Tech Talk: Longwall Mining - Using Hydraulics to Modernize Mines
Posted by Heading Out on August 15, 2010 - 10:50am
In writing about longwall mining, I have gone into some detail as to how the technology initially developed, in part because of my own interests, but also because some of its features help answer questions about today’s industry and this will provide a background for those answers in future posts.
The change in longwall came about as I went to college. The manual loading of the coal and setting of roof support that I have described in earlier posts ended as a result of a single technical change. The miners had loaded coal onto a rubber face conveyor that was advanced by being split into sections, moved forward, and rebuilt every day. This is incredibly inefficient and the innovation was the change to what has become known as an armored face conveyor. Basically this consists of a series of 5-ft long, hinged elements or pans, connected together in such a way that each can move forward and twist slightly, relative to its neighbors. (In using pictures of existing equipment let me just insert that they illustrate what I am discussing, but that shouldn't let you think that I believe that one particular brand is better than another.) A single element of a relatively modern version looks like this:
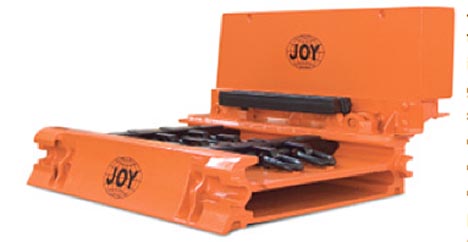
Horizontal link bars fit between elements in the hollows that can be seen at the ends of the piece allowing flexibility in the joints. The face of the conveyor is the wedge shape, that faces the coal face. Coal is loaded onto the conveyor from the mining machine, and any coal left on the floor then rides up the wedge onto the conveyor, as it is hydraulically pushed forward after the machine has passed. (A point I will discuss later). The coal falls into the top trough of the conveyor.
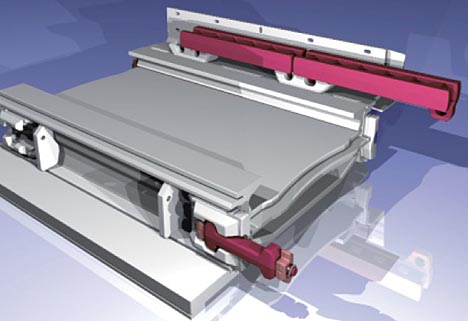
To move it along the conveyor, there are two chains, which connect to lateral steel bars called flights, which slide in the slots on either side of the top trough.
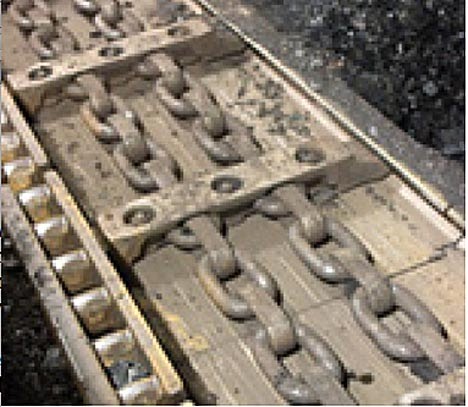
The chains drag the flights down the trough, pulling the coal that falls onto the conveyor with them, and at the end of the conveyor, the bed is raised, so that the coal is dumped onto the belt conveyor that runs in the entry tunnel to the longwall. (For historic reasons this is generally referred to as the Maingate of the longwall.) The empty chain and flights then return along the face in the underside compartment to the conveyor.
The moving parts of the conveyor are thus now the chain and flights, and they are driven by a motor mounted in the maingate of the longwall.
The arrival of this then new tool allowed a number of different changes to occur on the face. The first and initial requirement was for a way to move the conveyor forward after the coal had been mined out it front of it. It was too big and cumbersome to disassemble and reconnect, and flexible enough that it could be pushed over using a series of hydraulic rams, one attached to each of the pans of the conveyor. But what could provide the resistance against which the rams could push?
The only element in the face behind the conveyor are the roof supports. So these also had to be modernized so that they could work in this way.
Initially the supports had been individual elements, two props and an overlying bar, all made out of wood. I had mentioned last time the arrival of hydraulic props, and steel bars. By combining these into a structure, with the props set on a bearing plate, and the steel bar at the top permanently mounted to their upper section, a simple support element was created. This, as we found out, didn’t have much lateral stability, and so they were combined in sets of two. With a hydraulic ram on the front, this could now push the conveyor forward.
