Tech Talk: Charcoal, Oil Shale, and the Ecoshale Process in Utah
Posted by Heading Out on April 4, 2010 - 10:59am
If you drive West from St Louis (as I did Thursday after my check-up*) you will occasionally hit a pocket of air that smells a little sweet, and a little burnt. It is the product from the charcoal kilns up near Vienna, one of the larger centers for making charcoal in the country. Apart from its use in making barbeque, charcoal has other beneficial uses, and it is projected that it has been used over many millennia. Modern consumption in the United States runs around 375,000 tons.
To really simplify the technology for making the fuel (which may become a unique post at some future point)
Making charcoal from poor-quality timber and sawmill waste is a process that has changed little in centuries.
Before it becomes dimensional lumber, every log harvested in the Ozarks first must be sawed square. The bark covered slabs produced by that first cut become the raw material for charcoal briquettes. Seasoned hardwood is sealed in an air-tight enclosure and allowed to burn with the barest minimum of air. Just like in a woodstove with the damper closed, the wood slowly turns to almost pure carbon as its lighter, more volatile components are driven off by heat. This process, called pyrolysis, can occur in a pile of wood buried in a hole in the ground or inside a metal or concrete box called a Missouri-type charcoal kiln. For years, making charcoal was one of the few sources of income for people in the Ozarks.
In the modern, larger scale version of that process the sawdust or waste wood is treated in something that looks like a refinery:
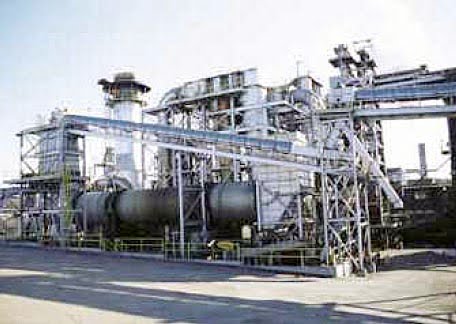
However, in the earlier times the kilns were made with earthen and turf walls to seal in the charcoal as it cooked. And it is that technology that I want to return to today in another post on Oil Shale, in this case discussing the EcoShale project in Utah.
The Ecoshale project is being promoted as a new approach to obtaining oil from the shales of Utah. The company proposing this “In-Capsule” process had a fair-sized booth at the MinExpo meeting in Las Vegas a couple of years ago, that drew my attention. I stopped by and watched the video (twice) picked up literature, and talked to one of the folks at the booth. Since there is considerable oil (well actually kerogen) locked up in the shale (perhaps as much as 1 million bbl/acre), it is worth seeing what they have planned. I will include a few thoughts as I go through the process.
Those in the UK might want to visit Ian West’s site which gives some history regarding shale burning in the UK.
Until now I have largely, in the recent posts on oil shale, focused on the thicker layers of oil shale in Colorado, but there are places in Utah where the oil shale near the surface is more than 10 ft thick, and where the shale will yield more than 25 gal/ton. With prices of oil fluctuating, the grade at which production becomes possibly economic will vary, but for the following discussion I am going to assume that a ton of ore will yield about ¾ of a barrel of oil. I will also assume, for simplicity, that a ton of shale occupies 14 cu. ft. before it is mined. The plans for the project, at the time of the MineExpo presentation, were that it would be scaled to produce 30,000 barrels of oil per day, at an anticipated cost of roughly $3 billion. This has now been split into plans for a 9,500 bd commercial project prior to that larger operation. Red Leaf, the company, holds leases to 17,000 acres of this shale (with an overall average of 25 gal/ton, ranging up to 70 gal/ton).
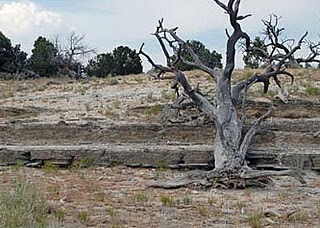
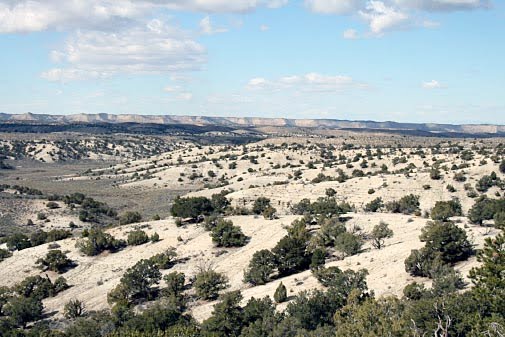
The first thing that happens at a site is that the overburden, and shale that doesn’t have a high enough oil content is removed and stored for site remediation after the process is over. (I am going to use oil to describe the hydrocarbon content, ‘cos it’s shorter to write than kerogen.) This will require a significant area, since the volume of rock being uncovered every day is going to be large. There are going to be three operations going on at one time, in order to make the process work. The first is the removal of the overburden, the second is the preparation of a site to act as a retort, and the third is the mining of the oil shale and the building of the retort. The retort is then left in place to “cook” the oil/kerogen over a period of some 90 days, before the site is reclaimed. Retort preparation will take place in a space where the shale has already been taken out. (This requires the initial removal of an additional volume of shale that has to be set aside and stored to give the space for the first retort to be put in place.) This is because the underlying bed must be prepared, and the infrastructure for the retorting has to be put into place.
