Tech Talk: Using heat to refine kerogen from oil shale
Posted by Heading Out on March 28, 2010 - 11:01am
One of the problems with the oil (kerogen) in oil shale is that it is not mature enough (i.e. close enough to being an oil) that it will easily flow through the rock. In earlier parts of this particular theme, I have written about mining the rock and then heating it in retorts as a way of transforming the kerogen and recovering it for use. I have also, somewhat tongue in cheek, discussed using nuclear weapons to heat the rock so that the transformation can take place without moving the rock, while breaking the rock at the same time, and the unlikely potential for burning some of the oil within the deposit to power the transformation of the rest. While it might work in a heavy oil sand, is not likely to be realistically practical for the finer grained shales. But there are ways of adding somewhat less heat to the rock than using a nuclear bomb, and that will be the topic for today.
This is a continuation of the technical posts that I usually write on Sundays.
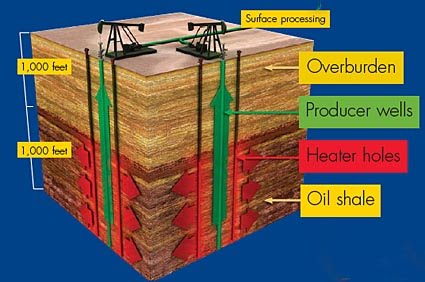
While I am largely going to bypass the use of nuclear power (apart from that of providing electrical power) in this piece, the potential use of nuclear power to heat penetrators that allow rapid drilling of weak rock has been partially demonstrated. As I have mentioned previously, Los Alamos National Lab, in looking at different methods for drilling, had come up with the idea of using a small nuclear reactor to provide sufficient heat to a ceramic probe that it would melt its way into the ground, pushing the molten rock to one side, and providing a glass lining to the resulting tunnel.
By the way, this has not been used to create the network of tunnels under this country in an idea beloved of some, it has been demonstrated. Not with a nuclear source, but with more conventional heating, Los Alamos drilled drainage holes at the Tyuoni pueblo plaza for drainage in 1973. A total of eight drainage holes were drilled at this archeological site in the Bandelier National Monument.
The first significant step in the Subterrene technology transfer program occurred when eight water drainage holes were melted with a field demonstration unit at the Rainbow House and Tyuonyi archaeological ruins at Bandelier National Monument in New Mexico in cooperation with the National Park Service. By utilizing a consolidation penetrator, the required glass-lined drainage holes were made without creating debris or endangering the ruins from mechanical vibrations.
At around the same time Dr George Clark, at what was then the University of Missouri-Rolla (now Missouri University of Science and Technology) had used ceramic electrical heaters in rock to raise rock temperatures enough to fracture and break out blocks of granite.
Field tests have therefore been able to take rock up to temperatures that are high enough to melt rock, using electrical heaters placed in holes in the rock. Which is a good introduction to the Mahogany Project in which Shell have been using electrical heaters to heat oil shale in place, to high enough temperatures that the kerogen transforms into a light oil. The investigation has been going on for some 25 years starting in the laboratory, and has progressed through an initial field trial.
Small holes are drilled down through the rock to house the electric heating coils, which slowly raise the temperature of the rock to between 600 and 750 deg F, at which temperature the kerogen will convert, depending on what is there, to a mixture of light oil and natural gas. These fuels can be recovered by drilling conventional wells into the rock, with typical depths at the test site being in the 1,000 to 2,000 ft range.
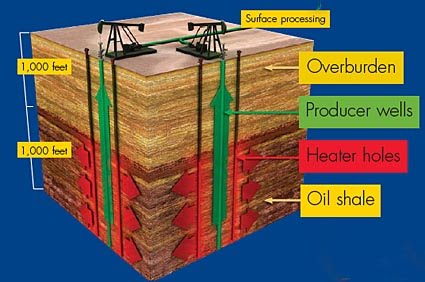
The field trial placed heaters in a grid over a 30 ft by 40 ft test area and found that a third of the volume produced was natural gas was produced from the lower grade layers of the shale above the layers with the highest concentrations of kerogen (the Mahogany layer) which produced the light oil.
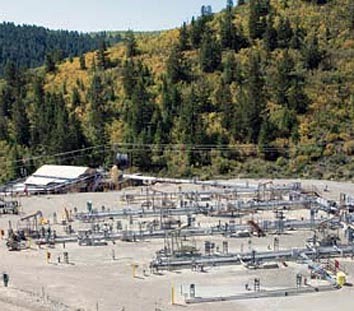
A total of 1,700 barrels of the light oil was recovered during the test period.
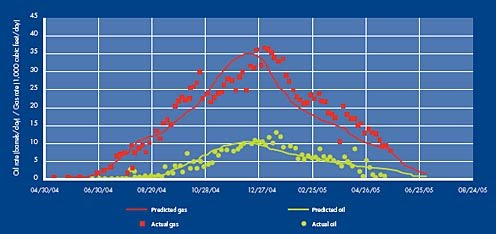
While the Bureau of Land Management has approved further sites for tests, the program is waiting to see what happens to the price of oil to determine whether or not the program will be sufficiently economically viable to move forward. At present this decision is anticipated to be in the middle of this decade, by which time it may be a little clearer whether the Cornucopians or some of the rest of us have been more accurate in our predictions on the future availability of sufficient oil to meet global demands at an affordable price. But it is the level of that affordable price that will decide whether the oil shale program is viable.
The costs of the project will not just have to cover the heating of the rock. One of the problems with the site is that there is some migration of water through the rock, and this can create two problems. The first is that it pulls heat away from the transformation process and the second is that it can interfere in the overall process itself. To stop the water flow (and concurrently the risk of transformed oil and gas migrating away from the collector wells) Shell has been looking into building an ice wall around the site to hold the water back.
Ground freezing is growing more popular as a tool for dealing with water underground. It has been used, for example, to stabilize the ground while the Boston Big Dig (the Central Artery/Tunnel project) was built and in stabilizing the ground for some of the underground stations in the London Tube network (including the collapse of one of the excavations). It has been used to hold back the water while uranium ore was mined at MacArthur River. Simply described, a dual pipe system is placed in vertical holes, and a freezing solution (usually a brine) is circulated through them, lowering the temperature of the rock to the point that the water freezes. Since the lowered temperature is distributed around the holes, there is no need to intersect any of the fractures, or voids, and the frozen water also helps to strengthen the rock where needed.
For the Mahogany Project test, which began in 2007, the freezing liquid was ammonia, and the test used a pattern of 157 holes drilled eight-feet apart, to a depth of 1,800 ft. The test removed the groundwater from within the well, but did not heat the rock to produce the oil and gas.
It will be interesting to see how this project turns out. It has been suggested that the technology would need a dedicated power source of some 1.2 gigawatts, in order to yield a production of 100,000 bd. Shell estimates it will yield 3-4 energy units for every unit consumed.
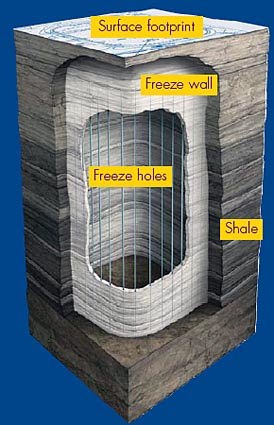
As usual with these technical posts, they can only briefly outline a process, if something is not clear please ask in comments, or if there is more information available, we all gain from reading of it.
Leaving aside (the very substantial) environmental issues for the moment, and just looking at the problem in the light of the dramatic changes in shale gas technology, then the most sensible approach would be as follows.
Find a source of natural gas, local if possible, piped in if necessary.
Use the recently developed fracking techniques to open up the shale. Pump natural gas and air down (different wells) and allow to ignite in a controlled burn.
The heat forces the light oil and natural gas to the surface.
Reuse some of the natural gas (if necessary) to continue the combustion process.
Sell off the oil and surplus natural gas.
It wouldn't work Kagiso. It would not be like heating the tar sands, where all you must do is get it hot in order to get it to flow. The kerogen must be cooked very slowly.
Shell in situ conversion process
There would be no way to control a fire for four years. Also the kerogen will burn as is, without conversion. Most of it would burn up in less than four years.
The long heating time was not mentioned by Heading Out above. An accidental omission I am sure, but still an extremely important omission.
The above ground mining process does not take four years of course, but in that process much higher heat is used. Which begs the question; why don't Shell use higher temperatures and therefore take less time? I don't know but I am sure it has something to do with the amount of energy consumed in the cooking process. That is the higher the temperature the more heat is lost due to convection. And of course the higher the heat the more problems you would have with the "freeze wall".
Ron P.
You make a very good point. I expect that investors into shale are going to want price guarantees, high ones.
I don't think the four years is actually needed to convert the kerogen. I think it's simply the time required for the heat to diffuse from the heaters to a sufficient volume of surrounding rock to make extraction feasible.
I could be wrong about that, however.
I think you are wrong about that. I Googled it and found several placed that sait the kerogen must be cooked slowly.
Ron P.
As per this paper:
So, it all depends on temperature. An hour at 500°C, or months at 350°C.
I take issue with Shell's EROEI estimate. All this is mighty infrastructure heavy. Factor in the embedded energy in manufacturing the electric heaters, electrifying a large production area, the requisite infrastructure involved in obtaining and shipping water, for oil extraction and cooling, and, finally, installing 1.2 gigawatts of continuous electrical generation capacity, as well as provision of the fuel required to maintain that production, I think we'll find this 3 or 4 to 1 ratio to be much slimmer.
Keep in mind that none of this is going to be a one-shot infrastructure investment either. There will be constant need to add new heater wells, with the requisite electrical transmission infrastructure put in place as well. Furthermore, the more you electrify, the more resistance losses you're going to accrue, and this will work to actually diminish the EROEI over time.
Until the technology advances to the point where we can ignore the embedded energy in such a huge infrastructure project, I think it's more likely that this method of extraction will never be economically cost competitive against other sources of energy, such as liquid fuel production from natural gas or coal liquefaction (as realistically this petroleum source will go primarily to transportation fuels) both of which also require huge thermal inputs, but which need not be dedicated electrical production.
