Tech Talk: SAGD and Well Production from Oil Sands
Posted by Heading Out on January 24, 2010 - 11:15am
This is a technical post relating to the production of oil from heavy sand deposits, such as those in Alberta. It is a part of an ongoing series of tech talks, and should probably be read after the post last week on surface mining of those deposits. It is simplified, and relatively short, and so there are some details that are abbreviated, but longer answers can be provided through comments.
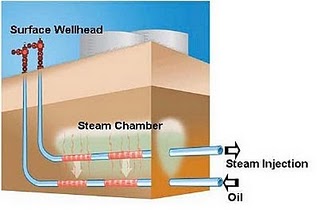
Surface mining of oil sand can only progress so far before the gradually deepening seams of the sand become too deep to continue to economically mine them. At the same time the viscosity of the oil is such that it does not flow easily to a conventional type of a well. This is not a new problem for the oil industry, which has had to address issues with the quality of the oil that it finds coming out of a well more than once over the past decades. One of the more easily applicable methods for improving the flow characteristics of the oil is through heating it. (And a quick caveat, the quantities of heat that I am talking about at the moment are significantly different from those that are needed in treating oil shale. I will come to that topic in a couple or three weeks.)
The example of the effect that temperature makes on the ease with which a fluid flows that always first comes to my mind is of a visit to the Nurse’s cabin north of Montreal one winter, a long time ago, when after struggling through waist-high snow, we sat and poured whisky from a bottle left there, as we waited for the wood stove to heat the cabin. When we started the Scotch poured as though it was a heavy syrup.
Viscocity of an oil is something that we usually only think about when we buy the engine oil that we put into the car on odd occasion. Buying the right oil means either looking for the little label that has the right description or reading the manual to get the number. But the oil that we buy for the engine is rated in part on how it behaves at different temperatures. We want the oil in the engine to easily circulate around the parts, and lubricate them from the time that we switch the engine on. But if the engine starts cold, and the oil is too thick, then it may not move easily around the parts, which may run dry for a while and wear more rapidly – which is not good. However if the oil becomes too thin once the engine reaches operating temperature then it doesn’t act as a good lubricant, and again engine wear is increased. And so manufacturers of the oil will adjust the contents, depending where in the country they plan on selling the oil, and what the temperature variations the oil can expect to operate under there. (And this is why oil is sometimes bought with two numbers – as in 10W-30 – the first number relates to the cold start, and the latter the performance at the engine operating temperature. And the higher the number the more viscose the oil is under those conditions.)
A typical oil found up in the oil sands of Alberta is much thicker, and more difficult to flow under normal operating conditions than that used in a car. For the areas of the province that are too deep for surface mining the temperature is not affected much by the changes in surface temperature, but the ground temperature is still low enough that the oil is very viscose, and production from a normal vertical well is usually too slow to justify the expense of putting in a well.
So how can the viscocity be reduced? For a simple example, take an apple, which has fallen in the butter, and you want to clean it off. If you take the apple and put it under a cold stream of water the butter sticks to the apple, but if you raise the water temperature, suddenly the butter melts and runs off the apple. This happens best at about 185 deg F, and if you were to turn a pressure washer onto a greasy surface you would find that it works better if the water is also heated above that temperature. (Some pressure washers are sold that way).
Think now, if you will, of little Johnnie (helped of course by Jessica) having raided the orchard and spread butter onto all the apples, gluing them together and filling the kitchen full, right to the ceiling. How do we clean the butter off and get it back without taking all the apples out and cleaning them one by one (which is sort of what they do with the surface mined oil sand up in Canada).
We could just stand in the hall and stick heaters up against the wall of apples, hoping that the heat would melt the butter and work its way back to the ones further into the kitchen. That sort of works, but burns the local apples and doesn't reach all that far. (They have tried setting fires inside oil wells, and we’ll get to that maybe next week). You could fill the kitchen with hot water, but while that washes out some of the butter, a lot of the heat goes into the apples and the water is cold before it reaches the back of the room. And the water doesn't have that much pressure to push the remaining butter off the apples.
What we need is something that will get through the gaps between the apples and keep its heat. So how about steam? So you go and get a steam cleaner (such as you use for carpet cleaning) and blow the steam into the apples. That works but as the butter starts to flow out it clogs the gaps and starts to re-harden except when the steam is right there. So you start to run the steam for a bit, stop and collect the butter that comes out, run the steam for a bit, etc. You can do this in an oil well and it has the exciting technical name of "Huff and Puff" (would I kid you?). To make the steam more effective it is heated to between 150 and 300 deg C. Where the rock is very permeable and the steam can, in time, work its way back through the particles (apples) this can recover a lot of our butter. But you still lose a lot of heat, which is expensive to generate, just in heating the apples.
The NETL shows how the process works, in three steps:
.jpg)
.jpg)
.jpg)
- The 3 stages of the process as illustrated by NETL.
The problem is that this is still limited by the length of the borehole through the deposit, and because it is an intermittent process, it doesn’t give a continuous flow of oil.
However, with the advent of directional and horizontal well drilling, the first part of that problem can be solved, and a longer hole can be drilled into the sand to give a higher exposure to the steam being fed in.
Then, to allow a continuous supply of steam into the sand, a second well can be drilled so that the steam is constantly flowing out of the one (upper ) well into the oil sand, and as the steam reduces the viscocity of the oil, so it flows easily into the lower well which can then capture it and carry it to the surface. Because the steam is cooled to water during the process, this is also recovered with the heavy oil, and is then separated from it. In some cases, as I mentioned last time, there is also some natural gas in the formation and this is also recovered and separated. It is often used to heat the water (as much of which as possible will be that reclaimed from the steam) to feed it back into the process.
