system. But I wonder about its use for deep drilling; would it even work in a mud-filled hole under very high surrounding pressure?
It is a function of the size of the particles produced, and with explosives the holes and patterns are designed to create pieces of certain sizes to most efficiently break the rock and to make it easier to collect together and move.
The movie shows how the company plan on using the mud to produce a high speed jet from a partial vaporization of the water in the mud, and thus to propel the rest at a high enough rate that it cuts into the rock, which is weakened and fractured by the heat. (At least as I understand it).
Really smooth holes are useful in some applications (they reduce fluid friction as it moves past) but can be a disadvantage in others, when you are trying to grip the walls to hold a steel casing in place, for example.
confusing.
Thanks for the post!
We sometimes hear about the possibility of using electricity to replace tasks that are now done by fossil fuels. How amenable to electricity use are rock cutting and other drilling? How much of drilling is powered by electricity?
What I have seen in the oil and gas business seems to be powered by natural gas or diesel, but it could be different elsewhere.
I don't think it's a clear cut situation. I know TBMs are operated by large electric motors; I suspect that the same is true for most all drilling equipment. However, the electricity is invariably produced by diesel electric generators near the job site. Not practical to run a transmission line tens or hundreds of miles to the nearest power plant or substation. Portable wind turbines? Not for the levels of power needed at these jobs!
I am raising this question because of all of the questions about wind turbines taking over for tasks now done by diesel. It sounds like there would have to be a lot of transmission lines built, to make it work (not to mention storage for non-windy days).
It seems like every renewable energy would have contain some extra cost in either more down time or more expensive equipment.
But it seems like a solar/wind/storage technique would cost on the order of 2X or 3X the price of diesel for the same unit of electricity. ($0.20/kWh diesel and $0.30-$0.40.kWh for solar/wind with storage)
There would be less drilling but I wonder if it's an acceptable cost to society...
A better bet might be mobile small nuclear reactors, like the Hyperion's uranium hydride reactor or Toshiba's 4S "nuclear battery".
Or the Ford Nucleon
H.O.,
It is great to finally see some numbers put to this concept.
According to David MacKay's book, Sustainable Energy - Without the Hot Air, a geothermal well can sustainably produce 17 mW/m2 of earth surface area (not the well). If this technology can be used to drill a 50cm diameter hole to a depth of 15km (as the inventor claims)then at 12,000 J/cc, it will take 3.5e13 J. So sustainably operated, the well will take 2.08e15 m2-seconds to pay for itself (not counting tiny details, like the energy cost of the 15 km casing). I will take a wild guess that the well can draw heat from within a 50m diameter circle - can you frac granite at 15 km depth??? Then it will only take 33,575 years to pay for the well drilling - after that its all gravy!
Heat mining. The only economical forms of geothermal energy withdraw heat at a far higher rate than the natural heat flow could replace. When the rock the geothermal well is drawing from gets too cool, it's time to drill another well.
The heat resource in deep rocks is vast enough that one can (arguably) ignore the fact that heat mining is not sustainable. A bigger problem is that the only practical way to do it involves creating linked fracture networks between an injection well and an extraction well. The frac'ing operations have an annoying tendency to lubricate any natural faults in the area and trigger earthquakes.
While I liked MacKay's book, and think it is a valuable contribution, sustainable geothermal isn't really a concept we need to embrace. Sustainable geothermal, means we extract the heat slow enough that the small heat flux leaking up from deeper down replenishes any heat we remove. Geothermal isn't used in that way, it is better to consider it as heat mining. Of course heat mining has obvious limits on the resource size, but those limits are actually quite large.
NORM, here = "naturally occurring radioactive material". (Had to look that one up.)
I'll leave it to somebody who knows more about it to give a definitive reply. But uranium oxides are pretty soluble. I'd expect the circulated water to pick up much of whatever was present in the fractured rocks of the geothermal well.
Roger -- this will sound like a bit of a tease but it's essentially true. NORM is something of a joke in the oil patch. We have another more common name for it: dirt. The NORM typically circulated to the surface while drilling is no different than the dirt in your back yard. In fact, depending on where you live, your yard may be a good bit more radioactive. All earth materials generate radiation with the most common being gamma radiation. Take a piece of production equipment covered with NORM (dirt) out of a well and it has to be treated as a hazardous waste. Take the same NORN from your back yard and it's OK for a kid to make mud pies out of it. Granted in rare cases well bore cuttings can be truly "hot" but in 35 years I've never seen it. It's just the nature of some environmental laws. Some years ago I had a environmental audit done on an oil lease I was selling. He found a creosote railroad tie on the lease. Since it was in the official audit I had to have it disposed as per the law. That meant spending $1800 to send it to a certified hazardous waste disposal company. But I could go to the garden store and buy the same piece for $8.95. If I had know the tie was there I would have thrown it in the truck and put it in my backyard. And done some a little more useful with that $1800.