This is all also in light of the 1.2 gigawatt per 100,000 barrel per day rubric. Currently, US daily petroleum consumption is something like 19 million barrels per day, so we'd need something like 200 gigawatts of end-use electricity to replace that with shale oil. If we were to say all this would be natural gas generated, even in the most efficient natural gas combined-cycle turbo-generators, we'd need enough gas to generate about 300 gigawatts of electricity to meet our total daily petroleum consumption with shale alone, a possibility we ought to consider given the rapid decline of conventional petroleum reserves.
Considering the amount of infrastructure and energy inputs required, I doubt seriously this will ever be economically viable over coal or natural gas liquefaction, or electrification of much of the transportation infrastructure.
I talked to s Shell engineer involved in this project a couple of years ago at a conference. They're not viewing oil shale as a primary energy resource. The goal is not to produce an "energy profit". Rather, they view their process as an efficient means to convert available energy from other sources into liquid fuels.
They've got a point. If their numbers are correct, they would get about three times as many barrels of shale oil per ton of coal as they would from a direct coal-to-liquids conversion plant. But the engineer I talked to said they were actually more interested in using surplus energy from wind and solar farms to drive the process, rather than building coal-fired power plants.
I see; use it to harness the surplus energy from wind and solar when they're really going and you get out of it what you get out of it. Sort of like a fuel of opportunity? When we have the excess renewable power from our current grid, I think the EROEI would probably make sense, since the turbines and solar farms had other economic/energy justification to be.
That seems a much more reasonable goal than building dedicated electric infrastructure just for this, but if that's their position with this technology, Shell may want to make it clear to policy makers, as many of them seem intent on counting oil shales among our recoverable reserves (a dangerous position for planning purposes).
If this is the case, and I suspect that it is, then EROEI becomes much less relevant and it becomes much more an economic issue. Assuming some sort of economic recovery, the success or failure of the project would rest on how quickly the transportation industry migrates away from dependence on liquid fuels. A large scale conversion to electric personal transport might be in the works. I don't know if there would be enough demand for liquid fuels, minus personal transport and possibly trucking, for the project to then be economically feasible.
Assuming no real economic recovery, I think the project is probably going nowhere regardless of EROEI.
We wouldn't even need a large scale conversion of personal transport to throw the economic calculus out of favor for this sort of thing. Imagine if every household in the US just swapped out the second car for electric and every diesel heavy truck converted to natural gas. This will have a knock-on effect in the availability of biofuels as a percentage of transport fuels and further stabilize prices.
At least in my arm-chair estimation, I'd imagine that electrification of even just 10% or 15% of our current personal transport fleet will have a much greater impact on primary energy consumption and alternative availability, especially considering that it takes a lot more energy input to make a gallon of gas than it does to make an equivalent amount of energy in electrical form.
At that point, you really would have to use run-off electricity that couldn't be sold elsewhere to power this system.
3:1 sounds like it would be on the high side. 2.5:1 sounds more likely.
And, that said, since this will likely be more polluting than anything this side of Canada's tar sands, don't we have to factor environmental clean-up costs into the EROEI?
Glad you are back, Dave.
One thing I was wondering about is water usage in the Shell Mahogany project. How does Shell use water in this project. I know I talked to a Shell representative quite a while back, and Shell said they weren't yet certain how much water use would be, but then quoted a number based on industry averages which I was thinking was 3 barrels of water for 1 barrel of oil produced.
Do you have any thoughts on where water is used in the process? Wouldn't water be a limiting factor in the arid West?
The Denver Post runs stories from time to time about Shell buying up water rights in NW Colorado. Western water law is complicated; it is unclear where the Shell rights will fall in the hierarchy. As this is a new application, the rights would normally be quite junior. Much of the water is over-committed; in dry years, the most senior rights holder gets their full allocation, then the next most senior rights holder, and so on, until the water is gone. People at the bottom of the pecking order may get nothing in those years.
The "new application" part is important. Generally speaking, rights are owned for a particular purpose. The most senior rights may belong to a farmer who uses the water for irrigation. That farmer cannot decide that he will instead use the water (or sell the rights to use the water) for a new industrial application and retain his place in the hierarchy; his senior right is only to use water for irrigation. His right to use the water for an industrial purpose would be junior to many farmers upstream or downstream of him who have used the water for agriculture longer than he has used it for industry. Some cases that get to court take decades to settle.
Gail:
One of the things that you have to remember is that oil will not suddenly decide to migrate to the recovery wells by itself. There has to be some pressure differential between the fluid in the rock and the well. Some of this might be provided by the expansion of the kerogen/oil at the higher temperatures, and some perhaps by an expansion of the rock, but the more conventional way of doing this is to use a water flood to push the oil into the well and generate/sustain the pressure that way. (Though thinking about it, with the slowness of the process, it might be possible to get by through using gravity drainage).
I seem to recall that one of the purported benefits of the process was the significantly reduced demand for water, but I couldn't tell you right off, where I got that information, or whether it is correct.
I read your post on using nukes... With the big drawback being Radiation... if you got past public horror... however, given that such craziness would only be debated in need of a "Crash Program"... In that spirit, id like to mention that I was wondering if you considered a FANTASTIC -CRASH- Program: "Rods From God" IE: http://en.wikipedia.org/wiki/Kinetic_bombardment
Hello Gail
I remember the reading a discussion about the water permit in that Shell was requesting up to 3 gallons for every gallon of "oil" produced. The DOE says the actual figure is between 1 and 3 gallons according to this reference:
Ref: http://twilightearth.com/energy/shell-to-divert-yampa-river-water-for-oi...
According to Environment Colorado, “Developing Colorado’s oil shale resource would have profound impacts on the northwestern part of the state, especially on the areas water resource. According to the U.S. Department of Energy, mature oil shale production of 2 million barrels of oil per day would require between 2 million and 6 million gallons of water per day for mining and processing.”
In a similar vein, water flow is another issue:
Ref: http://www.denverpost.com/breakingnews/ci_11867924
Shell is seeking a conditional water right to take up to 375 cubic feet per second, about 8 percent of the Yampa's average April-to-June flow.
Ref: http://en.wikipedia.org/wiki/Yampa_River
Discharge for At Deerlodge Park
- average 2,093 cu ft/s (59.27 m3/s) [4]
- max 32,300 cu ft/s (914.63 m3/s)
- min 1.9 cu ft/s (0.05 m3/s)
From the last two references above, note how Shell wanted to take up about 8% of the Yampa's average April to June flow [ed. Spring Melt] while the minimum discharge can be as low as 1.9 cu ft/s. They wanted to store the water for use during low flow periods. The average Shell was requesting is 18% of average flow which is significant in the dry climate of the western US.
The other issue not mentioned is what happens to the quality of the remaining water used in the process?
I remember hearing about Shell's water request before, but I didn't remember hearing it was as much as 18% of the average flow. Somehow, with all of the other needs for water, it is hard to see this getting priority. I would suppose that if there needs to be a 1.2 gigawatt electricity supply in the area (probably coal), it would need water as well. Or maybe that is part of the water they are considering.
Remember the 8% is for when the water is flowing it's fastest and the 18% is based on the average. So if they decide to work a project year round, the water consumption is much higher as a percentage of year round flow.
this is why i find the EROEI of all this so highly suspect... if i read that correctly they haven't tested the oven inside a freezer concept yet?
They need heat to cook the kerogen and ice to dam the water. This suggests use of heat pumps to pump heat from the ice dam area to the cooking area. I suppose the temperatures involved in heating might be too high for practical heat-pump operations? Any engineer types care to address this question?
holding rock at between 600 and 750 deg F surrounded by a freeze wall for years?
Rock is actually a fairly good insulant, so that once the temperature of the water is dropped to the level that is required for the integrity of the ice wall, and the internal water is removed (for the duration of the heating process) the natural insulation shouldn't provide much problem to heating the central section of the site, while keeping the outer perimeter cold. Typical ice wall formations generally are installed for months (unless it is an emergency freeze which would be shorter).
there is something about your explanation that I struggle with.. on one hand the natural insulation keeps the cold zones insulated but on the other is no impediment to conducting heat in the rock?... typical freeze walls have not been used to seal in a zone of heated rock
I would very much like to see (at least) a modeling of some heat pump solution
I am not sure if this is going to help or not, but when ice freezing is used, for example to build a wall around a planned shaft for a mine, the ice wall is located so that it creates a frozen barrier around the planned excavation, but does not freeze the rock within the wall and which is to be excavated (since that would make it harder to get out). Unfortunately, traveling today, I don't have any of my notes with me (I have taught this in a class) so I don't remember the exact thicknesses of the walls that are created, though they are somewhere around a couple of feet depending on how much strength you need them to give the wall and how deep it is. In the oil shale case all they are trying to do is to seal the permeability, so that the thickness will not be that great.
It doesn't take a lot of refrigerant to keep spaces cool underground (Kraft store their dairy products in the mid-West underground and use quite a small plant to keep it cool) because of the insulating properties, and those same properties will require some time to cook the oil over the radius required for each well (but remember that the heating tubes are spotted around each well).
Thanks to David Hagen (comments below) the presentations from the 28th Oil Shale Symposium are on line, and there is a good description of the Freezing test which Shell carried out. It describes the process, and the test results in a fair bit of detail.
cheers for taking the time I'll give that a read...
from your earlier point your basically saying that the insulating and conducting properties of the rock are manipulated by spatial design so as to optimize energy expenditures ...yes?
The pipes chilling the rock are supposed to be eight feet apart; presumably the rock is reliably frozen halfway to the adjacent pipes. The frozen zone would extend somewhat less distance toward the heated interior.
Now you have me scratching my head. How do you both remove the internal water in the ice dammed containment and pump water into the same containment to force the oil to migrate producing wells at the same time? You still have to contain the cooked kerogen, so the freeze wall must be maintained but water pumped in to push the newly cooked oil contacting the wall would freeze and pull the cold toward the center of the containment. Sounds quite complicated and inefficient.