.jpg)
The entire process is called Steam Assisted Gravity Drainage (SAGD – pronounced Sag-D) and over a 30-year period has become the popular method for getting the deeper oil from the oil sand. Just this week, for example, Alberta Oilsands Inc. has filed an application to install a set of 6 paired wells at a site that is a mile from Fort McMurray Airport. The six sets of wells will produce some 4,500 bd. The lower well runs along the base of the formation, while the steam injection well is located above it, and about half way down the formation depth. (It should be noted that the application is also considering a later use of electro-magnetic heating).
Typically several sets of wells are laid out beside each other to provide an interaction between the wells and heat the intervening oil so that it can be recovered. For example, this layout is taken from the application of Devon Canada Corporation for an expansion of their Jackfish project to produce an additional 35,000 bd. Notice, in the layout below, the close pattern of the parallel well sites.
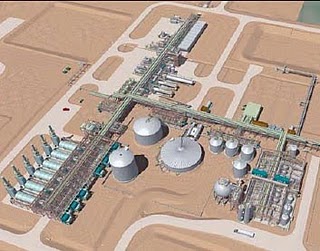
There have been a number of different posts at The Oil Drum about SAG-D over the years. Dave Cohen wrote about some of problems as seen in 2006, particularly as they related to the problem of natural gas supply for, among other uses, heating the water to steam.
But I’ll return to the issue of adding heat to oil sands, and then get on to oil shales in the weeks ahead.
With regard to tar sands production by SAGD versus mining of the sand, what is the recovery factor of SAGD? Mining of tar sands gives nearly 100% recovery, but EROEI may be less than SAGD.
Also, the reader should note that the hydrocarbon being obtained in the Alberta tar sands is "bitumen" which must be converted to a lower viscosity "oil" to be pumped in a pipeline and then refined.
The difference between bitumen and extra-heavy oil is somewhat arbitrary - mostly because it determines royalty rates (which are very low for bitumen). The Alberta government has a pre-defined oil sands area, and if a company finds heavy oil in that area, they deem it to be bitumen for royalty calculations.
The difference between oil and bitumen is mainly determined by viscosity, but that also depends on formation temperature. If a formation is hot, the oil will come out of the ground on its own and be considered to be heavy oil (although the tanks will have to be heated to keep the oil from turning solid). If a formation is cooler, it will have to be steamed out and will be considered to be bitumen. Reservoir temperature is one of the main differences between Venezuelan "extra-heavy oil" and Canadian "bitumen" reserves. The Venezuelan oil is also somewhat less viscous, but if it was in Canada it would be pretty solid stuff, too.
Historically, all the oil sands operations had their own upgraders, but now many sell bitumen as is. They can move bitumen through pipelines by heating it or diluting it with lighter liquids - usually natural gas liquids. Historically, there were lots of NGLs available from gas wells in the area, but as the nearby gas fields are depleting, companies are having to become more creative.
The big refineries near Edmonton (which have most of the refining capacity in Western Canada) are close enough that heating the oil is a viable solution. For more distant refineries, they have to use diluent. An upgrader is just the front-end of a heavy oil refinery, so most of the bitumen for export is upgraded to syncrude before it goes into the pipeline, while most big Edmonton-area refineries and some Mid-Western US refineries can handle bitumen directly. The way things are going it will not be long before Texas Gulf Coast refineries will be processing raw bitumen, too.
EROI of mining seems to be a somewhat better than SAGD, from what I can see, but the operators are working at getting the EROI of both up (so costs of mining/extraction go down).
The Surmont facility I visited (see this post) used SAGD, and got a 60% recovery. They have recently announced expansion, so one would think that they consider the current price high enough to support their costs.
What you say about the bitumen needed to be converted to lower viscosity "oil" to be pumped in a pipeline and then refined isn't quite true. It is true that that is what is done with mined bitumen (which Dave talked about last time), but that is not what is done with bitumen from SAGD. The SAGD bitumen produced at Surmont is mixed with upgraded bitumen (from other oil sands production), and the resulting mixture sent through the pipeline, to be refined. The upgraded oil purchased as a diluent is quite light, and mixing the bitumen with it produces a heavier grade oil.
It is also possible to ship bitumen by rail. It doesn't need to be upgraded for this process.
Heavy oil in California (Kern River) is also too heavy to go through a normal pipeline. The approach used there is to heat the pipeline.
So there are several approaches, and the problem isn't unique to bitumen.
They may build a diluent pipeline from the refinery to the tar patch and bring the lighter diluent-bitumen blend back to the refinery, seperate out the diluent and start the cycle over again.
That may be one approach, with a different diluent--I don't know.
With the oil from upgraded bitumen as diluent, the process is to make a 50% - 50% mixture of the bitumen and the purchased previously upgraded bitumen. The new mixture is called "Western Canada Select Blend". It is a standard type of petroleum purchased by refineries.
Just wanted to add some tar sand factoids.
The recovery rate for tar sands mining is 75%.
2 tons of mined sands produces 1 ton of 'bitumen'.
The recovery rate for SAGD is 60% of the original oil in place.
Huff and Puff recovers only 20% of OOIP.
The EROI of tar sands extraction plus upgrading is 5-6 and is expected to rise to 9 by 2015.
Alberta tar sands has at least 1700 Gb of OOIP with an expected recovery rate of 10%(which could be low).