To get just a little ahead of myself, the process of retorting the shale involves mining the shale, and then building the broken rock into a crushed zone, through which pipes have been placed, that will carry natural gas to heat the rock. The rock is then covered with a thick layer of an impermeable rock (for simplicity I am going to assume a crushed claystone) that will act as a seal. In this way the shale is encapsulated, and as the heat from the gas works then so, as with the wood in the charcoal kiln, the rock is processed, the hydrocarbons driven off, and collected in drainage tubes that are interspersed through the layer.
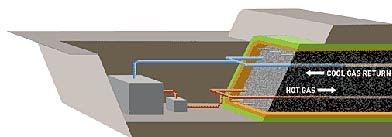
If we look at the operations required for the full 30,000 bd operation, the mining of the shale will require some 40,000 tons of rock to be mined and moved every day for production, as well as the removal of the overlying rock from the next batch down the strip. This is equal to around 560,000 cu ft of rock. For the sake of discussion, if the strip being mined is 50 ft wide and the shale seam is 35 ft high, this will require that each day the mine will move a panel that is 320 ft long. However this isn’t all the rock that is required. Because before the shale that is mined can be placed in the retort zone, a layer of clay will be placed over the pit section in order to give an impermeable barrier below the shale to stop contamination of the underlying rock and any water that it contains. This layer is going to have to be very thick, since the oil shale above it is going to be heated to the point that it releases the oil. This takes a temperature of 900 deg. At that temperature the clay will bake and becomes very brittle, so the clay layer must be thick enough to allow for this and allow enough temperature drop to leave the lowest layer still flexible enough to act as a seal. Let’s assume for now that this is going to need a layer that is 3 ft thick. (I’ll come back to this later.) In a recent test of the process the seal provided also included a plastic sheet as well as bentonite. (Presentation slide 19).
Once this clay has been placed (and it should slope at about 5 degrees toward the open face to allow for effective drainage), then the mined shale can be placed on top of it. Drainage pipes are placed near the bottom of the shale layer, then more shale is added, and a heating set of pipes is laid across the shale. These pipes are connected at the back of the day’s pile, so that the gas that will pass through them will also move back through the pile and back to the face of the pile for collection. More collection pipes are then placed as the pile rises and is flattened over the recovery site. The pile will be considerably higher than the mined area since, in mining the shale it also “bulks” in volume by about 60%. The reason for this is that the pieces no longer fit exactly together. Think about a jigsaw puzzle. When the puzzle is made it only occupies a small area of the table, but when all the pieces first come out of the box they fill a much bigger space, because of all the empty space around each bit, and that the pieces are all separate. It is the same thing for rock. (Some of those internal spaces will be filled as the shale heats and degrades, so that the pile may collapse a little during the heating process). Thus the pile that will be made will be have to fit into the same “footprint”, i.e the 50 ft deep, 320 ft long shape it came out of, but will now be 56 ft high. With the underlying clay layer this will make the pile some 59 ft high at this point. (And require about a thousand tons of clay a day.)
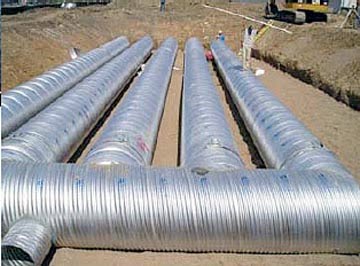
By going through this process the mine is creating a “use once” retort that encapsulates the spent shale, and collects the retorted products without some of the disadvantages of a more conventional retort. These include (from the brochure) protection of groundwater, lack of need to sequester tailings, and obviation of the problems of retort clogging and moisture retention within the retort.
Now the mine has to seal the retort to keep the retorting heat within the shale and not to let it, or the gas and oil generated out. So a cap will be placed over the broken shale and, for the same arguments as above we will assume for now this is also going to be about 3 ft thick. (I hope it doesn’t rain much in this part of Utah. The impact of water on clay/shale at 900 deg C is spectacular, since the clay shatters explosively and is easily eroded.)
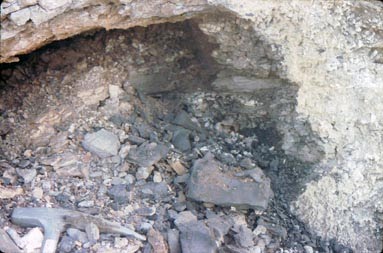
This will take the pile up to 62 ft high, which is quite a bit higher than the original 35 ft. It is interesting that the brochure suggests that this will be a “low temperature, stationary heating” given that the initial temperatures to liberate the shale have been documented (as noted above) at 900 degC. And my memory suggested that that number also cropped up in my conversation at the booth. It will also have to have a front panel of a sealing rock and clay placed over the face of the section, in order to complete the capsule.
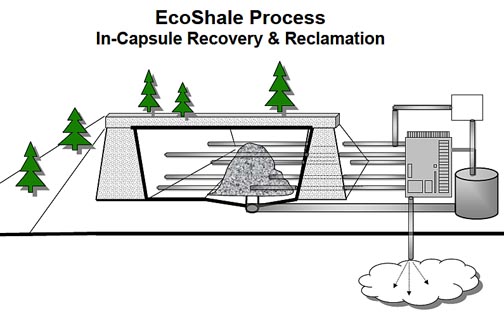
Now the heating pipes are connected to a natural gas burner that will feed the hot gases into the heating pipes, gradually bringing the shale up to the temperature where the transformed oil can flow to the collection pipes, and any gas produced can also be collected. The booth spokesman told me that they anticipate that the natural gas needed can be collected on site, and that the heating will take a total of 90 days to heat the shale to the point that all the hydrocarbon content has been recovered. That means that the retort section of the mine will be roughly (90 days at 320 ft per day) 5.5 miles long.