Glad to see you are in good enough shape to post again H O, 'Tech Talk' is one of my favorite Sunday things to do even if I don't get to it till the wee hours of Wednesday ?- )
Heat pumping might actually work pretty well. But not from the ice wall to the rock heaters. The temperature delta would be too large for heat pumps to work well.
The way I'd expect this to work in production -- if it ever gets there -- is with a slowly migrating "hot zone" through linear strips of the oil shale. At the front of the zone, rock would be heating and cooking; the middle of the zone would have the production wells. The end of the zone would be the "cool-down" zone. Heat would be extracted from the "cool-down" region and pumped to the front zone for heating.
in effect cooling the front zone? what medium for moving the heat would be used?
Is it me? am I just stupid?
Why cooling the front zone? Heat pump outputs can be significantly higher temperatures than the temperature of their heat source.
unless my understanding of thermodynamics is way off base heat pumps do this by adding heat to the medium so it can flow back in.. a "top up" as it where
so if your using the same heat source for the extra top up in the front zone.... you see where I'm coming from here?
if you are using a separate input for the top up then its a two stage process (ie probably worse)...
from an ignorant layman of moderate intelligence POV (IE me) the real issue from an intuitive perspective (which admittedly may be very very wrong) is that the whole scheme is essentially an artificial replacement for time and absent geological mechanisms that would turn this stuff into usable Fossil fuel..
i doubt "mother earth" gets a positive EROEI either?
In response to the heat pump operation part of your questions, a heat pump uses sequential compression and expansion of a refrigerant to extract thermal energy from a low-temperature source during the refrigerant expansion phase, then compression of the refrigerant to upgrade the temperature of the extracted thermal energy to a temperature where it is useful. The amount of energy in compression needed to put out eg. 6 kwh at 70+ degF from a 40 degF thermal source can be as low as 1 kwh of electricity, 1/6th of the total energy put out, eg. COP 6 air source heat pumps are commonly available on the market. The figures for the deltaT's needed in an oil shale operation would likely be somewhat lower depending on the deltaT's required, but as Roger points out, might be surprisingly high given the heat source might be the fairly hot oil depleted rock no longer being heated.
I'm not getting won over here ..but then again I am an idiot. Unless heat pumps have transformed into some sort of anti entropy engine I don't get...
I'll shut up now and think about it for a while ;-)
It's not rocket science. At the rear of the migrating hot zone, you pump in (relatively) cool fluid and extract (relatively) hot fluid. But you can't recover all of the heat from the rock, and the fluid temperature is is not as hot as you want for heating rock at the front of the zone. So you add more heat before piping the fluid down into the heating zone. You can do that directly, using gas burners or resistance heaters, or you can use a heat pump to pump in heat from an external hot fluid source (e.g., cheap solar heaters).
"Oven inside a freezer concept" HAHAHAHAhaha!
Thanks Heading Out,
but like in your last posting about oil shale I keep bashing the EROI issue of this technology. You write:
According to page 4-22 of the Shell document Shell considers the
"Energy Balance – the ratio BTU’s out as oil and gas to the BTU’s input via electrical power", which is the electrical end energy, but not the primary energy needed to produce the electrical end energy.
So if you use for example an oil-driven power plant, which has an efficiency of about one third (with about two thirds being lost as waste heat) - and if you consider the oil needed for other purposes like transportation, mechanical work etc. then the amount of oil needed for the process is very close to or even below the amount of oil recovered.
Any objections?
I think there is a fly in that ointment somewhere Drillo. If they are using coal powered power plants in their equation then coal also has about the same conversion loss when it is converted to electricity. That is one third of the energy in coal is to electricity conversion with the rest being lost as waste heat. In other words those losses must be already figured in.
What would be different would be the cost per BTU of coal generated electricity verses the cost per BTU of "oil from the process" generated electricity. I would suppose the latter would be greater, how much I would not know.
Ron P.
The one opportunity I had to speak briefly with Shell systems analysts, they said that the assumption that gave them a 3:1 energy return was integrated cycle gas-fired generation with an overall 60% thermal efficiency. Coal-fired IGCC at 45% net efficiency makes the return worse, and at the 33% or so for conventional coal, things are looking pretty marginal, at least to me.
IIRC, producing a million bbl/day would require roughly the same amount of electricity as currently generated in Colorado. Xcel Energy is bringing up 750 MW of new coal-fired capacity at their power plant in Pueblo right now; one of the major headaches in that effort was acquiring rights to sufficient water to operate the cooling towers. The Denver Post reports regularly on Shell acquiring water rights out in NW Colorado; this appears to be process water, not cooling water for a power plant. You can air-cool things, of course, but that generally costs you thermal efficiency. You could build nukes, I suppose, where you don't care so much about thermal efficiency, but that's expensive and time-consuming. People talk about wind, but that's a lot of turbines and transmission facilities.
Personally, I suspect that the total costs associated with a million bbl/day oil shale operation will be outside the reach of the private sector. I'm not sure anyone short of the federal government could afford the investment.
You cannot air cool a power plant condenser, it requires water. Of course the water can be air cooled, in cooling towers, and the water recycled through the condenser. But you still have massive evaporation even then. That is why you see columns of water vapor rising from the cooling towers. And even when you recycle the water you still must keep fresh water gradually replacing the recycled water as evaporation causes minerals to build up in the recycled water. The minerals do not evoperate. Every steam plant requires massive amounts of water.
Nuclear plants are no different of course. They still boil water and pass the steam through the turbine to generate power. Their condenser requires the same amount of water as a coal fired plant.
Ron P.
There are a handful of (expensive) power plants out West that use dry cooling.
I'm not convinced even IGCC on its own is ready for prime time. New plants have proven prohibitively expensive to construct, and investors have been shying away from coal in general. And while most of the other comments have sidestepped the environmental issues associated with the process, it's worth noting what they are and how far we are from overcoming them. Even aside from the air and water quality issues associated with cooking and refining kerogen from shale, which I assume are substantial, IGCC produces a slag from the ash fraction of coal, as well as some of the organic residues, in the gasification process. The slag can be either vitrified (dramatically increasing parasitic loading) and then landfilled, or it can be discharged into a nearby body of water, presumably the same one from which the plant's cooling water was drawn. Existing IGCC plants have had a history of creating serious water quality problems. Keep in mind we have not yet figured out what to do with our 120 million tons per year (it would be a third of the total municipal solid waste stream if it were counted as part of it) of dry coal ash from conventional plants and still have the occasional nasty spill from time to time.
If you accept Shell's EROI and energy requirements estimates as reasonable, the process would require 1.2 GW of dedicated power generation per 100,000 B/D. Then we are talking about over 100 GW of dedicated generation just to replace 10 MBD or about half of present U.S. oil consumption. That is about a third of current installed capacity of coal power for base loading power. And I assume, as usual, shale would follow a Hubbert curve and the EROI would steadily drop and environmental impacts steadily increase as lower-grade resources are exploited, no? If we don't assume CC generation (or maybe even if we do), then the EROI drops into negative territory pretty quickly.
Not so sure if counting on natural gas combined cycle generation as an alternative to coal for the fuel source is really that viable. Production on this continent already peaked, prospects for importing additional LNG are grim, and we already use the stuff for so many other things, peaking generation, home heating and other domestic uses, industrial fuel, alternative vehicle fuel (expect this one to increase).
Of course, if you can capture enough waste heat from the plant, you might not have to rely on electric power exclusively (cooking kerogen out of shale is a heat-based process, right?), of course I'd imagine you need pretty high-grade heat, so you'd probably exhaust the exergy of your heat source relatively quickly, making that route not too much better than the 45-60% efficiency of combined cycle plants.
WastedEnergy, thanks for the very informative post.
That shocked me, I had never heard of it. Having worked in a gas/oil fired power plant for two years, (1980 to 82), I could not imagine how a condenser could possibly be air cooled. So I googled it. Now I am still confused.
Thermal power stations
A dry cooling tower? What are they cooling in the tower? And a radiator? It sounds to me like they are still using water in the condenser but then dry cooling the water in a tower or radiator, no evaporation loss, no makeup water needed. Is this correct?
And, according to Mcain's post they are counting on combined cycle gas generation to make it economical:
So scaling it up large enough to make a difference would mean a huge amount of natural gas would be required. It seems to me that if we had that much natural gas we could decommission all the coal plants and make all power plants natural gas combined cycle. But do we really have that much natural gas?
Ron P.
Ron you could think of your car as a dry aircooled engine. Sure water is used as a heat transfer medium, but the heat is lost by advective cooling through the radiator fins. As long as the water is closed cycle (and pre treated to remove minerals etc.) it is essentially recycled.
The dry cooling tower heats the air that flows through it.
But as others have said, overall thermal efficiency is reduced and capital cost is increased.
I wonder if solar thermal process heat could be used instead? That would at least solve the excess emissions and power requirement issues of converting underground marl into pumpable oil fields (which is what we are talking about here). Presumably if it takes four years to heat and modify the kerogen, an intermittient supply of heat wouldn't be a problem? I suppose if it were feasible they would have tried it. It would make it tougher to oppose on environmental grounds.
We put a dry air cooled tower in at the army's old power plant up here. The ice fog created by the old wet tower used to be a major traffic hazard for weeks to months at a time on the fourlane that essentially connects the army post, the air base and the oil refinerey community (located on TAPS) in between the two. The dry cooling tower was not a cheap project, and it takes some fair sized fans and pumps to run it but the old (very much reworked) coal plant's cogen system keeps the post heated the eight or nine cool to real cold months a year so shutting down the plant was not an option. Just thought I'd point up just what sort of facilities can afford dry cooling towers.
I used to do some maintainence work in power plants during shutdowns, years ago, and I always talked to the real experts- ther guys who lived on the road, as much as possible about the way things worked. If I remember correctly, a dry tower actually does cool water, with fans , by runnning it thru giant radiators-basically the same kind of radiator used to cool a car engine, just a few orders of magnitude bigger. I've never seen one myself.
If this process works, it will probably be likely that the freeze wall will be very long, and as nearly circular as possible, in order to surround the maximum working zone and get the maximum bang for the freeze wall buck.