Radioactive is such a loaded term. But technically almost everything around us is radioactive to some degree. want to tease some folks: get your hands on a sensitive Geiger counter and watch their eyes when it starts clicking like crazy when you hold it to their belt buckle. Don't get me wrong: we need good environmental laws to keep folks honest but they can get a little silly at times.
Hmm, looks as though I'm going to have to do another post on current Geothermal operations (see for example the Geysers in California). At the moment the holes don't have to be nearly that deep, since you are tapping into places where igneous rock has penetrated near the surface and so you just have to drill down to it.
Once there the well can tap into natural fractures (which is what they do at the Geysers) or you can hydrofrac the rock. That gets a bit tricky since you then have to intersect that second frac with another well to get a loop for circulation. You need to be some distance from the first well at the point of intersection to get a large enough area of contact with the rock for sufficient heat transfer to the circulating fluid. Then the problem comes in finding the right fracture in the rock at that depth and steering the bit to intersect it at the right place.
I am confused. What do you mean by "geothermal drilling"? How is unaltered, (presumably) isotropic granite going to behave in comparison to a soft sedimentary rock in a high-pressure water-jet? In geothermal terrain, how often are you going to find unaltered granite? What are the alteration products in a hydrothermally altered granite and how will those products affect drilling? where does coal fit in here?
Actually granite is anisotropic (means the properties are different in different directions). If you go and talk to an old quarryman he will tell you that there is a rift, an easy way and a hard way to split granite blocks all at right angles to one another. Without that experience you can find the different directions by looking at changes in the speed with which sound travels through the granite.
Water can actually drill granite quite well, more easily if it is weathered than if it is not, but the large grain sizes make it easy to remove individual crystals and we have drilled it at about 90 ft an hour, as I recall. Our slotting rate in quarries and in carving sculptures is around 20 - 25 sq ft an hour depending on the pressure of the jet, and the contour that you are cutting, and the granite which changes properties and composition as you cut through it.
We haven't yet done much work with really hot granite, but have done studies on pressurized granite, down to the equivalent of 6,000 ft and you need to increase the jet diameter to a minimum of about 0.06 inches as you go down in depth and higher in hole back pressure.
Cutting coal with a waterjet at a pressure of about 10,000 psi is like a hot knife through butter. Most coal mines use higher flows (around 1,000 gpm) and low pressure - maybe 1,500 psi - since the high volume of coal produced can then be carried away by the water in a flume, and the jets can mine back up to 100 ft from the operator of the jet.
There are many isotropic granites. Granite is anisotropic if there is foliation or lineation (alignment of platy or prismatic crystals, like mica or hornblende for example). VAst regions of Main phase Pikes peak granite (geographic giveaway) is isotropic, ie, the physical properties are the same in the x,y and z dimensions. Some granites are isotropic, some are weakly anisotropic, some are strongly anisotropic. AnIsotropy in phaneritic igneous rocks can occur through partial melting, crystal cumulates, flow, contact and relict features. Isotropy is rather common in type A (anorogenic) granites, anisotropy is the rule in type S amd many type I granites.
more http://www.google.com/search?hl=en&q=isotropic+granite&aq=f&oq=&aqi=
megascopically speaking. Radiogenic aphanitic igneous rocks aside, excepting phenocrysts and aligned glomeroblasts, of course.
If there is a strain elipsoid (sigma1 > sigma2 etc - anisotropy) then the drill tip will tend to be deflected normal to the elipsoid, but I could be wrong about that at this late hour. At any rate, additional energy required if you don't want the bit deflected due to anisotropy, obviously.
Bye the way, that block up there in the model assumes isotropy. It does actually simplify the calculations by removing the elipsoid, though.
Grin:
I am actually at the Waterjet Conference in Houston this week, which means I can't reference my slides, but when we were developing the waterjet drills we proved that they are geology insensitive (because the jet drills the hole ahead of the material in the drilling head) by both drilling through rocks we had stacked so that they were inclined to the axis of the hole, and then in an underground mine drilling into and through one hole with another at an intersection angle of about 15 degrees. I have broken drill steels trying to drill that second hole straight with conventional pneumatic drills. (When we put the theater in under the St Louis Arch).
