The Mechanical Transmission of Power: Endless Rope Drives
Posted by Rembrandt on March 27, 2013 - 11:42am
This is a guest post by Kris De Decker, founder and writer at Low-tech Magazine, an internet publication highlighting the need for elegant yet simple sustainable energy technologies. Read the article at Low Tech Magazine.
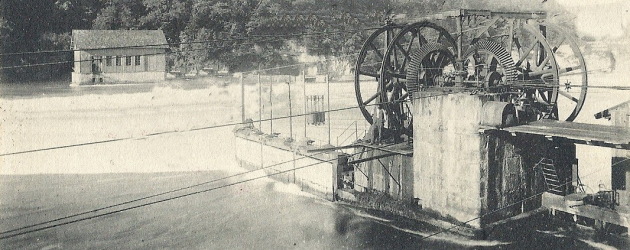
You don't need electricity to send or receive power quickly. In the second half of the nineteenth century, we commonly used fast-moving ropes. These wire rope transmissions were more efficient than electricity for distances up to 5 kilometres. Even today, a nineteenth-century rope drive would be more efficient than electricity over relatively short distances. If we used modern materials for making ropes and pulleys, we could further improve this forgotten method.
The rope drive is the culmination of a long history of mechanical power transmission. In the 1500s, mining engineers designed "Stangenkunsten": a method to transmit power from distant water wheels to machinery at the mineshaft, using reciprocating wooden rods. This early predecessor of electricity was improved in the 1860s oil industry's "Jerker line systems", which used steel cables instead of wooden rods.
The need for long-distance power transmission appeared first in the mining industry because mines could not be relocated to a nearby water power source. In the nineteenth century, the need for power transmission spread to other industries because the demand for power had grown considerably with the arrival of the Industrial Revolution, and most available water power resources had already been put to use -- especially in Europe. A new form of power transmission was needed to make previously inaccessible sources of water power available. For instance, many powerful water sources in mountainous areas were idle because these sites were unsuitable for building factories. The development of steam engines also called for power distribution and transmission, especially in Great Britain and in the US, because smaller engines were uneconomical to operate.
The pioneering power-transmission technology developed by the mining industry was not suited for most of these new demands. A Stangenkunst or jerker line system transmitted power using a reciprocating motion, while most industries required circular motion to drive machinery. Although these systems could be adapted to convert reciprocating motion into circular motion, this was possible only at low speeds and the expense of considerable energy loss [1]. Apart from this, the power that could be transmitted by a mere dead pull was limited. Enormous wooden rods or steel cables would have been needed to transmit the amount of power that could be harvested from mountain streams and waterfalls [2].
The Millwork
Around 1850, the only available technology for the transmission of fast, circular motion was the so-called "millwork". This combination of shafts, gears, belts and pulleys was aimed at the distribution (rather than long-distance transmission) of mechanical energy. It transferred power from a prime mover (a water turbine or a steam engine) to individual machines.
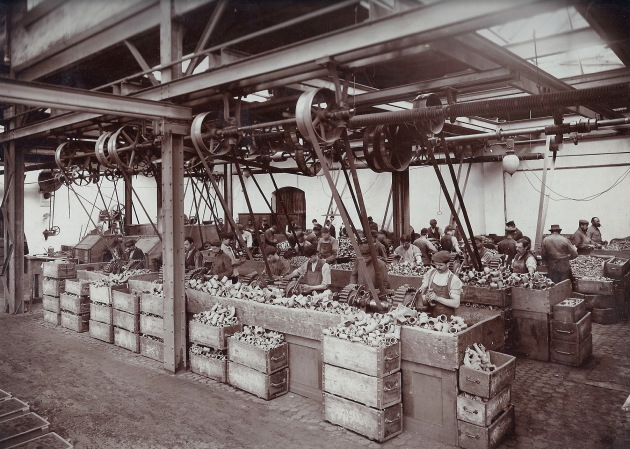
While the nineteenth-century millwork was considerably more efficient than the large wooden gears and shafts in the pre-industrial wind- and watermills from which it evolved, it was not suited for longer distances. One engineer calculated that 75% of the power transmitted by a lineshaft would be absorbed by friction of the bearings at a distance of between 95 to 600 m [3]. Moreover, millwork required protection from the weather and so could not be operated outdoors.
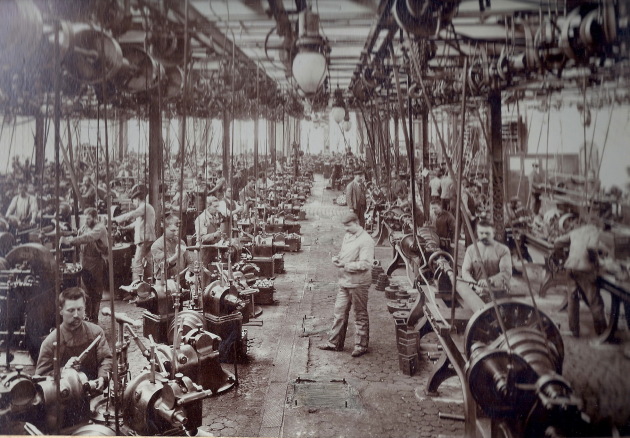
Even for short distances, nineteenth century millwork was rather inefficient. A major investigation in the early 1880s covering 55 industrial establishments, chiefly textile mills, revealed that the combined power losses in engines and millwork were on average 25%. For machine shops, the energy loss was on average 40 to 50% [4]. Line shafts were also hungry for space, costly to install, troublesome to maintain and adjust, hazardous in use, and inflexible in arrangement.
Wire Rope Power Transmission
Late nineteenth-century industry was in need of a more efficient and versatile method of power transmission for both short and long distances. Several alternatives were in the running: power could be transmitted by electricity, compressed air, hydraulics, steam, millwork, or ropes. While electricity eventually won the battle, a few others deserve more attention [5].
Rope transmission, the subject of this article, stands apart from all other power transmission technologies because it doesn't involve any conversion of energy. An endless rope drive transmits mechanical energy directly from a power source to machinery. As we will see, this makes rope transmission more efficient than any other alternative up to a distance of a few kilometres.
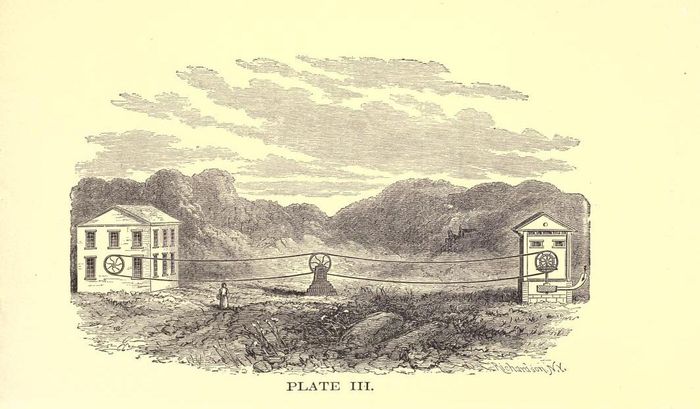
Contrary to electricity and compressed air, the transmission of power by rope was not a radical departure from traditional methods. Conceptually, wire rope transmission simply extended the range of millwork by improving its efficiency and flexibility, and by making it weather-proof. Rope transmission started in the 1840s as an element of millwork, using fast-spinning fibrous ropes as an alternative to belts transmitting power from the prime mover to the line shafts [6]. When fibrous ropes were replaced by metallic ropes (or "wire ropes"), a long-distance power transmission was born.
Wire Rope
Interestingly, the wire rope itself can be traced back to the same region that invented the Stangenkunst in the 1500s: the Upper Harz mining region in Germany. In the 1830s, mining engineer Wilhelm Albert twisted together several strands of metal wire around a hempen core, resulting in a superior hoisting cable for use in vertical shafts. Compared to a fibrous rope, a wire rope is much stronger, despite being the same weight and diameter. Unlike fibrous rope, it keeps its strength when it is wet, and its length remains constant under all weather conditions.
Metallic ropes were used throughout the global mining industry during the 1800s, replacing metal chains and fibrous cables for hoisting up ores and transporting miners up and down shafts. The wire rope also led to important uses outside the industry. It enabled the invention of the suspension bridge and came in handy as a means to carry other static loads such as smokestacks and masts. But its main applications involved moving passengers and goods, both vertically and horizontally. The wire rope gave birth to the elevator and made cranes and hoisting machines much more powerful. It introduced new transportation options on land (as in cable trains), on water (as in rope-powered canal boats), and in the air (as in aerial ropeways).
How did it Work?
Few know that wire rope was also used to transmit energy across land. A wire rope power transmission, or "telodynamic transmission" as it was initially called, was basically an aerial ropeway running without vehicles, at higher speeds. Both aerial ropeways and wire rope drives were sold by the same manufacturers. Wire rope transmissions used thin wire ropes (up to 2.5 cm in diameter) and large, cast-iron pulleys (up to 5 m in diameter), mounted on wooden, iron or masonry towers placed at maximum intervals of 90 to 150 m. The bottom of the pulley grooves was made of strips of leather to limit the wear of the rope.

The fundamentals of the method were concisely described by Albert Stahl in his 1889 treatise Transmission of Power by Wire Ropes:
"The construction of the apparatus is very simple. A tolerably large iron wheel, having a V-shaped groove in its rim, is connected with the motor, and driven with a perimetral velocity of usually from 50 to 100 feet [per second]. Round this wheel is passed a thin wire rope, which is led away to almost any reasonable distance (the limit being measurable by miles), where it passes over a similar wheel, and then returns as an endless band to the wheel whence it started."
For longer wire rope transmissions, two configurations were possible. Either one, long continuous rope was used, supported at intervals by carrying sheaves, similar to those of an aerial ropeway. Usually, though, a wire rope power transmission used shorter ropes that extended between stations, instead of running the whole length of the transmission. Each tower then served as the driver for another by means of a double pulley arrangement, or a double grooved wheel.