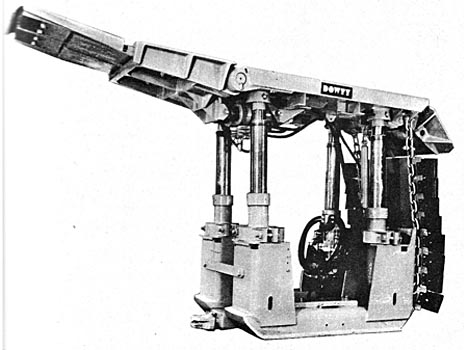
The ram would also make it possible, after the props were lowered, to pull the entire unit forward, and then, after raising the props, reset closer to the face. The plates at the back then stopped the rock that was collapsing into the void left behind the chock where the coal had been, from rolling into the working face. This became known as a chock.
Over time the props became larger, and the canopy which was meant to extend over the conveyor to provide early roof support didn’t work that well. The idea was that it could be slid out, after the machine had mined the coal, until the chock itself could be moved. The problem was that if there was a heavy load applied at the tip it would bend the cantilever so that it could not slide. Then life became a little more difficult. The answer came from Hungary initially. It was known as a shield support.
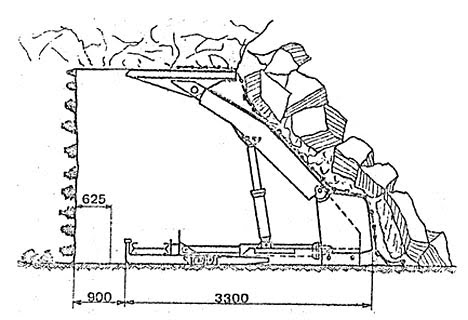
The design was extremely flexible and able to mine under conditions such as a badly broken roof that would not have been possible with normal supports, since the top and back (canopy) of the shield provided a virtual complete coverage of the roof and back of the working area, and the shields were installed adjacent to one another.
There have been considerable advances in design, but of an evolutionary nature, since this particular breakthrough – which occurred in the 1970’s. But in combination with the use of stronger and more powerful face conveyors these supports were able to make high-speed longwall possible in a wide range of differing conditions.
It is even possible to mine out a thicker seam by taking the lower coal with a mining machine (of which I will write next time) and then letting the upper coal collapse onto the back of the support, from which it can be recovered using a second conveyor. (And not a lot of energy – Charlie).

Support used for top coal recovery - it's a lot more complex than a wooden prop.
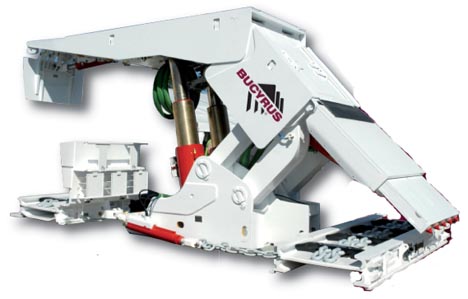
As I mentioned above, I’ll talk about the mining machines next time.
Thanks, Dave!
This may be a dumb question, but what technologies underlie hydraulics? Is it a technology that can be kept up with local resources? You mentioned that the changes date from the 1970s. To what extent does oil play a role in their manufacture? Certainly it plays a role in their transportation, today.
It 'takes' hydrocarbons to 'get' hydrocarbons?
There are biodegradable hydraulic oils for use in sensitive ecological areas. I suspect that something similar, perhaps castor oil (used as lubricating oil long ago) might do the job if it wasn't subjected to extremes of heat.
I know Tower Bridge in London went with a super cool steam and water based hydraulic system until it was replaced with a 'modern' electro-hydraulic system in the 70's. I bet the Brits wish they had that one to do over again. I am guessing they should have just upgraded the old system. Maybe there is a lesson there.
I noticed that your site has not been updated. Check out...
http://www.vbs.tv/watch/toxic/toxic-gulf-full-length
Did the local vendors ask you to not be an alarmist?
I hope those cheap beers were worth it.
The small local vendors I know have just told me what they plan to do next. Most are moving. It is going bad for the small guy. The large and mid guys can hang on a little longer. Everyone is uncertain. I could report from the locals, but to what end. I have no direct data. I need a flame atomic absorption spectrometer or I can post sad interview after sad interview. If you have suggestions, I am all ears.
TinFoil
BTW I have been studying for my GRE.
I don't know anything about renewable hydraulic oils, but hydraulic oil in layman's terms is basically just a thin, easy flowing lubricating oil with a few additives to control rust and foaming and so forth.
It needs to be changed at long intervals in most machines, but it is not used up like fuel;sometimes if a machine is in very good condition, you can run it for months of end without the level moving visibly in a sight glass-which is generally installed in the reservoir tank so that it is easy to check the oil supply without getting any dirt in the system.
Our farm tractors , which are old and have some very minor leaks, might average a quart or two each over the course of a year-which is three or four hundred hours of running time per tractor. Diesel comsumption is higher by a factor of a thousand or more at least.