After retorting is complete, the heating element will be disconnected and the shale and overlying clay allowed to cool. It will then be covered with the initial overlying rock that will be restored to roughly original contour, and the ground fertilized, seeded, and the ground cover re-established.
While the brochure cites the approbation of the Governor of Utah, the commendation for the project was written at the time that the price of oil was some $120 a barrel, so we may have to wait a short while until it gets back to that level before the project starts to take off.
By December 2008 the project was reported to have invested some $15 million in research and development of the process. They are currently in development of a large-scale pilot demonstration. Information on the web site, however, is a little sparse concerning current progress, through oil was apparently produced in November 2009.
Ecoshale's synthetic product has properties rated by the American Petroleum Institute (API) as 39 condensate oil and between 34 and 35 prompt oil with no fines, or impurities, in the oil.
Based on the test study, Nelson projects full-production at 30,000 barrels a day would cost $20.21 per barrel, not including transportation.
My concerns with this come in the transition from a single retort which can be built to quite high standards, to the operation of even a smaller continuously operating system, where there are likely to be considerably more and larger problems with operation than appear evident at this stage in the process.
* My thanks again to those concerned after my eye problem arose. The surgeon told me yesterday, 3 weeks after it happened, that I now am back to 20/20 vision – albeit using glasses. I remain highly impressed with what modern surgery can achieve.
Thanks! That process sounds pretty amazing. The expected cost of $20.21 per barrel is particularly amazing.
I'm also amazed - we'll have to see if such claims actually pan out (if some entity actually wants to try to scale this up).
With all that moving of overburden and retort building, 900F, etc, I'm wondering what the EROEI would be.
Shale gas or unconventional resources development had become economical in the last three to five years due to technical advances in horizontal drilling and hydraulic sediment fracturing and amid the increasing cost of gas. And we know that shale gas reserves are sufficient to meet the current and anticipated demand growth for home heating, industrial, power and transportation needs. Development of domestic resources will reduce our imports. There are still some concerns like water contamination issues related to these resource developments.
Want to learn more about balanced energy for America? Visit www.consumerenergyalliance.org to get involved, discover CEA’s mission and sign up for our informative newsletter.
A goddamned advertisement?
And that on top of the stock hypers at the end of this thread. There are obviously a few people trying to pump and dump oil shale...
Holy cow thats tiny, but the impact would be pretty noticable. How will they control dust? Any concerns for cryptobiotic soils?
These operations are not scaleable in any way and will end up trashing the place pretty good.
Note on the scaleability: Red Leaf actually makes note of the "small scaleability", promoting "pihole scaleability". I presume that refers to a pincushion in some way. That is, numerous filled pits and disturbed ground hither thither and yon. This would result in a moonscape - that is, no pretty junipers to help attenuate the wind. It gets windy out there.
How will these pits, roads, installation fair with rainfall? Ever make an attempt to drive these areas when they are wet?
They plan on stockpiling the overburden for "re-vegetation"? Hopefully they will cover it up so it wont blow away or wash away. What do they intend to do in places where the shales crop out on the surface?
Upon inspection of the corporate brochure, I'd have to admit I'm impressed with all the infrastructure they have at that site. Nice house. The rented equipment looks pretty well kept. Lots and lots of excavators. I hope they are able to streamline this - I am very skeptical of the $20/barrel "return".
As you say, the wind blows pretty good out here. Pinions planted on the east end of Boulder Mountain, following a logging operation, are now, 30 years later, only 8 to 10 feet tall. Junipers grow even more slowly. I'd guess it's the wind, the cold, the heat and the little water. I'd guess successful reclamation would be a tough project.
This past winter, my neighbor lost 12 of his mother cows, for sure, and is out another 23 as in can't find them, all from a herd of 90 cows. The cold, the wind, and the mud got em, and these are cattle that are used to this country.
Tracks made by little 4 wheel rv's remain for 10 years, 20? This past week we have had steady winds of 30+ mph. I've experienced gusts of 120 plus mph. Roads to these sites would have to be asphalted over a substantial base of heavy fill because, when the ground out there gets wet, a heavy vehicle can't get through the bentonite and clay mud. Asphalted roads in the area have a very short lifetime with just occasional personal vehicle traffic.
I doubt undesirable byproducts of this process can be kept from the ground water. I also doubt the $20 per barrel figure and suspect there is much enthusiasm lacking the restraints of reality.
There is lots of gold in the Colorado River, very fine, and shaped like little boats; it floats along and can be seen when the sun is right on the water. Much money and effort was spent on dredges and various other mining operations and schemes in an attempt to claim these glittering riches during the late 19th and early 20th centuries, all without success, and financial ruin for most of those involved. There is a lesson to be learned from this land; the little treasure we have isn't easily claimed. Of course, folks have got to find that out for themselves. Best from the Fremont
Also, why are we flogging the "shale" stuff???? If we're going to spend so much time discussing "shale" why not have a ~>geology<~ "tech talk". Some of this must be driving geologists nuts (I'm already nuts....)