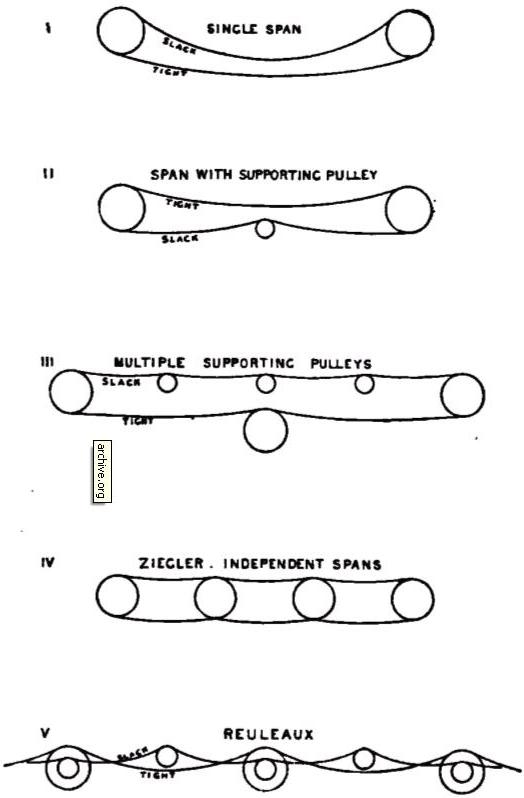
When using carrying sheaves to bridge larger spans, it was often sufficient to support only the slack side of the rope. The illustration above shows the different arrangements used for wire rope transmissions. When the rope drive had to change direction, or when the power had to be distributed to a number of consumers, this could be done by using either horizontal sheaves, or more frequently, bevel gearing/wheels.
Diffusion of the Technology
The use of wire rope for power transmission over long distances was invented by the Hirn brothers in 1850, while they were setting up a weaving factory in an abandoned textile works near Logelbach, Switzerland. The buildings were scattered over considerable distances and setting up multiple steam engines would have been too expensive. Following some initial problems (finding a suited material as a seating for the ropes proved to be one of the biggest) the Hirn Brothers set up power transmission lines between the buildings. The longest line reached 235 m, transmitting 50 horse power (hp).
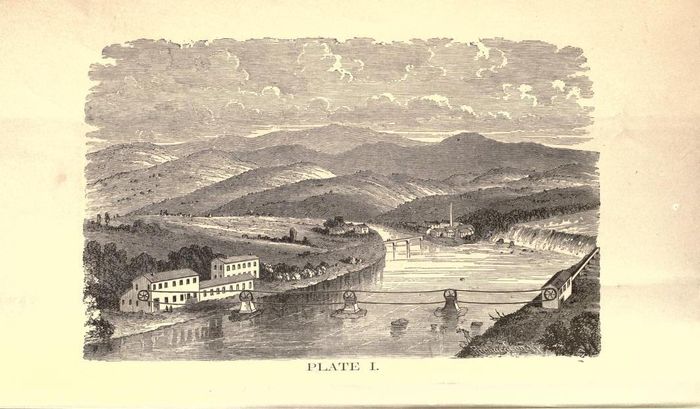
After the initial success of the Hirn installation, the technology spread rapidly throughout the Alps, and beyond. W.C. Unwin gives a detailed overview of the initial diffusion of telodynamic transmissions in his 1894 book On the Development and Transmission of Power from Central Stations:
"Soon after the erection of the transmissions at Logelbach M. Henri Schlumberger transmitted the power of a turbine 86 yards to work agricultural machinery. In 1857, at Copenhagen, Captain Jagd transmitted 45 hp to saw-mills at a distance of more than 1,000 yards. In 1858, at Cornimont, in the Vosges, 50 hp was transmitted 1,251 yards. In 1859, at Oberursel, 100 hp was transmitted 1,076 yards; and at Emmendingen 60 hp was transmitted 1,372 yards. In 1862 Hirn stated that about 400 applications of the telodynamic system had been constructed by Messrs. Stein & Co., of Mulhouse, carrying an aggregate of 4,200 hp over distances amounting altogether to 80,000 yards."
These installations had an average capacity of about 10 hp and a transmission distance of about 180 m. By 1869, two years after Hirn's invention received an award at the Universal Exposition in Paris, about 2000 permanent installations had been constructed on the European Continent. Most were relatively small ropeways, but some were fairly large. The Hirn system was adopted in three of the earliest central power stations in Europe: Schaffhausen (1864) and Fribourg (1870) in Switzerland, and Bellegarde (1872) in France. These installations transmitted between 560 and 3150 hp by wire ropes, over distances up to 966 m.
The Schaffhausen Transmission
The Schaffhausen transmission is regarded as the most complex wire rope transmission ever built, using 1027 m of ropes, aggregating more than 600 hp. After a period of trade depression there was a revival of industry at Schaffhausen. The required energy was found in the immense volume of water passing down the rapids of the Rhine in front of the town. Since the steep rocky banks forbade the erection of any factories in the immediate neighbourhood, the power was transferred diagonally across the stream to the town, about a mile lower down, and there distributed, with certain rocks in the water being used to set up the intermediate stations.
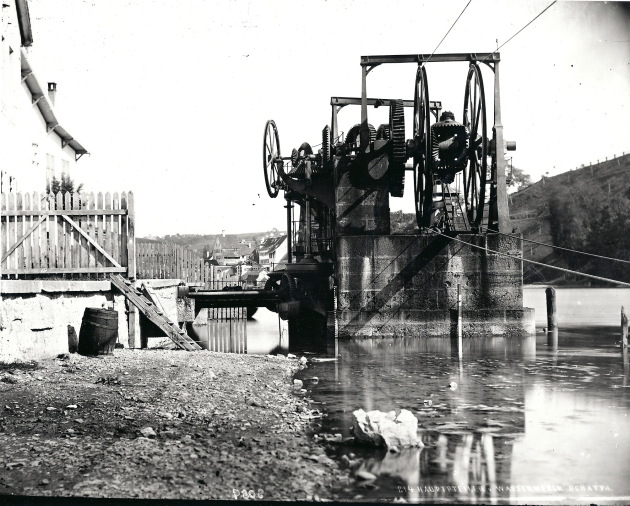
It is interesting to republish Unwin's full description of the Schaffhausen installation, because "it is essential to learn how far wire-rope transmission can be adapted to complex situations where many consumers require power":
"A weir was constructed during favourable seasons in 1864-66, across the rocky bed of the river, which is about 500 feet wide. By placing the turbine-house in the river-bed near the weir and constructing a tunnel tailrace 620 feet in length, a fall was obtained which varies from 15.6 to 13.7 feet. The turbine house contains three turbines with vertical shafts of 200, 260, and 300 hp, or 760 hp altogether. They gear with a common horizontal shaft by means of bevil gears. About 150 hp is transmitted from one of the turbines to a factory on the hill above the turbine-house, by a steel shaft 550 feet in length. From the same shaft also about 22 hp is transmitted, by a small cable passing down the left bank of the river and then crossing it, to a pulp factory on the right bank."
"This leaves a maximum of about 570 hp to be dealt with by the main cable transmission, which crosses the river directly from the turbine-house, and then passes along the right bank to the factories. The turbines are connected to two principal rope pulleys of 14.75 feet in diameter. From these pulleys two cables cross the river in a single span of 385 feet to a pulley station in the river at the left bank, where the direction of the transmission is changed by bevil gearing, and thence the transmission passes up the left bank of the river. The gross power in the horizontal driving shaft in the turbine-house is about 350 hp or, allowing for friction, say 500 effective hp to be transmitted to the factories, or 250 hp for each rope. Either rope is capable of transmitting at any rate a large fraction of the whole power temporarily, if the other rope is broken. The power is delivered by the ropes at the change station on the left bank. At that station about 22 hp is taken off by prolonging the second shaft of the bevil gearing and a subsidiary rope transmission."
"The remaining 478 hp is transmitted along the left bank to the first intermediate pulley station at a distance of 370 feet by a pair of cables. Thence to the second intermediate station, distant 345 feet, by another pair of cables. At 455 feet further is a second change station, at which the direction is again changed by gearing. Thence the ropes pass to two other intermediate stations. From the second intermediate station an underground shaft carries about 27 hp to ten small workshops, and from the second change station, and the third and fourth intermediate stations, cables are carried back across the river to factories on the right bank. From the first shaft on the second change station about 110 hp are distributed, partial by a special rope gear, partly by vertical and underground shafting, to four factories, one of which is the large Mosersche Gebaude; and from the second shaft of this station a steel shaft transmits 200 hp to Scholler's wool factory."
The Schaffhausen installation was a greatly successful undertaking. The number of renters of power grew from 13 in 1867 to 23 in 1887, while the average total horse power supplied grew from 121 to 641. The total income from rental of power rose tenfold.
Other Examples
The wire rope transmission at Fribourg, where the ravine is not suitable for factories, was no less impressive. Here, a wire rope transmitted 300 hp to an industrial site 90 m above the river. Power was distributed via wire ropes to a sawmill, a foundry, a chemical factory, a rope tramway for carrying timber, and a railway carriage works. The total distance of the transmission amounted to more than 1500 m. Part of the line passed through a specially designed tunnel.