It doesn't seem likely that hydraulic oils,or lubricating oils and greases, will be a decisive factor in oil depletion until we are pretty far down the scary side of the supply curve;they will be expensive , without a doubt.
Many thanks yet again Heading Out. I was raised up in a coal mining area, bloody shame not one school I went to did not explain how coal is mined. I thought, all my friends thought and the local media still think that there are vast caverns left underground where the coal was mined from and that is what causes the subsidence when they collapse. I had no idea that the underground rocks were encouraged to collapse and fill the voids left by the extracted coal seams.
So what causes the subsidence that still plagues previous underground mining areas in the UK?
HO: Thank you for these Sunday morning talks on coal mining, again. I always look forward to them.
Good history. Question - What happens if the load exerted by the roof on the chocks exceeds the capacity of the hydraulic cylinders and causes the chocks to bottom out? I think that this has happened in rare cases.
Coal and hydraulic oil everywhere and you gotta start all over? :)
I completely missed this one. I definitely look for comments from the folks here, either way. I am playing catch-up.
http://blog.al.com/spotnews/2010/08/will_mine_discharge_threaten_b.html
Are 'dirty' clothes the real concern? I just know little of mining risks other than the obvious.
Iron Toxicity is a concern.
http://en.wikipedia.org/wiki/Iron_overload
http://www.irontoxicity.com (a Novartis (drug company) site - liver cancer is a possibility from iron toxicity)
http://www.merck.com/mmpe/sec01/ch005/ch005f.html
Some people are more susceptible, but it's not just dirty clothes.
Iron encourages various "iron bacteria", they make the pink slimy coating on or in plumbing fixtures. Other "bugs" might want to live on them. c.f. the recent oil pipeline leak discussion: corrosion is often due to byproducts of bacteria living in pipes.
The question I would be asking is: given the high levels of iron, how are they dissolved in the water, i.e. what is the acid content of the water, thence, given that the water is so acid, what else (i.e. even more toxic metals) is dissolved in there?
Manganese is similar to iron, necessary for life, but toxic if too much is present.
http://lpi.oregonstate.edu/infocenter/minerals/manganese/
http://lpi.oregonstate.edu/infocenter/minerals/manganese/manganeserefs.html
From the oregonstate.edu page: section "Ingested Manganese"
If I were a parent in the area, I would be VERY CONCERNED about high levels of these elements in the water supply.
Damn, makes me glad I am just dealing with the Corexit.
Iron Toxicity is a concern.
http://www.immunocapinvitrosight.com/dia_templates/ImmunoCAP/Allergen___...
Raw Cabbage juice has been used as a peptic ulcer treatment, due to its S-methylmethionine content. But the juice, if consumed in excess, begins to inhibit iron absorption. Cabbage has also been used to help prevent cancer of the colon.
http://web.mit.edu/athletics/sportsmedicine/wcrminerals.html
Calcium inhibits iron absorption from non-meat sources
I live in a part of New Jersey that is COVERED in old (early 1800s to mid 1900s) iron mines. A lot of the houses are well water, and there is good reason to believe that a lot of those "wells" are really drawing from the nearby mine shafts. Luckily, filtering iron and manganese is fairly easy. There are sediment filters that take care of most of it, and filters for the really bad areas. Most wells that I have experienced have needed some sort of treatment to be usable, and it seems like these people are going to have to add/change/adapt. Iron issues are not that bad compared to radon or hydrogen sulfide issues (which we have here too).
This series strikes a little closer to home for me after this past week. I was visiting my mother (82 years old) and going through a variety of old family photos. Much of my family lived in southern Iowa at the time it had an active coal-mining industry. I learned that one of my great-grandfathers was killed in a coal-mining accident, and that one of my grand-uncles tended the mine ponies when he was young. The mines only operated five days per week, and one of my mother's fond childhood memories is of getting to go with her uncle to help care for the ponies on the weekends.
How on earth do those supports move forward?
NAOM
Consider 3 in a row. Lock 2 of them against the roof, pull the third one down and use the horizontal piston to pull it forward. Raise it against the roof again and do the next one.
Yup. The oilfield isn't the only place where you find big men with big iron. We have them in mining too.
From old memories: One of the scariest things you had to do in underground coal is to set a cap-and-post timber under a section of bad roof. The cap had to be hammered onto the post, which shook the roof and covered you with flakes from above. Now that's done with hydraulic props. I remember a man going to hospital after getting a slab down on himself while doing roof control.
How on earth do those supports move forward?
