Coal Mining - Mechanized Room and Pillar Mining
Posted by Heading Out on June 27, 2010 - 10:43am
This is the next in the series of Tech Talks on Coal Mining, and I’m now going to move more into more recent mining, rather than dealing with the historic background of the recent past. Specifically I am going to describe how the “Bord and Pillar” mining of the olden days transitioned into the much more mechanized mining method, known as “Room and Pillar” mining – the most popular method of mining in the underground mines of the United States.
To briefly review where we have been, coal has been mined for centuries. It is usually found as a relatively flat layer of soft rock, often under a layer of relatively soft shale, and just above a second layer of shale. These then form the roof and floor of the tunnels, or headings, through which the mine is developed. Because the shale is often softened by water, this can pose longer-term problems. But one can, simply, think of coal as being the layer of cream in the middle of a cake. And one of the tricks is to carve out the cream without the top half of the cake falling on your finger. In earlier times it was, unfortunately too often a method of widen ‘til it falls.
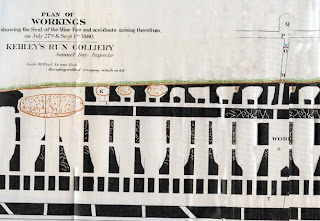
The most common method of mining started with driving tunnels, and then intersecting these with “cross cuts” through the pillars of coal left to hold the roof (the top half of the cake) in place. As I showed in an earlier illustration (above), since it was easier to mine from free faces then the solid, the initial rooms driven were often widened, until the roof fell in. And, over time mining practice came to narrow those initial tunnels to around 10 – 15 ft in width. They were initially smaller, when hand won, but with the advent of more mechanized mining the width grew greater, and required more support in the tunnel itself to hold the roof immediately above.
At the same time, as the mine workings moved away from the shaft (which took coal out of the mine, but also supplied fresh air to it) it became more critical to steer the air entering so that it reached the working areas of the mine, and then could be sent back to the surface. Without that proper circulation of air, the gasses which the coal would give off, including methane (natural gas, carbon dioxide and carbon monoxide) this could well be fateful. And so the miners began to also build temporary or permanent “stoppings” or walls across some of the abandoned tunnels to steer the air currents down the tunnels in and out of the working area. To separate the two flows (in and return) between the main roadways permanent “airlock” types of walls would be built with doors between so that one could cross from one passage to the other without interfering with the passage of the air.
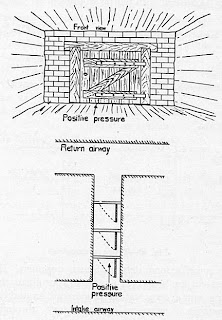
As the mines developed miners learned, sadly the hard way, that just having one shaft or access into and out of the mine was not safe. A major accident occurred at New Hartley in Northumberland, UK in 1862 where the main beam for the dewatering pump fell into the shaft, blocking it. The 204 men and boys in the mine, virtually the entire working male population of the village, were all killed, It was a result of those deaths that legislation was passed that required that there be two separate ways to get out of a mine. Where the mine is deep underground this means that there are generally two shafts, or more from the workings to the surface. As a small piece of family history, my father was manager at the successor to that mine, New Hartley, shortly after I was born.
There was also a novel of the disaster, sadly out of print, called “The Darkness in the Morning” by Gordon Parker. It tells of the different pressures on the miners, the management and the owners to survive, and how, in part, some of those decisions led to the disaster.
But air does not move by itself. There has to be some form of power applied to move it, and before there was electricity there was heat. So, if you have two shafts then at one stage, to power this air circulation, they would light a fire at the bottom of a shaft, and this would draw the air to it, and from the mine. It was given the name furnace draft ventilation. In other cases the shaft was divided, with fresh air going down one side, and the heated return air going up the other.
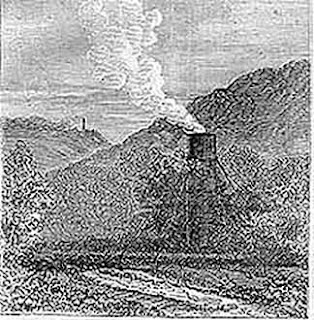
Once the air was moving into the mine it would toward the workings as Intake air, or fresh air, travelling down the main transport tunnels or drifts to get there. The worked out rooms on either side would be blocked off permanently, until the working area was reached. Here the air had to circulate across the rooms that were being mined, and then, since this air would now contain the gases and dust released from the mining process, it would be moved by temporary stoppings to the Return air passage, and thence out of the mine.