The naysayers seem to be fixated on talking about enough juice to supply all our current consumption by this process -basically this is a frivilious argument as a practical matter. We will still have some other production for the indefinite future, and we can and certainly will learn to get by with a hell of a lot less-with whatever we DO produce, actually,plus maybe a little from Canada.
Only an idiot could believe that there will not be plenty of practical and necessary uses for a few million barrels later on even at an inflation adjusted price of two hundred or even three hundred dollars a barrel-such as in my diesel farm tractor.Without a doubt this would mean a REALLY crippled up economy, an economy that I would prefer to not even contemplate-but things would be even worse without that few million barrels of two hundred plus oil.
The exhaust from an internal combustion engine is considerably hotter than the working range needed, and if this is done on a large scale, I don't see any real reason why an industrial diesel or ng engine could not be used for mechanical power, and the exhaust passed thru the zone being heated, thereby considerably upping the overall efficiency.It need not bring the shale to the final temperature needed-just halfway in an area not yet heated would be fine-then electricity could be used to finish off the heating in that section. Holes drilled for the hot exhaust could be used for the electrical appartus- there would be no serious loss as these holes would have to be drilled anyway , just a few months or a hyear later.
Furthermore this sort of thing would most definitely be a fine way to load balance the output from some wind farms-all the excess juice beyond that which could be utilized in the ordinary way due to grid limitations could be diverted into the heating process ;and it is my understanding that there is going to be a lot of stranded juice because it is not practical to build the long distance transmission lines with enough capacity to handle the wind farm output on rally windy days-it costs too much. These lines will be built to handle some maximum amount of power that is actually available most days.If a local use cannot be found for the excess on really good wind days, some of the turbines must be shut down.
ps : As always please forgive my one fingered typing, it takes along time to correct ALL the errors.
Use associated gas from the extraction itself. You have the chicken and egg problem of getting the extraction started in the first place, of course. Dedicated rail lines could ship in coal at first and switch fuels later. Or you could dedicate some of the local NG production to shale.
Is there enough associated gas to run most of the process? I am assuming you'd get some lighter hydrocarbons when you cook out the kerogen, but isn't it mostly heavier, longer-chain stuff to start with, until you refine it? I don't know enough about the process to say how viable running the operation on locally produced gas would be, although it certainly seems like it would offer some promise for reducing the activity's energy consumption footprint, particularly if the distance of the mine from civilization or poor gas quality makes piping the gas uneconomical. Tar sand operations certainly make use of associated gas, but as I understand it they still require some supplemental gas to be piped in, and the EROI of refining tar sand is generally considered more favorable than oil shale to begin with, no? Gas-fired CC generation does seem to make the most sense to begin with rather than coal in light of the availability of this potential resource as well as other reasons, at least given the short-term outlook for gas prices.
The biggest limiting factors, even if there is a significant amount of native gas to use as fuel once the site is up and producing (presumably 4+ years after start of operations), would likely be those identified earlier, namely capital costs for both the mining/refining operation and the power generation facilities, and environmental concerns including water usage, again for both power generation and for the freezing and extraction processes used in mining the shale and particularly in arid or semi-arid Western states.
Given the Federal deficit levels are you sure that they can afford anything?
It's a matter of political will. Suppose that Congress did the following:
Not necessarily the policy choices I would personally favor, but at that point, excluding one-time recession-related expenses, the federal budget is effectively balanced, and assuming the recession ends, probably in surplus. At that point, the feds could exploit oil shale or build a dozen new nuke plants per year, or put up thousands of wind turbines. The question is what the US population collectively wants to do with their spending on "public" things.
Darwinian,
thanks for your comment, but I don't see a mistake here and I really think that Shell talks about the electrical end energy, so the energy loss in the power plant still has to be subtracted.
This means that
a yield of 3-4 energy units for every unit consumed
is only valid on site, whereas the overall balance (including electricity production) is rather around
a yield of 1 energy units for every unit consumed.
This also in line with an earlier posting from Nate Hagens:
http://www.theoildrum.com/node/3839
So are there still any objections left - or are now all objectors K.O.? ;-)
Energy Returned on Investment(not Energy Returned on Energy Invested)?
Here's an objection.
Let's say I 'invest' $1 of electricity to produce oil shale by Shell's method.
$1 will produce 10 kwh of electricity(at 10 cents per kwh) and by Shell's method that would produce on average 35 kwh or 119420 Btus of light oil which produces 101570 Btus of gasoline (.89 gallons) once it comes from the refinery. The wholesale price of gasoline is $2 per gallon(without taxes).
So to recap, $1 of electricity produced .89 gallons of gasoline or $1.12 per gallon.
The wholesale price of gasoline in 2009 is $2 per gallon.
Profit on Shell's oil shale = $.88 per gallon to me the investor.
Over the 180,000 mile life of a 40 mpg hybrid car worth $25000 new(closest thing to an electric car-Nissan's Leaf is $32780 MSRP) you would use 4500 gallons of gasoline worth $9000 not counting taxes. Total cost of hybrid ~$33000 or 18.3 cents per mile.
The Nissan Leaf using only electricity (24kwh/charge / 100 miles range/charge) would use $4320 of electricity. Total cost minus maint. and taxes would be $37100 or 20.6 cents per mile.
http://www.nissanusa.com/leaf-electric-car/index.jsp
So what makes more sense, using electricity to power cars or to heat up oil shale?
If we add the price of electricity $1.12 to the price of gasoline from conventional oil we get $3.12 per gallon wholesale.
In a hybrid the total owner cost would go from $33000 to $39040 or 21.7 cents per mile.
Does 1.1 cents per mile more justify no range limit or the 2 hour charging time?
Then there's the amount of CO2 generated. Based on the present electrical grid an EV would generate 30.75 tons of CO2 over its 180000 mile lifetime(39 tons of CO2 if all the electricity came from coal).
Conventional oil would produce about 44 tons of CO2 over it's lifetime.
Shell's process using coal fired electricity produces about at 13.0 kg/gal or 58.5 tons of CO2(51.2 tons if natural gas was used to produce the electricity).
At $100 per ton carbon tax, you would total $44,890 per life for 40 mpg hybrid versus $40075 for the Nissan Leaf EV--12% more.
Right now, oil shale gasoline is considerably cheaper over a hybrid car's 180000 mile lifespan than a comparable electric car unless you include the price of carbon.
majorian,
thanks for your calculation. I've also read calculations that conclude that already now the total cost of owning and running an electric car is more economic than that of a gasoline car - at least with (the higher) German petrol price and of course depending on the annual mileage.
But what I really mean is Energy Returned on Energy Invested
(see http://en.wikipedia.org/wiki/EROEI )
And so far there are no objections that considering all processes the overall energy recovery from oil shale is around zero.
Germany has 6800 million tons of brown coal and uses 200 million tons per year to make electricity(50%). A 34 year supply. And you are going to add a bunch of EVs?
Germany has 2 billion barrels of oil shale near Heidelberg and consumes 240 million gallons per year. A 8 year supply of oil.
You should be looking at your options.
The situation of Germany is desperate.
Combusting hydrocarbon fuels in a power plant to produce heat to "make eletricity" to be shipped down a transmission line to be turned into heat again to retrieve, process and synthesize fossil fuels to burn in a combustion engine to turn wheels to move humans.... is a crime against thermodynamics.
Where are Odums calculations on this? Anyone bother to calculate eMergy? There's not enough water for this, it's not scaleable.
At some point these hydrocarbons should be used to make much needed plastics, etc, and the price should reflect the difficulty (work - thermodynamic work) in acquiring them. Or not.
Oh yeah and I forgot the freezing part. How much of the formation does Shell (or hoomever) intend to freeze off???????
Are they hurting for "reserves" on paper?
This is not scaleable in any way.
I have the distinct feeling some folks have a horse in this race (outside the fact you burn fossil fuels)
Any one been out to the test site recently?
You know why thats on Shell's very own private property dont you????
headin' out..... ~~~~~
A area of 1/30 of an acre produced 1700 barrels of light oil and ~850 boe of gas in a one year test cycle(a really long time).
One boe of electricity will result in 2 boe of oil and 1 boe of natural gas.
One boe of natural gas burnt in an efficient combined cycle gas turbine will produce 1/2 boe of electricity.
That leaves 1/2 boe of external electricity to produce 2 boe of light oil.
So 1 mbpd or 2 quads/year would require 1/2 quads/year of external electricity(150 Twh/year)which could theoretically be produced by twenty 1Gwe nuclear/coal plants.
The amount of CO2 produced by CCGT without CCS at .4 tons per Mwh and by coal without CCS at .96 tons per Mwh would be 210 million tons of CO2 per year for 360 million barrels of oil per year or .6 tons of CO2 per barrel of oil which is higher than the tar sands at .1-.2 tons of CO2 per barrel syncrude. The US has a policy of not allowing unconventional oil production that produces more CO2 than
conventional oil production.
The amount of water is also a consideration. The 150 Twh of CCGT power would require 325 gallons per Mwh or 150,000 acre feet of water per year. The 150 Twh of coal power would require 577 gallons per Mwh or 265,000 acre feet. Together that's
415,000 acre feet or 3.2 Gb of water for .36 Gb of light oil.
It is important to note that desert hydroelectric dams are titanic wasters of water losing 4500 gallons per Mwh.
http://www.azwater.gov/AzDWR/waterManagement/documents/TheWaterDemandofP...
For example Glen Canyon Dam, which produced 3.2 Twh in 2005 evaporates about 1,000,000 acre feet of water
http://en.wikipedia.org/wiki/Glen_Canyon_Dam
One solution is to use abundant local renewable wind electricity to provide
the 150 Twh of external electricity( US produced about ~70 Twh of wind in 2009), which uses no water and produces no CO2.
With the price of wind electricity at 20 cents per kwh it would need +$100 per barrel oil to justify the investment.
The remaining 150 Twh from site gas produced electricity CCGT would emit .21 tons of CO2 per barrel, about the same as the tar sands.
