The Mining Disaster in West Virginia
Posted by Heading Out on April 7, 2010 - 3:41pm
The news of the death of at least 25 coal miners at the Upper Big Branch Mine in West Virginia is a reminder of the human costs that are incurred in the provision of fossil fuels. Although American mines have grown considerably safer over the years, the nature of the work can mean that when there is an explosion in a mine, that there are multiple fatalities because of the layout which is most effective for getting the coal out. It also underlines the higher costs that must be met when mining coal from underground operations, rather than the more visible, and criticized surface mining operations.
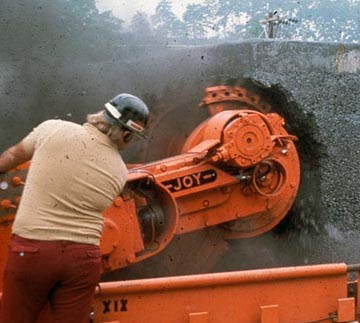
In the United States this is the largest mining disaster in more than 25 years at a mine that produced 1.2 million tons of metallurgical coal last year. Because of the pressures on surface mining operations Massey Energy were moving an increasing percentage of their production to the underground. The mine uses longwall techniques as the main means for producing coal and so I thought that it might be helpful if I reposted some of the information on that technique.
Part of the problem in controlling the ignition of gas in such an operation is that the mining machine breaks out the coal in relatively small fragments, by rotating a drum laced with picks against the coal face.
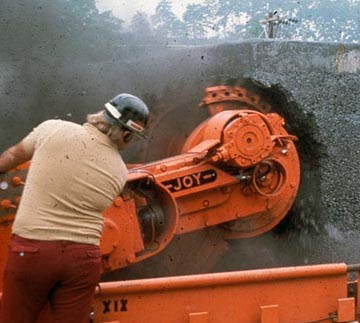
The fine crushing of the coal can lead to the release of methane gas (natural gas) that is found and formed with the coal. Levels of the gas are measured, and controlled by sending enough air down the face to dilute the level of the gas below that at which it is at risk of ignition or explosion. However within the space that the drum is carving out it is not always possible to get that air flow into the area to ensure that dilution is immediate.
At the same time if there are layers of rock within the coal, then the pick can rub against these and generate sparks, and heat up the rock to the point that it becomes hot enough to ignite any methane pockets that have been released. Once that ignition starts the very fine coal dust that is also a part of mining (as the above picture shows) means that this can also ignite, intensifying the resulting explosion. That becomes particularly deadly, given the geometry of the longwall.
And to explain that let me repost something I had written about before.
Back in the mid-1800's underground mining was usually carried out by crews of men and boys, where the coal was first removed by undercutting the coal seam manually with a pick, to a depth of about 3 ft. The bulk of the coal was then broken down to this slot and the fragments (ideally about 4-inches in size) were shoveled and hand-loaded into pit tubs, to be hauled away. A good day's work was about 20 tubs.
As the miners drove the tunnels (also called entries, headings, drifts, drives etc) into the coal they left pillars between the tunnels to hold the roof up. However in about 1870, and possibly in the Lancashire coalfield in the UK, they discovered that if they put these entries together, they could develop a way of getting all the coal out from that section (or panel). How could they get away with this?
Well there are two things that make it possible. Firstly, when you make a hole in the ground, the rock pressure that was applied to the rock (about the same pressure as the depth of the hole) has to move somewhere. And it moves just a little so that the weight of the ground over the hole is carried by the rock on either side. However, what happens if this additional load is too high for the rock and it fails?
Well if the rock were just a thin column it would collapse, but if it were thicker, then the weight would just move further into the coal. Now if we came along and moved the coal that had failed, then the hole would just continue to get bigger. But if we leave the coal in place, then the broken coal acts to confine the coal further into the solid. And this confinement gets higher, as the failing pressure continues to move into the wall. And what happens is that this confinement builds up the strength of the coal, so that at some distance into the wall (or face) the coal strength reaches a point that it can carry the weight of the ground above the working area. (For a simple analogy think of a deck of cards, which individually cannot bear weight, but when held together by a rubber band, or a carton, can support quite a bit of weight).