Alberta tar sands production is only 1.3 mbpd(2008).
http://en.wikipedia.org/wiki/Oil_sands
I'll add another thing to that list, which wasn't really touched on in this article. SAGD has far, far less impact on the surface environment than does "mining" I couldn't find any figure of land disturbed per barrel recovered, but it has to be much less than surface mining. You also don't need massive tailing ponds, etc, etc.
Given that most of the new oilsands projects are in situ rather than mining, I hope the hype about environmental destruction will get a dose of reality
Only about 10% of the oil sands area is suitable for mining. The other 90% will have to be produced using in-situ techniques. SAGD projects usually reduce the amount of land required for the wellheads by drilling 10 or 20 wells directionally off each gravel pad.
I think SAGD disturbs less than 10% of the surface area, and of course it is much easier to remove the gravel pads and reclaim the surface area they occupied than to reclaim an open-pit mine.
I have been reading all of these comments with much enthusiasm, and all of the points are well taken and placed. I have been working in the Fort McMurray area now for over 8 years and have been in Open mine and SAGD operations. Which is better I can not really answer that question, but my preference is SAGD, it is a Smaller footprint, does not disturb the fauna and flora as much, the one downfall is the amount of water that is required, but with the scientist and environmentalists working together they are discovering new ways to reduce the amount of water used.
I have been reading and talking to engineers about some of the new research being investigated on how to extract the Bitumen, for example electricity, chemical injection, remining the tailing sands to extract any left over bitumen and heavy metals i.e. titanium, so the research continues and thankfully it is all with the environment foremost.
I know that with the new advances in the Oil Sands it will keep all of us employed and keep our vehicles running for a long time, and also spur new research and findings to refine the bitumen and drive to a new more environmentally friendly Oil Sands.
Gary
OilSandSafetyGuy
Master Affiliate Marketing Now
There are new chemical injectants that can be used with SAGD to substantially increase recovery rates.
One chemical nanotechnology being tested for downhole EOR is EncapSol, which is proving to be quite effective in releasing stranded heavy oil from the sand, clay, rocks and water that usually bind it.
This video blows my mind -- it releases bitumen from oil sands in ice-water!
www.EncapSol.com/media
This is the best solution I have found -- and anyone who does their homework should agree that these kind of solvents may help us recover more oil/bitumen than without.
It's fake. Someone has been posting "adverts" about it here in a couple of threads, but most people here pretty much disregard it. I'm guessing that you might be that someone cos you registered just a few minutes ago.
Besides, if it's for real, why are they not using it already? There must be something about it which makes it unsuitable for industrial use on a large scale. Sell the product to one of the big oil sands producers and then let us know how it works out!!!
I don't know anything about this procedure, but it takes time to get all of the "kinks" worked out of new processes and get them scaled up to commercial level.
The fact that one process doesn't work ideally doesn't mean that another process won't work better. The situation has been one of gradually improving processes, and I would expect that trend to continue.
What a hater you are -- calling something fake when you haven't even researched it -- I'm doing my due diligence and from the people getting involved in this technology -- it is a very real and very exciting breakthrough despite your skepticism.
What if Encapsol technology really works? But if people like you criticize it and slander it as being fake -- you may scare people away from something that can really help America recover more of it oil. That would be a shame, but par for the course, I guess, in corporate America.
But this looks real to me and so does the scaled up machinery that demonstrates the extraction of bitumen from Utah tar sands without using any water or natural gas. No water? No natural gas? No effluent tailing bond emissions?
That is revolutionary unto itself and could solve all the environmental problems that prevent America from harnessing its vast tar sand and oil shale resources.
I hope every responsible geologist or oil industry executive actually spends a little time to investigate this Encapsol technology -- and then form an opinion about its effectivness based on facts not self-interests.
"I hope every responsible geologist or oil industry executive actually spends a little time to investigate this Encapsol technology -- and then form an opinion about its effectivness based on facts not self-interests."
That sounds like a monumental waste of their time. If this process is everything you claim it to be, then, like anything else, let it prove itself in the field, under real world conditions and constraints. If it is truly that much better, then you can be sure the companies that make their living from oil extraction will be looking at it - regardless of whether you, or anyone else, hypes it.
The more something is "marketed", the more suspicious we engineers get.
what utah tar sands are you talking about ? what is the location ? what county ?
Utah does in fact have oil sands, but they are smaller and more difficult to extract the oil from than the Canadian oil sands.
The main difference is that, while oil can be separated from the Canadian sands using a simple hot-water process (the original experiments used an old washing machine), the Utah sands require a more sophisticated technique (which hasn't been perfected yet.)
According to the EncapSol website, they own a tar sands property in Utah and have used their technology on an R&D basis to extract bitumen from Utah tar sands using their DRY process.
See the video of actual equipment operating at www.encapsol.com/tar-sands-and-oil-shale-extraction/
Note this is being done -- using no water, no steam, no natural gas, producing no liquid tailing waste -- yet producing bitumen plus cleaned sand/gravel.
I don't know why the Canadian oil sands industry isn't embracing this technology yet - maybe it's just new and people are just starting to learn about it being available in the first place -- but that doesn't mean it isn't worthy. It just means its new.
But from the looks of what this Encapsol solution can do -- it is certainly worthy of investigation by the industry which has the most to gain from its use.
If this can extract bitumen from rocks in an environmentally positive way without wasting water, natural gas or creating toxic tailing ponds like is being done now -- why shouldn't this technology, or others like it, be used?
Adding chemicals to the injected steam is one thing that can be done to increase the recovery rate.