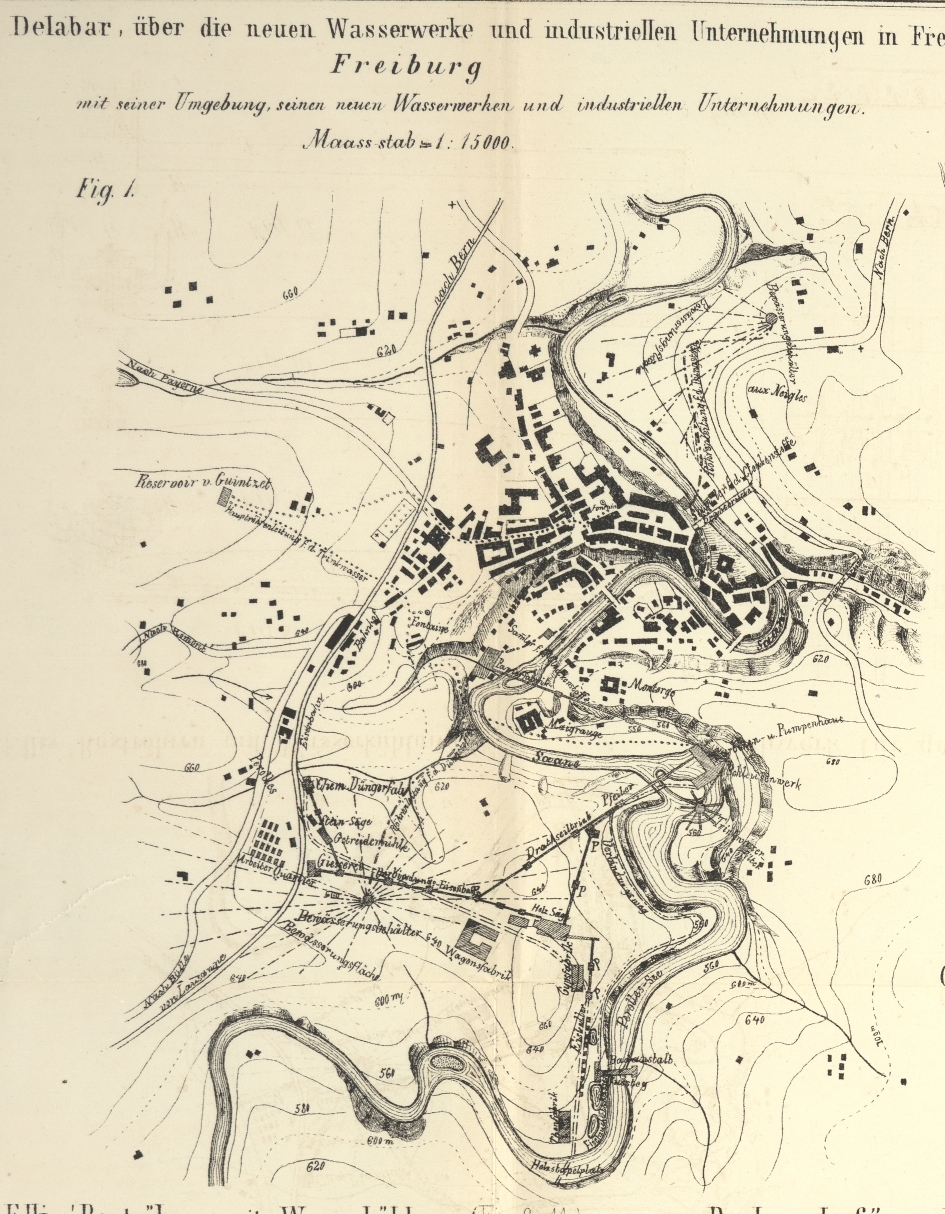
At Bellegarde, which lies about 25 km from Geneva, 3150 hp was transmitted in different directions via wire ropes from the river Rhône to the plain above, where it was used to operate a phosphate works, a wood pulp factory, a paper mill, a copper refinery and a pumping station. The transmission lines reached a total length of more than 900 m.
Most wire rope transmissions were built in France, Switzerland and Germany, but the technology was used all over the world. Following a serious explosion, an installation was put up at a gunpowder factory at Ochta near St. Petersburg, Russia, in 1867. A total of 274 hp was transmitted by more than 3000 m of wire rope to 34 widely scattered workshops and laboratories. The wire rope transmission was adopted to ensure that the buildings should be at a safe distance from each other were another explosion to occur.
At Gokak, India, a large telodynamic transmission was set to work in 1887. A total of 750 hp was transmitted to a large cotton mill via three wire ropes (illustration below).
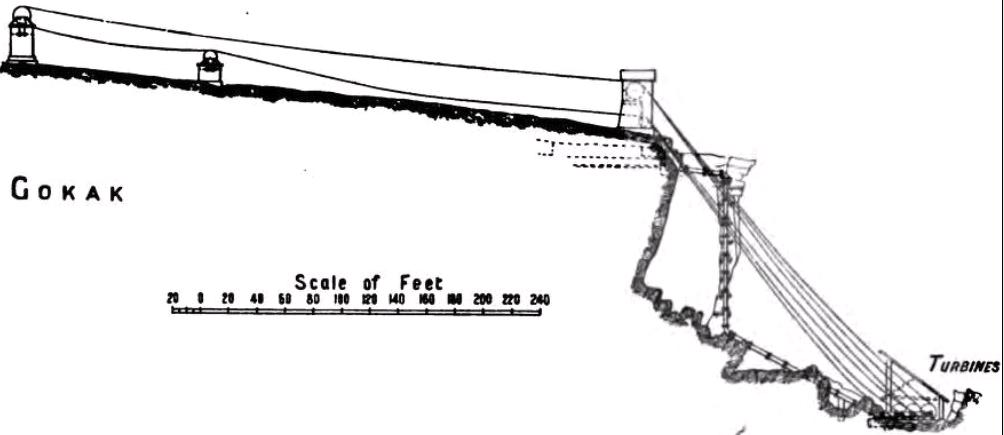
Numerous wire rope installations were built in the United States -- a total of 400 telodynamic systems were reported in 1874. Most prominent were those at Lockport (New York), Lawrence (Kansas), and near Great Falls (Montana) on the upper Missouri River [7]. However, none of them approached the size of the Schaffhausen plant in Switzerland. The technology seems not to have attained the popularity and importance that it did in the regions of its principal continental use, writes Louis Hunter, who adds that "this was no doubt owing to the greater abundance of water powers in the US in a wide range of capacities, and to the abundance of coal and the rapidly increasing acceptance of steam power from the 1850s."
Efficiency
It may seem that wire rope power transmissions running over hundreds and sometimes thousands of metres, could not be very efficient. However, a wire rope transmission was considerably more efficient (and cheaper) than electricity up to distances of about 5 km (3 miles). As with jerker line systems, the efficiency advantage was due to the fact that in a telodynamic transmission mechanical energy can be transmitted without conversion losses. This was emphasised by W.C. Unwin in 1894:
"The telodynamic system has the peculiar advantage that it transmits the mechanical energy developed by the prime mover directly, without any intermediate transformation. In electrical distribution a double transformation is necessary: a transformation into electrical energy by a dynamo, and retransformation back into mechanical energy by an electric motor. This double transformation involves waste of power and increase of capital expended."
On the other hand, a wire rope transmission introduces friction losses. The principal source of waste in rope transmission is the friction in the journals of the wheel shafts. The friction losses become larger as the distance increases, because more pulley stations have to be introduced, while the conversion losses of electric transmission are independent of distance. (There were transportation losses for electricity, too, but these were comparatively small). Beyond a certain distance, a wire rope transmission loses its advantage over electricity.
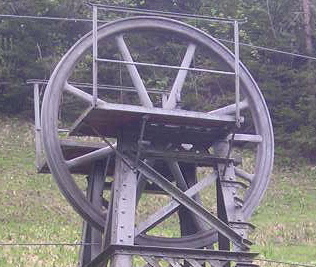
The efficiency of telodynamic transmission was carefully examined by Ziegler, one of the better known manufacturers. He made experiments at Oberursel, where 104 hp was transmitted over a distance of 963 m, in seven spans of about 122 m each. Ziegler's measurements showed that total loss of work over eight stations was 13.5 hp, which comes down to an efficiency of about 87%. The loss of energy was about 1.7 hp per pulley station.
From this he calculated that the efficiency of a wire rope transmission was 97% for a single span (two pulley stations), 95% for two spans (three pulley stations), 93% for three spans (four pulley stations), and 90% for five spans (six pulley stations). For nine spans (ten pulley stations), efficiency went down to 85%.
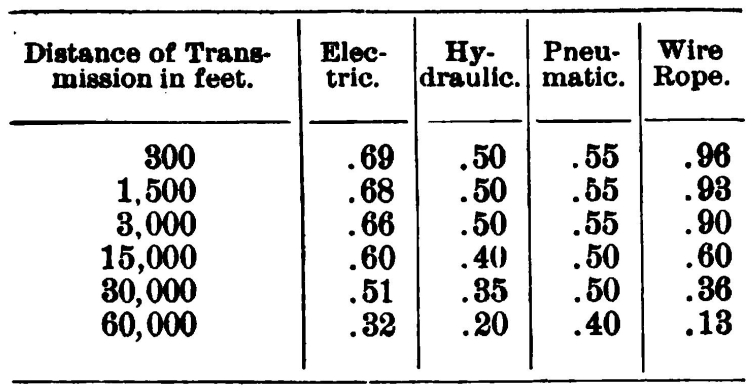
Another investigation, published in 1886, showed that wire rope had an efficiency that was largely superior for distances up to 900 m (3,000 feet), compared to the main competing technologies (electric, hydraulic and pneumatic transmission). Telodynamic transmission retained this advantage up to a distance of about 4,600 m (15,000 feet), beyond which it was defeated by electricity. In other words, wire rope lost its advantage over electricity when more than 35 pulley stations were involved. Were a wire rope transmission to be used over a distance of 18 km (60,000 feet), efficiency would go down to 13%. [8]
Note that the results are for a full load -- both electrical and wire rope transmission would have been much less efficient at partial loads. Also note that the results for wire rope transmission involve power transmission in a straight line -- every angle station would introduce additional losses. With regards to cost, Hunter notes that copper wire was 1.4 times more expensive than wire rope, and all nineteenth-century authors state that wire rope transmission was cheaper in construction and use than electricity, even though the ropes had to be replaced every two to five years.