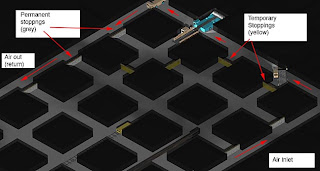
Initially men broke the coal from the solid with picks. When they worked this efficiently, a man can be very effective in breaking out the coal (about 4 joules/cc specific energy, for those that are interested. The machines mine at around 1,000 joules/cc of coal removed). But man is slow, and so the manual pick was replaced with a mechanically swung version. Initially a large number of picks were set into a chain, rather like a large chain saw, and this was used to undercut the coal seam about a hundred years ago. Then holes were drilled into the coal above the slot, filled with a stick of dynamite, and the blast would break the coal into pieces, that the miner could load into tubs.
From this came the idea of putting lots of these chains together to form a belt, wound around a rotating drum, that would grind away coal all across the face, without the need for the explosive. In other words the coal could be won continuously, without stopping to clear the explosive gases, It was found that the picks did not have to be right beside one another but could be spaced, and this was the birth of the modern continuous miner.
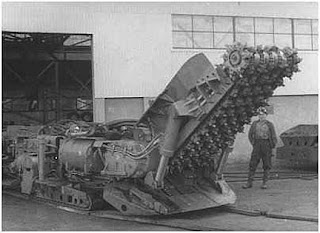
If the pick points are spaced around a drum, with a drive motor inside, and laced into a pattern that moves the coal towards the center of the machine, the drive becomes much simpler. The drum itself is mounted above a gathering arm loader apron, so that as the coal falls it is swept into the center of the apron, and falls onto a conveyor that carries the coal through the machine and into a shuttle car that is located behind the machine and can carry the coal from the machine to a nearby conveyor. The machine looks something like this:
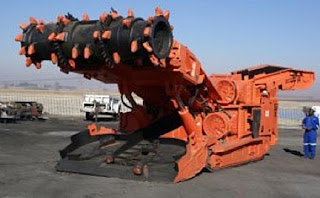
(The pictures that follow were generated using Strata 3D and portray, a simplified view of the parts of a working section of a relatively modern mine starting with the continuous miner.)
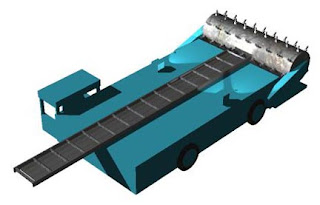
The continuous miner grinds the coal ahead of it as it moves into the solid carving a tunnel or heading as the coal is removed. You might note that there is a protective cab at the back of the machine. The machine can only go forward until the miner is under the last row of roof support. The machine must then back out of the heading, and move over to a second heading while the section that has just been mined is supported. At the same time the coal is being loaded from the conveyor onto a small shuttle car that will move the coal from the heading to the nearby continuous conveyor belt.
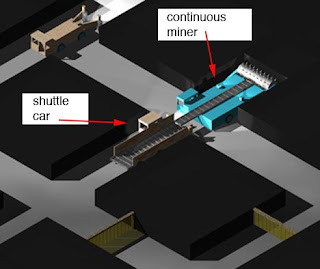
The picture shows the continuous miner starting to drive a heading while loading coal into the shuttle car behind it. (I have not shown the power cables or, people). Normally a section may have two or three of these cars, so that while one is carrying the coal from the continuous miner to the main belt conveyor transfer point, the second can replace it and catch the next batch of coal to come from the machine. In the heading above that being driven there is a machine with two drills on extensible booms. This is the roofbolter. (Note that the seam is about 6 ft thick in the model and I have taken away the roof so that you can get an idea of the layout, which is shown from above. (I’ll discuss how one holds the roof up in a later post.) The shuttle car can brush through the temporary stoppings, which I have shown as plastic hanging curtains.