However, there is a trade-off between the cost of the chemicals and the additional oil recovered. SAGD is already extremely efficient and recovers 60%+ of the oil in place, versus half that for most conventional oil recovery. the trade-off tends not to be very favorable given the already high recovery rate.
What companies are investigating is using chemicals to reduce the amount of steam required to produce a given amount of oil. This could be useful reduction, since generating steam is a major cost of the operation.
Given the density and fire-retardant properties, this has to be carbon tetrachloride, perchloroethane, or similar organochlorine. The toxicity of such material after entering the water and food web would be permanent and devastating.
There is no way this will be allowed, even in Alberta. Are these people for real, or just looking for gullible investors?
Don't get carried away.
The usual solvent for vapex is propane(NGL).
http://www.encyclopedia.com/doc/1P3-357036471.html
http://www.rigzone.com/training/heavyoil/insight.asp?i_id=186
Did you read the link? This is definitely not propane.
You're talking about two different things.
The Vapex process, which has actually been used in the oil sands, involves co-injecting solvents such as propane with the steam to improve its efficiency, or replacing steam with solvents. The solvents are simple hydrocarbons.
The dudes in the video won't tell anybody what they are using, but it is probably more useful for putting out fires or killing insects than producing oil.
Why does everyone speculate about what EncapSol is -- when you can just go to the www.Encapsol.com website and immediately see that your claims of toxicity are absolutely refuted by information provided by the company which promotes Encapsol as being NON-TOXIC.
In fact, they posted a copy of a Fish Bio-Assay test required under California environmental laws that demonstrated Encapsol as NOT being hazardous because 100% of the fish exposed to Encapsol lived.
Why do so many people on this site feel they have to denigrate promising technologies that can help us without even knowing what they are talking about?
America needs new domestic energy solutions -- whether it is EncapSol or something else -- we need to try everything possible to extract more oil out of the ground right here at home in America -- or else we are going to suffer severely in the near future when global population demand for oil exceeds current production supply.
That day is fast approaching -- hopefully EncapSol and other technologies can help us in time.
So, these people won't say what their product is, there is no patent, no peer-reviewed literature, no staff or advisors who are willing to be named on the website, but we are wrong to doubt their claims?
Are they going to use SAGD for heavy oil in Venezuela as well? Will the recovery factor there be higher than in Canada?
Wouldn't low temperature steam production by solar thermal be a natural here? The price per BTU of low grade solar thermal is several times lower than the price of solar thermal electricity, and it would allow you to substantially increase EROEI. At that lattitude, it is probably only good for about half the year, but it could be used either for intermittient use, or to offset NG use during the season when insolation is good.
Possible, but probably not scalable. They'll probably be burning some of their oil/NG to make the steam.
shox/EOS --They've actually been using various forms of thermal recovery for many decades in VZ. In addition to Huff&Puff they would use a poor man's gravity assist by injecting (down the casing) steam or hot water into the top of a thick reservoir and produce the oil up the tubing inside the casing. Often this would recover oil from just a few tens of acres around the well but it was cheap: didn't have to drill those pricey horizontal wells. The process made money when oil prices were high enough but the per well volume was very small...along the lines of tens of bbl /day. But multiply that by many hundreds of wells and it begins to look substantial. But if oil prices are high enough to justify horizontal redevlopment those numbers could be multipied many times
As far as energy sources they would often use the crappy oil to fire the boilers. You can imagine without any pollution controls how much nasty stuff got pumped into the atmosphere by this process.
The thing about North America is that companies have become very good at drilling large numbers of horizontal wells very cheaply.
In fact, that accounts for much of the success of the SAGD system. The original concept involved sinking a vertical mineshaft to the formation, and then drilling pairs of horizontal shafts off the main shaft in all directions. However, oil drillers came along and said, "Hey, we could drill horizontal wells from the surface a lot cheaper than that!"
It's gotten to the point that oil company executives have said that it would be hard to justify drilling a vertical well any more. The better production from a horizontal well usually more than justifies the cost.
They're quite accurate at doing it, too. They can drill a pair of horizontal wells ten feet apart for miles if they want to. This controlled drilling is another reason SAGD works so well.
I doubt that Venezuela is nearly as good at drilling horizontal wells.
Rocky -- I enjoy horizontal geosteering more than any other activity. It's the only time many drillers/engineers will pay attention to what a geologist has to say. Just love a captive audience!!! Bet you and I could put a drill bit through a car window at 5 miles. True story: a few years ago while drilling a hz well offshore Africa for ExxonMobil the DD (directional driller) came into the company man's office with a worried look on her face. She said we were off track by 8' to the right and 10' low (the target circle was 200' wide...she didn't know that). And this was about two miles out. Coman told the DD to just make a course correction as best as she could. She left and we began laughing. Probably like you when we started all those decades ago we were pleased if we got within 1000' of the target. Didn't tell her that. You know the very old saying: Aim small...miss small.
i'm paying attention and i actually want to hear what you have to say:
it seems to me that steering in hard rock such as the middle bakken dolomite is a lot more difficult. the wells want to dolphin, sometimes out of zone. the operators want to get the well drilled as fast as possible so they can perpetrate flashy power point presentations (pfppp) showing how much they have reduced drilling time. another problem with the bakken play is an economic necessity of drilling ever longer laterals, in some cases they encounter a fault and dont know where the he11 they are ! i know it ain't easy.
and, i think i have been exposed to mugambo acronym disorder (mad).
elwood -- the hard rocks can be much more difficult to steer in. I did 4 hz wells in Wyo in a very hard sandstone. Very difficult to make the bit go where I wanted it to. Fortunately I had a big window (40'). The rock mechanics were unpredictable. I would try to build angle at 12 degrees/100' and it would drop angle at 6 degrees/100'. The worst experience I've had was trying to stay in a 3' coal bed for El Paso. First hz coal bed methane well in the Alabama. I was screwed the minute I kicked off. Suppose to be drilling at a down angle to stay in the coal. The geologist's mapping was completely backwards: the bed was dipping upwards. Should have been a snap: I was drilling from one vert well to another. But he missed a fault between the two wells. Damn geologists! Had to do about 6 side tracks. They wanted 1200' in the coal bed. I got about 800'. All things considered they were happy with what we did get.