The shales you're talking about here in Utah are way different than the argillaceous limestones you "all" are calling "oil shales" over in Parachute. Why not have a "tech talk" describing these lithologies, and how their physical and chemical properties differ and why that is important. Also perhaps a good time to discuss hydrocarbons and the differences between olfins, kerogens, petroleum, etc. Repetition is a valuable tool in teaching.
You state that they will need to cook the sale at 900 degrees C as oil shale producers have in the past. However one of the benefits of the Ecoshale process is that they roast the shale as much lower temperatures which will result in much less expansion of the waste product I assume and also produces a much better quality end product as a result.
"Without using any water the process transfers dry, low emission heat from natural gas burners through the pipes. When the roasting is completed, they remove the heat by circulating air through the pipes into an adjacent cell. The company says no rock is burned at any time and they claim by burning natural gas, they avoid nearly two-thirds of typical CO2 emissions. The heat used to remove oil in other processes often burns the oil and it is not as good of quality. We heat the shale at relatively low temperatures and so the product, once refined, comes out and can be used as diesel or jet fuel"
"The pilot plant that ran this winter produced a test production of of approximately 15,000 barrels of oil. The oil extracted during that process has been rated with an average API of 34 which is close to that of intermediate Texas crude. This is a breakthrough for oil shale production product, which often is rated much lower and requires a lot of processing before it can be brought to market. "
http://www.sunad.com/print.php?tier=1&article_id=16029
Who's jet? :>
Really? How much different? Why is the shale in Utah so much different from the shale just across the border? Looks like, from the map, that they are connected and part of the same formation.
Map of the Oil Shale Basins in Colorado, Wyoming and Utah.
Ron P.
This is why we need a geology lesson.
The Alberta Taciuk Process retort with mining which produced 200000 barrels in 2005 had a break-even cost of $11-13 per barrel and today their retort at full capacity has a break-even price of $13 per barrel.
http://en.wikipedia.org/wiki/Oil_shale_economics
The article says they project a $21 break-even price but does this include CO2 sequestration?
They can put gas in but not let it out?
Besides limestone decomposes at 932 deg F or 500 deg C and most oil shale ia locked into a matrix of limestone and clay. Modified in-situ oil(except Shell's) shale methods are is biggest emitters of CO2s.
The fact that oil shale pops by 60% is interesting---bread rises a bit more in the oven.
The ash has been used as clinker in cement production.
http://www.medemip.eu/Calc/FM/MED-EMIP/OtherDownloads/Docs_Related_to_th...
http://en.wikipedia.org/wiki/Red_Leaf_Resources
http://www.redleafinc.com/
EcoShale In-Capsule Process
• ‘Capsule’ excavated and lined with clay; approx 1,000 x 500 ft (12 acres), up to 100 ft deep.
• Expendable heating pipes laid
• Capsule filled with crushed oil shale from the next excavation
• 120 day heating cycle using natural gas burners brings temperature up to ~ 750 deg C
• Oil collected from drain system (‘prompt oil’) and condensed from emitted gas. Methane gas used for heating
• ‘Spent’ capsule remains in situ. Surface reclamation can start immediately
• Scalable technology, based on number of Capsule Face heating/drainage systems in use
• Little water used in process compared to other technologies (very important in Utah)
• Each capsule expected to produce:
~ 1 million bbl oil
~ 250,000 boe gas (~1.5 Bcf, of which 750 MMscf used for heating and 750 MM scf available for sales)
$ 20.21/ barrel ? can they calculate the cost to the penny/barrel ? not at all credible, imo.
shale gas,shale oil and snake oil are looking better all the time.
Perhaps the volume is too low to recoup capital costs? 30,000b/d really is not that much.
I wonder if these smale scale efforts have a parallel in the conventional oil production world. The US is still one of the major oil producing countries despite the average well making less than 10 bopd. This is due in large part to small and very small operators. The ExxonMobil's cannot function profitably in this world...too much sweat equity. While 30,000 bopd doesn't side like a lot it is a huge amount compared to the small conventional operators in our country. If these small scale recovery projects are viable perhaps it could be expanded collective to a significant level. But I have doubts there would be enough players in this new game. Probably still going to need a very major scalable process to have any real impact.
So assuming a) this process works and is scaleable b) it can avoid contamination of the surroundings at an acceptable level and c) a significant volume of suitable shale is accessible to the technique, then the question becomes what will the equivalent price of oil need to be on that day when shortages cause prices to rise to the then-equivalent of today's $120 / bbl? Cerainly oil sands "required market price" has risen dramatically in the past several years, from $25 / bbl to something like $75 / bbl.
A key difference between kerogen in shale and lignin in the charcoal kilns is the carbon cycle time scale. Most of that carbon in shale will stay buried for a few million years so bringing combustion products to the surface is unlocking fossil carbon. On the other hand if wood and sawdust is harvested sustainably the carbon is cycled above ground between the air and the trees. There is however the problem of the large amount of diesel used in harvesting and transport.
If they ever get cap and trade right oil from shale should be hit with carbon penalties while charcoal avoids it.
I can't wait till we talk about how charcoal is/was made in upstate NY by individuals to sell and its short and long term
impact on the local environment. I continue to be amazed at the cultural and statutory negativism towards burning trees,
and hopefully someday other growing things in suburbia.