The second thing to know is that when a layer of rock breaks the rock lumps when piled together occupy more space than the solid rock. As a rule-of-thumb the bulking is about 60%. So that if we let the roof over the working area break and collapse, after we have taken the coal out, then by the time about twice the seam height of rock has collapsed, it has filled the hole where the coal used to be, and reaches up to the solid layers of rock above, to hold them in place. The confinement of the rock around each piece allows it to regain some strength, and so collectively the broken rock behind the working face (called the goaf or waste) will carry the weight of the ground from about twice the seam height, all the way to the surface, and with the other end of the "bridge" as it were resting on the confined coal ahead of the working face. (While the width of this bridge varies with depth, coal and rock strength etc, for an initial estimate you can imagine it as being around 500 ft).
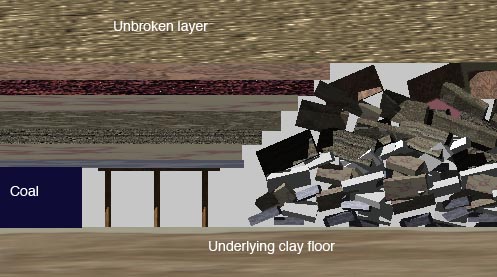
What this means is that the miner, working at the face, needs to support only the rock that is up about twice the seam height above his head (in those days women did not do the actual mining). And this could be done with relatively small tree limbs, called props. However, because the rock could break into pieces, the prop support would be distributed, by having a plank, or half split timber, as a bar on top of the prop. Putting one prop at each end thus gave a sort of "goal post" support. Thus, along the face, there would be, at about 4-5 ft intervals, these prop supports holding the roof up.(The coal is made slightly blue in the pictures to give a better contrast - sorry!)
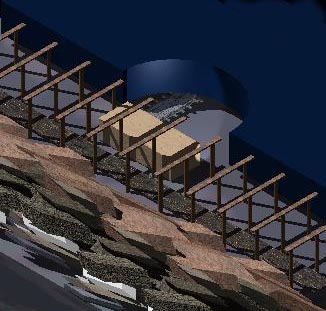
Now, to get the coal out it was possible to put in mechanical assistance. The first step was to use a machine, rather like a large chain saw, that was pulled along the face, undercutting the coal, to give that first free surface. At the same time holes were drilled along the face, about 6 ft apart, with a stick of dynamite in each one. After the face was cut the coal was blasted down between shifts (7.5 hours) then the collier shift would come in and each man would have about 10 yards of face to load the coal from, and to re-support. To get the coal from the face, a rubber conveyor belt was run along the back end of the supports that were in place before the blast, and the coal would normally not break that far from the face. As the miner shoveled he would also put in a new set of timbers, overlapping the old, and supporting the new working area. Typically this would take another seven hours, with an ideal seam height being about 4.5 ft. Above that the coal volume to move was much greater, and below that it got a bit awkward. (For example, below 2 ft thick you lie on your back, with a prop under your shoulder and shovel over your head - how would I know? Yes, there was a reason to go to college).

In the third shift, the men would come in and break down and move over the conveyor belt, and then remove the last row of wooden supports, bringing the roof down, beyond the new line of supports. [Smart folk would use a come-along and a chain to pull down the props, young idiots (guess who) would go in with an axe to chop them first].
The process needed mechanization and this required three different components to work. And these all came together in a period around 1960 - 65. Firstly there was a better way of removing the coal. The machine that was developed initially took the coal cutter power pack, and turned it on its side. By then putting a drum with picks on it, over the shaft to replace the cutter bar, the Anderton shearer was invented (named after its inventor). The drum rotated, and a shaped cover behind it moved the broken coal over onto the second part of the process.
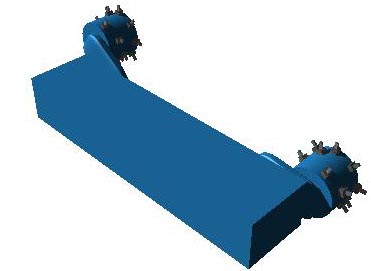
This is a rigid framed conveyor, made up of segments that can move against one another, and with rigid metal walls. The shearer can ride either on top of, or along side this conveyor, and load the coal onto it. The conveyor then carries the coal to the end of the face, and onto a second conveyor, that carries the coal out of the panel.
It is the third part of the concept that makes the whole system viable, because we now add the powered roof support. These are sets of hydraulic rams that ride on one plate of steel, pressing a second up against the roof. They are connected to the conveyor by a horizontal ram.