How would a Present-day Wire Rope Transmission Compare to Electricity?
The advantages of rope transmission calculated in 1860 and 1886 still hold today. The only difference would be that a comparison of a rope drive and an electrical transmission would now show much better efficiencies for electricity at distances of 10 or 20 km (30,000 or 60,000 feet). In the 1880s, electricity was still transmitted by direct current (DC), which is much less efficient at longer distances than the alternate current (AC) that we use today. With AC, the losses are only 3% over a distance of 1,000 km [9].
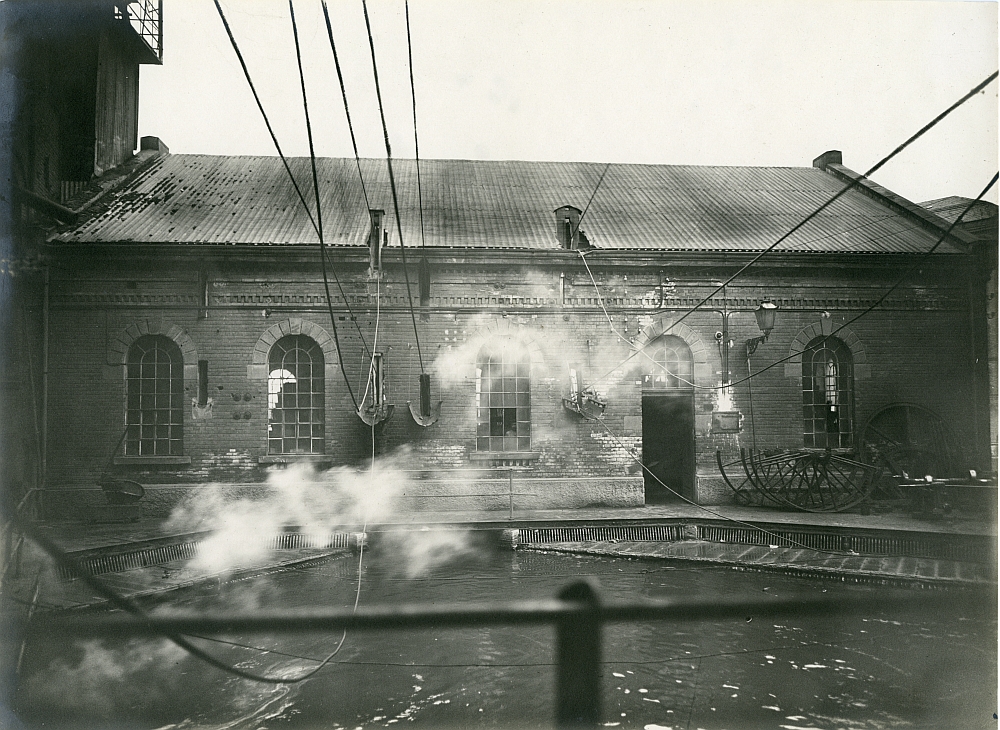
However, the efficiency of electricity would still be lower than that of a wire rope transmission over a relatively short distance, because of the double energy conversion that is required to move mechanical energy using electricity. The combined energy losses in a modern electric motor and generator are about 15%, which makes the double energy conversion 85% efficient [10]. This is better than the 69% efficiency in the 1889 table shown above, but still inferior to the efficiency of a nineteenth century wire rope transmission up to a distance of at least 1 km (3,000 feet).
Of course, it is not fair to compare a nineteenth-century wire rope transmission with a 21st-century electric transmission. With today's knowledge and materials, a rope transmission could be improved in two ways: by using stronger and/or lighter ropes, and by running them at higher speeds. The result would be that more power can be transmitted over longer distances with less friction loss. In 1894, Unwin noted that:
"The amount of work transmitted by a cable is proportional to the product of the effective tension (difference of the tension in the tight and slack sides) and the speed. To transmit power by manageable cables, the strongest material must be used for the cables, and they must be run at the highest practicable speed."
Substituting Velocity for Mass
This brings us to the basic physics of rope power transmission: in executing mechanical work, force can be transformed into velocity and vice versa. In a rope drive, energy can be transmitted at considerable velocity and little force, while at the receiving station it can be delivered in the generally more useful form of large force and little velocity. Increasing the speed of the transmission has a similar effect as increasing the diameter of the rope.

If a rope with a diameter of 2.5 cm (1 inch) can transmit 50 hp at a velocity of 20 feet per second (22 km/h), the same rope could transmit 250 hp at a velocity of 100 feet per second (110 km/h). Conversely, if a rope with a diameter of 2.5 cm can transmit 50 hp at a velocity of 20 feet per second, a rope of only half that diameter could deliver the same amount of power if it was running at twice the speed, and should run at a velocity of 200 feet per second (220 km/h) in order to transmit 250 hp.
Theoretically, there are no limits to power transmission by rope. "To put an extreme illustration", wrote Albert Stahl in 1889, "we may conceive of a speed at which an iron wire as fine as a human hair would be able to transmit the same amount of work as the original one-inch [rope]". Conversely, we could argue that if we could learn how to run ropes fast enough, a ship hawser could transmit the power of an entire nuclear plant [11]. While this is far from reality at this point, we do have better ropes than 120 years ago, and we can run them faster.
In the nineteenth century, the maximum power able to be transmitted over a single wire rope transmission was about 300 hp. Unwin explains that:
"The amount of power which is practically possible to transmit by a single cable is limited. It is not possible by increasing the size of the cable to transmit an indefinetely large amount of power. The cables become too heavy to be manageable, and the pulleys too large in diameter. (...). The peripheries of the driving wheels may have an anular velocity as great as convenient; the only limit, in fact, being that the speed shall not be so great as to involve any danger of destroying the wheels by centrifugal force. One hundred feet per second has been adopted as the greatest practicable speed."
Running Stronger Ropes at Higher Speeds
Today we have ropes made of artificial fibres, which have a similar tensile strength to wire ropes, but at one fifth the weight. Such ropes make it possible to place pulley towers further apart, reducing the friction loss and improving the efficiency of a rope transmission over longer distances. We could also try to run thicker ropes if they are lighter, thereby converting an efficiency advantage into a higher power capacity.
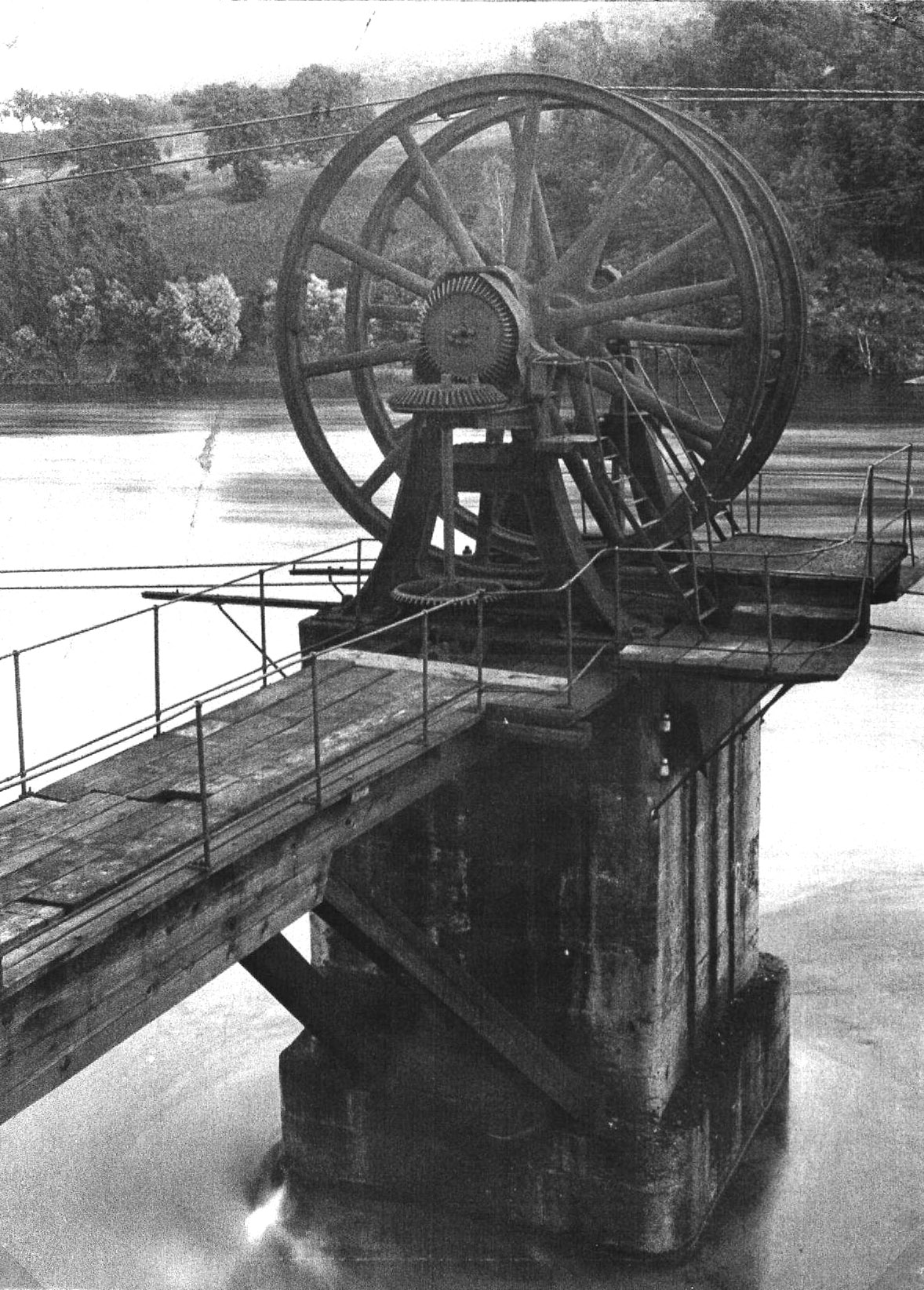
It's also possible to build sturdier pullies, allowing us to run these ropes faster. Higher speeds would allow more power to be transmitted at the same rope diameter, or further improve efficiency (because we can transmit a similar amount of power using lighter ropes). Albert Stahl already foresaw this possibility in 1889:
"The wheels themselves are made as light as is consistent with strength, not only for the sake of reducing the friction on the journals of their shafts to a minimum, but for the equally important object of diminishing the resistance of the air. It can hardly be doubted that abandoning spokes entirely, and making the pulley a plain disk, would considerably improve the performance, could such discs be made at once strong enough to fulfill the required functions, and light enough not materially to increase friction."