At the transfer point the cars dump their load onto the protected end of a long conveyor belt that will carry the coal to the shaft, where it is loaded into skips that carry it to the surface. Where the seam of coal comes out to the surface on the side of a hill (outcrops) the conveyor will come out through one of the entry tunnels (portals).
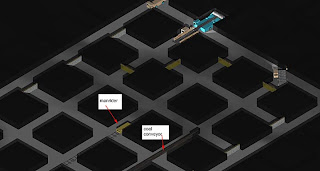
In the picture you can see that in this district or section of the mine they are driving five headings, with the miner in the second. There are two shuttle cars, one at the machine and one turning to replace the first along the cross-cut. The conveyor belt is in the fourth drift, while in the third, or central heading is the man-trip that carries men and supplies to the section, and the light rail segments that it runs on. (I have not shown the supply piles and other items normally found around this area).
The problem of gas is still present, as it was years ago, and because the coal is ground into smaller pieces (most of it less than an inch in size -while hand-got coal was around four inches), the gas volumes can be somewhat larger than with slower methods. The continuous miner can achieve short-term production rates of around 15 tons a minute, but must stop frequently to change cars, or to move.
The problems of ventilation remain. Large fans at the surface now supply the air to dilute the gas and sweep it away. In the immediate working area these stoppings can be made of cloth or plastic, so that miners can more easily move through them. When the working area moves on the stoppings are made permanent, and the ones shown are made of grey cinderblocks. Doors are placed in these stoppings at regular intervals to allow men and machines to pass, as shown above. Remember that in most of this area, all the miners have to see where they are going are the caplamps that they wear on their helmets, or the floodlights on the machines.
It is still necessary to leave pillars to hold the roof up. Roads, headings and cross-cuts are often the width or some multiple of the width of the mining machine, i.e. generally around 12 - 20 ft. based on the seam depth and the roof rock strength. Pillars may be around 40 ft on each side. It doesn't take long to realize that a lot of coal is being left in the ground.
That will become the subject of later posts. For those who know better, please recognize that this is a very simplified explanation of Room and Pillar mining, and that there will also be a few more details, as this series continues. But it should convey the concept.
Thanks, Heading Out!
Is all of this machinery electric, or is it diesel operated?
You're welcome.
The power is almost all electric in coal mines, and so there are limits to the movement of the machines, due to the cables that they trail behind them.
Diesel is generally more common in metal and non-metal mines, and I was recently in one that uses biodiesel because it produces less particulate in the air, which is otherwise a concern.
Interesting...I suppose "clean diesel" mining & other off-road equipment is not really on the market yet. The reductions achieved for on-road diesel emissions of particulates and NOx using particulate filters, exhaust recirculation, SCR, fuel oxidation catalyst, etc. to comply with the requirements for 2007 and 2010 respectively have been impressive. But those modifications are not yet required for off-road equipment and so I am guessing future-compliant diesel equipment for mining is simply not available at this time. As an example, Caterpillar nixed their plans to develop 2010-compliant on-road engines so they could focus on the larger part of their business in mining, construction, landfill equipment, etc. In other words, no clean diesel off-road equipment from them yet...I assume other manufacturers are in the same boat.
http://www.epa.gov/nonroad-diesel/
This page mentions specifics with regard to sulfur content and indicates more stringent requirements for NOx and particulate emissions, but I can't seem to find a specific timetable for when off-road diesel equipment will have to meet the same requirements as on-road. Of course the advanced clean diesel systems are a lot more expensive too so that together with rising oil prices could also propel a fuel switch from diesel to natural gas, biodiesel or other alternative fuels (as has been happening with fleet applications of diesel vehicles).
Is diesel equipment still used in coal mines to extract from places where the electric machinery can't reach? Or is that hard-to-reach coal simply left in place, being too expensive to go back in and extract? Or is there some other entirely different practice used to recover the leftovers after the electric stuff is done? It seems that as oil and coal deplete in tandem, we'd increasingly need more expensive fuel to mine coal from more remote and technically difficult locations, and maybe to extract some of the coal left behind by electric equipment in older mines...in other words, peak oil could cause the price of coal to go up too in a world of parallel depletion. This is just my intuition talking though, so perhaps you can clarify.