Is this way of converting coal or nat gas into liquid fuel better than just running the coal through an F-T process or using the nat gas in a CNG vehicle?
Not sure if it was Rickover or Hubbert who suggested that using nuclear reactors to provide conversion of kerogen to liquid fuel was a way to use nukes to power our cars. It is an interesting concept in that the nuke plants would be on BLM land far from population centers which would use the evolved fuels.
No.
CTL Fischer Tropsch (or GTL) is 50% efficient, so a boe of coal equals 1/2 boe of fuel.
In a coal power plant 1 boe of coal equals 1/3 boe of electricity but
in the process above 1/2 boe of electricity produces 2 boe of fuel so overall 1 boe of coal produces 4/3 boe of fuel. Nuclear reactors producing electricity would be no more efficient than Shell with coal.
CTL,GTL: 1 boe of coal = 1/2 boe of fuel
Shell: 1 boe of coal = 4/3 boe of fuel
Modified insitu oil shale schemes(Oxy) try to do use gas to directly heat oil shale in the ground without converting to electricity but they caused groundwater contamination and produce a LOT of CO2.
One downside of insitu extraction is that the recovery rate is 80% which is slightly less than retort methods at 90-100%.
Burning natural gas directly in cars would also be slightly less efficient as
1 boe of natural gas = 1 boe of fuel.
I think you either misread the question or meant to say "yes", Major. Your calculations show that the shell process is, indeed, a better way of producing liquid fuel from coal or natural gas than running the coal through an F-T process.
Browns Ferry Nuclear Plant, Unit 1 generates more than 1,155 megawatts of electricity, enough to supply about 650,000 homes. That 1.155 gigawatts. So it would take about 1 nuclear power plant reactor for every 100,000 barrels of oil generated. Of course Browns Ferry has 3 reactors.
100,000 barrels is not that much oil, about 1/200th the amount used every day in the US. So the question is, is it scalable? Or, as I suspect, even if they do build a few power plants will it still be peanuts?
Ron P.
Your argument is beyond rebuttal, and caps the case that investment in negawatts is the soundest macro and micro economic policy for our time. Negawatts are scalable, in place and in time. They are not subject to the second law. They are carried on cultural wiring as well as on best technical practices. They are locatable by price and public policy. They provide a high return on investment for all forms of capital.
Negawatts aree wonderful and wonderfully cheap, but they are inherently unscalable-the law of diminishing returns kicks in hard pdq.
unless we are going to really go back to the energy stone age-figuratively speaking-we must have some new production to make up for declining oil fields.
OFM, we should keep negawatts separate from negabarrels. There is much scope for doing negawatts, the individual measures don't "scale" , but there are hundreds of millions of buildings where they can be applied (though not all at once).
negabarrels are harder, though not impossible. With a concerted, wartime like effort, I think we could reduce our oil demand (N America)faster than fields our declining.
We have some low hanging fruit;
> eliminating heating oil and remaining oil fired standby generation
> CNG conversion of trains
> CNG conversion of city and school buses, fleet vehicles, etc
> replacing city taxis with hybrids
> hybrid city trucks (garbage, delivery etc) these are being rolled out already
And some higher, but still reachable fruit:
> further improvements to vehicle fuel efficiency (mainly be reducing size/weight)
>CNG vehicles
>rail electrification
> densification of cities to reduce traffic demand. Once we have densification, we can then have functional transit.
And highest of all;
>intra and inter city passenger rail
None of this is to say we give up cars soon, and if you live out of the city (as I do, and I presume you do too) then you have little choice, but there is a lot than can be done, for relatively small inconvenience and expense.
The problem is that "system" changes (city densification, electric rail) require a significant up front effort, and, today at least, it's easier to look for or buy more oil, but this will not last much longer.
When you start looking at the oil shale prospects, all the negabarrel options start looking good.
I suspect that the EROI ratio of 3 or 4 to 1 is theoretical. 3 or 4 to 1 is not super attractive and it seems unlikely that actual results would be that good.
If you need oil to make high value petrochemical products or lubricants, shale sands might be worth doing, but if you are going to build enough wind and nuclear plants to generate 1/3 of the total US electric power generation, wouldn't it make more sense to power the vehicle fleet, trains, and heating directly with the electricity?
(Reference on electricity use in the USA http://en.wikipedia.org/wiki/List_of_countries_by_electricity_consumption)
The direct use of electricity becomes even more appealing if it is combined with systematic program of energy conservation AND energy efficiency.
I can't disagree with any of that. However, there will always be a need for liquid fuels for some applications -- airlines, off-road heavy equipment, and stand-by generators for example. Obtaining that liquid fuel from shale oil could conceivably be more economical and even more environmentally benign than producing it from biomass.
I'm not saying that that's the case. I really don't know. Just saying that it conceivably could be.
Just a word of thanks to you Heading Out. I am a casual TOD reader and I have really enjoyed this series of posts. And this post today really was fun to read.
- Lot of discussion around the EROEI and Shells estimate of 3 or 4 to 1. Seems consensus is in the discussion threads is that this seems hardly worth the effort.
- The ice wall discussion was great. I have been reading about this for a long time now but really liked your explanation and picture. Its really ingenious, I think, freezing the ground to hold the water back. Seems like a massive undertaking but has been done before.
I am no great environmentalist, but if I were, these projects to extract the gas and light oil would be very concerning. There is not much discussion around what this does to the lands around the drilling sites. And from the previous post, nuking the stuff out, that would definately set folks into orbit.
Anyway, thanks! Love it!
Presentation and details on Shell's Shale Oil process.
Shell's In situ conversion process – Factors Affecting the Properties of Produced Shale Oil. 2008, 28th Symposium
Shale Oil: Exploration and Development 2006 Justin Brady, Laura Kerr, Mike Potts. Senior Capstone Project
Further Oil Shale Presentations
PRESENTATIONS, Extractive Energy, Unconventional, 28th Colorado Oil Shale Symposium
Lookin for money....
Oil shales. Organic marlestone. Marlestone. Marl. Muddy limestone. Limy mudstone..... what is it?
You fellas need to do more petrography. The petrology is rather important.
All of the above. Marl is just short for marlstone. Marlstone is limestone with variable amounts of clays and aragonite (mud) mixed in. Limey mudstone is just another way of saying the clays and aragonite has a lot of lime in it.
Any of the above descriptions of Marl is correct. The fellows on this list do need to do any more petrography. The above terms are quite common among geologists. They do not have a problem with it; you are the only one that seems to have a problem with our language.
Ron P.
Sigh.
There is a big difference between these lithologies, they are not all one in the same. "Organic Marlstone" has been dropped lately in favor of "oil shale" which is imprecise and is a marketing term..
Marl is not "short for 'marlstone'" Marl refers to a "crumbly earth material, composed primarily of clay with magnesium and calcium carbonate."
Shale can be marly, and called "marlstone", but will have very different physical and chemical properties than non-marly shales, like the Pierre shale.
Shale: a fine grained detrital sedimentary rock formed by the consolidation of clay, silt or mud. It is characterized by a finely laminated structure which imparts a fissility approximately parallel to the bedding along which the rock breaks readily into thin layers....
Marl: a old term loosely applied to a variety of materials most of which occurs as loose earthy deposits consisting chiefly of a mixture clay and calcium carbonate...
Marlstone: an indurated rock of about the same composition as marl called an earthy or impure argillaceous limestone. It has a blocky subconchoidal fracture and is less fissile than shale...
The thermal properties are also quite different.
SO.... there are important differences between these lithologies and if your going to attempt to fracture these rocks in situ you need to know the difference.
Oh, I am a geologist, a geochemist actually, ex USGS resigned 2001 due to philosophical differences regarding the Iraq war and energy accounting. FWIW...
I do hope that helps.
Roger M
Also, in regards to "refining" kerogen.... kerogens are "upgraded" by the addition of hydrogen/s, not "refined". The end product is refined.
I'm looking at the title to this tech talk again thinking - apparently too much... but we might as well get it RIGHT.
1)"heat" is used to move the kerogens
2) the kerogens are "upgraded" with the addition of hydrogens and heat. The final product (petroleum liquids) are then refined into product,
2) we're not talking about "shale" here specifically this is an impure argillaceous limestone, an "organic marlstone"
3) there is by definition no oil in this material.
~~~~~~~~~~~~~~~~~~~~~~~~~~~~~~~~~~~~~~~~~~~~~~~~~~~~~~~~~~~~~~~~~~~~~~~~~~~`
KEROGEN (wikipedia):
Labile kerogen breaks down to form heavy hydrocarbons (i.e. oils), refractory kerogen breaks down to form light hydrocarbons (i.e. gases), and inert kerogen forms graphite.
A Van Krevelen diagram is one example of classifying kerogens, where they tend to form groups when the ratios of hydrogen to carbon and oxygen to carbon are compared.[4]
[edit] Type I
* containing alginite, amorphous organic matter, cyanobacteria, freshwater algae, and land plant resins
* Hydrogen:Carbon ratio > 1.25
* Oxygen:Carbon ratio < 0.15
* Shows great tendency to readily produce liquid hydrocarbons.
* It derives principally from lacustrine algae and forms only in anoxic lakes and several other unusual marine environments
* Has few cyclic or aromatic structures
* Formed mainly from proteins and lipids
[edit] Type II
* Hydrogen:Carbon ratio < 1.25
* Oxygen:Carbon ratio 0.03 to 0.18
* Tend to produce a mix of gas and oil.
* Several types: exinite, cutinite, resinite, and liptinite
o Exinite: formed from the casings of pollen and spores
o Cutinite: formed from terrestrial plant cuticle
o Resinite: formed from terrestrial plant resins and animal decomposition resins
o Liptinite: formed from terrestrial plant lipids (hydrophobic molecules that are soluble in organic solvents) and marine algae
They all have great tendencies to produce petroleum and are all formed from lipids deposited under reducing conditions.
[edit] Type II-Sulfur
* Similar to Type II but high in sulfur.
[edit] Type III
* Hydrogen:Carbon ratio < 1
* Oxygen:Carbon ratio 0.03 to 0.3
* Material is thick, resembling wood or coal.