The mining process is thus that first the shearer moves down the coal face, grinding off the coal to a depth of around 2 ft. After it passes, the rams on the roof supports, in turn, are released, so that they drop away from roof contact. The horizontal ram is retracted and the support moves forward until it contacts the conveyor. It is then raised, and re-supports the roof. Each support moves forward in turn, so that the miners (who now include women) are always under a roof of steel. After the supports are re-established, the horizontal ram extends, pushing the conveyor over into the open space where the coal has just been mined. The exposed roof rock then collapses into the open space behind the back of the supports.
If one were to look at the operation from above, and with the roof removed, it might look a little like this:
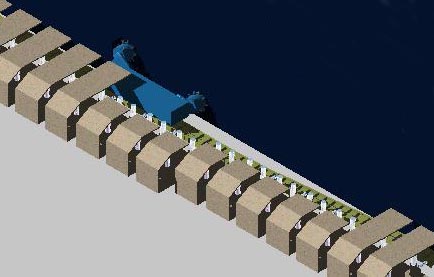
I have taken away some of the canopies of the shields so that you can see the conveyor snake after the shields move forward. The view closer in shows the conveyor and supports better.
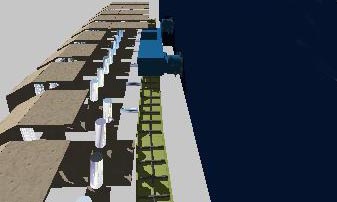
Because of the way the roof rock weight distributes, it is usual to drive entries out to the edge of the panel first, and then mine back to the main drive tunnels, rather than mining away from the mains. In part this is to keep the excess weight from acting on the tunnels the miners travel through. Because of the collapse of the roof as the coal is removed the panels usually start at the back of the section (known as a panel) and mine toward the main transport tunnel, with coal and people travelling in roadways on either side of the panel.
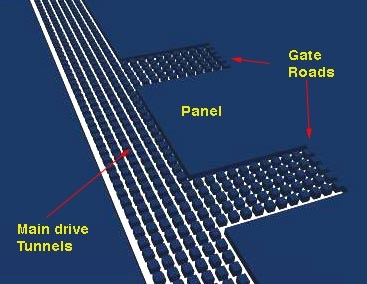
Over time the ground movement works to the surface, and the surface of the ground will drop, by some significant percent of the height of the coal removed, since the rock in the waste will crush and consolidate. This is called subsidence, and if the mining is carried out badly, then it can cause significant damage to surface buildings. However, if done properly, it should not.
I will cite two examples of the latter. Firstly in the height of mining and before North Sea Oil and Gas, Britain mined coal at a high rate of production, from where it was found. This included under the city of Coventry, which was at the time home to large manufacturing plants, with precision lathes. By back-filling behind the face props with the blown-in waste from the colliery treatment plant (called stowing the goaf), the waste was filled, and the ground movement minimized to the point that I only heard of one factory being closed for less than a week to realign their lathes.
The second example was in Duisburg in Germany, and a different problem. The town is a port on the Rhine, and over the centuries the river had eaten into the bed, so that the quays were becoming too high above the water for easy loading of the barges, and the town was losing business. They went to the local coal company and asked them to mine out seams under the harbor, and thus to lower the quays to bring them back in reach of the water. The miners complied, and lowered the area by over 11 ft. The area that was mined included highway overpasses, and a Shell oil storage facility in the middle of the river. The story goes that the tank farm manager went to the miners and asked them to tell him when they were going to start, so that he could drain the tanks as a precaution. They pointed out that the farm had actually already been lowered about 3 ft, as I recall the story.
As usual this has been rather a superficial description of a process, but hopefully it gives you more of a sense as to what goes on in a longwall mining operation.
Additional comment : It is possible to mine coal without using picks in a longwall, though it is a technology that has found much greater application in other industries, beyond mining.
Our thoughts and prayers go out to those in West Virginia at this time.
Mine too.
I do have a question about US coal supplies. I was just on conference call, where a guy was talking about the US once again becoming a net oil exporter, because of coal to liquids (CTL) technology. Other than the obvious problems (capital costs, net energy aspects, water use, etc.), it strikes me that a big hurdle is the following EIA chart, which shows US net coal exports, on a BTU basis, dropping, even with the uptick in 2007, at 12%/year from 1996 to 2007.
The difference between the US net export chart (above) and the Australian net export chart (below) is rather striking, especially since the US frequently described as the "Saudi Arabia of coal."
