Tech Talk: The Technology of Grouting
Posted by Heading Out on September 26, 2010 - 8:45am
For the last two technical talks I have been explaining how, by bolting rock layers around an opening, spraying concrete on the walls of the opening or a combination of both, one can stabilize openings underground. Sometimes, however, the rock itself is relatively weak. (This is a common problem when driving subway systems under major cities, as an example). In these cases the rock won’t have enough strength to hold the walls, until a stronger tunnel lining system is installed. Often that is pre-cast concrete liner segments, but the walls have to be kept open until they can be installed.
Another problem, which is common in almost every underground excavation, is that there is water moving through some of the rocks and, if not dealt with it can fill your excavation very quickly, even if the flow rates don’t initially sound that high. There are two fundamental ways of both increasing rock strength and stopping fluid flow through the rock. The first is to inject some form of grout into the rock, under enough pressure that it will fill all the cracks and then set. The alternative, and becoming more popular method, is to lower the temperature of the rock, so that the water freezes. This increases the rock strength, stops the water flow, and is temporary, rather than a permanent change that can be reversed, after the tunnel is finished. I’ll talk about Ground Freezing in a later post, and in this one I will run through some of the simpler descriptions of Grouting.
When the drillers at the Deepwater Horizon well in the Gulf wanted to stop the flow of oil out of the reservoir into the well, or drilled hole, they pushed a cement down into the well, to fill the gap between the internal casing they were leaving in the well, and the surrounding rock. That initial injection of cement into the well did not work well, and the oil was able to penetrate through cracks, weakness layers or perhaps zones where the cement had not properly set. When the well was finally plugged towards the end of the operation, cement was pumped down the well at higher pressure so that it not only filled any gaps that the oil and gas had been flowing though in the original cement plug, but also moved back into the rock, filling the flow channels that had developed to carry oil and gas from further back in the rock, into the well.
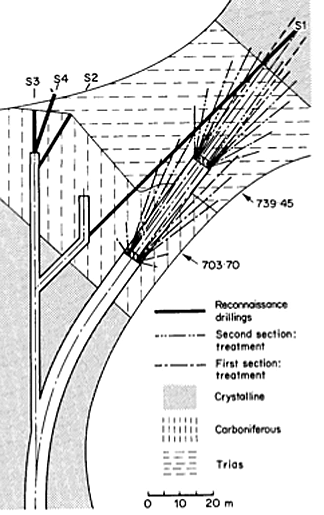
In a grouting operation, that is the goal. Normally a ring of holes are drilled into the wall of the tunnel so that they fan out around the planned tunnel path, and they are about 40 ft long. At this point the cement is brought to the site, ready to be injected. However, it is not just a case of bringing in say 8 bags of cement from the local hardware store. When dealing with the choice of cement, its physical and chemical contents and the pressure at which it will be pushed into the rock there are a number of factors that have to be established first.
The temperature and water chemistry of the surrounding rock are some of the initial critical factors. Changing either will change how fast the cement sets, or if it will. The object in this case is to get the cement to flow into the cracks around the drilled holes, so that the cement will flow to fill those spaces completely, before it sets. But it has to set in a reasonable time for work to continue on schedule. And since water chemistry in a tunnel, and temperature, change – so the mix has to be altered to accommodate those changes.
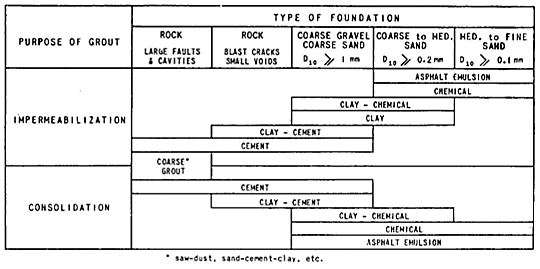
The next thing that has to be checked depends on the size of the cracks that the cement is being injected into. If the cracks are very thin, and the cement contains particles that are bigger than the crack, then the wall of the opening will act as a filter paper, stopping the cement particles from getting back into the crack and filling it. On the other hand if the particles are too small, then they will not bridge together to block the crack, and stop the fluid flow long enough for the cement to set up. If there are too many large particles then, when they lock together, they leave too large a gap between them, and fluid can still flow, and the rock will remain weak.
Over the years, a rough correlation has been developed between how much fluid is flowing though the rock, and the type of rock, and the size of initial particles needed to provide an initial seal of it. But, as with cementing in an oil well, when the first cement injection has been finished, and allowed to set, then the rock is tested to see if the flows have stopped. Very often they have not, though hopefully they have diminished. This is because the first shot into the rock is more aimed at narrowing the flow passages and slowing the flow of fluid through the rock so that when finer particles are used, in secondary grouting, they won’t be carried away into the rock, before they can set up and block the remaining passages.