* Tends to produce coal and gas (Recent research has shown that type III kerogens can actually produce oil under extreme conditions)
* Has very low hydrogen because of the extensive ring and aromatic systems
Kerogen Type III is formed from terrestrial plant matter that is lacking in lipids or waxy matter. It forms from cellulose, the carbohydrate polymer that forms the rigid structure of terrestrial plants, lignin, a non-carbohydrate polymer formed from phenyl-propane units that binds the strings of cellulose together, and terpenes and phenolic compounds in the plant.
Most of the biomass that eventually becomes petroleum is contributed by the bacteria and protists that decompose the primary matter, not the primary matter itself. However, the lignin in this kerogen decomposes to form phenolic compounds that are toxic to bacteria and protists. Without this extra input, it will only become methane and/or coal.
[edit] Type IV (residue)
* Hydrogen:Carbon < 0.5
Type IV kerogen contains mostly decomposed organic matter in the form of polycyclic aromatic hydrocarbons. They have no potential to produce hydrocarbons.
~~~~~~~~~~~~~~~~~~~~~~~~~~~~~~~~~~~~~~~~~~~~~~~~~~~~~~~
Van Krevelen Diagrams
Van Krevelen Diagrams show chemical evolution of kerogen and petroleum during thermal maturation in sedimentary basins, which is essentially what shell oil et al are trying to replicate on a much smaller scale:
source: http://www.nature.com/nature/journal/v426/n6964/fig_tab/nature02132_F1.html
What you are dealing with is over in that red zone in those charts above - not shown on these type of Van Krevelen diagrams:
I think it would be appropriate to have a tech talk on this stuff - kinda prerequisite....
source: http://www.geosci.monash.edu.au/heatflow/chapter5.html
Thanks for the lesson but hydrogen required here is minor less than is needed in Alberta plus in Colorado oil shale you get a valuable by-product, ammonia.
Colorado oil shale(TypeI,II kerogen) needs to be upgraded with hydrogen to remove nitrogen(2% by weight) and sulfur(0.7% by weight) impurities before being piped to the oil refinery. Hydrotreating is a normal oil refinery operation to remove nitrogen and sulfur from oil and take about 2000 scf(12 pounds) of hydrogen gas per barrel of oil. In tar sands, hydrogen is required to change tar into flowable oil, which is not the case with shale oil.
At Syncrude 800 cf of purchased natural gas, equivalent to 18 pounds of hydrogen gas is used in upgrading.
The waste nitrogen is removed as maybe 30 pounds per barrel ammonia which can be used as fertilizer. Anhydrous ammonia goes for $1000 per ton.
http://en.citizendium.org/wiki/Hydrocracking
Shale oil(heated kerogen) is oil and Shell's ICP shale oil was sent to Chicago refineries where it was processed as 30% naphtha, 30% distillate, 30% jet fuel and 10% heavy oil. Similarly, 270,000 barrels of Colorado mined shale oil(Tosco) from retorts in the 1970s was sent to Chicago refineries where it produced 10% naphtha, 40% kerosene(jet fuel) and 40% disillate(diesel) with 10% heavy oil.
Your 'facts' ignore the fact that US shale oil has been successfully produced experimentally for quite a while, though it remained economically non-competitive with conventional petroleum.
Peak Oil will change that.
POint is - you don't "refine" kerogen. You "upgrade it" then "refine" the product. AND we're NOT dealing with "oil shale" here. The stuff shell oil is playing around with out there doesn't contain oil nor is it "shale".
The terminol0gy here is all over thefuckingplace. Is this on purpose?
Yall need to define your terms BEFORE "technical talk". Put the definitions right up there at the top - every time - use a copy/paste "boilerplate" or sumsuch - so that there is NO confusion. Unless that's the purpose.
This new link you gave seems to work. I was having trouble with the ones listed above.
It seems to list a lot of material from both the 2006 and 2008 symposiums. Thanks!
So it would seem that no one here believe Shell's claim of EROEI of 3-4;1, and neither do I. Even Canadian oilsands, a much easier operation, have EROEI of 3:1.
One method that has not come up (or maybe I have just missed it in some previous discussion) is about using supercritical CO2 for both the heating and extraction.
This is used to enhance oil recovery in conventional fields, but at low temperature. For this application, you could heat the SCO2 to 3-400C (heat by any means, including concentrating solar) and then inject the stuff. NOt only will the heat cook the kerogen to oil, but the SCO2 will the dissolve that oil and carry it out. This is assuming, of course, that the SCO2 can migrate through the shale, but if the gas and oil can, then it should be able to.
If you build a gasification coal plant at the surface, gasify the coal and then water-gas shift the produced CO to CO2 + H2, and separate the CO2. The H2 is burned to produce electricity to run the SCO2 compressors (and sell the surplus) and the waste heat then heats the SCO2 to the desired temperature, and is piped into the ground.
Effectively, , what we are doing is a "reverse geothermal" process, which begs the question of doing a "forward geothermal" process -drilling down below the shale, to a depth where the strata is hot enough to provide the process heat. Inject steam/CO2 to the hot depth and then put it into the shale layer. But this too, would still be expensive, and there's no guarantee that the underlying strata are hot enough.
Anyway you slice it, it's expensive, and energy consuming, one way or another - it is to oilsands what they are to conventional oil. We will have to be very desperate when the day comes that we (corporate and/or government) think investing in this is a better decision than conservation measures to avoid the need for it in the first place.
Why burn it? ERoEI doesn't pertain to non-energy minerals. We can use the synthesized petroleum and distillates to manufacture plastics, medicines, etc. Of course, the cost of the products would reflect the effort required to extract, process, transport, and reclaim: expensive.
~George Carlin
One method that has not come up (or maybe I have just missed it in some previous discussion) is about using supercritical CO2 for both the heating and extraction.
This is assuming, of course, that the SCO2 can migrate through the shale, but if the gas and oil can, then it should be able to.
No. I don't think supercritical CO2 or steam can migrate thru 'marlstone'. Also the rock strata has the thermal resistivity of fire bricks, which are used to store heat in some electric resistance heaters so heat loss is not a real concern.
The process is very simple unlike CTL, just apply heat (equal to 25% of the final product) and overtime the kerogen is baked into light oil and natural gas.
If people are surprised at how much energy is required to make oil, they just don't understand how amazing oil is as an energy source.
Is it worth it to produce oil shale?
How do we get off oil?
Ethanol depends on land use and has 2/3s of the energy ensity of gasoline.
Natural gas has energy density issues(LNG's energy density is the same as ethanol, CNG is much worse) and does other things than oil.
CTL and GTL are worse than unconventional oil in terms of energy input.
Steam engines are less efficient than IC engines.
Hydrogen is clean but is made out fossil fuels or electricity at an energy cost.
Batteries lack energy density, are made out of unusual materials and have life cycle limits.
In the end, unconventional oil will be developed.
Majorian wrote "In the end, unconventional oil will be developed"
I think that is probably true - at some point, there will be a business for someone to do this, but one wonders what the oil price would have to be for that to happen.
Not too long ago, most people (though probably not the geologists involved) thought that shale gas would never be economical either.
You comment about steam engines merits a response. They are less efficient than IC engines, but of course, they can run off any fuel, liquid or otherwise, refined or unrefined, and can do so cleanly. If we are doing CTL or GTL, or biomass to liquid, the overall system efficiency is better to just use the raw fuel for a steam engine. However, that would require steam vehicles, and while there are actually some new steam ships and trains being built, I don't think we'll see steam vehicles re-appearing.
We will continue to make liquid fuels to fit our existing system, because that is far easier for any business, or government, than trying to change the system. And we don't even know, really, what we would change to. So, ultimately, if America is desperate enough, this will be developed, but the cost will be eye watering..
It seems most of this discussion has to do with a rather fixed test site. If it takes four years to get a site operating and at some point later it will no longer produce, a new site will have to be started every few days to provide a continuous flow of x million barrels of crude per day. The computations of electricity, water, ice and/or fire and then somehow provide the same would have to be done on a continuous basis for a variable geology.
If a site were started every four days, then 365 sites will be started before the first barrel of crude is delivered. No on really knows how much money all of this will cost or if the money will be available but the up front costs will be staggering. I’ll pass and give the dice to the next player at the table.
Question for Chem Eng people here. How much different is it to make a tire, plastic, latex paint, etc. out of this crude than say WTI?
Right. I'm willing to bet there is a power-law associated with enlarging the volumes of rock to be processed for extraction. IE, for every doubling of the volume of rock contained by the freeze-wall there is a corresponding quadrupling of the amt of energy needed to maintain the freeze wall - or something to that effect . I don't know and I wonder if any one else does. Should be pretty straightforward calculation.
The difference between burning the stuff for fuel and using it for plastic is the difference between Energey Returned on Energy Invested and mining. Much less upgrading is necessary for most plastics. Non-energy minerals are often substitutable and energy fuels are not. That is, one can substitute wood or metal for plastics and there is no sustainable substitute for liquid fuels at the rate we use them. Plastics are multi-use items and fuels get burned.
Actually I'd estimate the reverse, eg. the larger the operation, the lower the ratio of energy to the freeze walls vs. energy to the heating. Could result in some impressively huge installations actually ....
I disagree. Simply put, double the surface footprint and you have quadrupled the volume.
Eh? Assuming the bed thickness remains constant, doubling the surface footprint will simply double the heated volume. The easiest way to visualize this is with spheres. The ratio of a sphere's volume to its exterior wall area is
(4/3) x pi() x r^3 / 4 x pi() x r^2
On simplifying, we find that the ratio of a sphere's volume to its exterior wall area is
1/3 x r = r / 3
Using another simple geometry, a cube, its ratio of volume to its exterior wall area is
length ^ 3 / 6 x length ^ 2
On simplifying,
length / 6
eg. a very simple example:
a 1' x 1' square surface in a 2' thick bed excloses a 2 cu ft volume with a 10 sq ft exterior wall area.
and with the surface area simply doubled to allow math in my head:
a 1' x 2' square surface in a 2' thick bed excloses a 4 cu ft volume with a 16 sq ft exterior wall area.