WT, it would appear that Australia should take the "Saudi" title, as it is the world's biggest exporter, and basically sets the world price for coal. The US is more like the "Venezuela" of coal, in that it has the largest amounts in the ground, much of it lower quality/high ash/high sulphur (like the Orinoco tar sands).
Australia has made energy exports a key plank of trade policy, while the US is much more concerned about energy (oil) imports.
I think it's probably fair to say that, with coal, Australia has taken the Texan approach and "just got 'er done"
6,000 trillion btu is equivalent to one billion barrels of oil, or 2.7 million bpd. The coal, at about $100/ton, is worth about $70m/day. If it were oil, at $100/bbl, it would be worth about $270m/day. Saudi Arabia exports about 8mbpd, worth $800m/day.
And, of course, the US imports 10.5mbpd, which is worth about $1.05bn/day.
So as impressive as the Australian graph is, it is an order of magnitude less value than the oil trade - probably why the US doesn't worry too much abut coal exports
Of course, using the same 6:1 ratio (which in North America is more like 20:1 on a dollar basis instead of BTU basis), US net coal exports are about 270,000 BOE per day (versus about 1,350,000 BOE per day in 1981).
The "Saudi Arabia of coal" story has clearly been debunked meanwhile.
See for example
http://online.wsj.com/article/SB124414770220386457.html
One reason is that the EIA's reserve assessment is based on a much higher coal price than the real coal price, which leads to hugely inflated reserve data.
But just as people and the media continued to believe that Iraq had weapons of mass destruction etc. so do they with the coal story. For example:
http://www.politifact.com/truth-o-meter/statements/312/
You can find much more details about coal in Richard Heinberg's book "Blackout".
It's interesting that even the EIA, at least circa 2006 when the following article was published, was projecting that the US would soon become a net coal importer:
http://www.csmonitor.com/2006/0710/p02s01-usec.html
Why coal-rich US is seeing record imports
They've jumped from 9 million tons to 30.5 million tons since 1999, as demand grows for low-sulfur coal.
Four or five years ago, the electric utility in San Antonio was importing South American coal because it could not arrange reliable rail deliveries from Wyoming. This will continue to be a problem -- perhaps a limiting factor -- if the US moves to exploit reserves such as the large ones in Montana. Lower BTU content of much of the Montana coal translates into more tonnage, which in turn will require more rail capacity.
I have both in public, and in posts here, argued against some of the positions that Dave Rutledge takes. It is a matter of how you count some of the coal that is in the ground. If it is not economical to mine it, at today's prices, then it is a resource. If it is economical it is a reserve, simplistically. Much of the coal in the United Kingdom that was economically mineable in the 1960's is not at the present time because there are cheaper alternative sources and fuels available. That will likely not always be the case and the resources will then move back into the reserve category. Much of that coal has not gone away, it is just not currently cheap enough to be mined.
False dichotomy. There is no necessary 1:1 trade-off between (a) destroying the environment through mountaintop removal surface mining, or (b) killing lots of miners by tunnel bore mining. The company involved with this disaster --Massey Energy Company-- has been cited for 38,997 safety violations in its 35 underground and 12 mountaintop removal mines since 2005. http://peoplesworld.org/union-buster-massey-energy-cited-2118-times-for-...
There is definitely a cost to *any* mining operation. However, it doesn't have to be massive loss of life or devastated landscapes when adequate safety and environmental standards are enforced. Unfortunately, with U.S. big mining --as with big banking and big insurance-- the regulators are held captive to the interests they are supposed to be regulating.
First, my thoughts go out to the miner's families.
But I truly hope that I am misunderstanding what you seem to be implying! I hope the bastards who are responsible for both the deaths of the miners and the ecological devastation caused by mountain top removal mining techniques are held equally responsible and do hard time for all of their crimes.
I doubt that they would seat me on either jury...
I should have put some of those comments in quotation, since they did come from an industry source. However if the nation needs coal, and it becomes (vide the EPA moves) impractical to get the coal from surface mining operations, then it must be produced underground. That is, by nature of the conditions, inherently more dangerous. The danger must be faced by those who go underground every day to produce that coal. I have worked at two mines where, during the course of my work shift, individuals have been killed. In both cases the individuals were in the lower levels of mine management. Some of the risks (such as the roof fall which killed one) are not as much of a risk in surface operations.