A little off topic-we make some charcoal occasionally for our own use.If you have a reason to have a large outdoor fire that will last a while, you can fill up any fair sized steel barrel with small chunks of hardwoord, secure the lid, punch a couple of vent holes in it, and put it in the fire. After she gets good and hot, there will be a highly visible jas jet exiting the vent holes, and this gas jet will burn like a blow torch. Some tar may condense on the outside of the barrel in the early stages , depending on the amount of fire and temperature near the vent holes.
When the jet burns out, the charcoal is finished.DO NOT attempt to remove the lid until the barrel and contents have had plenty of time to cool off, else you may experience a fast flare up and get severely or fatally burnt.
The charcoal wil be light and fluffy and if you use it before it absorbs moisture from the air, it is easily lit with a match or a very small amount of paper.Since it has not been bricked, the charcoal has a low density and burns up fast, the same way it ignites.It is excellent for hamburgers and steaks or any food that cooks fairly fast.
We have large fires as a matter of course several days a year as the best way to dispose of pruning debris from an orchard operation is to burn it- for sanitary reasons.
I don't see any reason why a person could not manufacture small amounts of charcoal this way for use as a soil amendment in a home garden by putting a gallon or two gallon container of chips in a wood stove.There might be some danger of a flash fire from the fumes or gases, however, which might result in a house fire or personal injury.
Obviously any container used should be known to be free of contamination with any noxious mterials.
I could be wrong- but my estimation is that cap and trade is no more than the business equivalent of a badly shop worn call girl-it may be the only feasible method of passing carbon dioxide emissions legislation here in the industrialized west because of political considerations,but the process wil be simply riddled with special interest inspired regulations and literally drowned in gravy for thebankers and algor investors.
A simple carbon tax would be far more efficient and far less subject to income tax type manipulation.
Anyone who doesn't get it should reflect on the fact that our new health care bill is over one hundred times as long as canada's basic health care bill.The extra 99% is mostly for the nourishment of the parasites.
And anybody who thinkd that the rest of the world, or even the US, is going to quit burning coal OR pay for ccs if the economy keeps going down hill is a politically niave to say the very least.
When the oil starts running really short and members of environmental organizations start eperiencing rationed electricity,they will suddenly gain a new perspective, and the political pendulum will swing hard too the right.
I'm just predictin'and not preachin.
Interesting write-up. thanks
Isn't this project just a way to avoid the label "strip mine"?
It's unlikely that the environmental impact is less than building a refinery and conveyor system on site.
This plan just seems to be pretending to mine the oil in place. In reality it seems to be about minimizing costs through the least material movement possible. The tailing and uncaptured oil are kept out of sight.
The encapsulated in place tailings are certainly a positive that differentiates this system from other types of strip mining operations, but as rain has been mentioned, I wonder just what sort of precautions would have to be taken to keep the retorts dry? Several mile long piles would be expensive to temporarily 'roof.' Enough properly composed, graded and compacted dirt would work but lots of chance for error when covering a several mile long oven.
REDleaf.claim EROI of 10, & cost of US$25/bbl.
From REDleaf Economics
On costs, REDLeaf offers: Independent Evaluation
Great write up. Like everyone else, I find a cost of $20/bbl hard to believe. The most efficient Canadian oilsands surface mining operations have a cash cost of $30/bbl (not including capex), and they have had decades to get their process optimised.
This process is indeed analagous to the old school method of charcoal making, and for the same reasons as charcoal is no made in controlled retort conditions, I suspect that for oil shale the same would apply. What we have here is an artificial version of steam assisted gravity darinage used in oilsands, at much greater cost.
Once you have this stuff in the bucket of an excavator, a controlled retort type process seems a better option, and opens up possibilities for heat recovery, and some alternate uses of the end product. An oil shale operation in China use the hot, spent shale ("shale ash") for brickmaking, and some of the shale is fired to higher temperatures to make clinker for cement making. Both interesting ways to turn an otherwise unuseable, hot, waste into commercial byproducts. Google Fushun Oil Shale and you will find a few sources. They have been mining oil shale their since 1935!
That said, the fact that Red leaf is having trouble raising the capital suggests that none of the oil companies(major, minor or in between) think this is worth a bet - if there was money in it someone would jump on board.
I suspect that this scheme will prove in hindsight to have been one of a whole rash of mad, desperate, hyper-destructive, futile, and ultimately unworkable, BAU-defender delusions that we undertook in the first half of the 21st Century, to try to deny/prevent our inexorable progress down the backslope of the global Hubbert's Peak.
Here, for example, is a brief summary of why:
http://culturechange.org/cms/index.php?option=com_content&task=view&id=6...
There are plenty more. But perhaps the whole technowhizz balmy optimism of such ideas is best demolished by a patient working through the panoply of linked ideas and themes which the Archdruid lays out at his blog. Worth the patient effort.
This stuff ain't gonna happen for more than a short, stuttering while. The best way to make charcoal is by sustainable light-touch harvesting of timber feedstocks, both large and small, from heavily conserved, protected and +extended+ forests. And the best thing to do with it is to put it back into the soil as emending, atmospheric-carbon-resequestering biochar, where it will likely stay for thousands of years, working as terra preta chernozem all that time in highly sustainable community agriculture techniques. There are pyrolysis processes which allow modest amounts of liquid fuel to be drawn off as bi-products during the making of this char. That's about as good as it gets.
