Tech Talk: Flexible Roof Support Systems
Posted by Heading Out on September 19, 2010 - 10:55am
This is part of a Sunday series of tech talks, on various energy-related technical subjects. Last week I was talking about building tunnels, and tunnels need roof support.
In the last Tech Talk, I discussed the use of rock bolts as a way of building, from relatively broken bits of rock, larger packages that could brace themselves against one another. In this way, as they moved into the underlying opening, they would act in the same way the blocks of a Roman Arch, and would become self-supporting. I have crudely tried to show the blocks with this figure:
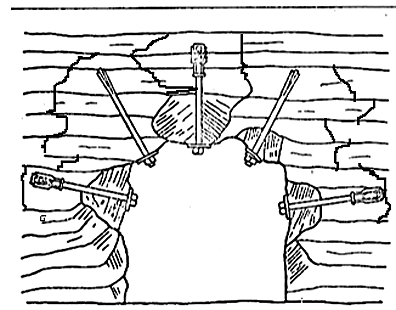
The intent is to create a compression zone just behind the face, and this can be shown with a photoelastic model, where a set of bolts is used to generate a central compressed zone. The black lines show zones of different compression, and while the bolts are tensioned, they compress the material between the ends.
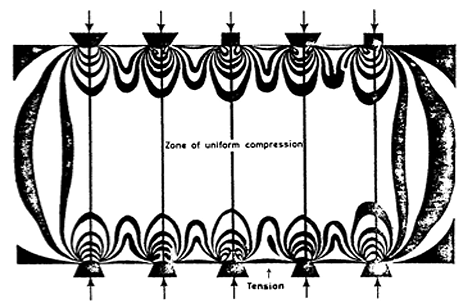
Using that model also allows me to point out the snag in just using bolts. You can see the small areas of tension between the bolts, where the compression cones from the plates has yet to intersect. Well, if there are small loose pieces of rock there, they will fall out. And over time this “raveling” will get worse, so that any rock at the edges of the compressed pieces that crushes can also fall out. Over time this may mean that a critical block is no longer held properly in place, and it may collapse, bringing down the entire roof.
But when that raveling started, it was very small, and only the weight of the individual small pieces caused them to fall. This can be stopped, therefore, from happening by putting a layer of chicken wire (so-called because we used to use it to build chicken coops) between the bolts. This has no great strength in itself, but it holds the small pieces in place, so that they can’t fall out, and if they are still there, then the small pieces above them can’t fall out either, and so with a relatively weak addition, we gain longer term strength.
The snag, however, in today’s society, is that putting up chicken wire between bolts – since it has to be inserted between the bolt plate and the wall, is labor intensive, and slow. So, perhaps we can replace this thin metal support with something else – how about spraying on a thin layer of concrete?
The concrete can be kept relatively dry, and accelerators can be added to it, so that it can set very quickly, and in this way it is possible, using compressed air, to apply a layer of concrete up to about 6-inches in thickness to the wall, almost as a single layer. (There are application skills that are needed to do that over one’s head). Now we have build a relatively solid wall that the small stuff can’t get through, and the natural arch can build in the surrounding rock.
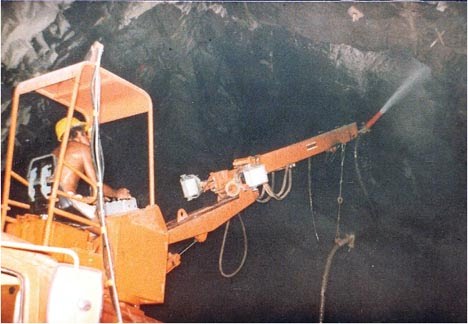
(As a passing comment for those of a technical bent, concrete sets up as a relatively rigid liner and to get the rock walls to move and support themselves you shouldn’t therefore apply it too soon after making the opening, but if you have to, because the rock is really bad, you might put wooden strips in the shotcrete to give compression members so that the support can yield).
It is not, obviously, quite as easy as it looks, and it has the snag that after you have applied a layer, it is hard to tell what you have covered up. (Though I have only heard of one job where it was stripped off and re-applied). Questions of chemistry and operator skill all play into getting it put on correctly, and if you are covering over a wet rock, you should allow a path for the water to get out, otherwise the shotcrete might peel off after a while.
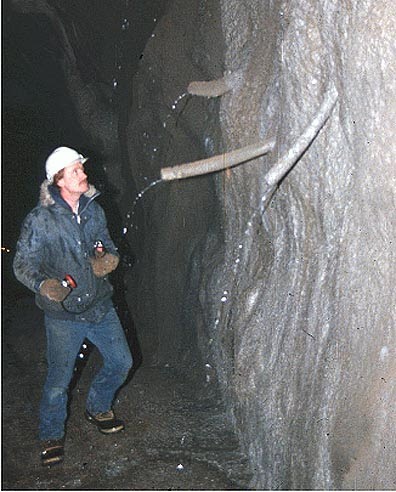
There is one further thing that can be done, and that is to add small fibers of steel or fiberglass. The problem with concrete is that it is not that strong in tension, and when the tunnel moves, there can be some pull or bending of the liner, that could allow it to crack. But by putting less than 5% fiber into the mix, a much stronger layer can be created, especially if a small amount of silica fume is added to the mix, to both help lubricate the mix, and also to improve bonding.