It is an apparent requirement that power be supplied at the lowest cost to the consumer. When I first came to this country that meant that mines could not afford to install the longer (and safer) roof anchors that they knew would increase safety, because of the competitive aspects of the industry. We have moved forward a great deal in enforcing safe mining practice in this country over the past decades (compare the fatality rates for example in China or Eastern Europe with those in the United States). Underground mining, however, is not without risk, and pretending that it is will not make it so.
What is the difference in death rates between unionized mines and non-unionized mines?
lots of answers to that here:
http://www.dailykos.com/story/2010/4/7/855068/-Want-Safer-Mines-Unionize...
and
The article used sort of a murky way of writing that up. It appears about 27% of the miners are union and they account for about 27% of the injuries but only around 20% of the fatalities. There is a good chance the safety programs in the union mines write up a far higher percentage of the injuries occurring than do the non union mines. Every safety program I have ever been a part of always stressed the fairly predictable ratio (within a large population engaged in the same type of work) between accidents as they progressed up the pyramid from near misses to reportables to lost times to fatalities. A higher fatality rate without a higher accident rate in the non-union mines indicates a higher percentage of their injuries go unreported.
Long wall has been used for many years in Australia.In most areas the subsidence has not caused too many problems that I have heard about.However,recently,a longwall operation South of Sydney has caused stream bed damage in a part of the water catchment area for the Warragamba Dam which is Sydney's principal water supply.Like most of the Sydney hinterland this is sandstone country.
Underground coal mining has severe safety problems due to gas build up and the coal dust factor.Over about 20 years from the 60s there were 3 mine explosions in 3 separate mines in the Moura area of Central QLD.A human toll of at least 60 if my memory serves me correctly.In at least one case it was deemed too dangerous to recover the bodies and the mine was capped.
Gas extraction from coal bodies would seem to be the best way to go if we must use fossil fuels.This also has problems with surface disturbance and water issues.
The sooner we develop nuclear power for base load electricity generation the better.This is by far the safest and cleanest option.Something that anti-nuclear lobbyists choose to ignore.
Amen (and cue the "no nukes --ever!" haterz).
Fine. Build the Nukes and we can (will) export the coal. BAU continues and all is well with the world.
The sooner we develop nuclear power for base load electricity generation the better.
Right. Because there is no profit motive that would result in corners being cut.
This is by far the safest and cleanest option.
Or to use the TOD manta:
Until it is not.
[points toward chernoybol, TMI, SA and the strike force that invaded a plant, the sleeping security guards in the US plant, et la]
1) You can clearly leave Chernobyl off that list, because profit motive of capitalists had nothing to do with the corners which were cut there. Equating Chernobyl to a typical N American reactor is worse than equating coal mining in China to coal mining in N America.
2) What exactly is your issue with TMI?
3) Security guards will always sleep when there are no REAL threats. Its the nature.
I'm not saying there is zero risk associated with nuclear power (except for weapons proliferation, which risk IS zero), just that the risks are manageable to a reasonable level.
Question. Would you still object to nuclear power if the reactor containment were buried 2000 ft deep in the hard stable rock of the northern Canadian Shield, the power was brought to you via HVDC transmission at the same price as coal generated power, the reactors were CANDU types designed to re-burn their spent fuel until its amount remaining were very small (see Quinshan operation in China), and things were pre-arranged so that the no people worked underground and if anything at all happened to the reactor then the access shaft is sealed with a slab of rock falling into place in the shaft and then the shaft is automatically filled with 1800 feet of wet concrete? If you would still object to that, then your objections are irrational.
I really wish I could remember the link, I think it was from the LFTR thread, where the standard for certifying safety of nuclear waste storage was changed to 1 million years.
"2) What exactly is your issue with TMI?"
Don't you remember the truckloads of horribly scarred bodies being removed from the surrounding area for months after the accident? Or the fact that no life has been able to continue in the area for decades?
Compared to clean, non-radiation spewing coal power, I don't see how you can support nukes.
/sarc
Thought the live link helped make your point better.
Thanks for this posting.
It may sound cynical, but safety is a matter of money.
And internalising the external safety risk (= imposing higher safety standards) can increase mining costs substantially.
For example according to an USGS study
and the EIA writes:
This means that coal prices have roughly doubled due to increased mine safety.