The best forms of sustainable community agriculture to serve this process, and many other benign and necessary human requirements at the same time, are the many variants of agroforestry/forest-gardening/forest-permaculture now well proven by modern re-pioneers.
As Jim Kunstler keeps hammering: forget keeping the sacred cars and the people's aircraft running. It's just not going to happen for most of us. The high-energy, cheap-energy lifestyle, even for just the Pampered Twenty Percent of the world's current gross over-population who've had it recently, is coming to its close (whatever we do), and the population overshoot with it. Accept that now, with greater ease, or accept it with a lot more pain and angst after a whole lot of these futile schemes have come and gone.
The current famine of finance and vital commodities isn't just a temporary thing, before 'we' get back to BAU. BAU is dead already, and just zombying around for a short while longer before it collapses unmistakably (how much more unmistakable does that need to be!). What resources we can actually marshall now need to be put to work in genuinely intelligent deployments which actually address the real circumstances into which humankind are now proceeding. Every year that we delay that sober awakening lessens the amount of such resources which will be available for sober, effective life-boat initiatives. The less lifeboats we create, the more Titanic drownees there'll be, worldwide -- including in neighbourhoods near you......
WRT charcoal, this is why I do not take too seriously or have much anxiety about the issue of keeping at least a minimal industrial infrastructure operating to rebuild/replace WTs, hydroelectric turbines, etc. Just about anything that requires coal could use charcoal as a substitute. There certainly are limits on how much charcoal we can produce and use, but we certainly are capable of producing enough charcoal, even just using the oldest, low-tech methods, to keep a few small-scale forges, iron mills, etc. running. Charcoal is likely to be one of the very last things we would run out of, and if it gets to that point, there won't be many of us left to worry about it anyway.
I agree with this. But note the insolation/afforestation-dictated order of magnitude which this old process must have to be sustainable (and even then only for as long as scavengeable steel stock or credible ores can still be found). This has to happen at a level a +lot+ less than current demands. There has to be a massive die-back of human numbers first, to make this workable for more than a small percentage of the numbers alive now.
The idea of making good, useable oil from oil shale, tar sands and other oil rich earthen products is nothing new. Processes for extracting oil based products from these sources has been around a very long time.
The Problem is, however, that there are major drawbacks in doing so with traditional processes. Some require more input of energy to remove the oil than the oil itself will supply. In other cases the environmental damage, both in terms of air and water pollution, along with desecration of the land that the earth is being removed from is unacceptable by many people.
And finally there is water. Most processes need water, lots of it. In fact in some processes the amount of water get the oil out of the petroleum laden rocks is as much or more than a one to one ratio.
That's why a new process, developed by Red Leaf Resources of Salt Lake City is so interesting. Many of these problems appear to disappear with their new process they have demonstrated in a pilot plant that is located in southern Uintah County along the Seep Ridge Road.
For those that attended the SEUPA banquet at the Carbon County Events Center last fall, there is some familiarity concerning this process. The speaker at the banquet was Laura Nelson, vice president of energy and environmental development for Ecoshale, a division of Red Leaf Resources and she spoke at the time about the upcoming operation of the pilot plant.
Now that plant has run and the results have been outstanding. A legislative tour spent time at the site in late May and the tour was an eye opener for every one involved.
The site is located on school and institutional trust lands, and the company has already obtained leases to do much more than just a pilot operation. The company holds leases on approximatley 17,000 acres of SITLA land. That land holds an estimated 1.1-1.5 billion barrels of in place oil equivalent shale resource. However, right now the pilot plant only takes up a few acres in the vast expanse of land that lies between Vernal and Thompson near I-70.
The pilot plant that ran this winter produced a test production of of approximately 15,000 barrels of oil. The oil extracted during that process has been rated with an average API of 34 which is close to that of intermediate Texas crude. This is a breakthrough for oil shale production product, which often is rated much lower and requires a lot of processing before it can be brought to market.
The pilot plant sits on a five acre plot, that includes the plant itself, storage capacity, a maintenance building and an office for site management operations.
The day the legislators visited the site, all was quiet, because now the company is just waiting to expand their operation and the plant was not running.
Before a tour of the plant Nelson pointed out some of the advantages of the plant over other methods of extraction.
"We use no external water to produce our product, which is important in this area of little water," said Nelson as the group gathered in the office buildings conference center. "The process does not disturb what ground water there is either. In addition the site can be rapidly reclaimed. In fact, initial reclamation begins as part of the process."
The test site consists of a small "cell" in which the process was operated. In many areas around the pilot plant the overburden above the shale is about 20-60 feet deep with some at surface. Oil shale seams are on average between 70-90 feet thick. The cell is excavated, the equipment for the extraction of the oil is put in and then the cell is backfilled with the shale and then covered with the overburden.
The plan is for the cells to be much larger, and after one cell is constructed and being processed the next one will be built right next to it and the equipment can be slid over to work on that cell when the previous cell has all its resources drained from it. At that point the previous cell has already been reclaimed with the exception of the pipes that are used within the cell, which remain in place.
"We have a completely innovative production process," said Nelson. "Rapid site reclamation, reduced carbon dioxide emissions, no process water use, and the protection of the ground and surface water make this process environmentally friendly."
Obviously with the kinds of oil shale processes that exist in most places today, people are skeptical of any kind of new process. But the company believes they answer most if not all environmental questions.