More Efficient for Small-scale, Decentralized Energy Production
Most telodynamic installations disappeared before the end of the nineteenth century, although some remained in use until the 1930s. Wire rope transmission lost the fight against electricity, mainly because the power network became ever more centralised -- ever larger power plants would send their power over ever larger distances, which could not be bridged efficiently by wire ropes.
Furthermore, a wire rope transmission did not offer a solution for the "last mile" in power transmission. It couldn't be used to distribute power to a great number of individual machines in a factory, because a wire rope transmission was not useful under a distance of about 15 m. In such cases, a wire rope transmission could not operate without millwork. Although the use of fibrous ropes had improved the workings of millwork, in this regard telodynamic transmission could not compete with the alternatives. Electricity, compressed air and hydraulic transmission offered an overall solution for both short and long-distance power transmission.
In spite of these drawbacks, power transmission by ropes might have a place in our energy systems. Today, there is a trend towards small-scale, decentralised power production, based on renewable energy sources. These solar panels, water turbines or wind turbines generate electricity, but whenever we need to produce mechanical energy, eliminating the step of generating electricity could result in a somewhat less practical, but more efficient use of energy.

For instance, it is more efficient to power a circular saw by mechanical energy produced by a modern version of an old-fashioned windmill or waterwheel than to convert the mechanical energy generated by wind or water to electricity by a turbine, and then convert it back into mechanical energy for powering the sawing machine. If power transmission is required in such a scenario, a wire rope transmission would be the most efficient choice.
Long-distance Rope Drives
Another advantage of a wire rope transmission is that it can double as a transportation system, combined with an aerial ropeway for goods or passengers. As we have seen in the article on aerial ropeways, it was not unusual to tap power from a gravity-powered aerial ropeway to power a crane or other machinery. The combination of a wire rope power transmission with an aerial ropeway only works at lower speeds, so that power transmission capacity is limited. (An aerial ropeway was generally five times slower than a rope power transmission). Still, this could offer interesting advantages for small-scale power production, especially in mountainous areas.
It may be that the future of wire rope transmission lies in long distance power transmission after all, at least vertically. The only research field that dedicates itself to rope drive technology these days is that of high-altitude kite power. Kites could harvest large amounts of energy at high altitudes, where winds are stronger and steadier. Transmitting this energy to Earth is most advantageously done by mechanical power transmission, says researcher Dave Santos from KiteLab Group in an interview:
"Electric cables would be too heavy. With kites, power-to-mass-plus-aerodrag is critical, and the mechanical case wins by a large factor. Wire rope is not quite so amazing as our new materials, but good enough for a critical advantage over electrical. The main challenge is to learn how to drive ropes at speeds of hundreds-of-miles-an-hour."
Ultimately, the rope drive may turn out to be useful for the same reason it was originally designed: it could unlock the potential of awkwardly-situated sources of renewable energy.
Kris De Decker (edited by Deva Lee)
Sources:
- "Transmission of power by wire ropes", Albert W. Stahl, 1889.
- "A history of industrial power in the United States, 1780 - 1930. Vol 3: The transmission of power", Louis C. Hunter and Lynwood Bryant, 1991.
- "The wire rope and its applications", W.E. Hipkins, 1896
- "Description of a new method of transmitting power by means of wire ropes", W.A. Roebling, 1872.
- "Rope driving: a treatise on the transmission of power by means of fibrous ropes", John J. Flather, 1900.
- "Notice sur la transmission telodynamique / Short notice of the telodynamic transmission of motive power", C.F. Hirn, 1862
- "On the development and transmission of power from central stations", W.C. Unwin, 1894. (alternative link).
- "Der Constructeur. Ein Handbuch zum Gebrauch beim Mashinen-Entwerfen. Für Mashinen- und Bau-Ingenieure, Fabrikanten und technische Lehranstalten", F. Reuleaux, 1869
- "Drahtseil Transmission", Polytechnischen Journals (multiple articles, 1850-1910)
- "Drahtseil", Polytechnischen Journals (multiple articles, 1850-1910)
- "Transmission des Forces Motrices des Turbine sur le Rhône de la Compagnie Générale à Bellegarde", web page, retrieved February 2013.
- "La Télémécanique", web page, retrieved February 2013
- "Turbinenanlage und Seiltransmission der Wasserwerkgesellschaft in Schaffhausen", J.H. Kronauer, 1867.
- "A trade catalog on the transmission of power by wire rope", Carroll W. Pursell, Jr., Technology and Culture, Vol.16, No.1, January 1975, pp 70-73.
- "From shafts to wires", in "Journal of Economic History", Michael Devine, 1983.
- "Kritische Vergleichung der Elektrischen Kraftübertragung mit den gebräuchlichsten mechanischen Uebertragungssystemen", A. Beringer, 1883
- "Cours de mécanique appliquée aux machines", J. Boulvin, 1891.
Notes:
- Stahl, 1889
- The Stangenkunst at the Lady Isabella wheel was the most powerful installation ever built, transmitting 150 hp using wooden rods. For pictures, see part one of this series
- Flather, 1900
- Hunter, 1991
- Pneumatic and hydraulic transmission will be discussed in a forthcoming article
- Flather, 1900
- Hunter, 1991
- Beringer, 1886 and Unwin, 1894
- AC Transmission Line Losses, Stanford University, fall 2010
- More powerful motors are generally more efficient, less powerful motors are less efficient. The figures given are for a 100 hp motor, similar to the power transmitted at Oberursel
- Dave Santos, personal communication, February 2013
Never even heard of Reuleaux. Went through high school and university Chem and Physics. They never mentioned him. Nice article, thank you.
A great alternative form of power transmission to chew on, Kris. (& Thx, Rembrandt)
One version of the Kite problem that has sprung to mind is the possibility of using Hydrogen to help with the lifting force for the kite, if that would do anything to offer less power lost to lifting work that could go straight towards Power Generation.
Don't have a scheme in mind for it, save to embed H2 cells in Wing Hollows that can then gain in span, chord and overall volume without as much concern over added weight.
Apart from that, I still look towards tying small windpower to a direct mechanical connection with a compressor for Heat Pump duties.. heating or cooling.. and so you've pulled out several conversion losses, and gone straight into a system that offers storage opportunities. With perhaps a bit of cleverness in creating the transfer gadgetry at the Wind Turbine head, and a potentially short enough run that you could use a Rotating Shaft or pulleyed cables.. unless of course, you could simply put the compressor right into the turbine and just transfer the compressed fluid. Hm. Ok.. think I just talked myself off that ledge, but I'd still like to have the transfer rigs drawn up anyway.. maybe to run my shop tools, or peel my potatoes.
I realise that you aren't being serious about this kite thing, but obviously just using the power generated from the turbine directly to power a horizontal lift device (like a helicopter) could hold the kite aloft.
IMHO, the kite idea isn't a bad one except that untethered, wind forces could tear it or the wind turbine blades apart if it gets really windy. Given that the mass of tethering cables becomes prohibitively expensive is where the kite idea goes down.
Perhaps you haven't heard about some of the proposals and tests going on out there.
Kites and tethered 'aircraft' that take advantage of stronger and steadier high-altitude wind are, in fact, serious proposals. Some of them are tethered with conductors for transmitting their energy, and others use flight patterns to allow the 'kitestring' (a much heavier and more engineered one than you may first think of) to supply the energy where it is generated by the kitereel on the ground.
We've had a few keyposts on them.. and I haven't seen them shot down yet. I don't think the tethering costs or weight have been fully proven either way, but numerous tests have already shown a reasonable amount of viability.
http://www.kitegen.com/en/
http://www.youtube.com/watch?v=FJmlt3_dOuA
http://www.youtube.com/watch?v=rsHUALU--Wc (This one, tested in Limestone Maine last year, is lofted inside a Toroid Helium Balloon)
Very good article. It's interesting that it could help out with high-altitude wind power, because when I think of a technology that could unlock vast amounts of energy without screwing the world up too badly and could be conceivably available to us, it's usually the first thing that comes to mind. Perhaps the Oil Drum could have an article about that as well? Here are two previously written ones by Ugo Bardi I found very inspiring, in any case:
High altitude wind power: an era of abundance? http://europe.theoildrum.com/node/5538
High altitude wind power II: the reactions http://europe.theoildrum.com/node/5554
I don't see how kites could produce much power. They have to be placed at great heights to extract much more power out of the wind, and the drag area would be huge so a brief strong wind gust would rip them to shreds. I realise the chemists have been working on some light and super strong materials which would definitely help out here, but otherwise it's not going to amount to a hill of beans.
I've provided links to your previous response to my post, but of course, it's awaiting moderation, and the new robot on the block might snip it.. but this is a serious proposal. Look up kite-gen for one, and there are a great many other demonstrations of the idea.
..And as far as heavy winds are concerned, these would be the only wind turbines around that could meet the wind with some flexibility already, and also be drawn down and packed into safety for more extreme weather situations.. (which we can usually see coming..)
Absolutely hilarious! I love the annotations, which give this some semblance of seriousness. Bravo!!