I know. It's remarkable what they can do. The modern technology changes the economics of a lot of things, shale gas being another example.
Nowadays, rather than arguing with government agencies and environmentalists about damage to a riverbed caused by putting a pipeline through it, companies just drill a horizontal well under the river and connect the pipeline at both ends. Makes the paperwork a lot simpler.
Interesting solution to a sticky problem. Would you happen to have a specific example of a horizontal well river transitting with the final projected cost per barrel differential using that method compared with a more traditional above ground pipeline? Projected per barrel cost with and without paperwork delays (if possible) would be instructional. Maintenance and security issues must also differ with the two methods. If the difference in cost per barrel (for all barrels that will ever make the crossing) is insignificant I know I would far prefer my oil to transit under a river than over it, it is just a much more predictable and stable environment.
I don't have any specific examples. It's just that one of my nephews was doing it, and he said it was quicker and cheaper than complying with all the environmental regulations. Modern environmental laws really stretch out the time frame and increase the costs when you have to deal with a natural fish habitat.
I've seen some of that fish habitat stuff. Even with something as inert as small amounts of concrete slurry you have to be darned careful if any kind of drainage is nearby. It can be a pain but often times the thought and effort used to avoid a paperwork blizzard do yield a more respectable end result than would have been obtained if such paper obstacles didn't need to be avoided (my experience is limited to temporary construction stuff that doesn't need the massive permitting of an oil project). It can be a real show stopper if you cross with the environmental boys anytime during the game. Unfortunately some them are far more interested in protecting their bureaucratic turf than the ecosystems they are supposed to be watching over.
I imagine you are talking about fairly small diameter feeder lines, any idea how big of a bore is feasible with this tunneling method? TAPS is pretty much my neighbor and it goes from above ground to buried within a mile of my house--permafrost considerations--but that is a 48" pipe. It would seem straight up and down shafts into the rock might avoid a lot of the issues permafrost poses for constructing warm pipelines. Just a thought, I'm guessing both TransCanada and Denali are doing pipeline/permafrost engineering studies right now for the 'maybe someday before I die' gas line to the slope.
Well bores usually range from 5 to 36 inches in diameter, but I don't think anything precludes you from making them smaller or larger. I'm sure if you wanted to drill a 48 inch horizontal well, some company would be willing to do it for you.
In permafrost, the trick is to avoid melting the permafrost, which is why the trans-Alaska oil pipeline is largely above ground. Heat rising from a warm pipeline would make the ground unstable.
However, for a gas pipeline, they would just chill the gas below the freezing point to prevent the pipeline from melting the permafrost. Oil would become too thick to move at these temperatures, but natural gas doesn't condense to a liquid until around −160 °C (−260 °F).
I wondered about how cold they could have the gas and still move it, thanks. I figured the sheer mass of the oil in a 48" pipe made TAPS a whole differenct game than a 48" gas line anyway (I'm sure the pressure in gasline is whole lot higher though). I guess the gas treatment plant Denali is talking for the slope would be the biggest on the planet to date. It will provide the initial chilling. It looks like compressors are planned for every 150 to 200 miles of pipe, I'm guessing they will have additional chilling equipment at those sites, or wouldn't that be necessary?
Back on TAPS I think they were a little more worried about the warm oil pipe radiating heat to the permafrost below the pipe than above it ?- ) but then a sunken trench above the pipeline wouldn't have been too desireable either. I think the section through a Atigun pass is refrigerated. The pipe had to be buried there because of the avalanche hazard but the ground around it needed to remain stable, which of course is frozen in those parts. That must be a spendy little section to keep maintained.
Speaking of pipes I got a few sections of ABS to glue together to ready this place for a decent sized jacuzzi tub, should be a nice touch to have around after a couple of hours skiing in the -10 to -20F. Cross country isn't too pure a skate endevour at those temps
?- ) Three score old bodies like a little pampering.
Orinoco extra-heavy(10,000 cp- like chocolate syrup, 3.5% sulfur) is different than tar sands bitumen.
The resource is +500 Gb.
It is mainly produced by cold pumping(CHOPS) with progressive cavity pumps. Recovery rates for CHOPS is 8% of OOIP.
The recovery rate for thermal systems is ~ 50%.
Then the extraheavy is diluted with light crude oil for transport. PDVSA is moving away from injecting diluents and isn't using heat much anymore.
http://www.slb.com/media/services/solutions/reservoir/200811_ep_venezuel...
http://www.slb.com/media/services/resources/articles/heavyoil/200801_ao_...
Indonesia uses thermal recovery at the old Duri field in Sumatra.
IIRC, the heavy oil in Venezuela is different than in Canada.
In Canada, there is a layer of water around each grain of sand, and the bitumen is outside the water. That makes the bitumen easy to separate. I don't think that is true in Venezuela.
I think that technically, the SAGD process would work perfectly well in Venezuela.