When you have pushed over the pans,you lower the chock and reverse the direction of the pusher ram which then pulls the chock forward, you then set the chock in place again by raising up too the roof it is as simple as that, another question concerning hydraulic oil, the chocks I was used too used water with additives you had a solution similar to cutting too cutting fluids used on lathes?
HO:
I often have trouble visualizing things. A picture that shows the whole in full detail is much to busy to make sense of, but everything that is left out to simplify, is ... left out. Here, I think I understand. But I'd like confirmation.
In your talk, the last picture, which is a picture of a Bucyrus roof support machine: In actual use there would be MANY of these lined up closely, side-by-side, so that the Bucyrus label would be visible on only the one machine that is at the Maingate. Is this correct? Typically, how many in a line?
These machines must involve an impressive capital investment. And in the event of an accident in which a machine somehow gets stuck under a pile of loose roof rubble, it is almost certain that many more than just one machine were similarly stuck as part of a single grand f--- up. To unstick them sounds like dangerous work, indeed.
Thanks for a very informative talk.
PS A comment on pontificating on the future of technological advance, which is done often on TOD: The rate of deployment of new technology in computers and integrated circuits is simply irrelevant to estimating the rate of deployment of these Bucyrus/Joy/whoever machines. Large scale wind energy deployment might be somewhere in between the two, but maybe not.
Geek: We usually didn't try to recover a lost machine. It was considered too dangerous, and the machine would have had to be rebuilt to satisfy MSHA regs anyway. They just wrote it off and bought a new one. Yes, very costly stuff. As I recall, a Joy continuous miner we lost was worth $800,000. But it's just the cost of doing business.
What was covered in that $800k figure? Just the roof supports, or did it include the conveyor and coal-cutting machinery too?
That was mostly the continuous miner itself. It was only 2 weeks old, and had a custom cutting head. Our mine was plagued with petrified tree stumps. (We had a name for those, but I won't repeat it here). They were silica, hard as flint, and would take the teeth right off a coal cutting head. So our heads were specially made to handle that. We lost the miner and its power system, a trip of rail cars, and some lesser tools. And a half mile of 60-pound rail. We walled off the bad area with concrete stoppings and never saw our stuff again. It should still be right there where we last ran it.
geek: You should see how they deploy a 1570 Bucyrus stripping dragline! IT has a 75 yard bucket and takes a year or so to build on site.
All the military and equipment stuff plays 24 x 7 here. I have seen the videos on Discovery.
TFHG: Yeah.i have watched those too. They are really cool when you actually get to go up in one! I got to get up in one at Kiewit's Rosebud Mine near Hannah, Wyo. Helped build load out facilities at several mines up in the Powder River country around Gillette, Wyo.; Buckskin Mine, North Antelope, Jacobs Ranch down south of there, Black Thunder near there, and the scale of the equipment used is incredible. Its just a hell of thing when you see that iron up close! :)
To clarify: I got to get up in a 1570 Bucyrus dragline. The mine superintendent was quite willing to let my Dad and I each run it, but, it was down at the time. They were changing the 4 inch drag ropes while we were there.
Did I ever tell you my idea if coastal flooding and sea level rise became a real problem? Dig a new lockless Panama Canal about a mile wide Atlantic to Pacific. Use the muck and cut to build a new coastline for the whole hemisphere and upgrade Panama City to bigger and better than New York as payback. That and the Panamanians keep the new canal. Crazy I know but could you picture hundreds of scoops and drags cutting and mucking from both coasts 24 x 7? The material would hauled by boat and dropped (for a small fee) to flooded city of your choice. The Panamanians would become the new Kuwaitis. I would laugh and say it serves us right.
TFHG: I believe the French(Ferdinand De Lesseps) tried that very thing round 'bout 1881! Even though they failed miserably. They were just WAY ahead of the technology OR didn't have a good handle on the effects of that there awl the Americans were drilling up there in Texas!Heh! Heh! Good on 'em, those Panamanians! I went to my nephew's wedding down there in Panama City, he married a little girl from down there, and, I tell you, it was one HELL of a party!!! Now, THAT, would be one heck of a ditch, my friend!!! Oh, just FYI, when we took the Isthmus, the subsequent dirt moving was done, for the most efficient part, by Bucyrus 95 ton steam shovels! There were some Marion shovels involved, but, we dont talk about THAT outfit!!! Heh! Heh!
Some selected videos from the MC252 ROVs last night for your viewing pleasure.
Fish and creatures caught by the Spill Cams on the sea floor.
http://bit.ly/Random-Fish
Crab visits ROV.
http://bit.ly/bC02OV
ROV untangle and Dock - did a flip this time to get rid of the kink.
http://bit.ly/dAwdnA
* All posted on #theoildrum