Absolutely interesting is how I would phrase it.
The best way to transmit power depends on the price and availability of resources as well as the circumstances of the transmission. EG on a ski slope every skier could have a tiny electric snow tractor charged of an induction grid buried under the snow - obviously an extremely poor solution - or an excavator could have a system of cables and clutches rather than hydraulics and cylinders (eg the steam shovel). Transmission by electricity and hydraulics is in its heyday but cable transmission still has its niche - eg large cranes, ski lifts, elevators, funiculairs etc.
I think if copper and aluminum were to increase in price a few hundred percent, and wiring and electric motors were to go up consequently, we may again see manufacturers using belt and cable powered machinery. What worked can work again - it's just a matter of looking past the circumstances of our present age.
I have always been amazed at how much power can be transmitted through so little material. I once worked in a nuclear plant where my inspection routine took me under a steam pipe that carried 1.4 gigawatts to the turbine hall - the pipe was about 18" in diameter and carried the entire output of the plant to the turbines. The pipe emitted a high pitched whine that was the sound of steam at a few hundred degrees and at, IIRC, about 1000 psi (or perhaps 3000 psi, that's the part I'm uncertain about), pumped to a very high velocity. There was enough power there to supply about 1.4 million homes.
I have no doubt that wire rope can be harnessed to transmit power efficiently and economically. The question is whether in a given economy and application, there is another method that is cheaper.
It is not a matter of whether one or another method is more technological or "advanced".
To shorten this, the rope transfer system is for local use.
Inductive power transfer ? Maybe the only hope for powering large numbers of electric cars.
http://en.wikipedia.org/wiki/Resonant_inductive_coupling
http://en.wikipedia.org/wiki/WiTricity
Unfortunately, inductive power transfer has the (serious) caveat that you have to run power lines wherever the cars go, and that's a lot of power lines. Don't know about the radiation hazard, but a lot of power is still lost to the environment.
Resonant transmission goes back to Nikola Tesla and good singers.
I was highlighting the dependance of choice of technology on the circumstances of a particular application by describing a very poor application of electrical power transmission technology (induction on a ski slope) next to a very good application of cable power transmission (eg a crane) - I was tired so I did not do it effectively - it was fun to try though, induction is fascinating.
Whether a technology is appropriate to a particular circumstances has nothing to with how advanced the technology is - the most elegant solution is often quite simple.
I'm having a wordy spell apparently.
:-) wordy
Interesting links.
I bring a portable induction range camping- very convenient and smaller than a propane camp stove.
Of course, what is the efficieny of mechanical>AC>mechanical? 90%+? There is a reason we don't see these systems any more.
For a cool operating relic, however, check out San Francisco's Cable Cars (they have a nice museum), same tech, pulls them over miles. Or a ski lift.
For a transfer of about 100 hp, the combined energy losses in a modern electric motor and generator are about 15%, which makes the double energy conversion 85% efficient. More powerful motors are generally more efficient, less powerful motors are less efficient. This was mentioned in the article.
Whether or not this efficiency loss is acceptable, depends on how much energy you have available, and how much energy you need. You don't seem to realize that these systems have disappeared at the same time that we got access to large amounts of cheap energy.
San Franscisco's cable car is far from the only cable car in the world still operating. Quite some new lines have been built, others have been modernized. I would not call them relics.
Always fun to read your articles Kris. Of course as I read it the amount of dedicated space rope transmission systems need jumped out at me as did the size and versatility of say a 1000kW diesel gen set--1340 HP comes off those little beasts. There is a reason we've leaned so heavy on oil for portable power. Not so very hard to lay insulated electrical cable every which way. Still on a modern construction site wire rope energy transmission is very high value, done by the very high dollar/hour construction crane. No doubt there are other industrial applications where the dedicated space required by the wire rope system wouldn't be and issue and the increased efficiency would pay.
Of course kite generation systems jumped to mind as well and I wasn't surprised you ended on that note but the sites don't have much fresh stuff (2010-2011). Have you seen any recent trial results published?
This is wonderfully ridiculous. For any significant power transfer, this system will be incredibly heavy and incredibly dangerous.
The key physics:
Power = tension * velocity
To transmit the power from a 1-gigawatt electrical power plant, you'll need a steel cable 3 inches in diameter, under its maximum load of 300 tons of tension, moving at the speed of sound. (I don't recommend exceeding the speed of sound.)
At these velocities, the aerodynamic drag losses will ruin you.
But worst of all, the kinetic energy of this cable (about a megajoule per meter) means that any failure will be catastrophic, with a wildly snapping cable decapitating entire neighborhoods. Expect damage similar to a series of airline crashes along the entire cable route.
You can reduce both the drag losses and the safety problems by using thicker, higher tension cables at lower speed, but then the whole thing will weigh 10-50 times as much as a comparable high-voltage electrical cable.
Oh really, even though they DID bring up some such extreme theoretical possibilities, it's really not credible to claim that they are really proposing anyone do such a thing as grab the output of a nuke and ship it this way.
It's from 'Low Tech' magazine.. it's taking the opportunity to look at industrial energy solutions of the past and consider the ways (and the reasonable scales at which) one might make good use of useful ideas.
'Significant Power Transfer' is not necessarily only a matter of sheer volume and size anyhow... and even with that, if some form of rope/wire transfer became a useful little residential item, like a drive train to have your kids run the fridge compressor with their bikes before school or the kite idea, which HAS been seriously 'floated' and demonstrated here.. or anything equally untenable and unpalatable today, then the potentially hundreds to millions of users that might buy or build such a thing COULD be able to start transferring a 'Significant' amount of power, all told.
I considered high power for a "reductio ad disastrum" case, but my point still holds for small scale. Suppose you want to replace the humble 20-foot orange extension cord with a rope drive. It will be far heavier, it will fail if you move either end as much as an inch, and it will mangle any child that tries to play with it.
No matter what the scale, a few percent gain in end-to-end efficiency is not worth the cost in weight, flexibility, or safety.
Personal anecdote: I have a cat who likes to chew on electrical cables. Last night he was apparently at it again, because the lights suddenly dimmed, there was a little "pop", a smell of singed fur. But he's fine, just a little scorch mark on his cheek. If I'd used a rope drive, even the slightest brush of his tail against it would have us cleaning bloody bits of kitty off the ceiling.
We had two neighbour's cats who crawled into our car overnight and they were killed when the motor started up. About 1.2 million people die worldwide every year in automobile accidents.
http://www.who.int/gho/road_safety/mortality/en/
Bad example, goodmanj
From the article: "A wire rope transmission is not useful under a distance of about 15 m".
First, you ridiculize the technology by using the example of a 1-gigawatt electrical power plant. Then, you do the same with a 20-foot cable inside your home.
Do you also have something to say about a practical wire rope transmission?
No, because there's no such thing. Long, short, intermediate: I assert that there is *no* real-world application for which wire rope is safer, cheaper, or more practical than electrical cable and a motor/generator set. Having given examples at both ends of the power spectrum, I put the onus on you to suggest one.
The article gives a beautiful summary of wire-rope power history, for which I'm sincerely grateful, but its only selling point for modern wire-rope is a tiny gain in efficiency for a narrow range of distances. This gain will never be worth the safety risk.
You have given two examples that are completely irrelevant. On the other hand, the article details several examples of wire rope transmissions that were operating succesfully, so I have no clue why you want me to suggest yet another one.
A modern wire rope transmission would be the most efficient power transmission option for distances between 15 metres and a couple of kilometres. You might call that a narrow range of distances, but in my opinion, this gives lots of potential in a decentralized energy production scheme. I do not advocate to replace all electric lines by wire rope transmissions. I am pointing out that they might be useful in some situations.
Where's the safety risk? Have you read any news about ski lifts falling down on people's heads lately? Aerial ropeways that come crashing down from the sky? I have an electric transmission line running over my house. How safe would it be if this snapped? And what about nuclear plants? Humanity uses lots of potentially dangerous technologies that still seem to operate rather safely. I don't see why a rope transmission should be different.
Ski lifts are not a power transfer mechanism and do not need to be under anything like the tension you would need to achieve reasonable power transfer efficiencies. Note the many suport points required to get a lift up a hill?
The tension applied to wire rope transmissions at the end of the nineteenth century (which allowed a power transfer up to 300 horse power per rope) did not raise any safety problems. None of the documents I have consulted mention safety issues with rope drives, while they all do describe the danger of steam engines, which had the tendency to explode, and of millwork, which could mutilate workers.
I kind of empathise or sympathise with both of you inasmuch as many are suggesting that civilization, itself, is dangerous and must be dismantled if it isn't already too late. Nice site by the way, Kris. One gripe is that your 'Doubts on progress and technology' text should be in another colour. Red and black seem so cliche with the engineering crowd. Try chartreuse. ;)
I'm wondering, though, if some (in)efficiencies might be 'swap-outable' or tolerated over other kinds of (in)efficiencies, such as in an economic, environmental and cultural permanence sense, and where the KISS principle fits into all this, too. Like, where investment, manufacture, shipping, maintenance, localization/local resilience, happiness, true, as opposed to manufactured needs, and self-sufficiency, etc., are concerned.
Engineering seems big on the KISS principle, and yet what do we have? Everything-but? Take nuclear energy for example.
I once proposed 'occupying' a fairly pristine ghost town-- Balaclava, Ontario-- that has a selection of old but nice buildings. One of them is an old mill-- apparently with some leftover hardware even. I love the idea of these rope transmission things to transmit power-- with some potential freedom from the state corporate oligarchy to boot-- to a small ecovillage created from that town.
Seems we really have to start looking more at our technology from a holistic/contextual viewpoint. Like what kind of life do we want for ourselves? Retro BAU?
While Chinese-made photovoltaic panels are all fine and nice, they seem a little remote for more visceral/tangible control.