First they say they set aside overburden to preserve topsoil biodiversity. They claim this allows them to rapidly reclaim the site within a few weeks of completion of the production cycle as well as support new grasses and brush for wildlife within months.
"Reclamation is started before the removal of the oil from the cell," stated Nelson.
The cell is rapidly reclaimed. Instead of years to reclaim, the company returns native soils within weeks of the completion of the production cycle. New grasses and brush begin to appear within a short period of time.
Secondly the company says they build an environmental protection layer within a bentonite clay impoundment. Clay impoundments like this are used to protect the environment in the mining industry and provide long-term protection of ground water and underground aquifers.
The cell is then filled with freshly mined shale ore. The ore is sized, sorted and then roasted in the impoundment to extract the kerogen oil.
The company uses nonheat the cell. Pipes do not need to be removed after operations. Without using any water the process transfers dry, low emission heat from natural gas burners through the pipes. When the roasting is completed, they remove the heat by circulating air through the pipes into an adjacent cell. The company says no rock is burned at any time and they claim by burning natural gas, they avoid nearly two-thirds of typical CO2 emissions.
"The primary emissions we produce are from the gas burners that provide the heat," said Nelson. "And as you know natural gas is the cleanest of carbon based fuels."
Once the operators complete heating the shale and producing the kerogen oil, the oil can be upgraded to remove nitrogen and sulfur. Kerogen oil is a feedstock that is highly compatible with the production of premium low sulfur diesel fuel.
The process is a simple one and much of the equipment to do it looks like it came right off the shelf of a big box home improvement center.
"As you look at it you can see this is not very fancy equipment," said site manager, Les Thompson, as the tour of the facility began. "There were only a couple of things here that had to be invented. Mostly this was constructed with present technology, off the shelf stuff."
In the west and particularly in the Bookcliffs water has been a major factor in the failure of oil shale processing getting off the ground. Historically, traditional oil shale removal operations have used four or even five barrels of water for every barrel of oil produced, although this average has decreased to closer approximately 2 barrels today. In the case of the Ecoshale system, the company claims only one barrel of water is used for every five barrels of oil produced. That water is not used directly in the oil removal process, but for dust control, reclamation, and staffing use at the site. Even the average oil well uses two to three barrels of water to produce a barrel of oil.
As to the quality of the product, Nelson said the reaction from some has been surprising.
"Historically oil shale production has been a problem," she stated. "The heat used to remove oil in other processes often burns the oil and it is not as good of quality. We heat the shale at relatively low temperatures and so the product, once refined, comes out and can be used as diesel or jet fuel."
Cost of production has also been a factor for oil shale in the past. Often the cost of producing it has outstripped the price at the customer delivery point. But with the cost of a barrel of oil presently over $70 per barrel, the economics of the process look pretty good for Ecoshale.
"Based on pilot plant results we estimate the the operating cost to produce a barrel of oil at less than $25 dollars a barrel for an 8,000 barrel per day operation," explained Nelson. "We estimate that the cost would be lower for a 30,000 barrel per day operation.
One of the advantages to the process is the steady flow of oil that results. Nelson said that while most oil wells have an initial high point they drop off rapidly in production very quickly with most of their production coming in their first three months of operation.
"This process is consistent," she said. "The volume from the process remains steady throughout the operation."
The pilot plant ran for only 90 days, but the process worked well. Nelson said bigger cells would produce up to 8,000 barrels of oil a day and each cell which would have a relatively small foot print producing between 80-90 thousand barrels of oil per acre.
"At a production rate of 8,000 barrels a day, the company would generate roughly $10-15 million per year for SITLA," said Nelson. "With a 30,000 barrel a day operation SITLA would bring in about $150 million per year."
While the Bookcliffs hold a great deal of shale, there are also large reserves all over the world and people from many countries have visited the plant. Rather than the oil the technology could be the big money maker for the company. Oil shale reserves around the world are estimated to be eight to 10 trillion barrels with the total United States resources consisting of six trillion of those.
This technology could hold a lot of advantages for Carbon County since it can also be used to remove oil from tar sands, which is more prevalent in Carbon than oil shale is.
Obviously the Ecoshale in-capsule process could be a good portion of the answer to the energy crisis as well as to economic growth in the area and around the country.
http://www.sunad.com/print.php?tier=1&article_id=16029
Natural-gas-fired process, this press-release quietly admits. Good luck with that then, for any long time; good luck also with a sufficiently-large positive EROEI.
This is just ridiculously blinkered to what's happening throughout the whole global system.
Looking at this just on the scale of the single process is an inadequate way to assess it, and especially by listening to executives of the company which wants to float it. Look at such schemes within the larger system-wide energy/materials/finance flows; for example, within the context of the FEASTA and Risk/Resilience Network's paper, four posts down from this one:
"Tipping Point: Near-Term Implications of a Peak in Global Oil Production"
These are blind-alley schemes which distract us from the really important life-boat actions, and waste already bleeding-away resources.
I think it's important to emphasize that the product of the Ecoshale process is kerogen, which is a low-grade oil precursor. The kerogen needs further refining to make it usable as diesel or jet fuel.
I recall from a previous oil shale article that converting kerogen to fuel takes a lot of water because hydrogen is added to the kerogen. This hydrogen is usually derived from water. So while the mining might be nearly waterless, producing a usable fuel requires water.
