Tech Talk - Extracting the Attic Oil From Abqaiq
Posted by Heading Out on April 15, 2012 - 11:40am
Current figures suggest that world liquid fuels production is running at around 90 mbd, of which roughly 74 mbd is crude. A reasonable estimate of the annual decline in existing well production lies at around 5%, so that each year new sources of oil must be brought on line to generate 5% of 74 mbd (3.7 mbd) to cover these declines. In addition to that need, if world oil markets continue to grow as expected, then an additional roughly 1 mbd of new production will have to be added this year to meet the growth in demand. (China imported 5.95 mbd in February, and though this dropped to 5.55 mbd in March, this is still up 8.7% on March last year.) This state of affairs does not include the fall-out from political actions, such as the embargo on Iranian oil, which imposes additional demands on the rest of the global suppliers of crude by taking that production out of the market. As Econbrowser has just noted, the countries that are potentially capable of upping production to meet the size of the total additional demand likely foreseeable this year seem singularly limited to a kingdom whose initials are KSA.
There is no doubt that Saudi Arabia has considerable oil assets, though I have noted in the past that they tend to use the total discovered oil volume as their reserve, without discounting the amount that they have already produced. Rather, the question that will increasingly arise in the future is whether the country can continue to produce at the same rate, or – if they are to meet the claimed 12.5 mbd of achievable production - to be able to achieve a rate that is 25% higher than current levels. Not that the amount available from some older fields is not of some concern. Consider this plot that came from Aramco in 2004, when Mahmound Abdul Baqi and Nansen Saleri debated Matt Simmons at CSIS. And remember that production has continued from those fields in the eight years since.
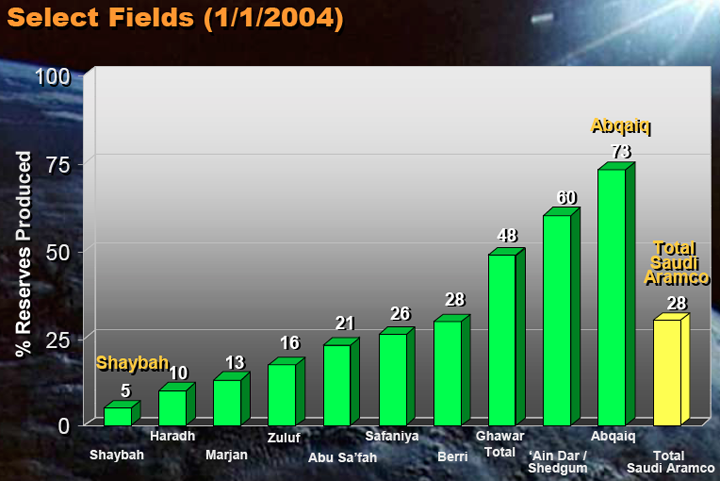
In the post last week (and my apologies to Glenn Morton for unintentionally confusing him with Greg Croft at the beginning of that piece) I pointed out that there are a significant number of rock layers under the surface in the country that contain oil. Now not all of them do this very consistently, but as the example with Abqaiq showed, as the original oil reservoir becomes depleted, so other rock layers can be tapped to produce in their turn.
However, the story with Abqaiq shows the difficulty in being able to sustain production as fields reach the end of their life, and the increasing costs that must be incurred to do so.
In the early life of the field, wells are vertical, relatively inexpensive, and produced for decades. Now it is only advances in technology that allow production to remain at high levels. The original vertical wells have been sidetracked so that a horizontal section is established in the top 10 ft of the reservoir.
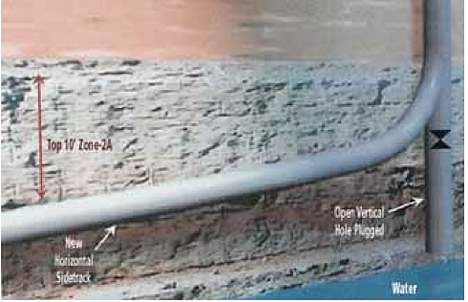
However, to reduce costs and improve production (which stalls at a certain level as an individual horizontal well gets longer) Aramco has changed to the use of Maximum Reservoir Contact wells (MRC). These initially started out as a series of laterals drilled out from the main horizontal well, so that although the distance from the vertical remained quite short for each segment, the overall exposure of the well to the formation could reach, in this case, some 12 km.