And so, typically, after the first grouting operation, there will be a second, to further fill the narrower passages in the rock, and those bits not properly sealed by the first injection. The cement grouts also act to give some strength to the rock, since they are filling the spaces within the rock structure with the set-up cement, that has some strength to it.
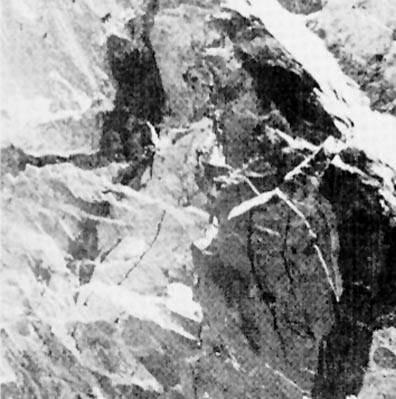
However to fill the finer cracks, and to stop the flow, cement may be too coarse a material in some of the rocks found. In such a case, then a chemical gel might be injected into the ground to fill those finer cracks. These tend to set up rather more like Jello, and while strong enough to resist water flow, do not usually give any additional strength to the rock.
There is one caution in injecting grouts into the rock that has to be borne in mind (and I know of cases where it wasn’t). Grouting operations force liquid into existing cracks within the rock surface. The liquid hopefully fills those cracks, before it sets, but if it is injected at too high a pressure, then the force on the walls of the crack can cause it/them to grow. At that point the rock will become weaker, instead of stronger, and the section in the tunnel roof/walls that is already open can fall in. Which is not good!
In the main, it is not economic to keep injecting more and finer grouts into a rock until the flow is totally stopped. As the flows diminish the costs to stop them rise, and so it is usually the case that the operator accepts a certain small flow rate as the most economic alternative, and makes arrangements to deal with that water as it enters the tunnel. (If not I have seen tunnel floors lifted by the pressure that develops in the water trapped behind them).
Of course, if all else fails, then you can cut a slot into the wall and fill it with cement to completely seal off the excavation – though this is often done with a series of drilled holes, it can also be done with a variety of rock saw.
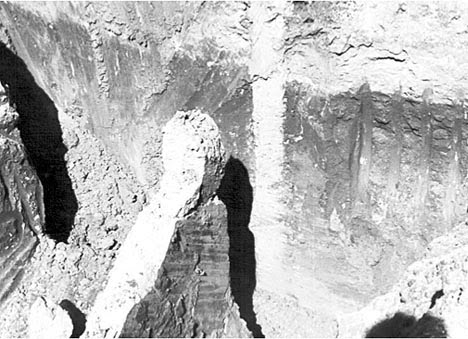
Thanks, Heading Out!
It seems like there are a lot of details involved in any of these things, that we don't often think about.
It seems like quite a number of these cements and gels are necessary for drilling oil wells the way we do today. Are these products made locally, with local materials, or are these pretty much high tech materials, needing technology and materials from around the world?
When we are drilling the extra deep wells and polar wells and other unusual wells that we are drilling today, it seems like we would need even more specialized products, too.
The subway system I use needs its tunnels grouted, because the initial section had the moisture barrier installed wrong way around and water comes in to the tunnels. Also the concrete, even above tunnel level, has visible cracks in it, which don't give me great confidence in its safety. (The maintenance engineers' written width notations next to the cracks in the walls aren't helping. Seeing stalactites growing overhead doesn't do anything for me either.)
Great post, Heading Out, thanks very much. I understand that some tunnelling operations are hampered by highly abrasive silicate particles. The particles wear down the teeth in the boring apparatus. Does adding grout change the abrasive quality?
Thanks HO.
You mentioned that typically the holes drilled in a ring around the planned tunnel path are about 40 feet long. Is there more a less a typical range of pressure under which the grout gets pumped in to fill the cracks or does that vary greatly depending on rock types?
One chemical grout I recalled because it had a particular sounding name, "Takanaka Aqua-Reactive Chemical Grout". It could penetrate fissures and set up into a foam upon contact with water, hopefully shutting off the flow of water.
For more details see:
http://www.concreteconstruction.net/industry-news.asp?sectionID=716&arti...
Grouting is a science and an art and specialist grouting consultants are well worth what they charge because the work can be halted (expensive delay time) until water inflow is abated or reduced to manageable rates.
Chemical grouts are expensive and there was some concern over some of them being somewhat toxic and contamination of ground water.
Added On a water dam job were I was the owners rep I asked the contractor how much more cement grout he thought it would take to stop the water? He replied - How much more money do you have?