What we did find though was that when drilling into rocks with a stress ellipsoid that the holes drilled were also oval. Where the rock is under high compression the jets find it harder to penetrate and the hole is shallower, where the stress is less the cracks open and let the jets in and they accordingly cut deeper.
Very cool stuff...
I notice the book Waterjetting Technology (referenced with respect to the second photo) is by D. A. Summers. If you are David A. Summers, I suspect there is a connection. Good to have an expert on the subject!
Grin - caught - but lest you think I get rich with the current price of the book, my actual royalty check each year is about $150 - the agreement was signed long ago when the book was a lot cheaper.
Hard data would be useful on the effort required to drill rocks like granite. An unusual piece of theatre is unfolding with granite geothermal
http://www.petratherm.com.au/
Holes are drilled about 4000 metres deep into radioactive granite and the intervening spaces are fractured. Water is pumped down one hole and steam/froth (containing radon) returned to the surface via other holes. An ammonia heat exchanger is supposed to drive generators.
Critics point out that every couple of years as the granite cools new holes will need to be drilled but not too far from the surface generator. I believe the Australian federal government has chipped in $50m towards drilling costs. Therefore we must ask what energy cost of drilling should be deducted from the surface electrical output. Thus over a two year period; electrical output 20 MW X 8760 hours X 2 years = 350,400 Mwh. Drilling effort 4 holes X 4,000 metres X 0.2 Mwh/metre = 3,200 Mwh. That's a tidy energy profit assuming the figures are appropriate. I suspect the problems won't be the drilling costs. For example I think the fracked granite will undergo plastic creep at 200C temperatures.
Hard data would certainly be nice.
I wouldn't think that plastic creep would be a problem at just 200 C and 4000 meters. But I'm no expert. I'd expect, however, that pumping sand into the fractures, same as in oil and gas work, would keep the cracks open for at least as long as the rocks could continue to supply heat.
Just speculating, but one way to reduce drilling costs might be if the same bore holes could be used to support multiple horizontal drilling runs in different levels and in different directions. I don't know if technology for that exists yet.
I think that the need to renew wells is a function of how much heat you extract - relative to the make-up rate of the rock in situ. There are, bear in mind, locations around the world where Geothermal energy has been extracted for decades, so there is a body of practical knowledge to fall back on.
Drilling costs have, in some cases, been the issue of concern, since the cutting teeth of the drilling bits also soften as they get hotter (and that includes diamond).
There is at least one hundred years worth of data concerning hard rock drilling. Are you guys talking about latent heat or geothermal heat? All granites are radioactive. Some are way, WAY easier to drill than others. Altered granite, found in areas of hydrothermal alteration, common in areas of high geothermal gradient is quite soft. Most granite is foliated (not all) and is easier to drill in one direction than the other. How much granite underlies major population centers - granite, not gniess or migmatitic gneiss? ???? Are you sure what you are calling a granite is not a quartz syenite or a monzonite? The physical and chemical properties differ greatly between felsic igneous rocks, often by alot. Show me where there is a pile of "granite" 4000 meters thick, you'll be drilling through many rock types and they b-have very differently.
I believe the rock there is a granodiorite containing pitchblende. Alluvial outwash from the hills is mined nearby using in situ leaching at a place called Beverley. In other places the Proterozoic granite is overlain by Cretaceous sandstone which has trapped the heat.
Funny how nuke opponents think this is OK but controlled fission reactors are not.
Most nuke opponents worry about long term effects of nuclear wastes and the consequences of improper disposal. Perhaps a bit more knowledge and familiarity with the workings of ancient natural nuclear reactors like the ones discovered in Oklo would help put them more at ease.
http://www.scientificamerican.com/article.cfm?id=ancient-nuclear-reactor...
Last week I saw a program about using a heat drill. There was no drill bit as such, just a blast of very high temperature to bore through the rock. It looked very promising, but I have no idea how far off this technology is. If anybody knows more...
This may have been the Potter drill, which uses high temperatures. But there have been a number of different thermal methods proposed and a review of some of these is going to be part of my next post in this series.