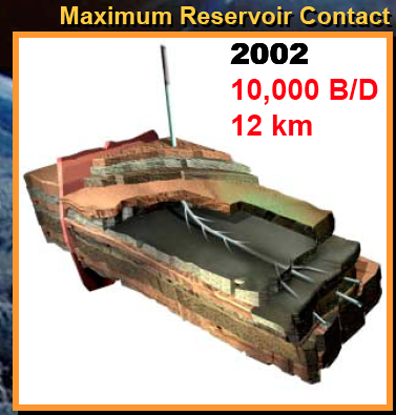
However, with the laterals laid out in this manner alone, the entire layout become vulnerable if there is premature water breakthrough in any of the laterals. The initial test at Abqaiq, for example, watered out in six months. A second test with five laterals to give a total reservoir contact of 6.9 km produced initially at 19,000 bd and lasted for two years.
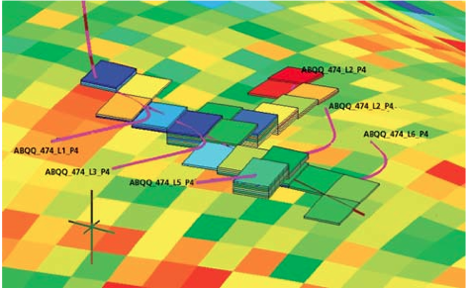
To prevent water penetration into individual lateral from having a fatal result on the whole well, a series of small valves was interposed at the entry to each lateral, so that it could be bypassed if flooded, without impacting the rest of the well.
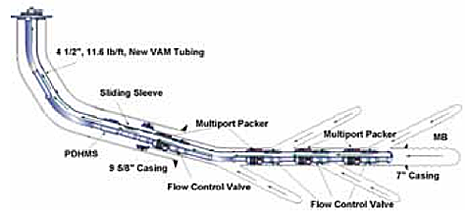
The life of each well is limited, as I noted last time, since these technologies were introduced as the water flood reached levels close to the top of the reservoir, and the remaining oil (sometimes referred to as ‘Attic” oil) is thinner in depth and underlain by varying heights of water column.
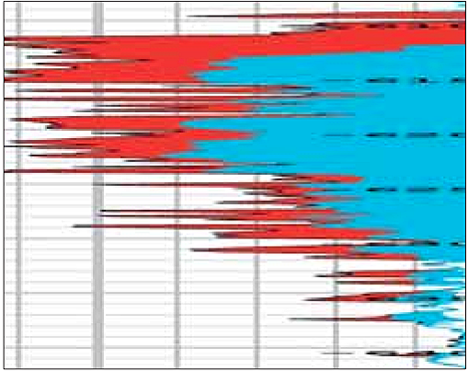
Simplistically, the above figure, which is a log of the well's relative fluid content as a function of depth from the top of the reservoir down, shows that while water (blue) is present in much of the lower segment of the reservoir, there is still a significant amount of oil (red) in the section of the reservoir flooded with the water.
By 2008, some 30% of the field production was coming from these attic wells, with 71% of that coming from 15 medium radius horizontals, 1 MRC well and 15 MRC wells with smart completions. In 2009, the program had 98 km of reservoir contact. (Lyngra et al). The more recent innovation has been to switch to a segmented slim smart completion product (SSC) with a more sophisticated valving system.
The SSC system consists of three major components:
1. Downhole hydraulic flow control valves: Three downhole valves were run. These valves provide the necessary controls to choke/shut-in laterals.2. Permanent downhole pressure and temperature gauges: These provide important real-time data used for optimization of the well production. After production start up, individual lateral production tests are performed to determine the Productivity Index (PI) and reservoir pressure for each lateral. This information is used with flow modeling software to determine the optimum flow control setting for each valve to achieve the desired rate from each lateral.
3. Open hole packers: These are utilized to hydraulically isolate and compartmentalize the three laterals. The packer is a hydraulically set, open hole packer with a high expansion solid rubber element capable of setting and sealing in washouts up to 21⁄2” higher than the run- in Outer Diameter (OD) of the completion string. The packers were set in anhydrite sections to ensure complete isolation from the other laterals. The proposed packer depths were confirmed suitable by the four-arm caliper log at gauge hole intervals.
The advantage of the SSC completion is that with valves down the laterals, it can be divided into segments and thus water inflow in one section of the lateral does not shut down the whole lateral.