The problems are political in nature. Venezuela does not have the technology. Canadian companies have the technology, but Venezuela is not a favorable environment for foreign companies. It is also not a favorable environment for foreign capital, and SAGD is a very capital-intensive process.
In theory, Venezuela could develop the technology on its own, but a few years ago it fired most of the people in its research center, including all of the PhDs, in a political dispute. Many of Venezuela's former heavy oil experts are now working in the Canadian oil sands.
Rocky -- As you know they can import that technology anytime they want. Granted they'll have to prepay Schlumberger or Halliburton up front given their history. There has to be a lot of untapped potential. Even with conventional reservoirs. Even 15 years ago a company (Bennington?) took a concession on a field making less than 400 bopd. Within a few years using hz wells they upped production to 40,000 bopd. They could have ramped it up even higher but the concession agreement gave 100% of production above 40,000 bopd to the gov't. How behind the times were Vz production ops at that time? Bennington showed pictures of the oil tanks the field was producing into. They were unlined earthen pits. Pretty much a 100 year old production technique.
Who knows how much Vz or Mexico could bring to the market if they utilized current technology. Probably not as much as folks are speculating about Iraq but who knows?
Well, they could do it in theory, but first, there is the problem of politics, and second there is the problem of economics.
The politics of Venezuela or Mexico don't allow them to do the efficient thing. It would be more efficient to just put it out for bids and take the best one, but they don't do it that way. The state oil companies (PDVSA and PEMEX) are first and foremost, cash cows for the government, and second, places that provide jobs for political favorites. Producing oil efficiently ranks low on their list of priorities.
Economically these companies are overstaffed, underqualified, and undermotivated. They can't do small things cheaply. Something like SAGD requires drilling a lot of technologically sophisticated wells as cheaply as possible. PDVSA and PEMEX are good at drilling a small number of simple wells very expensively. That's not going to work very well in a mature oil area. The oil is there but not the aggressive independent oil companies that could produce it.
Venezuela doesn't have the technological expertise to do SAGD on its own, it's not going to condescend to let some foreign company do it instead, and it's not willing or able to commit the cash up front to build the necessary infrastructure. Other than that it would have no problem producing large amounts of oil from its Orinoco oil sands.
In the final analysis, Venezuela has more oil than Iraq, but not the political system or economic capital to produce it.
Even with SAGD, it would be quite slow to extract the bitumen, and the cost of the process would tend to make the oil produced high-priced oil. Unless world oil prices were fairly high, it probably wouldn't be worth doing--the same problem Canada is running into. Also, there is a fairly high front-end cost of the first the research, and then drilling the technologically sophisticated well. This would need to be paid, before any oil was actually produced.
EIA says about 600 kb/d from Orinoco heavy oil. Production has gone sharply down for 2009, is that them obeying quotas, or fallout from Hugo seizing foreign oil companies' assets? I guess the former since there's nothing in the news about the latter.
BBC News - Venezuela oil 'may double Saudi Arabia' says the new USGS estimate is based on 45% recovery, that would be SAGD etc by definition, right? I don't pay attention to these revisions since they're basically revising from peak to mountain; this 2002 Rice University doc says that the overall size of the Orinoco has been known since the first formal study in 1967; they even exported a barrel of oil in the 16th century! For the king, medicinal purposes. The techniques for mass extraction have been around since the 50s at least.
re:EIA says about 600 kb/d from Orinoco heavy oil. Production has gone sharply down for 2009
I don't believe Orinoco heavy oil is subject to quotas. I think the oil production is falling because their infrastructure is worn out and they can't afford new wells or new equipment. Chavez is using PDVSA as a cash cow and spending all the money on his other adventures.
re: BBC News - Venezuela oil 'may double Saudi Arabia' says the new USGS estimate is based on 45% recovery, that would be SAGD etc by definition, right?
Yes, you could get those kind of recovery rates from SAGD, but did you read the part in the article that said:
The usual definition of "proven reserves" is oil that can be produced using current technology under current economic conditions. Using current Venezuelan technology under current Venezuelan economic conditions, they can't get 45% recover, and per the quote, 25% is unlikely.
So, if they had Canadian economic conditions and technical expertise, and they used SAGD, and pigs could fly, they could get 45% recovery and produce 513 billion barrels over the next millennium or two, if production didn't keep falling.
Honestly, I think the USGS has lost contact with the world we live in and are doing their estimates in some kind of alternate universe. These unrealistic "if pigs could fly" kind of numbers are only useful for confusing people who don't know what they are talking about. Which may be their goal. Or maybe somebody needs big numbers to justify an invasion plan. Who knows?
No kidding the research is expensive. It cost the Alberta government around $1 billion to develop the SAGD process, not including time and money contributed by the oil companies.
But, overall, it was not a bad investment. The total value of the oil reserves added, say 170 billion barrels at, say $80/bbl would be $13.6 trillion.
Now, most of that money will end up in the hands of companies, but if Alberta ekes out a 1% royalty, that would still be $136 billion dollars, a net profit of $135 billion. Unfortunately, that's over then next 400 years, but it's nice to know that the government will have a nice steady stream of income to pay for our great-great-great grandchildren's education.
If the people of Canada can't manage a better than one percent royalty I might just have found my niche-I'll go up there and help start a socialist revolution.;)
Does anybody here know something about the amount the provinces or local govt collects taxes on oil and/or the oil industry in Canada and how big a bite they get?
Actually, Alberta has sliding-scale royalties. Oil sands royalty rates go as low as 1% and as high as 9% of gross revenues.
If the price of West Texas Intermediate is $55 or lower, the royalty rate is 1%; if WTI is $120 or higher, the royalty rate is 9%. Which do you think is more likely in the long term?