HeadingOut, a couple of questions about your contention that the Potters are on the wrong track because their system produces powered rock fragments rather than larger (more efficient) chips. 1- Drilling residue has to be removed from the borehole. Isn't chip size limited by this factor when doing deep drilling? 2- If the Potter system achieves hard rock drilling rates several times faster than conventional drilling, does this not represent a revolutionary improvement? 3- It would seem that drilling cost per foot could be lower than rotary bit technology, and horizontal drilling facilitated?
Since you have done pioneering work in the field, you are the right person to ask!
When you research and write your post on conventional geothermal you might want to look at the Laurence Livermore work on hydrogen isotope mapping for identifying underground fracture systems.
What are they drilling through?
You are right that you can offset higher drilling costs with an increase rate of penetration. The Flowdril system that I referenced in an earlier post, for example, needed to achieve a gain of around 2.8 times conventional, as I recall, but though it reached 4 times on occasion, sustainably it seemed only able to achieve around 2.4 and is no longer with us.
In regard to what I put into the next Geothermal post, part of my problem is that I have several feet of reports on earlier work and trying to condense some of that down to 1-2,000 words and keep it interesting yet simple enough to follow means I can't put too much into any one post. (But then there will be others).
Potter proposes drilling through a pile of sedimentary rocks to get at the basement rocks. According to this, cost advantages arent seen in drilling until "granite" is reached at depths of 4000 meters +.
http://www.potterdrilling.com/wordpress/wp-content/themes/wpremix2/image...
The HDR/EGS real-costs actually don't look so good. Also, note the line showing parabolic increase in costs is largely based on ultra deep drilling in non-igneous rocks.
A couple more general questions regarding EGS:
1) Is the hot water flashed? Is there a weirbox?
2) Are there any problems with scale/mineral deposits?
3) Injecting water into hot/warm rocks creates an essentially artificial hydrothermal system. What happens to the feldspars adjacent to the fractures/exposed to the hot water? Is clay/sericite sealing of fractures ever a problem? Eventually, over time, will the formation of clays from hydrothermally altered feldspars seal the fractures? Will silica throttling be a problem with time?
4) whats the (real) lifespan of one of these wells?
The application of heat spallation of hard rock in mining is ancient. See "Fire-setting" and "ancient mining techniques" for more on that.
"Zero emmissions"? Really?:
http://www.geodynamics.com.au/
http://www.geodynamics.com.au/IRM/Company/ShowPage.aspx?CPID=1864&EID=10... (page2)
These power plants are essentially in the middle of NOWHERE.
If you want to see a really different way of combining fire and water in mining, you should look up how the Romans mined gold at Las Medulas in Spain. (Pliny wrote about it).
The Beverley ISL uranium mine on the flat plain
http://www.heathgateresources.com.au/homepage.jsp?xcid=1
is supposed to be powered by geothermal electricity from the Petratherm setup on the hills nearby. Whether the granite in the well disintegrates or dissolves I can't say. The Geodynamics well is about 200km away and was supposed to light up an outback town last year but is experiencing repeat glitches like steam leaks. That steam contains radon. Also topping up water is scarce.
As of now I don't think granite geothermal is going to provide baseload.
A random article I saw in Oil and Gas Journal http://www.scandoil.com/moxie-bm2/news/spot_news/discoverer-clear-leader... Discoverer Clear Leader starts deepwater quest
That looks like a pretty deep drilling project, 8.55 km under the seafloor. Is there any reason the technology they're using couldn't serve for geothermal?
The simple answer is that the basic technology, either roller cone or diamond drill bits is the same. However these are likely to be straight vertical holes to detect whether there is enough oil/gas in a deposit to be economical. In geothermal you will be generally drilling more deviated wells in the deeper deposits to get the areal surface for high heat transfer if you are fracing hot dry rock. If you are tapping geothermal fluids you would probably be much shallower.
HO,
A general question this time.
Is this technology,in your opinion, now good enough that geothermal will be cost competitive any time soon other than in the very best spots?
And do you plan at some point to cover the earth quake issue?
It really suprises me that it apparently takes so little to set one off.Maybe the early experimenters have been unusually unlucky in selecting sites that are prone.Or maybe the whole world,at those depths and in that kind of rock, is like a bango string ready to break at one more touch or a sheet of glass stressed so hard it's ready to shatter.????
My guess is that it's too early to tell.?
With this post, I can improve my knowledge. I am waiting for your next article.
Thanks and Regard
__________________
custom made golf clubs | custom built golf clubs | custom golf clubs