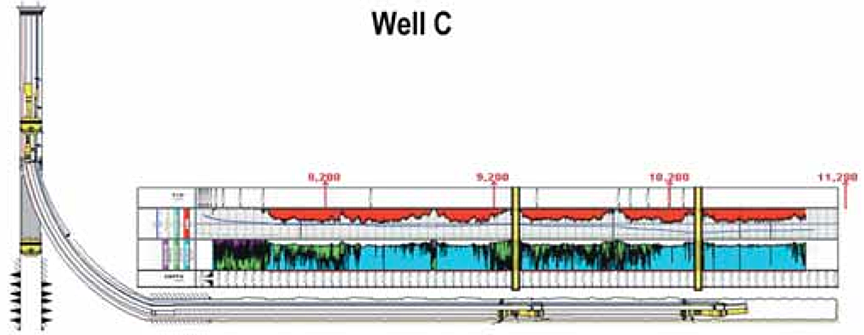
Lyngra et al note that for best success, the laterals should be located in the 3-10 ft thick upper lobe of the attic oil zone, with entry being through side-tracks from wells otherwise defined as dead. Life of the wells will still, however, remain limited due to the fact that this is the last remaining trapped oil now being recovered from Abqaiq, and then it will be over. Some of the initial wells watered out within six months.
But the technology has proved beneficial already in extending the life of not only Abqaiq, but also of the reservoirs in the nearby Berri field. Back in 2004, Baqi and Saleri noted that this field had the highest depletion rate of the major fields in the kingdom.
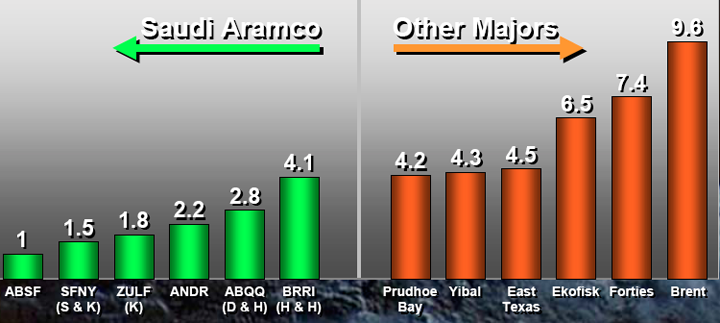
Note that these rates were reported in 2004, and that the fields have shrunk a little in size over the past eight years. So, at a relatively constant draw-down of the oil, the amount that is removed becomes an increasingly large fraction of that remaining, and the lifetime of the wells and now the field, shrinks accordingly.
As I just commented, it is the evolution of this technology which has provided new life to Berri, but given the length of this post already, I will postpone that discussion until next time.
P.S. Although the representations of the wells shown above are relatively straight and have a smooth path, the reality is not quite that simple. Sung et al have shown the reality of the first five-lateral MRC well paths in their paper.

Another good explanation of how Aramco is getting the last drops of oil from their reserviors.
After the technique of sectioning the laterals with "smart valves" to keep oil flowing in those small areas that have some oil remaining, what is left to do? Aramco now claims it will get at least 50% recovery rate, some reserviors planning to get 75%, IIRC. Seems to me like this technology will produce shark fin production plot on a per well basis and lower slope decline on a reservior basis.
This last oil from Abqaiq is certainly not the $10 per barrel oil of the past; maybe their production price for this last oil is closer to $60. Now I see why Aramco sees $100/barrel price as the new floor.
editted for clairity
Thanks Heading Out for an intersting discussion of current Saudi production.
Yes that seems likely.
One question I have is if the wells cycle at all, after the initial buzz of production? In N Slope fields I have worked, horizontal wells in a thin oil column (thin due to gas encroachment, rather than water) will come on strong, then taper off. In their final years, these wells will go on cycle production. Shut in for awhile, then produced for awhile, then shut in, etc etc. Cycle production can go on for quite a long time (at decreasing production rates) before they are finally P & A.
geo - I haven't experienced firsthand but another operator told me about a Venezuelan hz well. When water cut came p at the toe they set a packer and produced the heal. When the heal began to water out the pulled the packer and the toe produced with a lower w/c then when it was plugged back.
Rock - I'm not surprised that the Vensuelan horizontal well might perform that way. Similar things have happened up here. One strategy for horizontal wells in Prudhoe is to perf out near the toe first. Then when the gas rate gets too high, set a plug, and perf further back. The heel will usually be perfed last, then the well will be sidetracked. Sometimes a perfable whipstock will be used, so that after the sidetrack has declined, the original bore can be re-opened. Some wells have been sidetracked as many as five times from the original straight or slant well. The majortiy of these are coil side tracks in Prudhoe, which are significantly cheaper than rotary sidetracks.
First, thanks again to HO for another easy to follow very well illustrated key post.
And thanks for chiming back in with your rubber meets the road insights A_g.
Kind of wondered if you might be in the field up north this season as it has been the busiest in many a year.
Couple of quick questions. Any idea of how much ice road was built and how long they could be used this season (temps up north looked mostly pretty low which was likely related to the weather pattern that contributed to the ice pack extending out into the eastern Aleutians)? I don't have a very good handle on where the North Slope work was being done by whom this winter/spring. Any good web sites for that or do I have to resubscribe to Petroleum News?