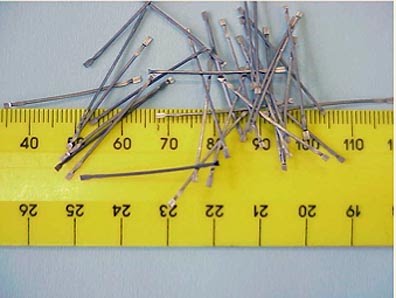
When this idea was first introduced, it met with a lot of cynicism. And obviously it is not the answer in all cases (swelling and plastically deforming rock in particular can cause problems). But the story that I used to tell was of the operation on the West Coast. They were tunneling under a relatively poor sandy rock, that would not stay up. They had strong steel girders for support, and wooden lining between the arches, and still the walls were deforming into the opening.
Then, almost in desperation, they tried spraying the walls with shotcrete, before putting in the arches, and then spraying over those. After a while they increased the spacing between the arches. Then they replaced them with lighter arches, then they continued without arches.
The major advantage that shotcrete provides, particularly when it is combined with rock bolts and the judicious use of steel arches, is that of flexibility. As I mentioned in an earlier post, when you used to drive a tunnel under a harbor, for a certain metro system, you designed the tunnel for a certain estimated condition, and ordered the steel girders ahead of time. If conditions got worse, then you were out of luck, unless you were a lawyer.
However, with the shotcrete, bolt and arch system, the contractor, the owner and other interested parties can have their engineers meet about every 100 ft of tunnel advance and decide if the conditions are getting worse. If so, then the shotcrete can be sprayed on a little thicker, the bolts moved a little closer, or light arches inserted. And the converse can also occur, with less support if it is not needed. This flexible approach became known as the New Austrian Tunneling Method, and while it was for a while very controversial, is now much more widely accepted.
Underground construction can provide lucrative work for lawyers when ground and other conditions change from that covered in the original contractors bid. Properly structuring the contract can help minimize or eliminate litigation due to changed ground conditions. Test borings to predict ground and water conditions before designing the job is money well spent to specify the type of roof support, tunnel liner, water control etc necessary. However, as pointed out in the discussion one can only predict what is needed and actual conditions incurred during the excavation dictate the actual roof support needed.
Briefly, the contractor bases his bid for the job using the predicted support etc. It is not really in the owners interest to insist on a lump sum bid because the contractor will insert a lot of contingency which may or may not occur. A more equitable contract has unit prices for additional steel sets, shotcrete, water to be pumped , delay time etc. The unit prices should include the additional time for the extra work. When evaluating bids different contractors will have varying unit prices which complicates the owners evaluation to predict the final cost of the work. Successful contractors are quite adept at structuring their bid to reduce their risk and/or increase profit.
Other contracting methods can be used to help avoid litigation and minimize the cost of the work e.g. cost plus fixed fee, target cost plus incentive fee (where the owner and the contractor share in cost savings or cost overruns).
Love the idea of sending Lawyers underground to work ;-)
My only complaint is that shotcrete is used in the areas I most want to map. If you are not quick about it, the structures you really need to measure are covered. Still, beats having a closed-casket funeral from having a chuck of back coming down on your head.
I'm wondering if the shotcrete approach approach is fairly dependent on our oi-basedl economy. Is the manufacture of shotcrete oil dependent? Are the big machines you show very often used? Do they run on diesel or electricity?
The primary energy input into shotcrete is coal or NG, for making cement powder.
The machines themselves can be either - diesel/truck ones are common for road construction (shotcreting rock cuttings by roads), but in mines they prefer electric - IC engines are a hazard.
Of course, depending on how remote you are the mine/tunnel electricity might be coming from a diesel generator anyway...
Shotcreting has become very popular for road cuttings as it can sometimes allow steeper angles. However the energy used is miniscule compared to that used to make the cutting and build the road, or, of course, the vehicles that drive on it. The same would apply to tunneling.
Hi Paul Nash,
I have never seen an electric jumbo or any other piece of electric heavy equipment underground. All of the mines I have worked in are all diesel equipment; this includes all the underground mines in the Carlin Trend and in Canada. Yes, ventilation is a major expense, but diesel is fairly safe, especially compared to petrol engines.
Do you have any direct experience with electric heavy equipment underground?
Friend of mine in Australia, in a coal mine told me this - may be special regulations? It might have been hydraulic drive too, but he said it didn't have an engine. The mine did have to control methane, all electric stuff was explosion proof, etc, so maybe that was the reason?
My direct experience has only been related to roads when I worked as a geotechnical engineer, but once they discovered shotcrete, they wanted to spray it everywhere!
I worked at a water treatment plant that had a small footprint and installed two 15 MG clearwells. The contractor excavated 10 feet of hillside, then drilled and bolted. Repeat, then shotcrete, total excavation was around 100 ft. to provide a pad to build the clearwells and piping, etc.
There is around 11 million lbs. of water and I don't know how much concrete and re-bar adjacent to the excavation site, I'm surprised the hillside hasn't collapsed.
lat 32.606936
lon -116.932700