In any event, thanks again for an excellent piece. I really enjoy these technical primers - after reading them I feel like I actually know something :)
Not an expert here, but electric powered equipment is used because of all the coal dust down there? Are diesel engines more of a fire hazard in coal mines as opposed to a silver mine?
I'm no expert either but I was assuming the main reasons for using electric equipment was that it is available to be produced on-site from coal and that it is cheaper than using diesel. Had not thought of the fire hazard possibility, seems plausible but as I understand it the main fire/explosion hazards are related to methane or dust being ignited by sparks or compression from the physical grinding against the walls to extract the coal. I suppose diesel exhaust-related air quality issues could become a concern in underground mining as well?
Yeah. Remember also, there are severe space limitations down there as well. Coal seams can be very narrow, not much head room. Electric equip can be built a bit more compact. I dunno.
last I read electric motors were quite a bit more efficient than small diesels, of course that might vary quite a bit depending on power generation efficiency and all. A detailed ERoEI comparison is probably available somewhere, hopefully one that actually equalizes the apples and raisins.
Machines such as the ones pictured obviously require a good bit of horsepower;running a diesel engine big enough to do the ob would simply FLOOD the work area with hot , toxic exhaust fumes.
Furthermore electric motors and thier cables are easy to service-they need almost nothing in the line of routine maintainence, compared to a diesel, and the number of actual breakdowns is probably less than (swag) ten percent of the number suffered by even a top quality diesel, over a long period of time.
Managing the cables probably ios less work than just servicing air cleaners and radiators in a coal mine type environment.
I'm strictly guessing but I suppose the cables are constructed with a very easily replaceable outer cover , ot two such covers , to protect the insulation and conductors inside.such a cable will last indefinitely;welders often run thier leads thru heavy rubber hose sleeves to protect them from a harsh work environment-this is much cheaper than buying new leads everytime a cable suffers a cut or abrasion exposing the conductors, which can otherwise happen several times in the course of a day under some conditions.
Yes, thanks HO. I do so look forward to Sundays and this tech talk on coal mining! Especially the underground end of it.
WastedEnergy: You are probably right about going back after all that coal left behind for structural support. Maybe they are doing so already.
Yeah, after going back and rereading the original post more carefully I saw that HO plans to do another piece on what happens with the support pillars, etc. So I will be patient and wait another week I suppose :)
I know, huh. I start gettin sorta excited on Sat night to go to Sunday school! Heh! Heh!
It's interesting that most of the coal in the seam is left behind to provide support. If the area removed is too large, the roof gives way and presumably, a column of material possibly extending to the surface drops downward. This is likely an over simplified view I admit, because the geology of the strata above the mine would include structures that provide support that a simple pile of dirt could not.
Yet in Pennsylvania for example, it is written into the deed of title to property that there is no protection or recourse afforded to the land owner in case of "mine subsidence". This term describes the situation where the surface of the land drops away, taking with it your yard and perhaps your home. Because there are old coal mines underlying areas where houses are currently built this is a real occurrence.
Would it make any sense to extract all the coal, in a manner that deliberately caused the roof to cave in when the seam was exhausted? In another simplistic view, work it from the deepest end of the deposit back outward, taking out a section at a time and purposely dropping the roof in on the open gallery before moving to the next one? If echo sounding can model the size and location of the extent of the seam could you not then know pretty clearly where and how far to tunnel?
Well, like I say, I am not an expert at all,but I was wondering if there are new roof support systems available so they can get the coal and not have subsidence problems up top. I've seen what those old abandoned mines can do to a home and am glad it didn't happen to me, for sure! just wondering.
Thanx once again Heading Out --- informative and interesting.
Just as in the oil industry the coal industry is notorious in safety violations. It's incredible how these companies ignore safety and later have to pay enormous payout for penalties and civil damages. It's amazing how they will skimp on safety in the short run and ignore long term ramifications so they eventually spend a buck to save a penny.
http://en.wikipedia.org/wiki/Crandall_Canyon_Mine
Pillars collapsed on miners.