Hardly a low quality product. I also read that it will fetch a $6-$10 premium to NYMEX prices.
The test of the EcoShale™ In-Capsule technology was carried out in the Uintah Basin in Utah. The field test pilot validated the technology modeling and engineering design aspects. The process produced a high quality product with a prompt oil that was approximately 29 API gravity, about 65% paraffin + naptha, and about 12.6% hydrogen. A condensate liquid was also produced with an approximate 39 API gravity, about 55% paraffin + naptha, and about 12.9% hydrogen. Sulfur content was approximately 2,200 ppm and nitrogen content was about 1 – 1.2 wt%. The oil produced contained almost no entrained solid fines from the shale ore. Red Leaf Resources anticipates that the EcoShale™ In-Capsule Process will be scalable for the levels of oil production specific to individual properties. Capsules (or, impoundments), which contain the hydrocarbon treatment zone, can be sized in various ways so as to facilitate desired project volume production or to match initial capital or equipment requirements. From smaller impoundments that produce a few hundred barrels per day, to enormous impoundments which produce thousands of barrels per day, the process scalability and internal rate of return on capital will be an ongoing benefit to the company
Okay, I see the quality of the oil varies quite a bit, depending on the process:
and:
http://www.theoildrum.com/node/3310
So is the EcoShale product equivalent to a light sweet crude?
Hi aadvark
It appears to be a high quality product.
"Ecoshale’s synthetic product has properties rated by the American Petroleum Institute (API) as 39 condensate oil and between 34 and 35 prompt oil with no fines, or impurities, in the oil."
Link
The process produces a shale oil with a much higher concentration of middle distillate than West Texas intermediate crude. Two synthetic shale oil products are produced: (1) prompt oil of approximately 29 API gravity; (2) condensate oil of approximately 39 API gravity. The oil and condensate produced with this process have no fines and have very low acid numbers.
http://tiny.cc/r1jow
I am thinking of buying shares in company called TOMCO energy. They re list in June on London Stock Market and they have done a deal with Red Leaf Resources. It is look good for a good profit.
It looks anything but good. This is a company registered in the Isle of Man ( a semi-offshore tax haven) that has already been delisted, has questions over it's past financial dealings, a company head who "dissappears" regularly, is in dispute with the Israel holdings partners, and is now looking to invest in a shale oil startup that is very risky indeed.
So, if you are the type of person who likes betting on the long shot horse that walks with a limp, then go ahead. But since you have been a TOD member for all of 20 minutes, and your first post is try to promote a shonky stock, I think you are looking to sell stock in this company that you already own.
There are plenty of other places on the Internet where you can "pump and dump" such companies - this is not one of them. If you haven't got anything meaningful to add to this discussion, then take your shameless stock promotions elsewhere
Paul
The Tomco Energy which will be relisted in London in May is a TOTALLY different outfit than the one that existed up to now.
They have a new investor Kenglo One / Chris Brown who will hold 26% of the shares.
Have a look at the web site of London Mining. Chris Brown was the co founder of London Mining. As CEO in four years he built up the company from a £25m mkt Cap to over £600m Mkt Cap and in addition was able to repay £250m cash to shareholders.
He left the company (London Mining) in 2009 on excellent terms, to persue other personal interests and is still a consultant to the company and also a substantial shareholder in London Mining.
His CV is excellent and he is still under 50 years of age. He has vast expertise in several areas of mining worldwide and he could transform Tomco Energy fortunes.
This is certainly not "a shameless stock promotion" to promote "a shonky (?) stock" as you might think.(the shares are currently suspended)
In mid May Tomco will be issuing a re listing document and I suggest that you take time to read it (on their web site www.tomcoenergy.com)before making such rash comment as above. Ref Leaf is not currently a publicly quoted company.
The Ecoshale process outlined in the article above could transform the oil shale industry. Tomco & Red Leaf / Ecoshale will be co-operating on the development in Utah and elsewhere worldwide.You may or may not agree. The majority of the above comments are positive towards the Ecoshale process.
Would Chris Brown with such a fine reputation, really want to get involved and invest £m's in Tomco Energy, without seeing some potential?
Unlike conventional oil exploration, it is not case of searching for oil as it is already there, under your feet, as oil shale.
s
Hmm, three new people join TOD within the three days that this article is published, and they are all very favourable or defensive of this company, Tomco energy.
This Chris Brown seems to have a history of being a wheeler dealer, his experience seems to be is raising money and doing share deals. Even the information you provide is all about share prices and not at all about anything of value actually produced.
In case you hadn't noticed, here, we are more interested in talking about energy, than share prices and deals.
That said, if you and your friends here are invested in this company, I wish you well. When you have real results/data/production to talk about, let us know. If you are just talking about shares, well, they are not "energy" at all, and I am not going to waste any more of my energy talking about them.
Hmm what exactly?
The fact that i registered three days ago is of absolutely no relevance.
Of course the discussion is about energy and oil shale.
But in case you have forgotten it was YOU who decided to criticise
Tomco Energy.You obviously took the time to look up them up somewhere
as you would not have known that they were an Isle of Man registered
company.
The simple fact that you described Christopher Brown as a "wheeler
dealer" just goes to highlight an element of ignorance on your part.
It is a pity that before replying you did not take the time to refer
to the web site of London Mining PLC where he was CEO. If you had
bothered, you would realise that your "wheeler dealer" comment sounds
so stupid.
s