In the end it is up to the (elected) policymakers to decide what should matter more:
Miners' safety or cheap energy.
I would be willing to bet there were other issues involved in the rising price of coal in addition to the Black Lung taxes and new mine safety regulations.
This is a link to EIA coal prices, 1949 to 2008. It is hard to see that real (inflation adjusted) prices jumped much then. Coal prices seemed to jump on an inflation adjusted basis when oil prices went up a bit later.
I would be very doubtful if black lung is a cause of high coal prices, The number of men employed underground has fallen as production has increased due too higher productivity through mechanization. This would mean that the number of men exposed to the chance of getting black lung would be reduced and the number suffering also reduced. The other side of the coin though is that with increased mechanization you have to increase the air speed of the ventilation along the face to remove the dust. In the old days of hand getting the colliers always tried to just crack the coal face with explosives, and pull the coal down in large lumps. It was always easier to load large lumps of coal onto a conveyor than shovel fine slack. As most of the coal now is for industrial use there is no need for large lumps. Modern machinery tends to produce small coal and therefore more dust therefore the higher ventilation speed of the air to get rid of the dust from the coal face. This also means that the dust does not settle out of the air so quickly. It is always the very fine dust that is the cause of Black Lung disease. There are very many simple ways to reduce the dust and protect yourself from the disease. The simplest and cheapest is to use fine water sprays when I worked in the mines during the transition from hand got to mechanization, we had spays on the machine that used 11 gallons of water a minute and produced a very fine mist, conditions in the return airway were very similar to when the coal was mined by hand. Face masks with filters is another way, all of these are very cheap, compared to the cost of mining the coal.
Nice explanation, thanks HO. Appreciated the references to your underground youth. Your posts are colored into far more readable shades than they would have been if you had never actually WORKED for a living. Did you mine in Colorado? Great grandfather was my last ancestor to mine coal. Black lung got him, though his strike activity in Pennsylvania yielded a little better result than that of the poor suckers who went up against Rockefeller in CO. My tunneling was strictly in limestone, pouring five foot sewer mains about 1-2000 feet behind the blast face.
I'll won't put on the BGs but rather Genesis, 'Driving the last spike'--more hopeful--and hope for the best for those last four under Montcoal.
Thanks for the kind words - my background is that I am, at the least, a ninth generation coal miner (as far as we can trace back) with my ancestors mining coal just outside the village of Eglingham in Northumberland. (There is still evidence of those coal mines and the old cottages if you look closely). The family moved to Ashington several generations ago at the opening of a new mine. My father started his mining career there and I was born there, but my father moved up in the industry and so we moved around the UK. I served as an Indentured Apprentice in the National Coal Board, before going on to University, doing my face training on one of the last hand-won longwalls (Seghill) in the North of England. My grandfather would write verse in Pitmatic.
It looks rational (to me) that with a lot of planning and development, remote robotic mining should be do-able in these mines. I know that the hardrock nickel mines in Sudbury, Ontario have developed Teleoperation to quite a high level, with all equipment operators at the surface in offices. Given the much higher hazard level in coal mines and how highly mechanized operations now are, I'd have thought that should be an obvious application.
Telerobotic mining tour starts May 7 - Sudbury Mining
The first fully automated longwall face that I am aware of was the ROLF face put in by the National Coal Board in 1964. Films of those trials exist and have, at least at MO S&T, been transferred to DVD. (Ask the librarian). Room and pillar continuous mining machines are increasingly being operated remotely, however there are some significant operational problems with running a longwall face totally without operators. (A simple illustration would be a roof fall in the middle of the face that jams a support so that someone must go down the face to free it - having someone there to immediately fix the problem can save more than 15 minutes of down time, and with the machine producing perhaps a thousand tons of coal an hour, that is a significant delay. )
Coal seams are also not flat (though they may appear so in snapshots) and thus the cutting head positions must adjust to the varying position of the coal:rock interfaces as the machine moves down, and into the face. This steering can be handled automatically, but again it is a cost and maintenance issue.
It seems to me that coal burning is a 19th century technology that should be phased out in the 21st century. Australia doesn't have so many mining accidents but there are plenty of other negatives.. the coal ship run aground on the Great Barrier Reef, prime farmland to be strip mined, brine discharge from coal seam gas wells and so on.