First off I am not a coal mining expert, but since a lot to the original coal is left in place it is / was inevitable the attempts would be made to extract this seemingly easy resource.
The well publicized mining disaster in Utah last year or the year before was a result of a miscalculation or poor execution in a process termed "retreat mining" where the an additional increment of coal in the support pillars is mined and the roof is allowed to collapse as the mining face retreats toward the entry.
By reports, this process can be done with reasonable safety, provided adequate engineering and skilled execution is employed.
Thanks for the post HO. I have one question that occurred to me the last time I saw you post the following:
Are those numbers just for the energy used at the break out point at the mine face or are they more all encompassing?
No, these numbers are just for breaking the coal from the face. However in most operations it is this, and then the crushing to fine size that can consume much of the energy cost - depending on such factors as how deep the mine is, obviously.
Thanks again for doing these.
What are the thickest seams that can be mined by this method? Some seams in the Powder River basin are 20 meters thick, but are shallow enough that surface mining has worked. If you ignore embedded mudstone layers less than 20 cm thick, some seams are 60 meters thick. These seams tend to slope, and as miners follow them, the overburden is eventually too thick to economically remove. Are such thick seams amenable to mining using regular underground techniques?
Once you get above about 12 ft it gets hard to maintain conditions, and in these cases the mine can extract the coal in several lifts. In those cases they more often use longwall techniques that I will get to in a couple of weeks.
I'm from West Virginia and my brother and my grandfather worked in the coal mines. I worked for the Department of Environmental Protection as a software systems developer for systems tracking coal mine permitting among other programs for most of my career. My customers were mining geologists, engineers, and experienced mining regulators. I'll speak to some of the questions and topics I've seen in comments already made.
One of the most significant health problems in underground mining is pulmonary health. People still contract and die of "black lung" and the rates are getting worse, not better, more recently. So diesel-powered equipment is not legal in WV for underground mines. I have seen diesel machines in Colorado mines, in extremely thick seams (20 feet) compared to WV UG mines. We know how to control coal dust, by using water sprays when coal is moved and by spreading limestone dust to dilute the coal dust so as to keep its proportions from becoming explosive. This is what appeared to happen recently at Massey's Upper Big Branch mine. No water spray, no rock dust, rigged methane detectors, 29 dead miners and no more coal, for a long time.
In room and pillar mining, the big companies want to leave the pillars, because it's much safer. Typically, then smaller contractors will lease the mine, pay less, take more chances, and retreat mine the pillars, allowing the mine to collapse behind them, in theory in a controlled manner.
When this doesn't work out, the collapse can be uncontrolled, as happened in Utah not so very long ago. Both the shift of miners and a rescue crew were killed in a collapse during retreat mining, also known aa pillar pulling or pillar robbing.
Depending upon the rock over the coal seam, mine subsidence (another term of art for mine collapse, whether controlled or not) can result in structural damage to highways, bridges, factory, commercial and public buildings like schools, shopping centers, prisons, etc, and private homes and farms. Suddenly dry streams can also be caused by cracks opening up in bedrock from the earth movements caused by subsidence. Basements become REALLY deep.
Subsidence actually occurs even when pillars are left in place, over time, if conditions are just so. Whole towns can become affected when rock types and seam depth allow crevices to reach the surface as roof falls in over time.
There are programs to repair this damage, but changes to aquifers, streams, water tables and land quality changes can't really be remediated very well. Much like cleaning oil from a marshland, it's a lose / lose proposition.
Long wall mining will probably be the topic of a future story. It also allows for "controlled" collapse, but instead of pillars they use huge hydraulic jacks. More modern than continuous mining room and pillea
Mining can be done relatively safely, but as long as the industry is allowed to they will often avoid spending an extra dollar on safety. Just like BP did.
Thanks JR.
So even if you had an accurate map of the tunnels and galleries for every mine there is no way to predict what, where, when, how much will happen on the surface. You just know over time it will probably change and not for the better. Even a controlled collapse, while answering at least part of the "when" question, does not guarantee the changes above will be compatible with uses other than mineral rights extraction.
You folk are getting ahead of me again. There will be a few more posts on these topics, at least one of which will discuss ground movement and the control of subsidence at the surface.