While this 'fuelless' friction heater runs on electricity, it, along with others, could run directly off some kind of wire rope or windmill system, thus, as direct mechanical transmission to heat without electricity or fossil/other fuel.
Does this type of heater make sense?
Here's a comment from this video:
Well, He is claiming to be violating the second law of thermodynamics. What's to be said?
How do you mean? (In layperson's terms? :)
Incidentally, and in any case, my regard for using electricity to spin the contraption, assuming it works, is more as a proof-of-concept. I like the idea of direct mechanical heat without having to burn anything, and doing away with electricity altogether, which seems to be less self-sufficient and have a higher reliance on technological infrastructure.
Of course friction produces heat, and primitively-speaking, some of us rub our hands together, for example, to get them warmer. Seems to me that if one had a decent wind, a simple windmill, and a well-insulated, maybe straw-bale post-and-beam timberframe 'Thoreau cabin', one might be able to "rub" something inside it to get a good section of it a fair bit warmer. That is, besides the partner under the down blankets.
James Joule did many such experiments carefully measuring the amount of heat produced against the amount of work needed.
A given amount of work makes a given amount of heat, no matter if by friction, heating of wires, gas compression, pumping liquid through small holes, or in his most famous experiment, using a falling weight to turn a paddlewheel in a tank of water.
http://en.wikipedia.org/wiki/James_Prescott_Joule
A heat pump is another story, that can indeed provide more heat than the work expended, by pumping it from a thermal reservoir, a heat engine in reverse.
A heat pump just moves heat energy from a source to a 'load' or sink. What the guy in the video is claiming is that, over time, using friction, he's getting more energy out than he's putting in. Even ignoring entropy, this is not possible; it's a perpetual heat machine. Besides, elecrical resistance heaters are near 100% efficient (virtually all of the electrical energy is converted to heat), so he's claiming efficiency higher than 100%.
Ok, thanks, guys. I think that was understood, almost intuitively. Also, the wrong video was linked. TOD's recent spam filter issues might have thrown things off a little. ;)
No, the friction heater is no more efficient than an electric resistance heater. Both convert 100% of the electricity used to heat.
Save your money and buy a resistance heater.
Well my regard to this (and other kinds of) friction heater was as a simple direct mechanical transfer, rather than electrical. More 'ecovillagey' perhaps. Electricity seems to rely on a greater level of complexity, although it is doubtful that we will ever completely be without it, no matter how decrepit our civilization becomes.
There are some interesting videos on U-Tube of friction welding.
http://www.youtube.com/watch?v=LcQgf23dC4Y
I can guarantee you there is less heat energy being produced, than electrical energy going in.
Thanks, TFL, I figured as much. I am also the previous victim of an almost-seized motorcycle piston.
As for your video, there seems no real fundamental difference from that robotic shop, and this. It's for a truck? To ship food or widgets to and fro'?
Kris, FWIW I greatly enjoyed the article. I'm always amazed at ingenuity when it is a necessity.
I concur, Turnbull. Great stuff!
There was a remote sawmill here in Western NC that used one for years, pre-WW1. There was no electricity or fuel available, the trees at the time were too big to haul out, so they used a cable several hundred yards long to transmit power from a large creek out into the flats. The foundation is still visible in the creek at the base of a cascade; now private property. I always considered it an elegant solution. They couldn't use sluices to divert water because there was a small ridge between the creek and the mill site. The cable drive went up one side of the ridge and down the other side into the flat. All of this was related to me by an old wood carver who worked at the mill (when I told him I thought they had been generating electricity).
There are some engineers who put a great amount of thought and imagination into asserting how something CANNOT be done.. and then calling that their proof. I find it an unfortunate misapplication of brainpower.
Apart from Every Ski Lift and Tramway and Funicular Trolley out there, another extremely practical example of the utility of cable drive systems would be practically every Elevator that is in service.
Using an example of an extension cord replacement that would be set up to be in reach of one's kids.. you're not really trying to look at where it CAN be useful, only where it can't.
No, the systems you present are using the wires to do physical work, not primarily for power transfer, and have other technical requirements that make the technology appropriate for that niche.
Well how do ski lifts fare? Last time I was on one, some time ago, if for many years, they seemed to work fine, safely and similarly, and go all over the mountain, the distances of which seemed significant, and adequate for any small-scale locality to leverage.
And if you were so inclined, and it was convenient (and/or deliberately multi-use-designed), you could always hitch a ride and wire yourself over to some place. Like email. ;)
Ski lifts are not a power transfer mechanism, they are a high volume transport mechanism in places which do not have roads.
Ski lifts and rope drives are basically the same technology. How you define them doesn't matter.
A good fit with the previous article about windmills:
http://www.theoildrum.com/node/5913
Transmissions losses on the electrical grid are around 6% to 7%, so it is pretty damn efficient.
An ordinary asynchonous electric motor of a few kilo watts usually have an efficiency around 85% http://en.wikipedia.org/wiki/Asynchronous_motor
NEMA Premium motors help push the needle a little higher.
Cheers,
Paul
No it has very little to do with AC or DC what matter is voltage. For a higher voltage the same power could be transmitted with a lower current and over longer distances most of the losses are resistive which are proportional to the current.
It may however be noted that conversion of voltages are a lot easier with AC. In fact a common method to transform DC voltages between different levels is to chop the voltage to AC, use a transformer for the conversion and rectify the voltage. By using this method to chop the voltage smaller transformers may also be used since it is possible to use higher frequencies.
In fairness, the technology for doing DC-DC conversion did not exist in the 1880s, unless you wanted to consider the rather extravagant possibility of using an electric motor to drive a generator. At the time, DC power had to be generated at a voltage not far removed from what was required at the application end.
Edison did come up with a three wire distribution scheme that, similar to that commonly used in homes today, made distribution possible at twice the required voltage. However, even with this, DC power distribution was very expensive in requirements for copper if unacceptable losses were not to be incurred over even relatively short distances.
I can't speak to the 1880s, but in the early 20th century, motor-generator sets were the standard way to do DC voltage conversion.
Correct, AC or DC is not the issue. High voltage, like high velocity wire rope, is the issue. Today we have mostly high voltage 138,000 to 765,000 volt AC lines, but also many +/- 250,000 and higher volt DC lines. This is thanks to semiconductors that can invert (chop) DC to AC and rectifiers to make AC back into DC. By 1977 semiconductors were the choice for conversion. But the really good semiconductor improvements for large power conversion have come in the past 30 years or so with the IGBT: http://en.wikipedia.org/wiki/Insulated-gate_bipolar_transistor with devices like this: http://www.pwrx.com/pwrx/docs/cm750hg-130r.pdf providing MegaWatt inverters with just 2 modules that weigh a few pounds each.
Willie
6500 volt, 750 amp. Switching just under 5MW, and dissipating 10,000 watt, that's an incredible 99.8% efficiency.
Do they stack like 100 of these for a 500,000 VDC to AC converter?
AC is of course the grid of choice for retail distribution (and serves an energy 'storage' function because of the useful spread of demand and supply among millions of end consumers).
However, stability and bulk transfer between AC grids is served by modern HVDC. (There are some spectacular bulk transfers these days, particularly in China.)
http://www.abb.com/hvdc
In aggregate us millions of small males will still need to obtain our own small supply of … whatever … - especially if our male preoccupation has led us to supporting a family, even if it is of the female-led kind ;-)
PS My father in early part of 20thC England saw ploughing using wire ropes linked to semi-mobile steam engines (hauled by horses) on areas of 20 - 30 hectares. Timing, and therefore speed, matters in many farming operations and efficient diesel was not an option.
This reminds me of the old ceiling fans that were linked together with ropes or belts and ran off of one motor. I have five of the assemblies; down rods, mounts, bearings, fan hubs, all solid brass and ornate. My wife bid on a lot at an antiques/estate auction wanting a nice vintage art decco lamp, and these fans (less the blades) were included in the lot. I've thought about hooking them up to a PV-direct DC motor, but maybe someday I'll run them mechanically from a windmill ;-/
If you like this sort of thing, the Kona Inn restaurant in Kailua-Kona, HI has a gigantic network of belt-drive fans in its dining room.
Since I went looking for a link with photos.
http://www.windandsearestaurants.com/konainn/gallery.htm
Or, like Wilie Coyote, you could use the fans to power the windmill to run the fans, and the belt drive interconnect would be very efficient...
Bryan
... or I could just open the windows ;-/
This is all rather interesting. It might also be noted that, into the early 1900s, it was common for mechanical power to be distributed in factories using arrangements of shafts with belts used to provide power takeoff points along each shaft. The original power source would likely have been a steam engine or water wheel, or later, even a large electric motor. There was an alternative scheme for delivering power over a distance that was also used in the 1800s - basically, it was to redirect existing waterways or create new ones. As a bit of a hobby, I've been researching the early development of the Welland Canals in Canada. In the case of the First and Second Welland Canals, the Grand River to the West was dammed and a feeder canal used to provide a source of water to the canal at an elevation higher than Lake Erie. Not only was this used to allow the main portion of the canal traversing the Niagara Peninsula to be filled to a level above that of Lake Erie, but it also made water available that could be used to power mills and other manufacturing facilities, particularly in Merriton and St. Catharines. Even after the Third Canal was built along a different route below the Niagara Escarpment, the water flow along the old route was maintained for some decades into the 20th Century to supply industrial needs. Subsequent technology developments were unkind to Merriton in particular; the availability of electricity from Niagara Falls negated the advantage of having locally available water power, and, although a local portion of the Second Welland Canal remained in operation to about 1915, nearly all of the industry in the area disappeared in the following decades. This is well documented, for example: https://docs.google.com/viewer?a=v&q=cache:yeoLa56V0_UJ:www.erudit.org/r...
Thanks for your comment. TOD has a new aggressive spam filter that is trapping legitimate comments.
If you submit a comment and see that it doesn't post, please be patient and don't resubmit the comment multiple times.