It's actually much more complicated than that. They use different rates for pre-payout, post-payout, gross revenues, and net revenues, and companies have to figure it out using a complex formula. Here's a link to their oil sands royalty site: http://www.energy.gov.ab.ca/OilSands/584.asp
Royalties on conventional oil are higher but similarly complicated, and go from 0% to 50%. If well production is low and WTI is low, the rate may be 0%; if it is a high-production well and WTI is high, it may be 50%.
It reduces oil company risk, but means Alberta government revenues are highly volatile. When the oil price were $30 in early 2009, the government was making more money from casinos than royalties; when it was $147 in mid-2008, they didn't know what to do with all the money they made. So they paid off all their debts. That was the smart thing to do - go into a recession with zero debt and a few billion in the savings account.
Since the Alberta government owns the mineral rights, you may ask, "What about the Canadian government". Well, as it happens, on oil sands the Canadian government makes more in income taxes and goods and services taxes than the Alberta government makes in royalties. If you're expecting either government to clamp down on oil sands development, don't hold your breath. Those extra billions look too good at budget time.
Local governments don't do as well unless they have an oil sands operation in their tax base. That's why the City of Fort McMurray (pop. 70,000) unincorporated itself and became a hamlet within the County of Wood Buffalo. Another exception is the Hamlet of Sherwood Park (pop. 80,000), sitting near Strathcona County's Refinery Row, which has most of the refining capacity in Western Canada. Most other hamlets in Alberta have less than 50 people.
RockyMtnGuy - see my post in today's Drumbeat in re: Venezuelan production figures.
So the steam condenses in the reservoir and then oil and water is pumped or driven to the surface. When the water is separated from the oil, the water is heated and pumped into the boiler. The cycle repeats itself. Is there an added expense of both heating the water before it is fed into the boiler and the feed water pump. Is there heat recovery? Are these boilers operating around 450 psi. Is it possible to heat the water without changing it to steam to save BTU’s.
Is this high pressure hot water that flashes to steam in the reservoir?
I'm asking questions.
The object of the exercise is to put heat into the reservoir to melt the bitumen, but not necessarily steam heat. They've experimented with using radio frequency radiation to heat it, but steam is cheaper. Another technique involves injecting air and setting the bitumen on fire, but that is harder to control.
The steam condenses to water in the reservoir and releases the heat of condensation. That's the advantage of using steam rather than hot water - it puts that heat into the reservoir.
It's cold water that goes into the steam generator, because the function of the steam generator is to heat water to steam. You put the heat of condensation into the steam, and in the reservoir it comes back out when the steam turns back to water.
The heat melts the bitumen, the bitumen flows down into the lower well bore, and progressive cavity pumps move it to the surface. That's the basis of SAGD: Melt the bitumen and collect the drips. The drips can add up to a million barrels per well, so it's pretty effective.
Rocky -- I tried for 10 years to talk operators into air injection (in situ combustion or "fire flood") on the Texas Coast. though folks tend to associate such thermal recovery techniques with CA the most successful pilot projects were in S Texas and N La. I did find some projects in Vz that appeared to be economic. But, as you say, difficult to control and even more difficult to understand for most operators. Oddly enough I discovered the most dangerous part of the operation was the compressed air. Turns out to be highly explosive when it comes into contact with hydrocarbons like lube oil. They blew up quite a few compressors and pipelines as a result. I had one engineer almost throw me out of his office when I pitched the idea. When he was a young buck with Getty Oil he blew up half a field on night. Today they have non-combustable lubes but folks are still afraid.
All the injection programs I know of now are using inert gases like CO2 or nitrogen. But ICU is so much more efficient as you are using only around 12% of the hydrocarbons in the reservoir to fuel the process. Recovery can be as high as 80%. I did get one operator to fund a project but before we could finish acquiring the field he had the audacity to die on me.
I had similar experiences experimenting with fireflood in the oil sands. We couldn't control the fire front enough and kept blowing up wells. This was a traumatic experience for the production operators because they would blow the tubing string high into the air.
In another case we took over a heavy oil field that someone had tried fireflood on. They had completely screwed up the whole field and there was only one good well left. We abandoned all the others, tore down the production facilities, and just trucked oil out from the remaining well.
SAGD is much more controllable and rather low-pressure and subtle. The geologists can watch the steam clouds forming on 4D seismic and make sure they are not losing steam down some fault or something.
It actually works better than it should in theory, and will just kind of ignore anomalies that should stop it. There was some paper describing how, if a thin shale layer blocked the steam, it would just fracture it and continue on through.
It's not perfect yet, but it works better on oil sands than anything developed prior to it. It works particularly well in thin formations that would otherwise be uneconomic. A lot of the smaller deposits are not very thick, but they just go on forever.
Rocky -- I would think your oil sands would be much more complicated then my proposed ISC projects. My reservoirs were high porosity (30%) and low water sat. They were pure pressure depletion and undersaturated to boot. The porosity and perms were so good water flooding efforts almost always failed: channeling. And the oil, though viscous, was high quality and got a premium price.
But no more pushing fire floods for me. I've turned to the dark side (exloration) just like our bud westexas.