So doubling the surface footprint of even an inefficient rectangluar shape with constant depth, increases the volume to 2 prior but only increases the exterior wall area to 1.6 prior, not 2 or 4 prior.
Thanks for correcting my haste and confirming that the surface area/volume relationship is not linear. However, You are totally missing the point.
What I suspect, but have no time to spend on (lazy lazy lazy), is that when the volume of material to be heated is doubled, the amount of energy required to heat it to the same temperature will more than double. Just a thought....
Well, I decided not to be so lazy.
Plot 1: 10'x10'x2'deep (100 square feet in area)
volume = 200 cu ft
Now, double the surface dimensions:
Plot 2: 20'x20'x2' deep (400 square feet in area)
volume = 800 cu ft
There ya go.
sorry lengould is right. You doubled the outside dimensions which then quadroupled the surface footprint. If you start with a 10' by 10' foot print then a 10' by 20' foot print would be double. Or if you want it square you would have outside dimensions that are square root of 200 for each side. Or in other words double the surface footprint of 100 square feet is 200 square feet.
Sorry guys. I Posted without thinking and I have no brain and no editor. Double the PERIMETER.... see what happens to the volume. This is about energy required anyway.
10'x10'x2'
double the perimeter:
20'x20'x2'
If you increase the perimeter (the freeze wall), the volume increases exponentially. This is important because the amount of energy required for a simple doubling of the perimeter of the freeze wall will require an exponential increase in the amt of energy required to heat the volume of rock.
...tripled the volume oop-s.
Just another vote of thanks to HO for the excellent technical series. Terrific.
It seems that a lot of the discussion about nuclear energy to replace Nat. Gas in Alberta oil sands which was heard two or three years ago has gone mute, likely due to a) the recent uncertainty in oil prices b) the rapid appreciation of the $Cdn. in which costs are incurred vs. the $US in which oil is sold. Conventional oil interests (OPEC) are well served by rapid market fluctuations creating long-term uncertainty.
http://www.cbc.ca/money/story/2007/08/28/alberta-nuclear.html discusses recent activity to get two 1200 MW reactors built in Alberta, offgrid, dedicated to oil production. More recent news articles discuss Henuset's company being bought out by Bruce Nuclear, the operator of eight reactors in Ontario, and the target location being moved into the Peace River area with Shell Oil as the partner. Hmmmmm... Also some discussion of EROEI for the process. "Approximately 1.0 – 1.25 gigajoule of energy is needed to extract a barrel of bitumen and upgrade it to synthetic crude. As of 2006, most of this is produced by burning natural gas.[74] Since a barrel of oil equivalent is about 6.117 gigajoules, this produces about 5 or 6 times as much energy as is consumed. Energy efficiency is expected to improve to 0.7 gigajoules of energy per barrel by 2015,[75] giving an EROEI of about 9. "
Good reliable background data on oil sands from National Energy Board at these sites.
http://www.neb.gc.ca/clf-nsi/rnrgynfmtn/nrgyrprt/lsnd/pprtntsndchllngs20...
http://www.neb.gc.ca/clf-nsi/rnrgynfmtn/nrgyrprt/lsnd/pprtntsndchllngs20...
Len, I think the main reason for the lack of talk about a nuke for the oilsands is that NG prices have dropped, and NG reserves in the US have increased dramatically, ensuring low prices for some time to come. With the oilsands operators shelving current expansion/upgrader plans, I can't see any of them wanting to spend the capital on a nuke.
That said, if I was Shell I'd at least do the feasibility study, just in case things change...
Interesting as well is that the Oil sands companies have been searching for years for a customer who could use the large excesses of electricity available from their co-generation steam plants. They've been talking for years about building transmission lines from Northern Alberta to California (Northern Lights - 3 to 4 GW)
http://www.transcanada.com/pdf/company/projects/NorthernLightsHVDC_LR.pdf
and I've never heard any discussion of sending the power down to the oil shale sites. I suppose that might get complex though, as they are market competitors, which probably explains why the SAGD operations which have the excess co-generation aren't talking to Shell at Peace River, who is planning nuclear powered extraction. Would it be very easy to extract steam from a CANDU6 or an ACR reactor?
A private firm named Red Leaf Resources controls thousands of acres of Utah State land, (not Federal lands). A proposed OIL SHALE project could be in production of greater than 5,000 bpd as soon as 2012. The beauty of the process is in its simplicity, a hybrid of mining/in-situ. Near-surface shale is mined with the shale rubble placed into a pit, the pit, called a capsule, is enclosed with a non-permeable liner and is roasted for several months. The void space from the rubble in the capsule allows for heat convection from hot pipes to efficeintly extract hydrocarbons. The capsule is small enough (a handful of acres) that it can be heated to 700-750 degrees F in months, not years as with the Shell ICP proposal. The capsule is a closed system, nothing gets in or out except for oil and condensate coming out of the capsule. Advantages are clean (no fines or bottoms) output, energy efficiency of 5.5 to 1, vs. 3.5 to 1 for Shell ICP, 2/3 less CO2 than surface retorts, very good project economics. Easily scaleable.
Since each capsule's life is a matter of months, immediate reclimation occurs by simply replacing top soil over the capsule and leaving the expendable pipes in the capsule and moving to the next capsule. The company says that the spent shale is non-hazordous. No permamanet structures are needed, all the equipment is skid mounted for easy movement to the next capsule. All of the equipment like bloweres and nat gas heaters are off-the-shelf. Up to 50% of the heat employed can be re-cyled to the next capsule.
Has anyone heard of this company? ROCKMAN commented on it based on an earlier post I made. I'm new to Theoildrum, and I'm not an energy analyst, can someone please explain to me why this isn't a potential game-changer? Thanks.
AS a process, the Red Leaf proposal is a bit like a an oil version of the heap leach used for gold mining. You trade off reduced capital cost for a lower recovery %, and not having to move the stuff again when you are done. It may well be as efficient as they claim, but the whole thing is conditional on being able to surface mine the shale. Once you have the stuff in the bucket of a front end loader, from that point even conventional retorting will work, and would pay for itself, but it's all a question of whether you can recover the mining costs.
If RL's process is economical for their limited area of shallow deposits, then power to them, but for the deeper shale, which is most of it, this process is not applicable.
Shell halts Colo. water bid in oil shale project
The Associated Press
Posted: 02/23/2010 03:47:40 PM MST
Updated: 02/23/2010 04:00:10 PM MST
DENVER—Shell Oil Co. said Tuesday it is abandoning its quest for water rights from a northwest Colorado river to develop oil shale production, citing delays in the project due to the global economic downturn.
Colorado, Wyoming and Utah are thought to hold 800 billion barrels of recoverable oil in shale. But critics of a federal management plan for developing oil shale on public lands say the process would use too much of the region's scarce water.
Shell was hoping to obtain water rights from the Yampa River. The company, which is the U.S. unit of Royal Dutch Shell, left open the possibility of pursuing the project in the future.
"The exact scale and timing for development will depend on a number of factors, including progress on our technology development, the outcome of regulatory processes, market conditions, project economics and consultations with key stakeholders," the company said in a statement.
Shell said the ultimate goal is to create an operation that is economically viable, environmentally responsible and socially sustainable.
The state was notified of Shell's decision on Tuesday, Colorado Department of Natural Resources spokesman Theo Stein said.
The last attempt to mine Colorado's oil shale, considered the region's richest, went bust when oil prices dropped and government subsidies dried up. People still refer to "Black Sunday," May 2, 1982, when Exxon shut down a $5 billion project near the West Slope town of Parachute, putting 2,200 people out of work.
The Bush administration in 2008 approved a plan to make nearly 2 million acres of public land available for oil shale development and finalized rules for commercial production, bringing protests from environmentalists.
Companies are still testing the best ways to tap the vast reserves, but commercial production is likely at least a decade off.
Read more: http://www.denverpost.com/business/ci_14456121#ixzz0jZxMD1kP
Depends on the sense of desperation.
The Chinese are building two ATP oil shale plants at Funshun in Manchuria.
http://www.ceri-mines.org/documents/28thsymposium/presentations08/PRES%2...
Thanks Paul Nash-- Read Leaf believes that they can acheive 80% of Fisher Assay...... They did a field pilot in late 2008-early 2009 that produced very promising results. Based on the pilot, they hope to be in production as soon as 2012. Another important advantage that I failed to mention-- no process water is used. Mining costs are pretty low as ONLY near-surface shale is mined, they don't go for the deeper shale at all. Thus Read Leaf's process could be used in combination with a deeper in-situ process at a later date.
Am I correct in assuming that no other surface OR in-situ process will be in commercial production in the U.S. in the next five years? That's my understanding of the oil shale space. Thanks so much for your response.
The operation would probably still needs some water relating to post processing, but otherwise, that is a big advantage for them. If they don't want to do any post processing, then I guess they could just take their crude condensate and sell that to a refiner.
Overall, I suspect the economics would be similar to surface mining of oil sands, though with more energy input to cook all that shale
As for your assumption, I think that's a safe bet. Even if someone else, like the Calgary outfit, gets something up and running, five years will really only get you a pilot operation, assuming you can get through the approvals process in that time.
Len, those reactors are all about producing steam, but you might as well run it through a steam turbine first, before using the steam for SAGD production. A reactor in Alberta would be a very controversial project
That DC line is a big up front investment, and as with a pipeline, becomes a bit of a chicken and egg, because its only worth building if the generators will use it, and those generators are only worth building if the line is going to be built. I'm sure that Montana and Wyoming would love someone else to build that line for them, but with all the uncertainty about carbon tax/cap and trade etc, who would invest in that right now?
It's hard to think that using electricity to heat the ground to extract the oil would be economical, but at a high enough oil price, it will be.
Since Shell has it's finger in both pies (oil sands and oil shale)they will know more than anyone else on the economics of both - it will be interesting to see where they place their bets in the coming years.
Agreed. I'd guess the water availability issue alone might be the determining factor.