We're trying to train the program to see the difference and it tags you as a spammer if you submit more than once. :/
Trying to stay patient myself -
Kate
I remember seeing mechanical power being used in the shop that my dad worked at during the early 1950's in Pitcher OK. The building was old and in disrepair. The shop part had open sky over the operators for natural light. The machines including lathes and overhead rotating shaft were covered by a row of corrugated tin. The speed of the lathe was adjusted by moving the belt on a step pulley while the belt was still spinning. I would guess that there were around 20 machines being powered from one engine in this shop. By today's standards it was not a safe working area. By the mid 1950's the machine shop had closed down although dad still stopped by from time to time to visit with the owner who lived across the street.
Pretty cool stuff. Could this be advantageously used to move windmill generators off the tower and onto the ground? I imagine the tower could be lighter and/or taller, which might improve the cost per megawatt. Perhaps multiple towers could share a single generator?
I remember hearing stories about my great-grandfather's wood-working business in rural Iowa circa 1900. A donkey engine of some sort outside the shop turned a line shaft that ran the length of the workshop. Every few feet along the length there was a power tool of some sort (saw, lathe, drill press) that was connected to the power shaft with a thick leather belt. Each had some sort of clutch arrangement so they could be independently disconnected from the shaft.
Yair
This was often a beatiful simple devise called "fast" (as in fixed)and "loose" pulleys . . . a simple lever arrangement slipped the flat belt from one to the other
Reverse operation if needed was achieved by putting a twist in the belt.
Cheers
power shaft with a thick leather belt.
Ignoring the nasty ways one can die or be maimed by things like rope/leather/power takeoff shafts - Leather power transfer was part of US College teaching till the late 1960's. MSOE (Money Simply Overrides Ethics) shut down its Institute of Leather Technologies in either 1967 or 1968.
There is a reason things like line shafts aren't used - they are dangerous to the workers.
I’m not an engineer, I’ve had freshman level physics, but.....isn’t this a description of the cable cars still operating in San Francisco? They are primarily for the tourista, but do serve the local commuter. There should be a lot of data on the mpg equivalent and I would love hearing you folks a lot smarter than me banter this about.
Kris,
Great article and obviously well researched, like all of your work. I forward links to my engineering inclined family members every time.
Having a old sawmill that used flat belts I learned something about them, their tracking/seeking the crown of a pulley, etc. I was surprised to learn of their greater efficiency over V-belts. You document quite well the idea that the old timers had less energy available and so efficiency needed to be higher, a situation whose time will re-emerge.
Keep up the great work!
I've just remembered one of my newest On-Topic shop projects, which has been to take a lovely old 30" Scroll Saw ($40 on Craig's List), and convert it from having this massive, 70 pound Electric Motor, to being Rope-Run, hence quiet, independent and much more pleasurable and satisfying to operate. It is mounted Long-wise on a classic Sewing Machine Treadle-Table that my grandfather had used in novel ways decades ago in his shop as well.
Instead of using the original remaining treadle elements, since an operator will need to be positioned at the End of the table, I have Hung a ball-bearing'd 5/8" axle perpendicular under the Saw-table and this bears two flywheels from Nordic Track Exercise Machines, a pulleywheel aligned with that on the Scroll saw, and a pair of Nordic Track Clutch Drives, which allow me to pull a length of Nylon Parachute Cord Back and Forth, getting forward propulsion with either pull.
The two drive pulleys in this system are also connected through a double-stretch of this para-cord, instead of a logy and stiff v-belt, as would generally be expected in this setting.
I still have to Fashion a 'Double Treadle', which will allow one to comfortably drive this saw with each foot, alternating.. and I'm changing the Spring Return at the top of the blade with a set of sprung arms linking this action to the drive bar below, to remove some of the drag from the system, a bit like having a controlled Coping Saw, in effect..
Sorry I don't have pix of it yet.. but will have some avail. for a future conversation, I'm sure. Part of the point of this for me, is that our power tools are often ridiculously overpowered.. I can make some very nice and controlled cuts on my (other) Grandfather's old Delta Band Saw by just reaching back and pulling on the belt to drive the blade when I don't want all the sound and fury that comes from bringing three-quarters of a horse into the shop with me. Much of the benefit of many shop tools is in having a good means of holding the cutting tool and the workpiece more firmly and accurately than we usually do with a free handtool and a crude vise. That sort of proper management of the elements is NOT dependent upon Fossil Fuels, while it's advantages are vast!~
Best,
Bob
30" Scroll Saw .... to comfortably drive this saw with each foot
What is the plan for keeping the blades sharp? Back before power handsaws (1500 watts) and 2-3 man homebuilding crews (2 weeks to put together a modern home - 4 to 8 for a stick built) there used to be a 30+ man crew using handsaws (90 watts) and the hand saw crew would have to take 3 to 4 breaks during the day to sharpen the hand saws.
power tools are often ridiculously overpowered
But it does let you use duller blades.
Well in this case, the 30" refers, possibly in error*, to the throat of the saw (possible dist. from the edge of the wood to the cut), and the blades are only about the same dim. as coping saw blades. I'm not claiming total independence from a world that still has sawblades around.. while my hands are nonetheless quite familiar with cutting on tools that are hardly as sharp as they could be, and those jobs only get easier, as said above, when you have a proper little work surface holding the tool and the wood steady at a consistent angle, and you can power them from different muscle-groups than are managing the workpiece.
Still, I keep trying to source really good Coping and Hack Saw blades, as these are some of the so-called 'disposables' in the kit that are the most vulnerable part of my shop, it seems to me.. any referrals to really good blade suppliers would be welcome!
*(but the dimension that is most often the limiting factor for various tasks..)
The first time I ever helped build a house (it was the same summer the US got out of Vietnam) we were off grid and the generator did not show up until we got to the interior. The builder was a retired painter and we used his grandfather's handsaws. We had the saws sharpened every evening, as none on the job had sharpened hand saws and the old painter wasn't going to start experimenting on those venerable tools.
What fun to make the long top cut for porch rafters where the 4/12 pitch lay on the 12/12 pitch main roof. Back and forth between the crosscut and ripsaw I went but neither was too impressive making the diagonal cut. I'd have liked to have something like jokul's treadle powered rig then that's for sure. But those old saws were still in excellent shape, the painter said the trick was to never let them lay out in the sun and get baked.
Skilsaws do make a horrible racket, but since the cheap, disposable carbide tipped blade has been introduced not a whole lot of time is spent sharpenning/changing blades. Ripping two thicknesses (three if they'll do it) of 3/4 inch used form ply at the end of 200-300 feet of cord coming off temp power makes those worm drive Skilsaws work. They aren't overpowered then, and I've yet to see another make that doesn't get its guts sucked out by that abuse--which is regular usage on commercial concrete form work.
You'll probably not be surprised to hear that I have sketches for another rig that would have one or two folks, kids even, driving a blade with a see-saw or 'hand-cart' lever, so one can put their whole body into the work of such a cut as those you had to do, instead of just one arm. Otherwise, so much of the effort ends up going into holding and control.
Not surprised at all. Have you a copy of Treatise on Mills and Mill Work: On machinery of transmission and the construction and arrangement of mills by Sir William Fairbain?
The link goes to the Google ebook page for the download (~15MB PDF). No doubt you'd have been a much sought after millwright a century or two ago
Those lines begin the preface to the first edition (1863?) of the work
Energy Cache 50kW Installation.
http://www.youtube.com/watch?v=G3nz_kU604s&feature=youtu.be
Storage system using cables, ski lift fashion, to haul gravel up a hill. Then back down to generate electricity. They are claiming efficiencies comparable to lithium batteries.
I don't however see how they can switch between storage and generation mode quickly enough to provide frequency regulation as their website claims they can.
It seems like so little power for the amount of machinery required. Think of the complexity compared with a turbopump/generator, a pipe, and a perhaps natural reservoir at elevation. There are so many parts.
I wonder who granted funds for this.
Maybe it's a wink to those snarky barstids who have to crack wise about the end of the stone age..
Of course, my version of this would have a series of train cars fashioned from Repossessed Suburbans and Humvees, filled with Marble Countertops and riding up and down tracks at Vail and Aspen.. (They've already got the cables right there!) .. but that's me.
"...Humvees, filled with Marble Countertops..." OMG that is funnier than what I was thinking - used oil fright cars filled with water on a sloped track.
Excellent use of local resources!
In addition to the vehicles and countertops available in Aspen, there's plenty of raw marble down the road in Marble, Colo.
Fun read as always Kris.
The thing that jumped right out at me was the amount dedicated space wire rope power transmission requires. Did you have any numbers for what sort of losses occur when a straight line transmission is impractical--no efficiency loss bending a power cable. I've put in a utilidor or two to carry steam lines and power cables for co-gen systems. A moving cable in those confines would be terrifying.
Simple, durable, reliable safety clutches would certainly be needed these days. The circle saw example you gave is a prime example of that--I'd hate to be running logs through a headsaw that wouldn't trip some sort of 'circuit breaker' if it started to bind up.
It took a while but we've a pretty good handle on using electric power safely--that and its versatility will likely make the efficiency losses in the double conversions worth the cost just about every time the calculations are run.
There may be some industrial applications today where the dedicated space wire rope transmission needs is trumped by the efficiency gained by transmitting the mechanical energy directly, but I'm guessing mostly wire rope will keep transmitting power generated by ICE and electric motors and mostly for vertical lifts--elevators and cranes, it is darned hard to beat it there.
In my 1950s childhood in Lancaster, Pa., one of our Amish neighbors had rigged a cable to a small dam and waterwheel at the lower part of his farm and fed the power uphill about 200 yards to an old-fashioned well pump handle outside his farm house. It creaked a lot, but got the job done. (I've also seen Amish use hydraulic rams.)
Some of those guys were pretty sharp despite only having an 8th grade education.