It also seems like bald faced hypocrisy for Australia to encourage coal exports having signed the Kyoto treaty. CO2 from exported coal is about the same as domestic CO2 (including from oil and gas) at about 600m tonnes a year. I think foreign coal buyers should pay a $50 per tonne carbon tax equivalent. The host country can ask for the money back if they provide a list of cleantech projects it will be spent on.
Incidentally the recent upsurge in Chinese coal imports gives credence to the idea of an impending coal peak in China. Whether it will be as soon as 2015 I think the convergence of Global Peak Oil and China Peak Coal will be a significant event.
It seems to me that coal burning is a 19th century technology that should be phased out in the 21st century.
The 19th century idea is you heat water, make steam and then drive a turbine. This hasn't changed....now you have people wanting to split/combine atoms to make heat to heat water to make steam.
Welcome to the nightmare--
We will be having it on a regular basis from now on.
Actually, young women and girls were involved in coal mining in the 1800s. Emile Zola wrote a novel about this "Germinal" in the coal mines in Northern France. The novel is extremely sympathetic to the coal miners who were dreadfully exploited laborers and contains a terrifying account of miners being trapped under ground. Young women were in the mines in the UK. One of the early goals of the labor movement was to get women and children out of the mines. Cynically part of the movement to get women out of the mines was probably to increase the number of children they would bear who would in their turn be expendable as cannon, machine and mining fodder. Someone more knowledgeable than I about women's studies or labor movements could comment more.
Actually getting women and children out of the mines was largely done for humanitarian reasons, at least in the UK. One of the first jobs one of my ancestors had, as a child, was to sit in the dark, and open the ventilation doors when a putter (man hauling a coal tub - usually by that time with a pit pony) came along, and then shutting it behind him. Taking the women and children out of the mines initially posed great hardship to many of the families since it removed a significant portion of the family wage from the pay apron. It was the practice at least through 1842 . Of course today women work in mines both as workers and in management.
Like Heading Out, I come also from a mining background, and have worked in the mines and have completed a National Coal Board apprenticeship, great apprenticeships by the way. I have many similar tales to tell. Conditions were very bleak in the British mines during the 1830s. The changes in the law which brought about 1842 act, this was 8 years after the banning of all slavery in the British Empire was this accident at Silkstone in Yorkshire. I have copied it from an old 19th century book on coal mining in the British Isles,please enjoy and weep.
At Silkstone in Yorkshire on July 4th 1838 no fewer than twenty six children were drowned in what is described as “only a few buckets of water” owing to a panic. It had been raining hard during a thunderstorm, so much so as to interfere with the working of the engine, and the engineer gave the alarm to the banksman who incautiously shouted to put the lights out and come out of the pit. The children and people were frightened , not knowing what was the matter. A number of the children attempted to reach the surface by means of a futterrail, which formed a second outlet to the pit. A brook at the entrance to the futterail was overflowing into it, and this, with the water escaping from some old working, rush down the futterail and met the children who had passed a trap-door, against which there were driven by the water and being unable to open it, the water rose and occasioned the drowning of eleven girls and fifteen boys.
THE CHILDREN WERE BURIED ON 7TH JULY 1838
THE GIRLS IN THREE GRAVES:
CATHERINE GARNET (8)
ANNIE MOSS (9)
ELIZABETH CARR (13)
HANNAH WEBSTER(13)
ELLEN PARKER (15)
ELIZABETH HOLLIN (15)
HANNAH TAYLOR (17)
SARAH JUKES (8)
SARAH NEWTON (8)
MARY SELLARS (10)
ELIZABETH CLARKSON (11).
THE BOYS IN FOUR GRAVES:
JAMES BURKINSHAW (7)
AMOS WRIGHT (8)
GEORGE BURKINSHAW (10)
ISSAC WRIGHT (12)
SAMUEL HORNE (10)
WILLIAM ALLICK(12),
FRANCIS HOYLAND (13)
JAMES CLARKSON (16)
GEORGE LAMB (8)
GEORGE BARNETT(9)
ELI HUTCHINSON (9)
JOHN SIMPSON (9)
JOHN GOTHARD (8)
WILLIAM WALMSLEY (8)
JAMES TURTON (10)
So sad to see a blatant example of rich bosses putting profits over workers' safety.
So sad.
And, I think I agree with what I heard on the radio yesterday: no one is going to prosecute those bosses for this.
So sad.
They'll get away with it just like the bankers with the bailouts, like Bush, Cheney, and Rumsfeld, like so many others do anymore.