Salt Lake City - An energy company with government approvals to launch the first significant U.S. oil sands project is trying to raise money to build a plant in eastern Utah that would turn out 2,000 barrels of oil a day. Earth Energy Resources Inc. has a state lease to work a 62-acre pit in Uintah County, where it has demonstrated technology that can extract oil out of sands using a proprietary solvent it calls environmentally friendly. But first, the Calgary, Alberta-based company says it needs to raise $35 million, and it acknowledged that could be tough because private equity groups turned skittish after the 2008 economic meltdown.
"Until we raise our capital, we are unable to proceed with the project in any major way, but the minute we do, we are fully prepared and committed to advance," D. Glen Snarr, president and chief financial officer, told The Associated Press by e-mail. Regulators say the company has obtained all permits necessary to open the first U.S. oil sands surface mine designed for producing bitumen. Snarr offered no timetable, but the company has demonstrated for officials, researchers and regulators that it has equipment capable of producing bitumen from the oil sands.
The Obama administration has been slow to lease large tracts of federal land for oil shale or tar sands development. Utah is more willing to lease its state lands, however, and Earth Energy joins a neighbor on state lands, Salt Lake City-based Red Leaf Resources Inc., which is working on a small scale to develop the region's oil-shale reserves. Red Leaf also is looking for investors to ramp up production. Wringing oil from hard rock or oil sands is technically possible, but nobody has proven it economical on a large scale yet, University of Utah chemical engineering professor Philip Smith said.
"Is there a future for this? There's a lot of hurdles to overcome yet." Smith said Utah's oil sands contain as much energy as those of Canada's massive reserves, but Utah's contain more nitrogen that can give off smog-forming nitrous oxides when processed. Earth Energy says refining removes the nitrogen before it becomes a problem. Utah's oil sands are lower than Canada's in sulfur, which makes for a "sweeter" crude that's easier to process, he said. Earth Energy Resources says its process leaves spent oil sands clean for disposal in the same pits where they are taken out.
"We will have the greenest oil sands mine on the planet," Snarr said. "There has been a reconciliation between the oil sands and the environment," Eisler said. "Oil sands are an absolutely critical reserve for North America." Some skeptics doubt Earth Energy Resources will ever get to work in earnest in eastern Utah, where it has snapped up leases on 6,000 acres of land. "The Uintah Basin seems to attract these speculators," said Steve Bloch, a staff lawyer for the Southern Utah Wilderness Alliance. "Is it environmentally or economically sustainable, or is this just a project to attract investors?"
The Uintah Basin of eastern Utah contains an established oil and natural gas field that has been worked since the 1970s, plus reserves of barely touched oil shale and oil sands. More accessible oil shale outcrops can be found in western Colorado, and Wyoming has its own share. Together, these hard-to-tap reserves are believed by government and industry estimates to contain a trillion barrels of oil. Starting in 2006, the federal government awarded small plots of lands for experimental works that have yet to produce any meaningful quantities of oil.
Attempts to extract shale oil stretch back a century, but with the rock holding the energy density of a baked potato, it's "folly," said Randy Udall, co-founder of the Association for the Study of Peak Oil and Gas USA. "If someone told you there were a trillion tons of tater tots buried 1,000 feet deep, would you rush to dig them up?" Oil shale is said to be "rich" when it contains 30 gallons of petroleum for each ton of rock, but pound for pound that amounts to only 1/10th of the energy of liquid crude oil.
Thanks again Paul Nash. You said the economics might be similar to that of mining projects-- but this process requires just simple surface mining and no retorts, multiple handling of shale, permament structures. And, in terms of energy input-- self sufficient after initial use of natural gas to get the ball rolling. 5.5 ratio of energy out vs. energy out, and that's all-in energy, not just process energy.
I have no investment or relationship with Red Leaf at this time. I am still looking for the smart people on oildrum to find red flags or fatal flaws. I've spoken with many oil people including petroleum engineers, and none have been able to "kill" the technology or process. Again, a simple, innovative process on paper, tested in field pilot a year ago.
Gunns, I don't doubt their technology at all, for both Red Leaf and Earth Energy. I am skeptical of the economics, that's all. "simple" surface mining is anything but, it needs lots of equipment to move the stuff around, and to break it out in the first place, since we are dealing with rock, not sands.
I think the best way to evaluate this is to compare with oil sands operations (surface mining) as much as possible, as they are a successful operation on a similar resource.
If we look at how things have gone in the oilsands we see that all of the projects have had to move to large scale operations, to get economies of scale. We also see that they are profitable, just, at current oil prices, because much of the original capital is paid off (Suncor and Syncrude have been at it for 30 years). BUt, all the expansion plans, for all of them, are on hold.
Now, one bright spot is that they don't need to build upgrading plants, refineries are wiling to take the heavy oil, so there's an avoided capital cost.
Applying all this to the oil shale, I'd say it needs some major innovation to be able to get around the scale issue, i.e. that a 2000 bpd operation can be profitable, instead of the 200,000bpd scale of oilsands.
Assuming their technology works, I'd be having a very careful look at the business plan before jumping in - how does it work with the optimism replaced with reality? Almost every alternative fuel business that has said "we are profitable at x $/barrel" has not been. As oil costs rise, so do all their input costs - the "law of receding horizons". Even oilsands are not immune - they used to say $50 was their break even, but they are shelving projects at $80, so i would say the real level is probably $70.
There are many, many innovative fuel production/extraction/conversion processes out there, but very few of them are economic at current prices(coal to liquids), and some will not be economic at any price (algae to oil). The trick is boiling away the optimism to see what economic reality lies beneath - like processing the oil shale itself!
Cheers,
Paul
The company claims that they are profitable with oil in the $30's. While I agree that optimism must be measured, I need a reason to take them to taks on that estimate. Comparing the company to mining projects in the oil sands may not be fair. Those projects require massive huge Terex trucks and shovels and roads and housing and treatement facilities and water and hundreds or thousands of people.
Red Leaf doesn't need anything remotely as extensive. They are digging up several acres of land to a depth of say 200-250 feet and putting the shale rubble back into the hole they dug. I realize it's more complicated than that, but since the process is repeated again and again every few months, the amount of equipment and people needed is far less.
I think that cost estimate is unlikely, given that the Utah deposits are much more technically difficult to extract than the Canadian deposits. I can get you a much better deal on a bridge in New York that might be for sale, soon...
The reason they use 400-ton trucks and 100-ton power shovels is because that is the cheapest way to do it. They found that out the hard way, by trying other methods first. There are huge economies of scale in these mining operations, and the bigger they are, the higher the profit margins are. Small cottage-scale operations are also feasible, but they require much higher prices to be profitable. Size matters in oil sands.
Which differs from Canadian oil sands operations - NOT. The main difference is that the Canadian oil sands have been in operation for 40 years, and have grown incrementally to an enormous scale, with enormous reductions in cost as a result. In constant dollars, the costs are a fraction of what they were 40 years ago. There's a steep learning curve on these projects, and it's an expensive learning process at the beginning of the curve.
Suncor's oil sands mine didn't make any money at all for the first 8 years, but now, 40 years later, it has turned Suncor into the biggest oil company in Canada. 40 years from now it might be the biggest oil company in the world (but mostly because the other big oil companies have run out of oil).
Rockymtnguy-- good points. if not this technology / process-- which is the best emerging surface or in-situ? thanks
In the Canadian oil sands, in-situ techniques are the wave of the future because 90% of the resource is too deep to mine. The SAGD process works extremely well and is cost-effective at current prices.
In the US oil shales, they need to find an in-situ technique that actually works, and we're several decades and several billion dollars of research away from having one. Failing that, the only option is surface mining, and oil shale mining costs are considerably higher than oil sands mining.
I found out that the Chinese actually have an oil shale process in operation, at a place called Fushun. It is surface mining, and has been going on for decades. The interesting theing there is that they use the spent shale for things like making bricks. shale makes good bricks, but has to be ground, dried, heated to over 600C (sound familiar?) then formed, heated further etc. They are also using some of the shale ash as clinker for cement making.
Basically, the Chinese have made a brickworks, that uses oil shale as the feedstock, so the oil produced is a bonus. This seems like a good idea, as the first steps of both processes are identical, and once you have removed the oil(kerogen) from the shale, you have hot shale that can then carry on in the brick process.
Seems analgous to corn ethanol plants, where they are only really viable if you make full use of the byproducts. You couldn;t do this on too big a scale, as there are only so many bricks needed, but the bricks wholesale for around $100/ton, and if you have mined ground and heated the shale anyway, seems like a good idea. The value of the bricks as a product exceeds the value of the oil produced from the same ton of shale!
So there's a potential way for a profitable surface mining oil shale operation, but not at huge scale.
http://www.thefreelibrary.com/Mining+and+utilization+of+Chinese+Fushun+o...
I'm arriving late to this party, but I'll comment anyway.
As to the direct water questions about water needed by the Shell process, yes, Shell has bought a large number of water rights in NW Colorado. They had proposed a reservoir near the Yampa River, but they recently withdrew that proposal and request for unallocated water rights in the Yampa. The proposal was to pump the river water into the reservoir rather than directly damming the Yampa, which is the last free flowing river in the Colorado Basin. Info here:
http://www.gjsentinel.com/breaking/articles/shell-withdraws-water-rights...
The electricity requirement is a sticky one, but there is an active proposal to build a nuke plant in Green River, Utah. There is really no reason to build a plant there other than to power the various shale and oil sand projects conjectured for the basin in the future. As pointed out, water is a huge issue in electricity generation, and these water numbers are NOT included in Shell's analysis of the impacts of shale production on water in the area. The Green River plant is asking to be GIVEN 50,000 acre feet of water per year out of the Green, which empties into the Colorado just thirty miles south of the proposed plant. Obviously, this would have an impact on the downstream users of the Colorado, which include Phoenix, Las Vegas and Southern California. 50,000 acre feet is a huge amount of water in the context of the Colorado River.
This is a pretty good summary of the water issues around the Green River plant:
http://www.hcn.org/issues/42.4/water-fallout