Petrobank has been operating an insitu combustion production pilot facility (Whitesands THAI = toe heel air injection) in the Alberta Oilsands for over three years now. The original review of THAI on TOD was August 2007.....see http://www.theoildrum.com/node/2907 with an EROI analysis of the 10,000 BPD May River Phase l Project last March...see http://netenergy.theoildrum.com/node/5183
Those of you with a technical background interested in the progress on the commercial development of this technology will find the latest response to Alberta's SIRs dated Dec 15, 2009 for the 10,000 BPD May River Phase l Project at http://www.petrobank.com/wp-content/uploads/2010/01/Petrobank_Round1_SIR... very informative. Bottom line....the year long dialogue with and responses to the Alberta agencies Supplemental Information Requests and front end engineering is complete....detailed engineering and procurement has began with commissioning/well preheat scheduled to begin Nov 2011 and full production of THAI™ sales oil scheduled for August 2012.
As I recall from subsequent posts on THAI method for tar sands production, the uncontrolled gasseous emissions violated environmental rules. The two main problems were with oxides of nitrogen (NOX) and sulfur dioxide, both of which could be controlled, but at a cost. The NOX could be eliminated by incineration using natural gas and the SO2 controlled like gas from a power plant. Control of both emissions lowers the EROEI, so I have my doubts about the claims of THAI having 40 to 50 EROEI , maybe it would be more like 10 to 20, IMO.
Furthermore, what happened to the tests of CAPRI method for upgrading oil (higher grade bitumen) insitu coming from THAI process? The CAPRI design relied on pipes with very small holes to collect the oil, which would seem to get easily glogged with sand, restricting flow. Any progress there?
Is it true that in a fireflood or THAI system that once the front moves through the formation, and you recover the hot, flowing oil -- that you cannot ever go back into that reservoir to recover more oil because the fire front has effectively glazed everything and solidified remaining oil? That's what I heard. But if the average oil recovery using THAI is <50%, then aren't you leaving a lot of oil in the ground that won't be recoverable later?
No....there's no oil/bitumen left to recover....in the mobile oil zone, the bitumen viscosity drops to that of water and is produced out the horizontal collection well...only a coating of bitumen remains on the sand which becomes the fuel for the THAI oxidation process.....elegantly simple (once you have selected an appropriate FacsRite™ liner that filters out the sand downhole :<)
heavy -- I don't know about THAI but in the few cases where they went back and cored reservoirs that had been fire flooded there was no oil left. All that remained was the coked residual (around 10-15%). This represents the fuel used to drive the ISC. The rest of the oil had been produced. But these were in high porosity reservoirs with good permeability and fairly mobil though under pressure oil reserves. Other methods such as THAI and poorer quality reservoirs might not be as efficient.
Recovery in the Athabasca Oilsands......70 to 80% OOIP based on the Whitesands Pilot ....3+yrs running....http://www.petrobank.com/heavy-oil/the-thai-process/ ...as I understand the resource, about as difficult an application for insitu combustion production as one can find....
http://www.petrobank.com/wp-content/uploads/2010/01/Petrobank_Round1_SIR... ....pages PU-26 through PU-33....
documentation filed with the Alberta Gov't energy and environmental agencies Dec 15, 2009.
Anyone whos ever used a pressure cooker to cook a potatoe should know that high pressure steam is very good at getting heat into the interior of a porous medium.
to encapsol ,spammer
show us our MSDS and then we can talk? until that, spam elsewhere.
No MSDS? , no use in USA. sorry. Canada, don't know about that.
Has to be safe to handle and safe for the environment.
sorry to fuel the fire(pun) of spammers.
I too could make a video showing any thing you want. Your video means nothing here. (smart ppl)
I'm not a spammer, I'm someone who cares about the oil industry and new technologies of value. You, on the other hand, seem intent to suppress ideas and innovation that can help our country produce more oil. I've done my homework, you have not done yours.
EncapSol passed California's strict Fish BioAssay tests and other required tests to prove it is a non-hazardous substance -- did you read their website? -- all the fish survived exposure.
If you are in the oil industry, then you would know that 90% of the chemicals we inject in the ground are toxic and classified as hazardous substances -- so Encapsol should be lauded for its environmental friendliness -- not scorned by those who didn't take the time to research the facts.
What other solvent technology do you know of that is non-toxic, can make oil flow in cold conditions, can extract bitumen from oil sands using no water, using no natural gas and producing no liquid tailing pond waste?
These are the environmental reasons why America is NOT currently harnessing its vast oil shale and tar sands resources (which could totally replace expensive foreign oil imports).
If Encapcol or any other technology can help America cleanly harvest its unconventional resources -- then we should be supportive, not antagonistic -- and let such technologies prove their worthiness. But don't shoot the messenger...
"What other solvent technology do you know of that is non-toxic, can make oil flow in cold conditions, can extract bitumen from oil sands using no water, using no natural gas and producing no liquid tailing pond waste?"
Actually, supercritical CO2 extraction will do all those things...
"let such technologies prove their worthiness"
That's precisely what we are saying, let it prove itself, rather than your infommercial like hyping.
We are not shooting the messenger, the messenger (you) has given no indication of who you are, what your experience/background is, and you sound like an evangelical preacher for this unproven technology. We don't want to shoot you, we just don't trust you.
If it proves its worth, then you can have the satisfaction of being right, and I hope you make lots of money off your investment.
Keep in mind that in the energy, and alternative energy (biofuels etc) field, there are many, many companies that have been making great claims on now processess (think algae/cellulosic ethanol) or new efficient engines/batteries etc, and very, very few have come to pass.
I wish this company well in their endeavours, and if it is everything they/you say, then they have a game changer. But in this business, until you have proven your process technically and economically viable, you are just another tech dreamer.
Many great inventors had their doubters, and the ONLY way they overcame them was with actual working results, in the commercial world. And at that point, no messenger is required, as the results speak for themselves, as they should.