So sad.
Longing for the days of Daniel Ellsberg and the Pentagon Papers; the days when whistleblowing made a difference.
Hi Dave,
Thanks for a great post.
Massey's blankenship:
Just this:
I admit to being a regular monitor of the MSM. Kind of keeping my finger on the pulse of what's programming our society. Since this incident, there has been an obvious uptick in the "clean coal" commercial programming, as if to say that these disasters represent acceptable losses, much the way that we glorify wars for national security (energy) overseas. Heros are created, and BAU can continue as before.
Rest easy folks......the soldiers and coal miners have your back. Think about that the next time you turn the lights on or start your car.
Heading Out said:
Interesting, but this translation of a German report from 1966 (pdf) says (about the oil tanks - on a dock, not island):
"Particularly intensive precautions had to be taken with storage tank installations.
...
As a result of changes in length due to tensile and compressive stresses, it was necessary, in spite of the use of expanders, to alter the conduits from time to time."
BTW, the max subsidence was 2 meters (6 1/2 feet), not 11 feet.
(1.8 meters original plan).
The 3 coal seams were at depths of 90 - 500 m.
Though, "As soon as the first subsidence began, it was obvious that a constant and very careful supervision of the harbour installations would be required.",
nevertheless,
"The coal under the harbour was extracted with such a high degree of skill that the operation was a complete success for the Duisberg-Ruhrorter Hafen AG, except for the few limitations described above. It should again be pointed out that the mine surveyors performed exceptionally well, directing the mining operations and predicting with great precision the subsidences and their consequences, so that by taking preventive measures, it was possible to keep damages within reasonable limits."
When I wrote the original text I was quoting from a journal article that I had in front of me. I have retired and given all those journals to others so that I cannot at the moment dispute the German report. I had originally heard the presentation given at a conference, which is where I remember the story from. (And hence there may have been some artistic license in the telling). But looking through the document it has some information that I did not. Thanks for providing it, which I will pass on to the colleague who now deals with this.
Massey to up coal output at other mines after blast
http://finance.yahoo.com/news/Massey-to-up-coal-output-at-rb-1449534218....
talking heads said this am that there were indications that a fire was still active. the rescuers have switched to pumping nitrogen instead of air.
have you checked your smoke/fire alarms lately ? some consider these a nuisance.
This is really a question to Heading Out.
Explosions come from methane and/or coal dust mixing with oxygen. The proportions must be in a range. Methane and coal dust cannot be eliminated from the mining of coal. But what about oxygen? Could the miners breath with scuba-diver type portable breathing devices and the mine be flooded with dry nitrogen? Although the depth can be a few thousand feet, the ambient pressure seems to be very near surface level atmosphereic pressure, so there should not be a problem with 'bends'.
I sure I am not the first to make this suggestion. What are the known problems, other than a reluctance to innovate?
While there have been lightweight helmets that have been tried to overcome some of the problems of miners being poisoned by bad air, the problem of carrying around your own atmosphere is illustrated by the mine rescue crews that go into the mine. They do carry their own breathing equipment. It is, however, a little heavy and can only sustain breathing for four hours. (This is partly why rescue teams have a limited range of action since part of the time must include the travel time back out of the mine).
The amount of effort that a normal miner makes during the course of a shift would make working with a breathing apparatus of this type very difficult, and significantly lower production. There are more gains from automation of the equipment, and from draining the methane from the face before the machine arrives. (One can also use high pressure water as the cutting tool to obviate heating spots).
You mentioned high pressure water cutting, something that entered the mines a century ago, and Yorkshire miner talked about the spraying of a fine mist to settle the dust. Is there a reluctance to bring extra water into contact with some coal because it would be retained and lower the quality? Or is just very expensive to bring in and remove water from the operations and thus not a popular solution for alleviating some of the difficulties encountered mining underground? Or is water used a great deal as an underground mining tool? When I was building tunnels water was pretty much just in the way, though after we pumped enough of it out for a long enough time some local wells went dry.
I'll just add a little to what HO already said. In HAZMAT training we used self contained breathing aparatus, though only about a twenty minute bottled air supply. A much larger bottle would have been quite cumbersome and the effort to carry it around would have burned a lot of the extra air in the bottle. Anyway, even that twenty minute bottle lasted maybe fifteen minutes for me. It takes a lot of training to get the most out of a limited air supply.