And last but not least good luck to all those who are out in the line of fire working to keep our fuel tanks filled.
Reading Sung et. al.'s paper, I came across "tar mats" and "tar bodies",
apparently zones where the oil is so thick and tarry that it blocks flow
either of oil, or as in the example in Ghawar, pressure from water injection.
How does deep oil turn into tar?
Are there bugs way down to eat the light stuff,
or due to overcooking/undercooking of the source material,
or what?
How common are tar mats/tar bodies?
Petroleum Filling History of Central Alaska North Slope Fields
Graph on P 130.
P 44:
176 deg F to 230 deg F over 400' vertical. Its a fractionation tower.
Bob - thanks for the link to the dissertation.
And thanks to all the other answers posted.
The lack of a (or oversize) degree sign in the dissertation writer's typesetting is a tad confusing.
"290 API" Two hundred Ninety degrees API ???
Oh... 29 ° API (I can only hope the degree symbol via "°" displays in everyone's browser).
And that's 110 ° C.
contour of temps on page 159 (as the pdf viewer counts).
Very interesting stuff... that coal is way the heck down there, but I guess sedimentary rocks is sedimentary rocks, whether they're formed from a peat swamp or pond scum, etc., at one time they were the (land) surface.
Bets on ever mining coal at 9000 feet?
What's the thickest extant column of sedimentary rock known?
I know the Anadarko basin is up to 40,000 feet - like 8 miles of smushed sediment - amazing.
sun - I've read a number of reports of oil degradation as a result of bacteria being injected into the reservoir during the course of a water flood. It can also happen naturally when the reservir is uplifted close to the surface.
Prudhoe Bay Field has an extensive tar mat (about 40-60 ft thick) at the base of the main 400 ft thick oil column in the Ivishak sands. The tar mat is referred to as the "HOT", for "Heavy Oil Tar". This is on top of the OWC at a depth of about 9000 ft. There have been two competing theories for the HOT at Prudhoe.
One theory is that gas percolating upward from coals in the deeper Kekiktuk Fm has caused asphaltines to settle out at the base of the oil column. The other theory is that the HOT is simply the result of gravity segregation of the oil column. Neither theory is universally accepted. Biologic degradation of N Slope oil has been documented in the shallower West Sak reservoir, which in part accounts for the heavy oils found there.
Geo,
What are the chances of SAGD production of this Heavy Oil Tar, you certainly have plenty of spare Nat Gas up that way, as well as spare pipeline capacity.
As for Saudi, their Ghawar tar belt may offer itself to SAGD as well, Chevron have been trying it in the Neutral zone, but I am not sure of its economics.
The uppermost few feet of the HOT at Prudhoe is thought to be somewhat mobile, and may be producible. However the bulk of the HOT is solid tar, which is not mobile at all. I doubt that much if any of the tar mat at Prudhoe will be produced. There is however approximately one billion bbls of conventional oil still to be produced at Prudhoe. Much of this remaining conventional oil is directly on top of the HOT. Coil tubing drilling, being much cheaper than rotary, has proven to be the key to maintaining production.
There is a great deal of heavy (but still somewhat mobile) oil in other shallower reservoirs on the N Slope, notably in the Ugnu and W Sak. There is currently a big effort underway to evaluate various schemes to produce those reservoirs. BP has at least one HOT pilot production project underway in one of these shallower reservoirs.
Geo,
Thanks for the info, it looks like the production of heavy oils will also be one of the last frontiers that we will end up tapping as our daily production battles to meet demand.
At say, $350/barrel for Brent, I wonder if diluent/solvent extraction might work.
Several chemicals come to mind - which can be easily extracted and recycled. Everything from benzene to carbon tetrachloride (C Cl4) could help dissolve asphaltenes.
Alan
It seems that these attic wells have high costs and short lives.
$$$ in and oil out in a several year time frame.
Any idea
1) How long to develop a new SSC well ?
2) How long do they last ? A minimum of 6 months is given, but what might be (speculation ?) the average ?
18 months ? two years ?
I would expect that the best locations would be picked first (already done by 2008 in Abqaiq) and less promising locations after that.
This is certainly not long term "sustainable" oil extraction - but it keeps the oil flowing a few years longer.
After this, I assume, the next step is producing large volumes of oil stained water, water cut 95% - 99%.
Not Much Hope for Sustianed Saudi Production,
Alan
Alan
Alan:
This is still a fairly new technology, and they are working in a field that is very drained, but my impression is that they are looking to get about two years out of each well, but there is not a lot of information out there yet on the technology, that I have been able to find.
Dave